In industrial settings, safety is paramount. Whether it’s in a chemical plant, oil refinery, or any other hazardous environment, maintaining the right temperature is crucial for both safety and operational efficiency. This is where Hazardous Area Thermostats come into play, ensuring that critical equipment operates within specified temperature ranges while minimizing the risk of explosions or fires. In this article, we will delve into the world of Hazardous Area Thermostats, exploring their importance, applications, and key features.
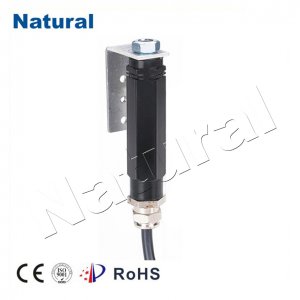
Importance of Hazardous Area Thermostats Hazardous areas, classified as zones with the potential for explosive atmospheres, pose unique challenges. In such environments, flammable gases, vapors, or dust can ignite if exposed to heat sources or electrical equipment. Controlling temperature within these zones is essential to prevent accidents and protect personnel and assets. Hazardous Area Thermostats are specifically designed to meet the stringent safety requirements of these environments. They play a pivotal role in maintaining the temperature of critical equipment, ensuring that it operates within safe limits. By preventing overheating or excessive cooling, these thermostats mitigate the risk of fires or explosions, safeguarding both people and assets. Applications of Hazardous Area Thermostats Hazardous Area Thermostats find application in various industries, including: Oil and Gas:In drilling rigs, refineries, and petrochemical plants, Hazardous Area Thermostats regulate the temperature of equipment such as pumps, compressors, and heat exchangers. Chemical Processing:Ensuring precise temperature control in chemical reactors and storage tanks is vital to prevent reactions or leaks. Hazardous Area Thermostats are indispensable in this regard. Mining:Mines often contain explosive gases and dust. Thermostats are used to maintain safe operating temperatures for machinery and electrical components. Food and Beverage:Hazardous Area Thermostats are used in food processing facilities, where combustible dust or gases are present, to control the temperature of ovens, dryers, and refrigeration units. Pharmaceuticals:In pharmaceutical manufacturing, maintaining strict temperature control is critical to ensuring the quality and safety of products. Key Features of Hazardous Area Thermostats Hazardous Area Thermostats are engineered with unique features to meet the demanding requirements of hazardous environments: Explosion-Proof Housing:They are housed in explosion-proof enclosures that can withstand and contain any internal explosion, preventing it from spreading to the surrounding area. ATEX or UL Certification:These thermostats are certified to meet international safety standards, such as ATEX in Europe or UL in the United States. Temperature Sensing:Advanced temperature sensors, such as RTDs or thermocouples, are used to provide accurate and reliable temperature measurements. Adjustable Set Points:Users can customize temperature set points to ensure equipment operates within safe limits for specific processes. Remote Monitoring:Many models offer remote monitoring capabilities, allowing operators to track temperature conditions from a safe distance. Fail-Safe Mechanisms:In the event of a malfunction, these thermostats often have fail-safe features to shut down equipment or trigger alarms. Corrosion Resistance:Hazardous Area Thermostats are built to withstand corrosive environments, ensuring long-term reliability. In conclusion, Hazardous Area Thermostats are indispensable tools for industries operating in potentially explosive atmospheres. They play a crucial role in maintaining safe operating temperatures, protecting both personnel and assets. With their explosion-proof designs, international certifications, and advanced features, these thermostats are vital components in ensuring safety and efficiency in hazardous environments. Properly selected and maintained, they contribute to smoother operations and peace of mind for industries where safety is paramount.