In the evolving landscape of industrial automation, the role of an electric two-seat regulating valve manufacturer is pivotal. These manufacturers are at the forefront of developing sophisticated valve technologies that enhance process control across a variety of sectors, including oil and gas, chemical processing, and water treatment. This article explores the key aspects of electric two-seat regulating valves, their benefits, and the current trends in the manufacturing industry.
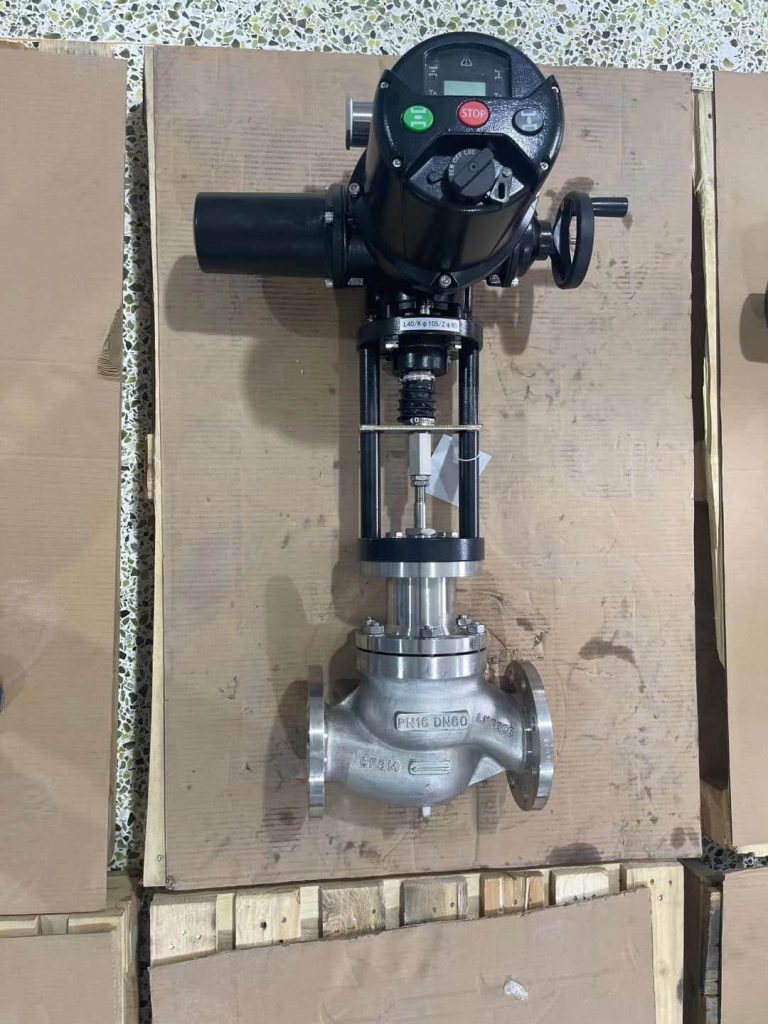
Electric two-seat regulating valves are designed to control the flow of fluids with high precision. Unlike traditional valves, these electric variants employ an electric actuator to adjust the valve position, enabling precise control over flow rates and pressure. The “two-seat” design refers to the presence of two seating surfaces that create a tight seal when closed, which helps in minimizing leakage and ensuring optimal performance. One of the primary advantages of electric two-seat regulating valves is their ability to provide consistent and accurate control. The electric actuator, which is powered by an electric motor, offers several benefits over pneumatic or hydraulic actuators. It allows for remote operation and integration with advanced control systems, making it easier for operators to manage complex processes from a centralized location. Additionally, electric actuators are known for their energy efficiency and lower maintenance requirements, as they do not rely on compressed air or hydraulic fluids.