In the intricate world of metalworking, one industry stands out for its crucial role in shaping the modern manufacturing landscape: metal stamping die manufacturing. With a blend of artistry, engineering precision, and advanced technology, these manufacturers play a pivotal role in the creation of countless everyday items. This article delves into the realm of metal stamping die manufacturers, exploring their significance, the processes they employ, and the impact they have on various industries.
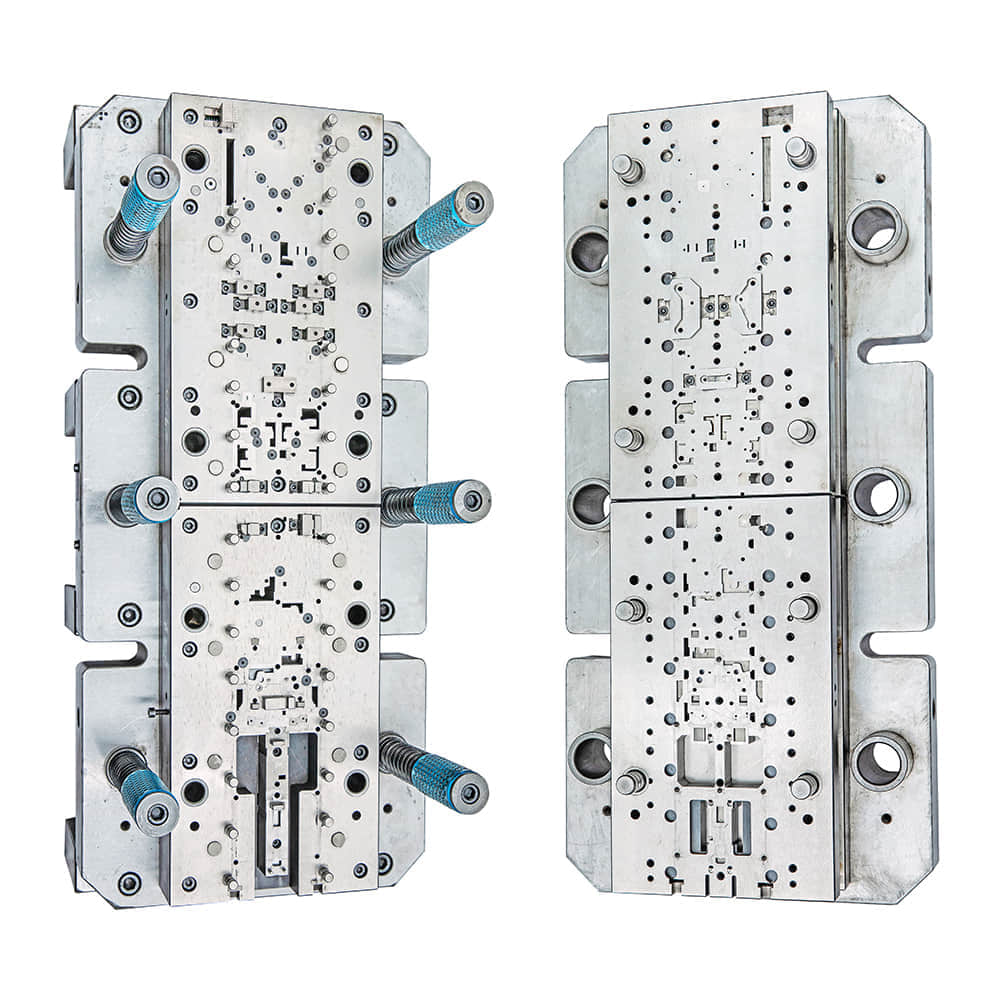
The Significance of Metal Stamping Die Manufacturers
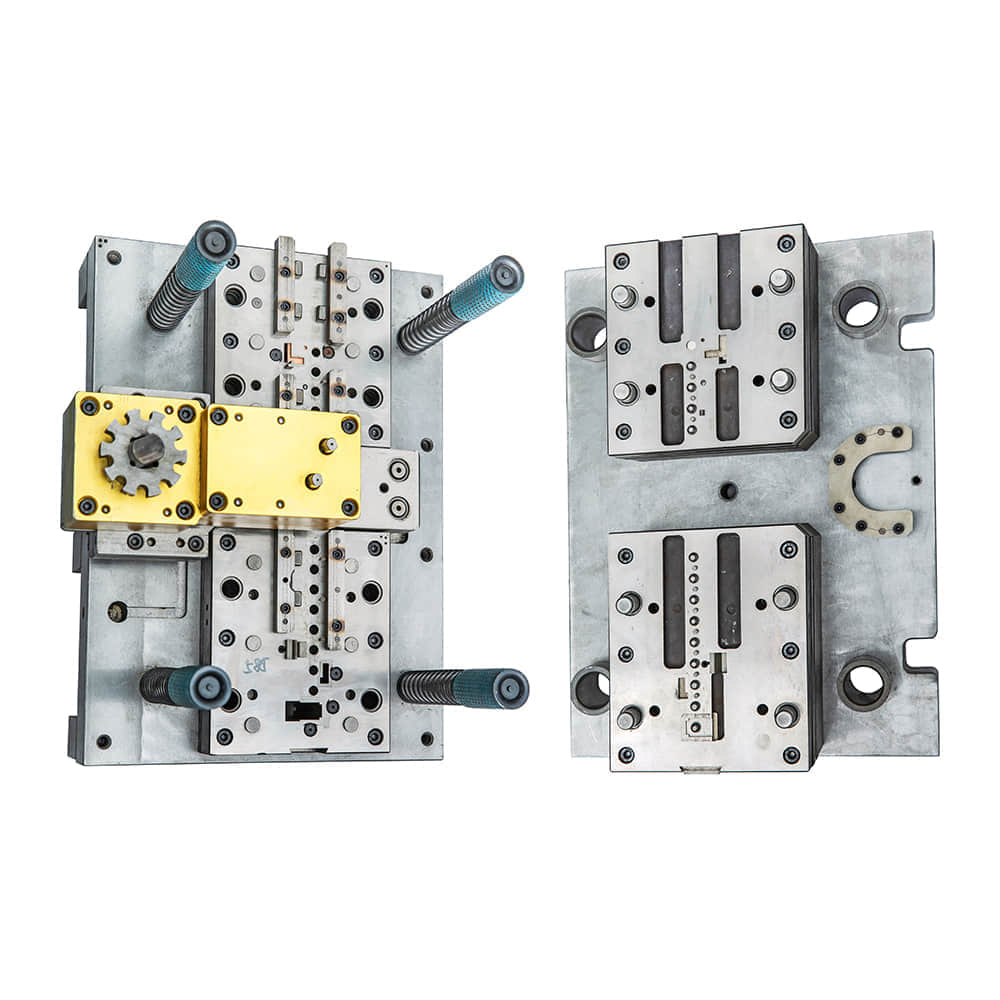
Metal stamping die manufacturers are the unsung heroes behind the scenes, responsible for producing the molds that shape metal sheets into diverse forms. These forms are the basis for numerous products, ranging from automobile parts to household appliances, electronics, and even aerospace components. This industry’s significance lies in its ability to provide cost-effective, high-volume production solutions without compromising on precision and quality. The Art of Precision Engineering Creating metal stamping dies is a blend of science and art. It requires intricate design skills, a deep understanding of metallurgy, and advanced engineering techniques. Manufacturers meticulously craft these dies to exact specifications, considering factors such as material properties, durability, and the intricacies of the final product. The precision engineering involved ensures that each piece manufactured is consistent, reliable, and adheres to the strictest tolerances. The Manufacturing Process The journey of a metal stamping die from concept to completion is a multi-step process that demands expertise and innovation: Design and Prototyping: Manufacturers collaborate with clients to understand their needs and specifications. Computer-aided design (CAD) software plays a crucial role in creating virtual prototypes, allowing for adjustments before physical production begins. Material Selection: Depending on the end application, manufacturers select appropriate metals with the desired properties, such as strength, malleability, and resistance to wear. Die Creation: Highly skilled toolmakers then craft the metal stamping dies using a combination of traditional machining techniques and modern technologies like computer numerical control (CNC) machining. Testing and Refinement: The initial prototypes are rigorously tested to ensure they meet the desired standards. Any necessary adjustments are made to enhance performance and precision. Production: Once the final prototype is approved, the metal stamping die enters full-scale production, where it is used to shape metal sheets into the desired forms through stamping presses. Quality Control: Quality control measures are implemented throughout the production process to identify and rectify any deviations from the desired specifications. Impact on Industries The products of metal stamping die manufacturers touch nearly every aspect of modern life. They provide essential components for industries such as automotive, aerospace, electronics, and home appliances. From the intricate parts of a smartphone to the structural components of an automobile, metal stamping dies enable the creation of complex shapes with unparalleled efficiency. Advancements and Future Trends As technology evolves, so does the field of metal stamping die manufacturing. Manufacturers are incorporating data-driven approaches, simulation software, and advanced materials to enhance precision, reduce lead times, and optimize the manufacturing process. Additionally, the industry’s focus on sustainability has led to the exploration of eco-friendly materials and energy-efficient processes. In conclusion, the world of metal stamping die manufacturing is a harmonious blend of creativity, engineering prowess, and technological innovation. These manufacturers silently shape the world around us, enabling the mass production of intricate and essential components that drive various industries. As technology continues to advance, so too will the capabilities of metal stamping die manufacturers, ensuring that the art of precision metalworking remains an integral part of our modern world.
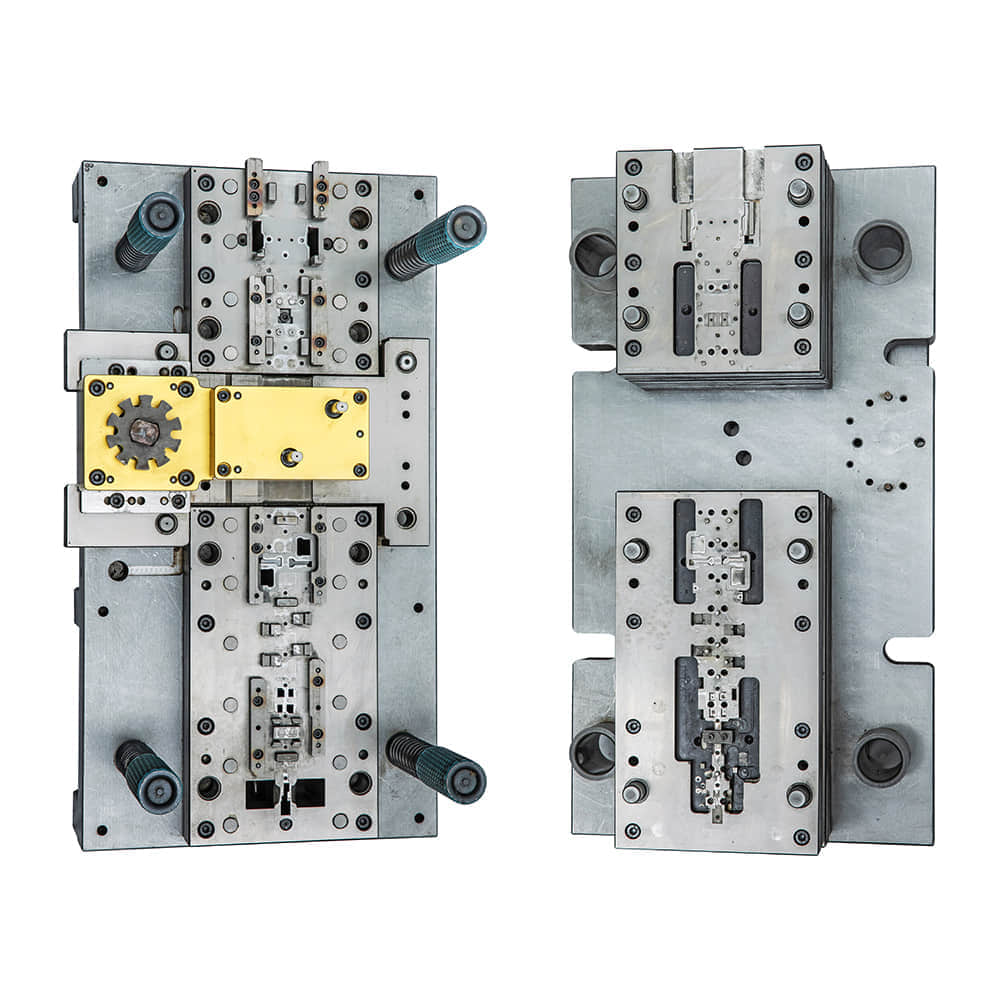