In the world of advanced manufacturing, BMC (Bulk Molding Compound) has emerged as a game-changing material known for its versatility, durability, and exceptional performance. BMC molding manufacturers are at the forefront of harnessing the potential of this composite material to create innovative and reliable products for a wide range of industries. In this article, we will delve into the world of BMC molding manufacturers, exploring their processes, applications, and the impact they have on various sectors.
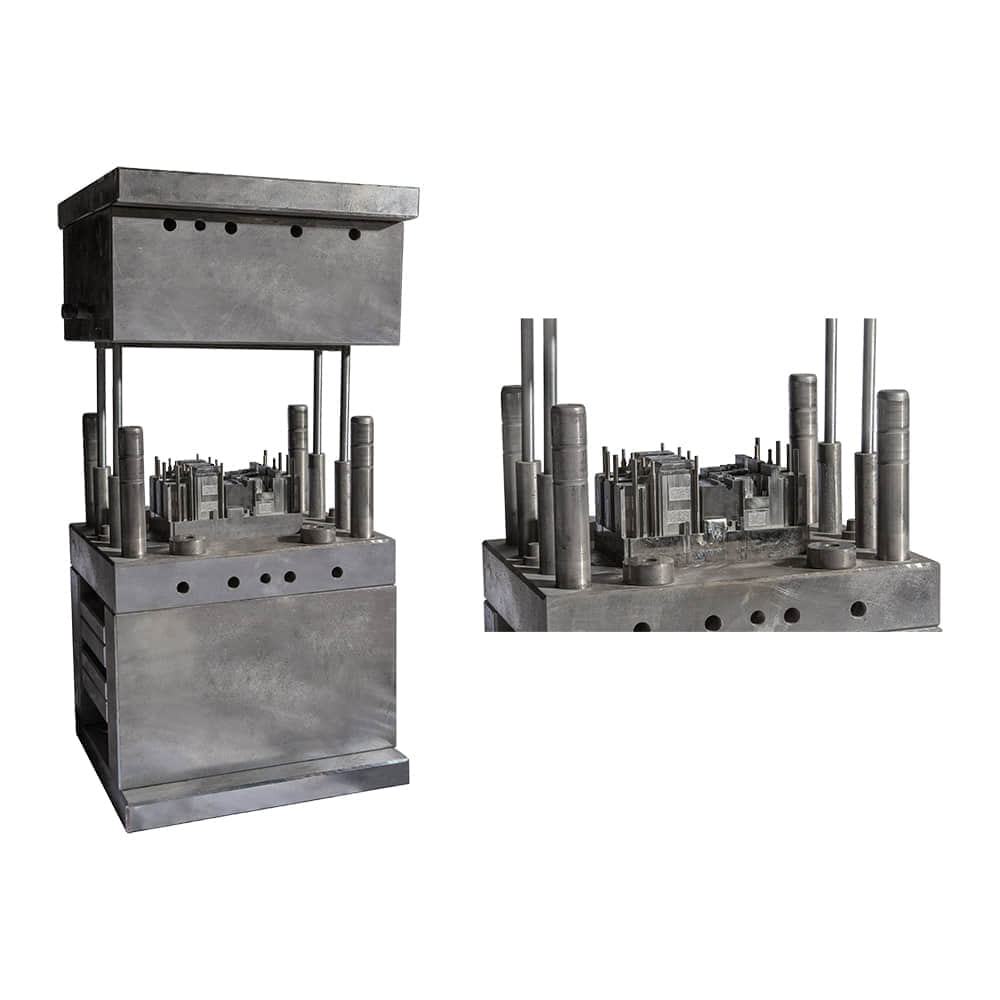
The Essence of BMC Molding
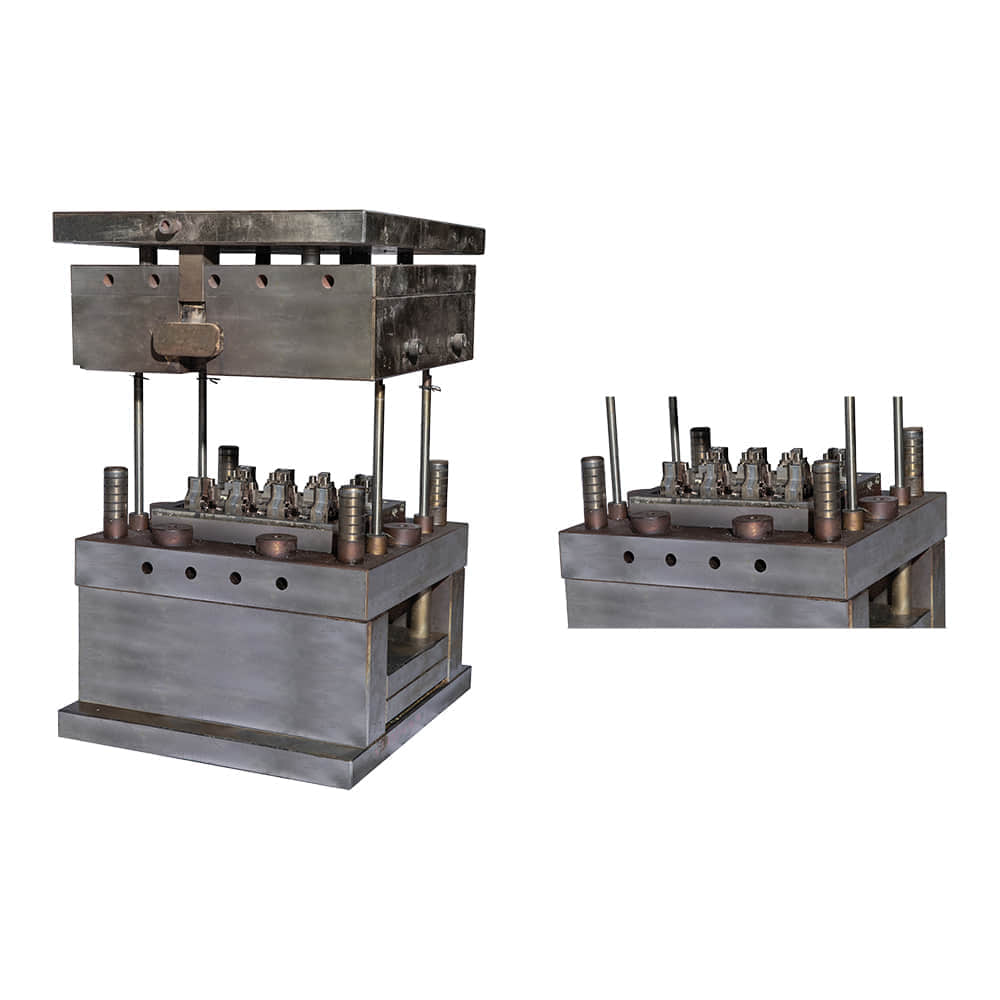
Bulk Molding Compound (BMC) is a composite material consisting of thermosetting resins, glass fibers, and various additives. This unique blend results in a material that exhibits outstanding mechanical, electrical, and thermal properties. BMC is particularly known for its high strength-to-weight ratio, resistance to corrosion, and dimensional stability. These properties make it an ideal choice for applications in demanding environments, where durability and performance are critical. Manufacturing Excellence BMC molding manufacturers are experts in the art and science of transforming BMC into precision-engineered components. The process begins with the careful selection and mixing of raw materials, ensuring that the BMC formulation meets the specific requirements of the intended application. Once the BMC is prepared, it undergoes a molding process where it is injected into molds under high pressure and temperature. The molding process is characterized by its ability to produce complex shapes with tight tolerances. Manufacturers employ cutting-edge machinery and advanced techniques to ensure the consistency and quality of each part they produce. This level of precision is particularly valuable in industries such as automotive, aerospace, and electrical, where safety and reliability are paramount. Diverse Applications The versatility of BMC makes it suitable for a wide array of applications across various industries. Automotive manufacturers utilize BMC for components like bumpers, engine covers, and electrical housings due to its lightweight yet robust nature. In the electrical and electronics sector, BMC is the material of choice for insulators, connectors, and switchgear components, thanks to its excellent electrical insulation properties. The aerospace industry benefits from BMC’s resistance to high temperatures and chemicals, employing it in the production of interior and exterior aircraft components. BMC’s corrosion resistance also makes it a preferred material for marine applications, where it is used in shipbuilding for components like radar domes and ventilation systems. Environmental Responsibility In addition to its performance advantages, BMC molding manufacturers are increasingly embracing environmental responsibility. BMC is a sustainable material choice as it can be recycled, reducing waste and environmental impact. Moreover, the production of BMC consumes less energy compared to some alternative materials, further contributing to its eco-friendly credentials. Meeting Industry Standards BMC molding manufacturers adhere to stringent industry standards and certifications to ensure the quality and safety of their products. These standards often vary by sector and application but may include ISO 9001 for quality management and ISO 14001 for environmental management. Compliance with these standards is a testament to the commitment of BMC molding manufacturers to delivering excellence in their products and processes. Conclusion In the world of advanced manufacturing, BMC molding manufacturers stand out as pioneers of excellence in the use of Bulk Molding Compound. Their ability to harness the unique properties of BMC and transform them into high-quality, precision-engineered components has far-reaching implications across numerous industries. From automotive to aerospace, electrical to marine applications, BMC molding manufacturers continue to shape the future by creating products that are not only durable and reliable but also environmentally responsible. As technology advances and innovation continues to drive the industry, BMC molding manufacturers will remain at the forefront of engineering solutions that redefine what is possible with composite materials.
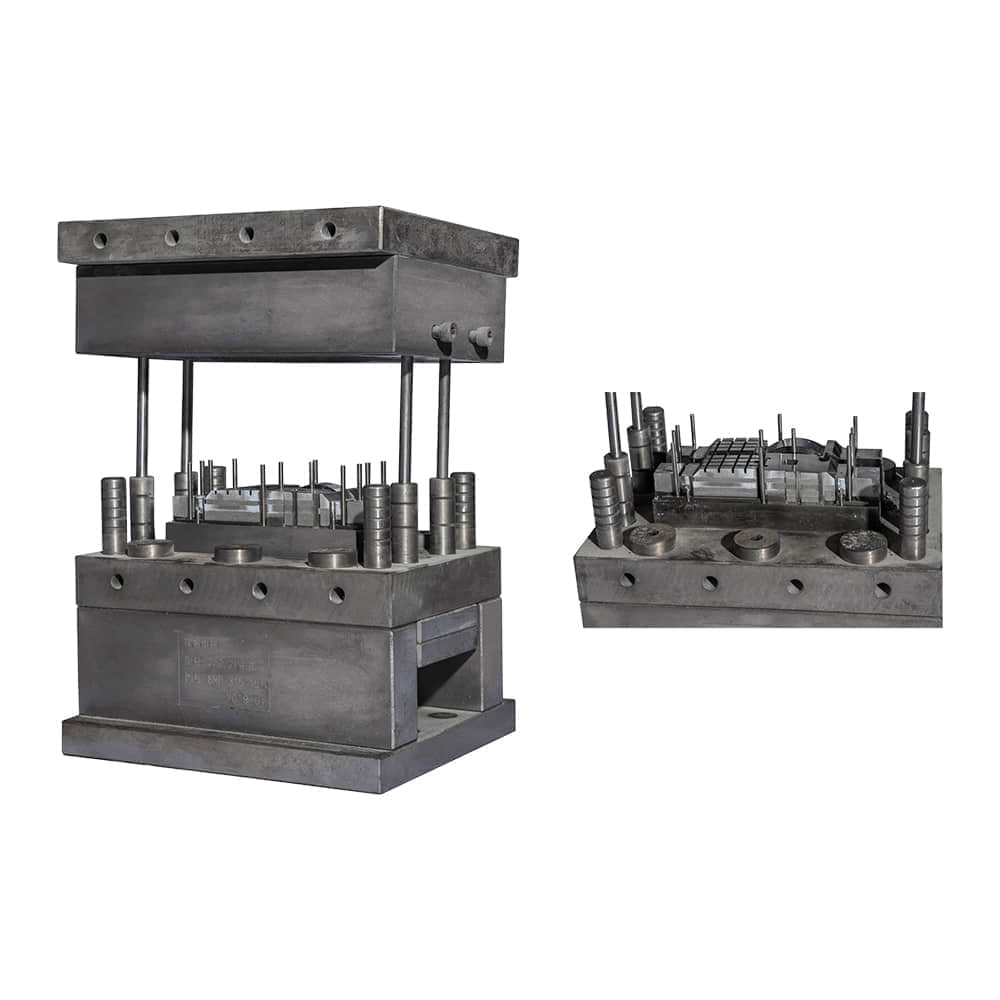