Electric globe valves are essential components in various industrial applications, providing efficient control over fluid flow. These valves are particularly known for their ability to regulate flow with precision, making them ideal for processes requiring fine adjustments. In this article, we will delve into the key features, applications, benefits, and maintenance considerations of electric globe valves.
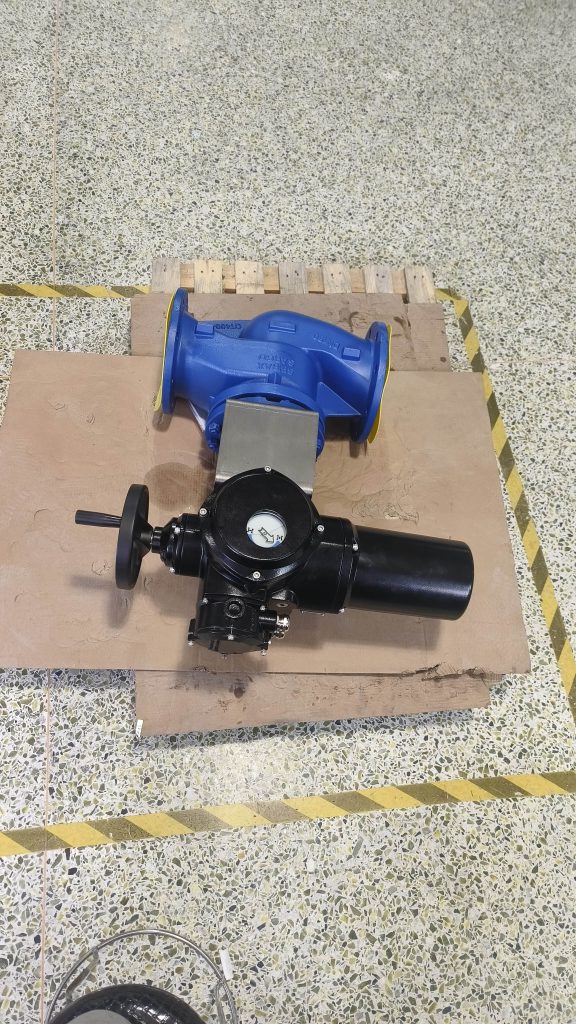
Electric globe valves operate by using an electric actuator to open or close the valve, thereby controlling the flow of liquid or gas. The design of a globe valve, characterized by a spherical body and a movable disc, allows for a significant reduction in flow turbulence. This design provides better flow control compared to other valve types, such as gate valves. When the actuator moves the disc, it either increases or decreases the flow area, effectively regulating the flow rate.
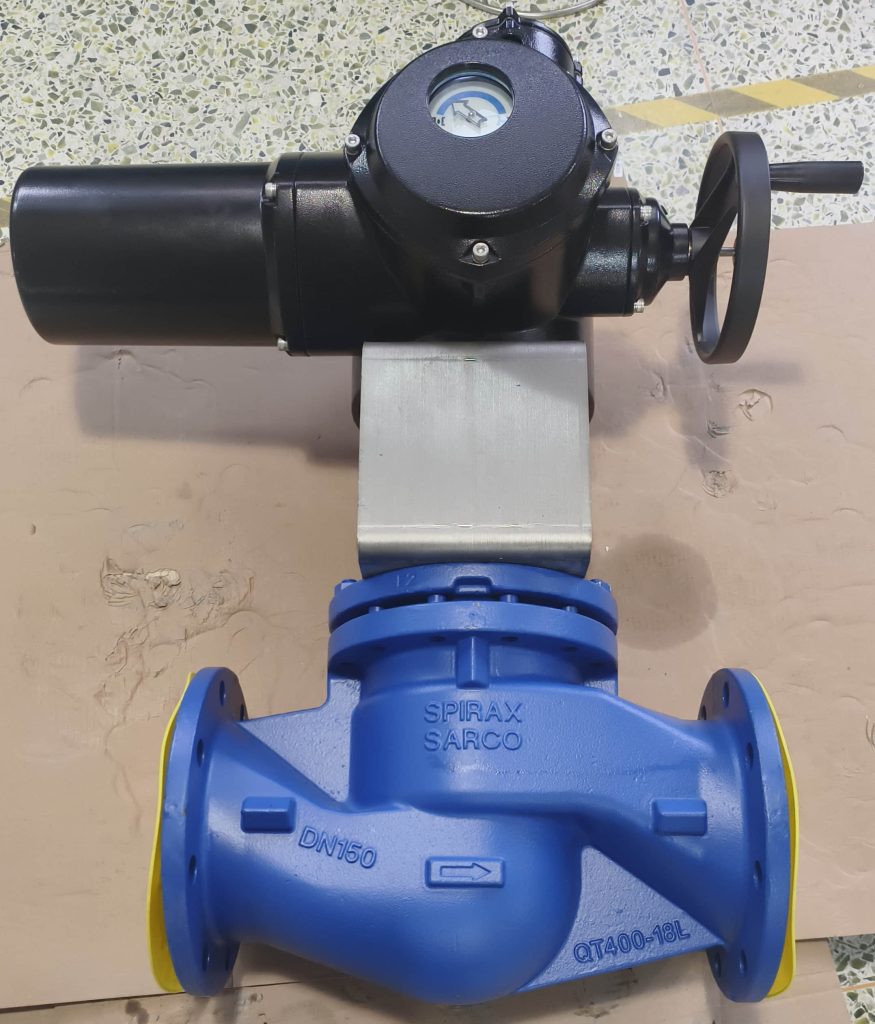
One of the primary advantages of electric globe valves is their precision. The electric actuator allows for automated control, which can be integrated into a larger system for remote monitoring and adjustments. This automation reduces the risk of human error, enhancing the reliability of the system. Additionally, electric globe valves can be equipped with positioners and control systems that enable real-time adjustments based on varying conditions, further improving operational efficiency. Electric globe valves find applications in numerous industries, including oil and gas, water treatment, chemical processing, and HVAC systems. In the oil and gas sector, they are crucial for managing the flow of hydrocarbons, ensuring safety and efficiency in extraction and transportation. In water treatment facilities, these valves regulate the flow of water through various treatment processes, contributing to the overall quality of water supply. Their versatility makes them suitable for both high and low-pressure environments.
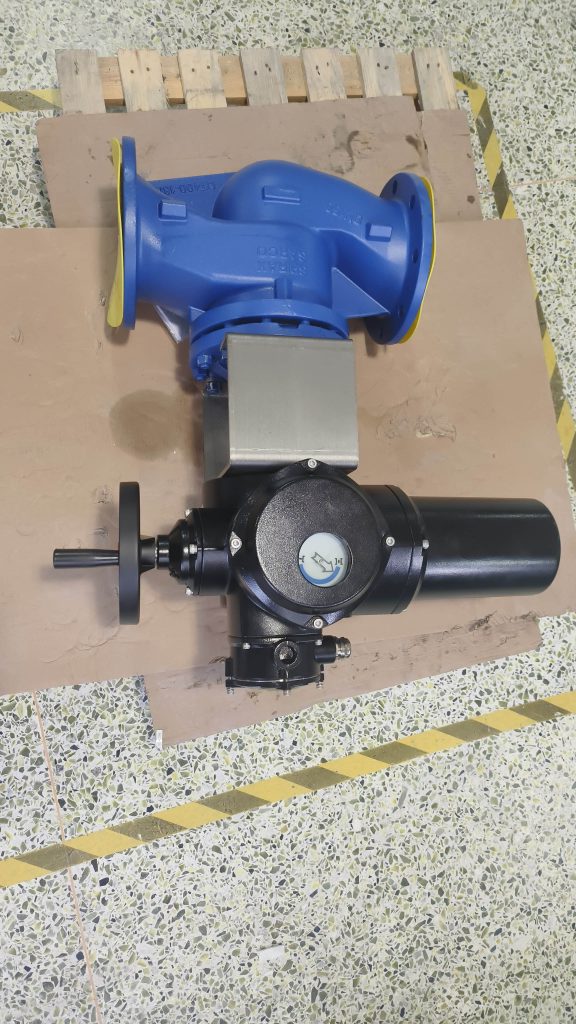