Introduction

In the realm of modern manufacturing, injection molding has emerged as a revolutionary process, enabling the creation of intricate and precise parts with remarkable efficiency. Injection molded parts have become indispensable across industries, from automotive and electronics to consumer goods and medical devices. This article delves into the world of injection molded parts, exploring their production process, benefits, and wide-ranging applications.
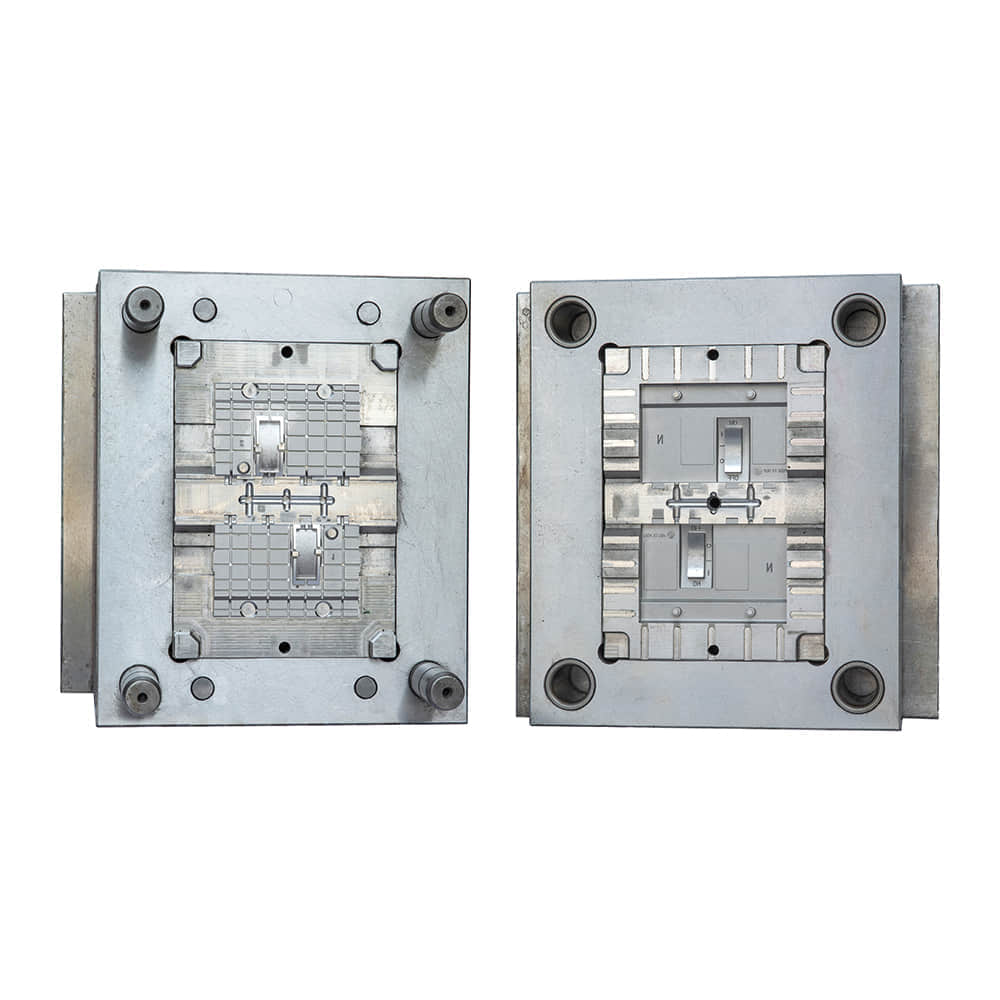
The Injection Molding Process Injection molding is a manufacturing process that involves injecting molten material, usually plastic, into a mold cavity. Once the material cools and solidifies, the mold is opened to reveal the final product. The process encompasses several key stages: material feeding, melting, injection, cooling, solidification, mold opening, and ejection. This cycle can be rapidly repeated, allowing for high-volume production with consistent quality. Advantages of Injection Molded Parts Precision and Complexity: Injection molding is known for its ability to produce highly detailed and complex parts with tight tolerances. The process allows for intricate features, such as thin walls, sharp corners, and fine textures, to be replicated accurately. This precision is crucial in industries where small deviations can lead to malfunctions or performance issues. Efficiency: The high automation potential of injection molding translates to increased efficiency. Once the initial setup is complete, the production process can run autonomously with minimal supervision. This efficiency reduces labor costs and speeds up production timelines. Material Variety: Injection molding is compatible with a wide range of materials, including various types of plastics, elastomers, metals, and even ceramics. This versatility enables manufacturers to select the optimal material for the desired properties, such as strength, flexibility, heat resistance, or conductivity. Cost-Effectiveness: Despite the initial tooling costs, injection molding becomes cost-effective in high-volume production runs. The speed of production, minimal material waste, and low labor requirements contribute to a lower cost per part over time. Surface Finish: Injection molded parts often exhibit a high-quality surface finish directly from the mold, reducing the need for additional finishing processes. This is particularly advantageous for parts with aesthetic or functional requirements. Applications of Injection Molded Parts Automotive Industry: Injection molding produces components ranging from interior panels and dashboards to intricate engine parts. Its precision and efficiency align with the automotive industry’s demands for both safety-critical and visually appealing parts. Electronics: The electronics sector benefits from injection molding for producing casings, connectors, and even micro-components for devices like smartphones and wearables. Medical Devices: Injection molded parts are integral to medical devices and equipment due to their ability to meet strict regulatory standards while offering customization options and tight tolerances required for surgical instruments and diagnostics. Consumer Goods: Everyday items such as packaging, toys, and kitchen utensils are often created using injection molding due to its ability to produce consistent, high-quality products quickly. Aerospace: In aerospace, where weight reduction and precision are paramount, injection molded parts find application in interior components, housings, and structural elements. Conclusion Injection molded parts have revolutionized modern manufacturing by offering unparalleled precision, efficiency, and versatility. The process’s ability to produce intricate designs with consistent quality makes it a cornerstone of various industries, from automotive to electronics and beyond. As technology advances and materials evolve, injection molding is likely to continue shaping the way products are designed and manufactured, driving innovation across a multitude of sectors.
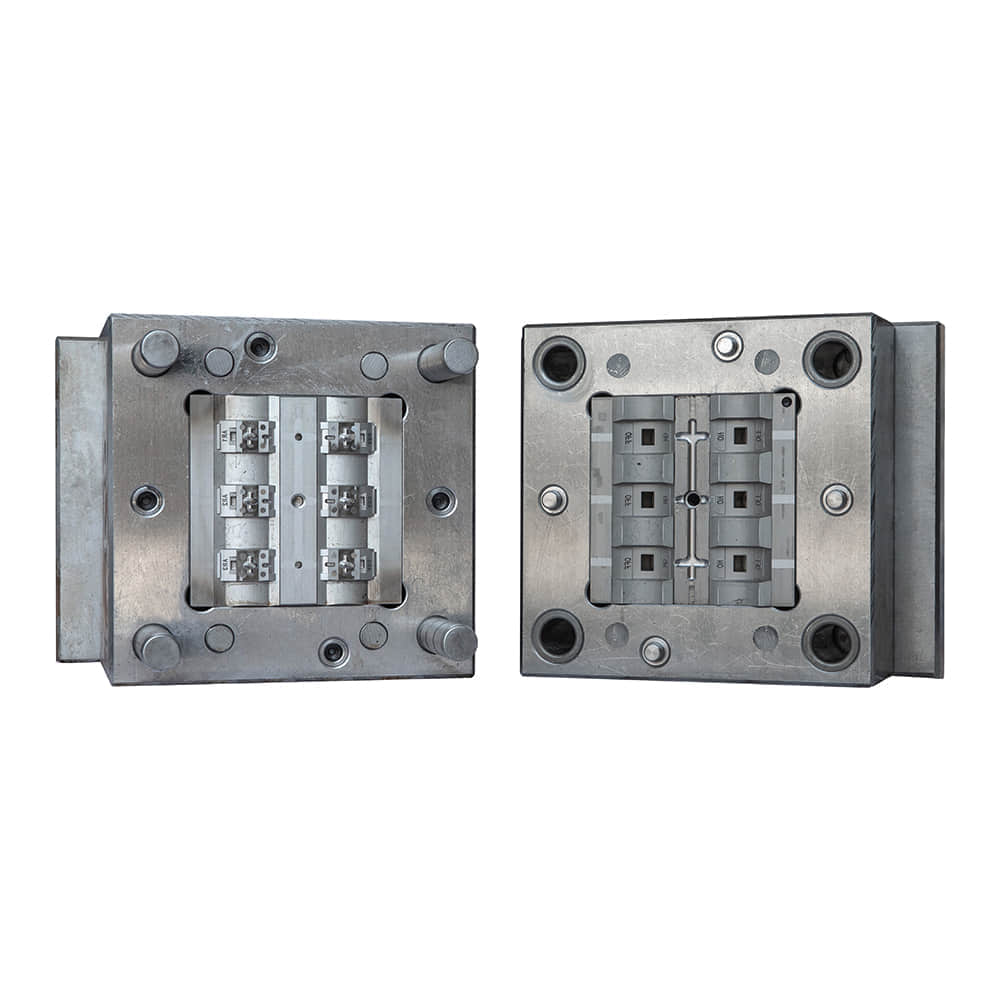