In recent years, Dimethyl Carbonate (DMC) injection has emerged as a revolutionary technique in various industrial processes. This versatile compound, DMC, is gaining traction for its eco-friendly attributes, efficiency, and cost-effectiveness. In this article, we will delve into the world of DMC injection and explore its significance in shaping the future of industrial applications.

The Rise of DMC Injection
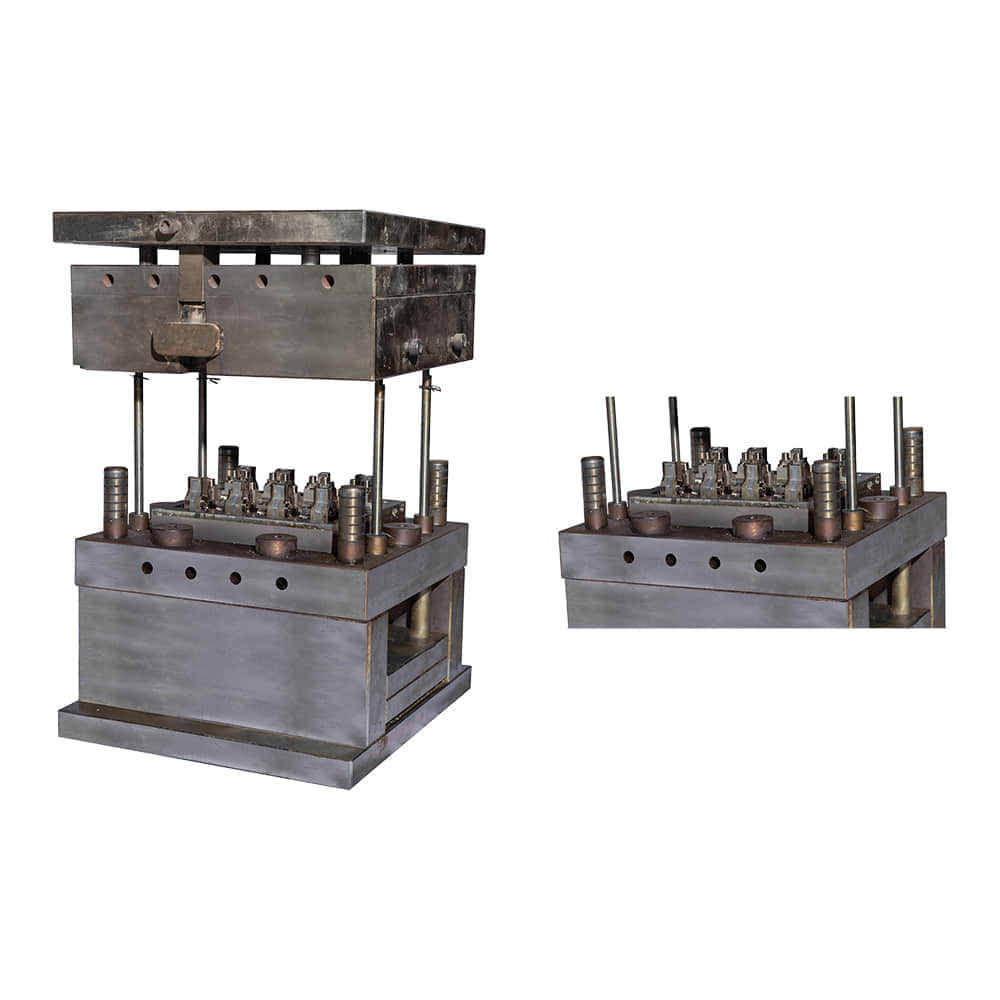
DMC, a clear, colorless liquid with a mild, pleasant odor, is a non-toxic and non-carcinogenic organic compound. It is produced by the oxidative carbonylation of methanol and carbon monoxide. Its low toxicity and environmental safety profile have made it a viable alternative to hazardous solvents and reagents in industrial processes. Eco-Friendly Advantages One of the most significant advantages of DMC injection is its environmental friendliness. Unlike traditional solvents and chemicals used in industrial processes, DMC is biodegradable and poses minimal risk to human health. It has a low volatile organic compound (VOC) content, reducing emissions and contributing to a cleaner atmosphere. As industries increasingly prioritize sustainability, DMC stands out as a responsible choice. Enhanced Process Efficiency DMC injection has the potential to optimize various industrial processes. It serves as a powerful solvent and reactant in applications such as: Polymer Production:DMC is used as a safer alternative to phosgene in the production of polycarbonates and polyurethanes, resulting in improved polymer quality and reduced environmental impact. Pharmaceuticals:In pharmaceutical manufacturing, DMC is employed as a solvent and reactant, replacing more toxic and less efficient alternatives. This not only ensures product safety but also streamlines production processes. Lithium-Ion Batteries:DMC plays a crucial role in the electrolyte formulation for lithium-ion batteries, enhancing battery performance and longevity. Cost-Effective Solution Aside from its environmental benefits, DMC injection also offers cost advantages. Its efficient use as a solvent and reactant leads to reduced waste and lower production costs. Additionally, its compatibility with existing industrial equipment minimizes the need for costly infrastructure changes, making it an economically viable option for many industries. Challenges and Future Prospects While DMC injection holds great promise, some challenges need to be addressed. These include the need for further research and development to expand its application areas and optimize production processes. Additionally, regulations and safety standards must be updated to reflect the growing use of DMC in industrial settings. Looking ahead, DMC injection is poised to become even more integral to sustainable industrial practices. As industries strive to meet environmental regulations and reduce their carbon footprint, DMC’s versatility, safety, and cost-effectiveness make it a valuable tool for achieving these goals. Conclusion DMC injection is a game-changer in industrial processes, offering eco-friendly advantages, enhanced process efficiency, and cost-effective solutions. Its rise marks a significant shift towards greener and more sustainable industrial practices. As research and development efforts continue, DMC is set to play an even more prominent role in shaping the future of industrial applications, making our world cleaner, safer, and more efficient.
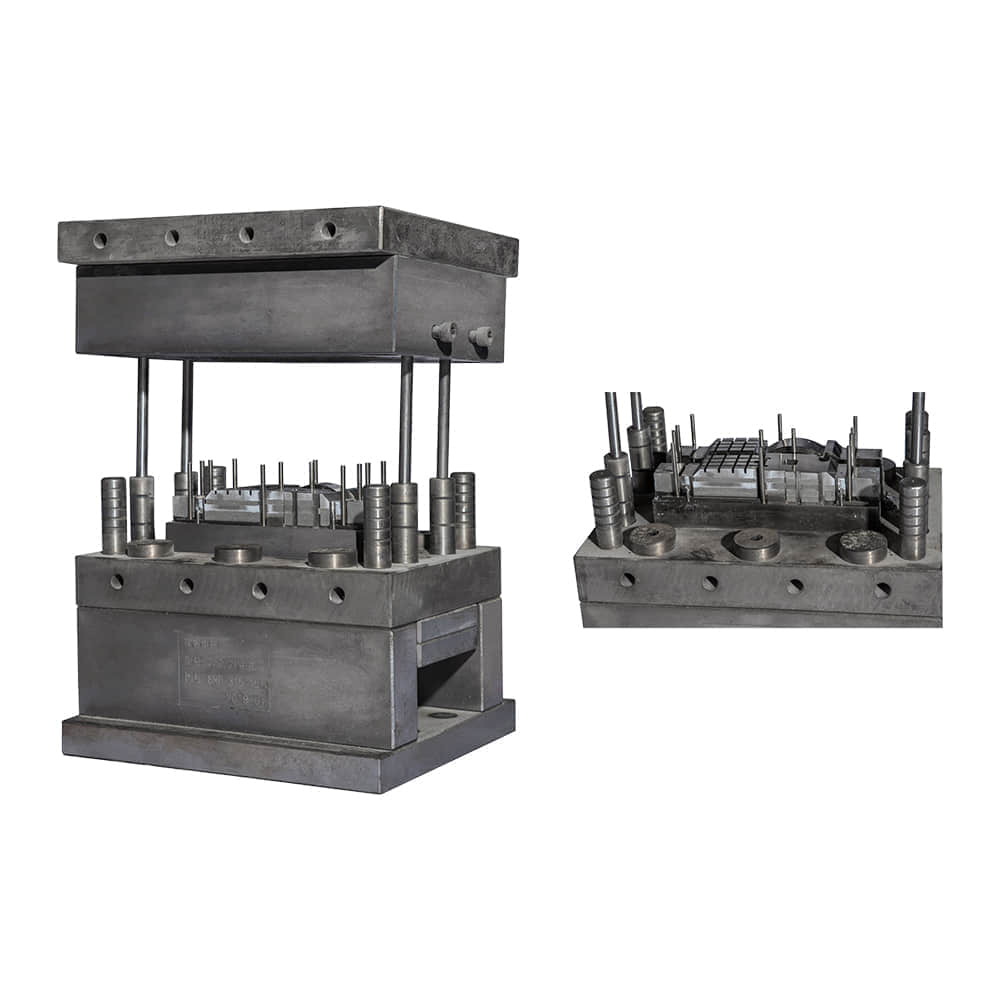