Moulded Case Circuit Breakers (MCCBs) are indispensable components in modern electrical systems. They serve as crucial safeguards against overloads and short circuits, ensuring the safety and reliability of electrical installations. In this article, we delve into the intricate world of MCCB manufacture, exploring the meticulous processes and cutting-edge technologies that contribute to their high quality and dependability.
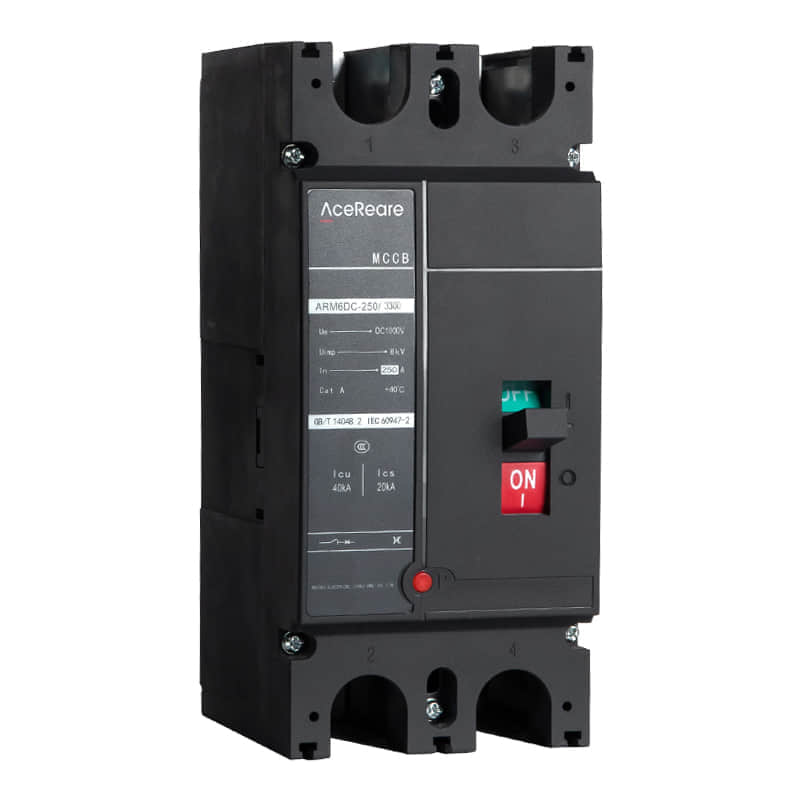
1. Design and Engineering
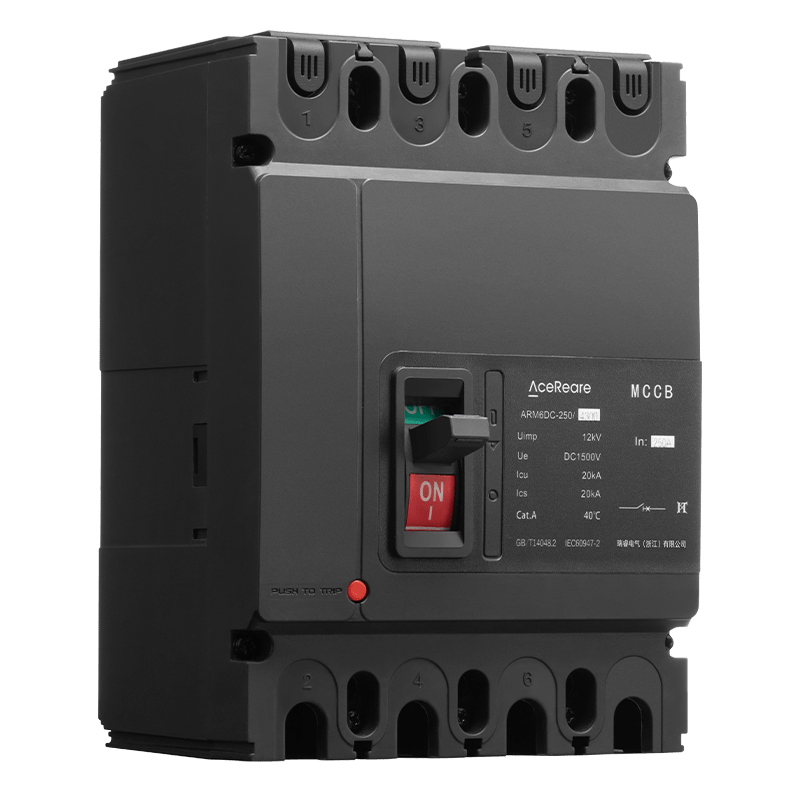
The journey of an MCCB begins with meticulous design and engineering. Skilled engineers meticulously plan the product’s specifications, from current ratings to breaking capacities, considering various electrical scenarios it may encounter during its service life. Advanced computer-aided design (CAD) tools assist in creating precise schematics and 3D models. 2. Material Selection The choice of materials is paramount in MCCB manufacture. High-quality, durable materials, such as thermosetting plastics for casings and contacts made from copper or silver alloys, are selected to ensure long-term performance and reliability. These materials can withstand the heat and electrical stresses that MCCBs are subjected to during operation. 3. Injection Molding Injection molding is a critical process in producing the outer casing of MCCBs. Molten thermosetting plastic is injected into molds, creating the MCCB’s rugged housing. This process ensures uniformity and precision in every unit produced, meeting the strict quality standards that MCCBs demand. 4. Precision Machining The internal components of an MCCB, including the contacts and arc chutes, require precision machining. Computer Numerical Control (CNC) machines cut, shape, and finish these components to exact specifications, ensuring optimal electrical and mechanical performance. 5. Assembly and Testing MCCB assembly is a delicate process. Highly trained technicians meticulously assemble the various components, ensuring that everything fits perfectly. After assembly, each MCCB undergoes rigorous testing. Comprehensive tests check parameters like tripping time, breaking capacity, and insulation resistance, guaranteeing that every MCCB meets industry standards. 6. Calibration and Quality Control Calibration is essential for MCCB accuracy. Highly sensitive instruments are used to calibrate the tripping mechanisms, ensuring that they operate within precise parameters. Quality control teams rigorously inspect each MCCB for visual defects, ensuring the final product is flawless. 7. Environmental Considerations MCCB manufacturers are increasingly mindful of environmental concerns. Many have adopted eco-friendly practices, including recycling and reducing the use of hazardous materials. Some MCCBs are designed to be easily disassembled for recycling at the end of their service life. 8. Research and Development The MCCB industry is dynamic, with continuous research and development efforts. Manufacturers invest in innovation to create MCCBs that are more efficient, compact, and intelligent. Features like adjustable trip settings and communication capabilities are examples of innovations that enhance MCCB functionality. 9. Compliance and Certification MCCB manufacturers adhere to international standards and regulations. Products must pass rigorous certification processes to ensure they are safe and reliable. Compliance with standards like IEC 60947-2 and UL 489 is critical for market acceptance. 10. Global Distribution MCCBs are in demand worldwide, and manufacturers distribute their products globally through extensive networks of distributors and partners. This ensures that these critical components are readily available to support electrical infrastructure everywhere. In conclusion, the manufacture of Moulded Case Circuit Breakers is a complex and highly specialized process that requires precision engineering, quality materials, rigorous testing, and a commitment to environmental responsibility. MCCBs play a pivotal role in safeguarding electrical systems, and the dedication of manufacturers to producing high-quality MCCBs is essential for ensuring the safety and reliability of our modern world. As technology continues to advance, we can expect even more innovative and efficient MCCBs to emerge, further enhancing the protection of our electrical infrastructure.
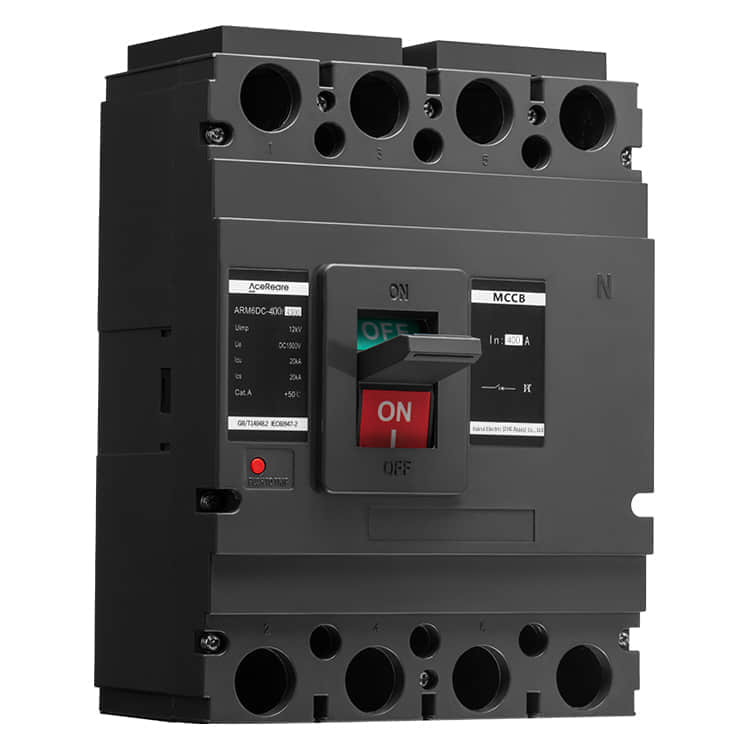