In today’s rapidly evolving industrial landscape, maintaining optimal air quality and equipment performance is of paramount importance. One essential component in this regard is the fan filter unit (FFU), which plays a pivotal role in filtering out contaminants and ensuring a clean environment within critical spaces such as cleanrooms, laboratories, and data centers. To ensure the efficacy and reliability of your FFUs, selecting the right fan filter supplier is crucial. In this article, we will explore key factors to consider when choosing a fan filter supplier.
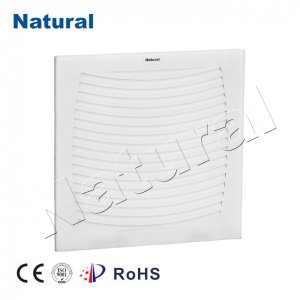
Quality Assurance: The first and foremost consideration when selecting a fan filter supplier is their commitment to quality assurance. Verify if the supplier adheres to international quality standards such as ISO 9001 and ISO 14001. This ensures that their products are manufactured and tested to meet stringent quality criteria, guaranteeing performance consistency. Product Range: Different applications demand different types of FFUs. Ensure that the supplier offers a diverse range of FFUs, including various sizes, filtration efficiencies, and mounting options. This versatility allows you to choose the most suitable FFU for your specific requirements. Customization Options: No two facilities are exactly alike, so having the option for customization is vital. A reliable fan filter supplier should be able to tailor their FFUs to fit your unique specifications, including size, airflow, and filtration efficiency. Customization ensures optimal performance and compatibility with your existing systems. Energy Efficiency: Energy consumption is a significant concern in today’s environmentally conscious world. Look for a supplier that offers energy-efficient FFUs. These units are designed to maximize airflow while minimizing energy consumption, resulting in lower operating costs and reduced environmental impact. Longevity and Reliability: FFUs are a long-term investment, so durability and reliability are paramount. Investigate the supplier’s track record and ask for references or case studies to ensure their FFUs have a history of longevity and minimal maintenance requirements. Technical Support: Even the best FFUs may encounter issues from time to time. Choose a supplier that offers comprehensive technical support, including troubleshooting assistance, maintenance guidance, and readily available spare parts. Compliance and Certification: Depending on your industry, specific compliance and certification requirements may apply. Ensure that the supplier’s FFUs meet the necessary industry standards and regulations, such as those for cleanroom classifications, fire safety, and electromagnetic compatibility (EMC). Cost Considerations: While cost is a critical factor, it should not be the sole determining factor. Balance the cost of FFUs with their quality and features to ensure that you are making a cost-effective, long-term investment. Warranty and Service Contracts: Investigate the supplier’s warranty policies and available service contracts. A robust warranty and service package can provide peace of mind and protect your investment. Customer Feedback: Finally, research customer feedback and reviews. The experiences of other customers can provide valuable insights into the supplier’s reputation, customer service, and product quality. In conclusion, choosing the right fan filter supplier is a crucial decision that directly impacts the performance and efficiency of your critical facilities. By considering factors such as quality assurance, product range, customization options, energy efficiency, longevity, technical support, compliance, cost, warranties, and customer feedback, you can make an informed choice that ensures clean, healthy, and efficient operations. Remember that investing in high-quality FFUs and a reliable supplier is an investment in the long-term success of your facility.