Electric globe valves are an essential component in modern industrial systems, providing a reliable solution for regulating fluid flow. They combine the robust structure of a traditional globe valve with the precision control of an electric actuator, making them ideal for various applications in industries such as oil and gas, water treatment, and HVAC systems. This article delves into the design, functionality, advantages, and applications of electric globe valves, highlighting their significance in contemporary fluid control systems.
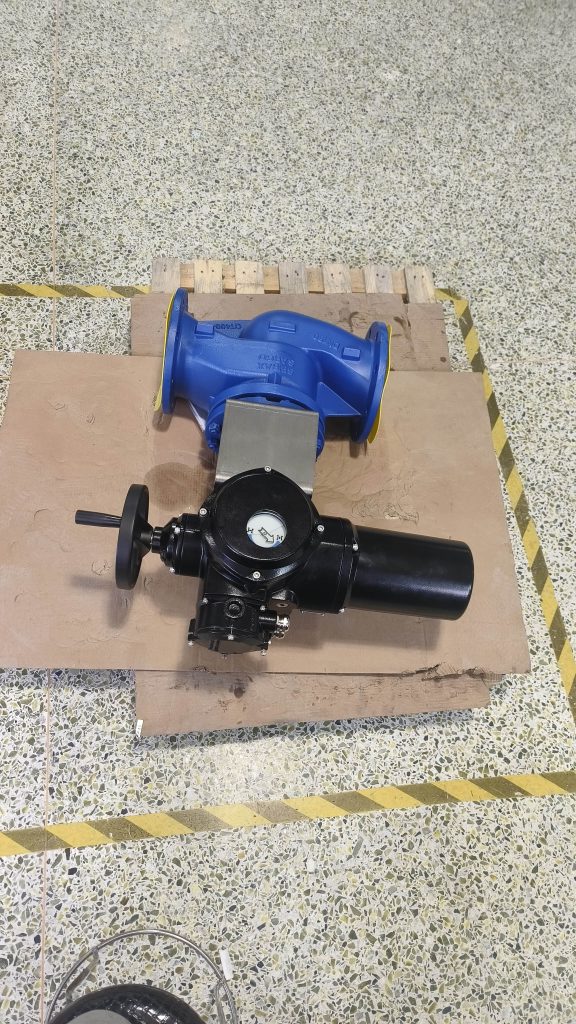
Design and Structure
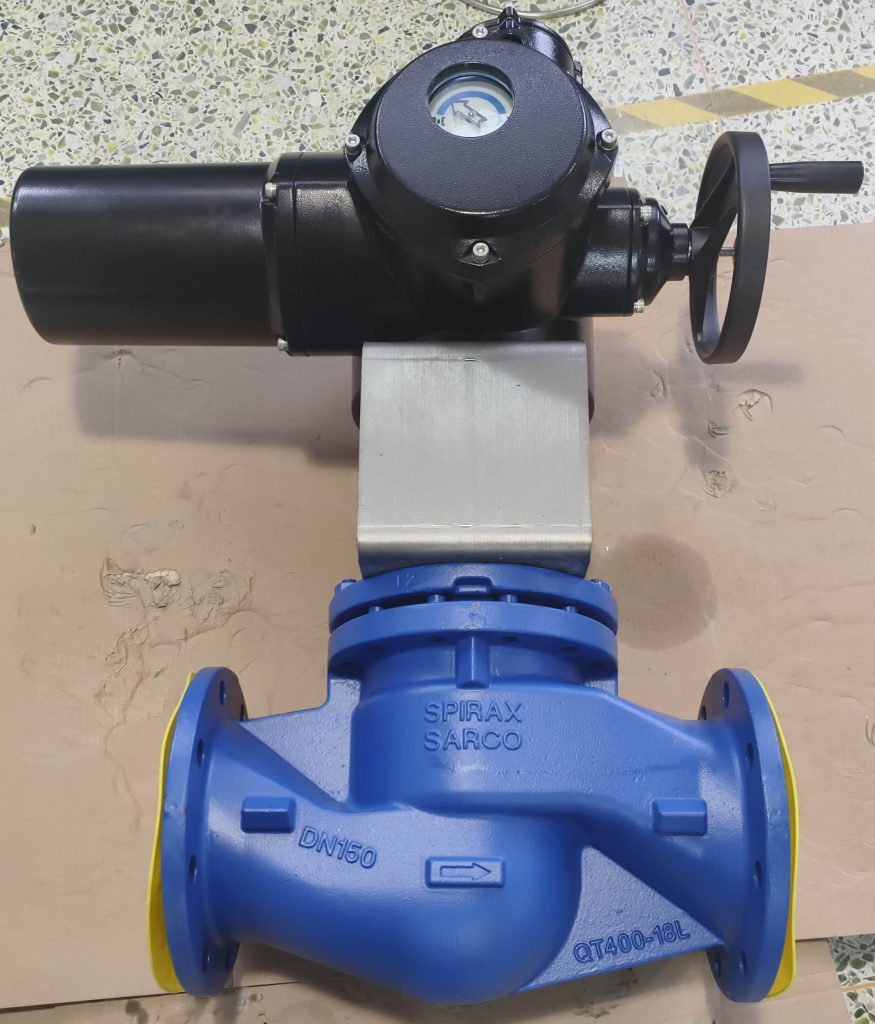
Electric globe valves consist of a spherical body with an internal baffle that directs fluid flow, creating a defined path. This design allows for effective throttling and flow regulation, which is particularly useful in applications where precise control is required. The valve features an electric actuator, which is responsible for opening and closing the valve by adjusting the position of the internal disc. The actuator receives signals from a control system, allowing for automated operation and real-time adjustments based on system requirements. The primary materials used in manufacturing electric globe valves include stainless steel, brass, and plastic. These materials are selected based on the application environment, as they must withstand varying pressures, temperatures, and corrosive substances. The choice of material not only impacts the valve’s durability but also its compatibility with the fluids being controlled.
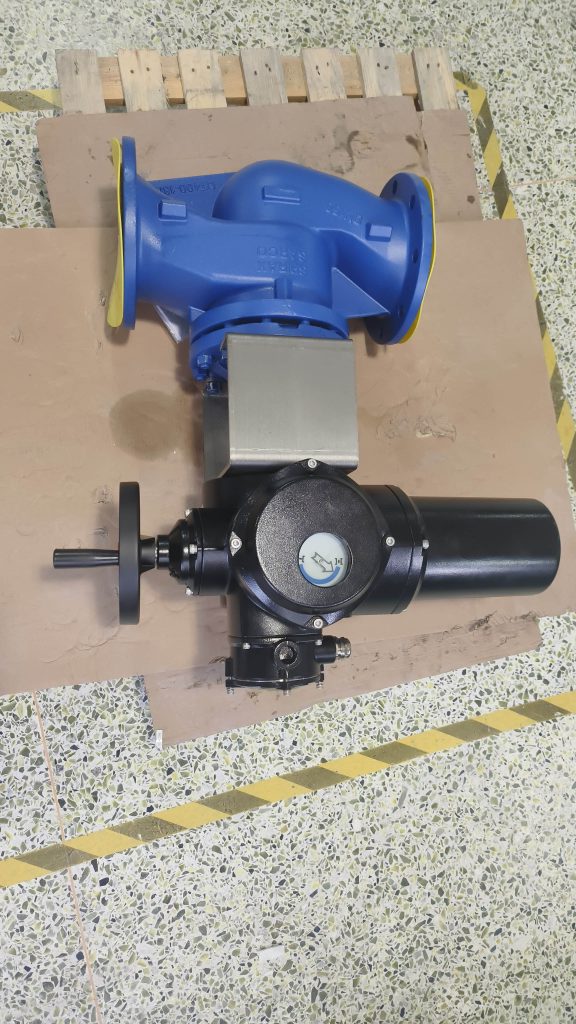