In the realm of manufacturing, efficiency and precision have always been the driving forces behind technological innovation. One such innovation that has significantly transformed the way intricate metal components are produced is the Progressive Die. This ingenious tool and die system has revolutionized mass production, allowing for remarkable strides in productivity, cost-effectiveness, and quality control.
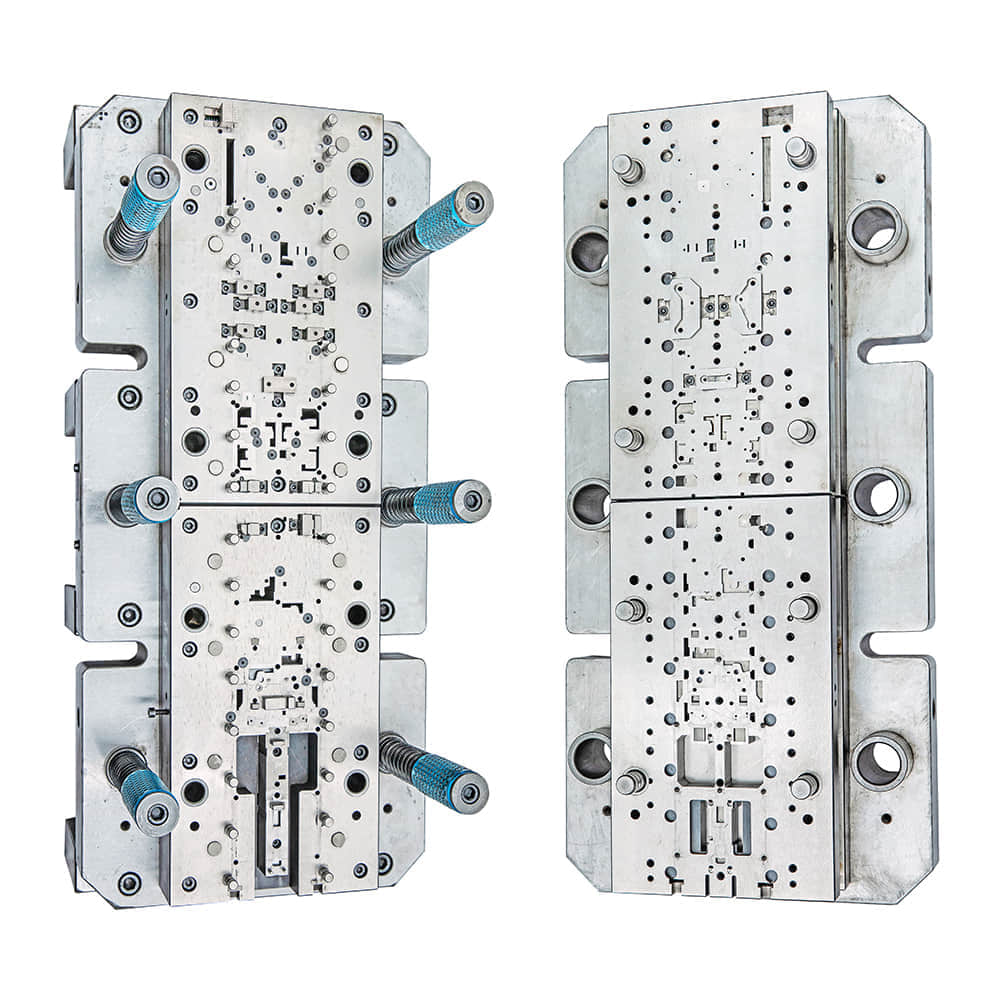
The concept of the Progressive Die is rooted in simplicity, yet its impact on manufacturing processes has been profound. Essentially, a Progressive Die is a specialized tool that performs a series of cutting, bending, and shaping operations on a metal strip as it moves through the machine. Unlike traditional methods that require multiple steps and setups, the Progressive Die integrates numerous functions into a single, streamlined operation. This integration not only drastically reduces production time but also minimizes human intervention, consequently diminishing the margin for errors.
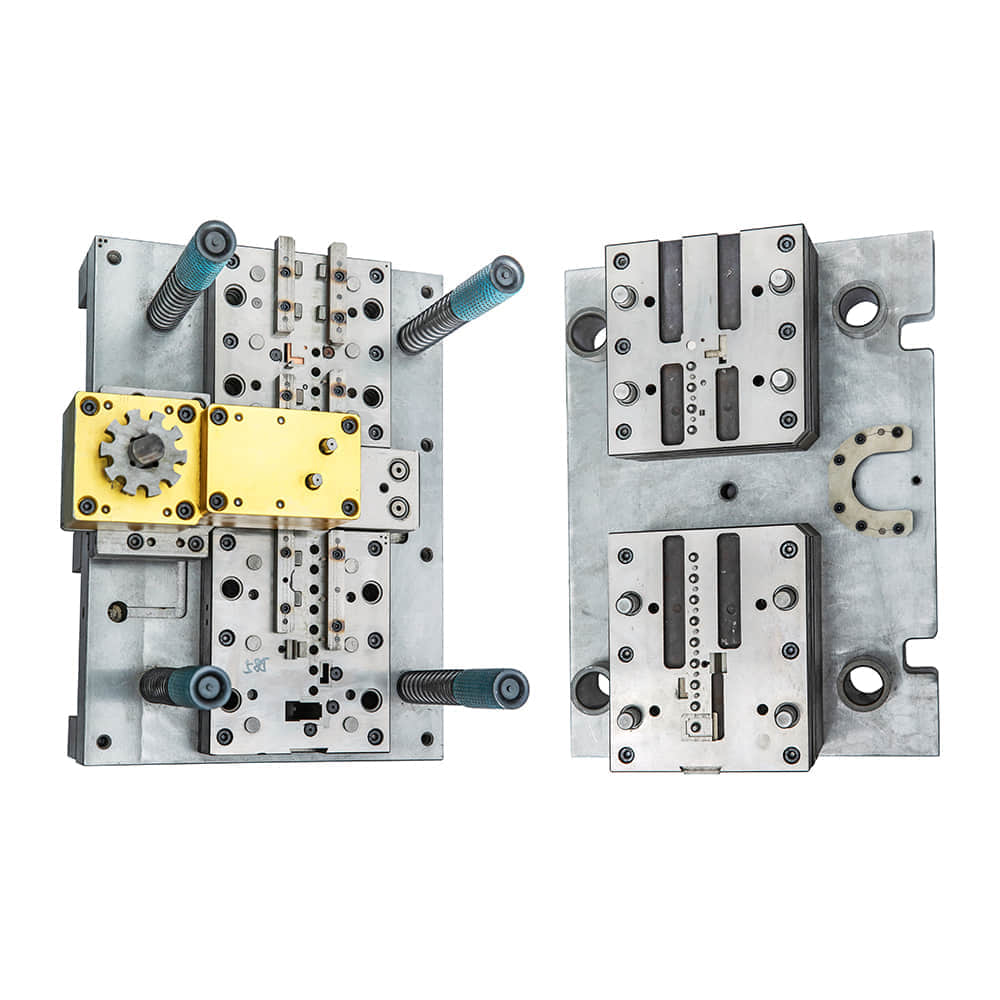
The genesis of Progressive Die technology dates back to the late 19th century when industries were seeking ways to produce complex parts with increased efficiency. However, it wasn’t until the mid-20th century that significant advancements in materials, machining techniques, and automation paved the way for the widespread adoption of Progressive Die systems. One of the most remarkable features of Progressive Die technology is its adaptability to various materials and component complexities. Whether it’s automotive parts, electronic components, or even everyday household items, Progressive Die systems can be fine-tuned to meet the unique specifications of each product. This versatility has not only fueled the growth of industries but has also contributed to the concept of “mass customization,” where products can be tailored to individual customer preferences on a larger scale. The integration of automation and computer numerical control (CNC) technology has further propelled the capabilities of Progressive Die systems. Modern systems can now be programmed to execute precise operations with incredible consistency. CNC integration allows for real-time adjustments, enhancing the accuracy of cuts and minimizing material waste. Additionally, the data collected during the production process can be analyzed to identify potential bottlenecks or areas for further optimization, enabling manufacturers to refine their processes continually. In the era of sustainability, Progressive Die technology plays a pivotal role in minimizing material wastage. Traditional manufacturing techniques often generate substantial scrap materials due to imprecise cuts or inefficient processes. However, the precision of Progressive Die systems significantly reduces such waste, contributing to both cost savings and environmentally conscious production practices. Despite its numerous advantages, the adoption of Progressive Die technology does come with its own set of challenges. The initial setup and design of the tooling can be complex and require a thorough understanding of both the manufacturing process and the end-product requirements. Moreover, regular maintenance and calibration are essential to ensure consistent quality and prolong the lifespan of the tooling. In conclusion, the evolution of Progressive Die technology stands as a testament to human ingenuity and our relentless pursuit of manufacturing excellence. From its humble beginnings as a concept to its current state as a cornerstone of mass production, the Progressive Die has transformed the landscape of modern manufacturing. Its ability to seamlessly integrate various processes, coupled with the power of automation and CNC technology, has propelled industries towards higher levels of efficiency, precision, and sustainability. As industries continue to evolve, one can only anticipate further innovations in Progressive Die technology that will shape the way we manufacture intricate components in the years to come.
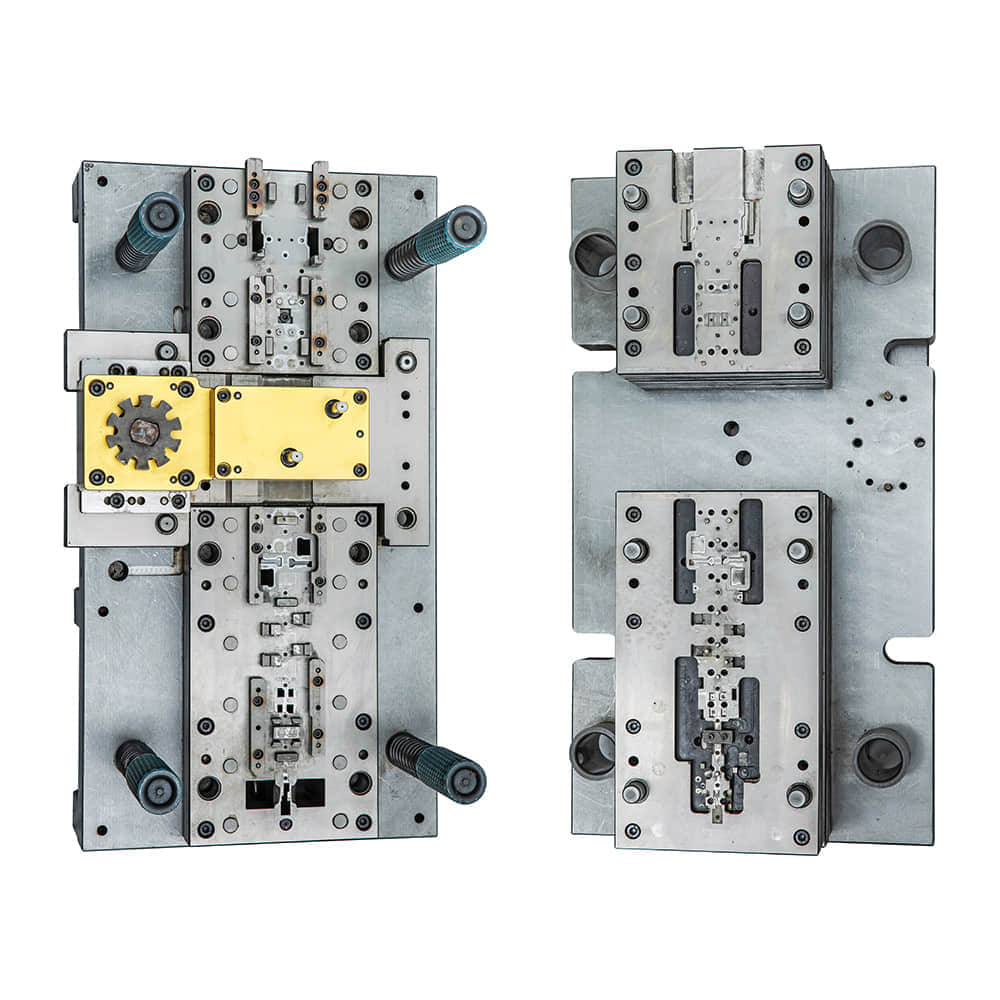