In the realm of modern manufacturing, where precision, efficiency, and quality are paramount, the progressive die stands as a testament to human ingenuity and technological progress. This innovative tool has revolutionized the production process across various industries, from automotive to electronics, by streamlining operations and enhancing product quality. In this article, we delve into the intricacies of progressive die technology, its benefits, and the ways it continues to shape the future of manufacturing.
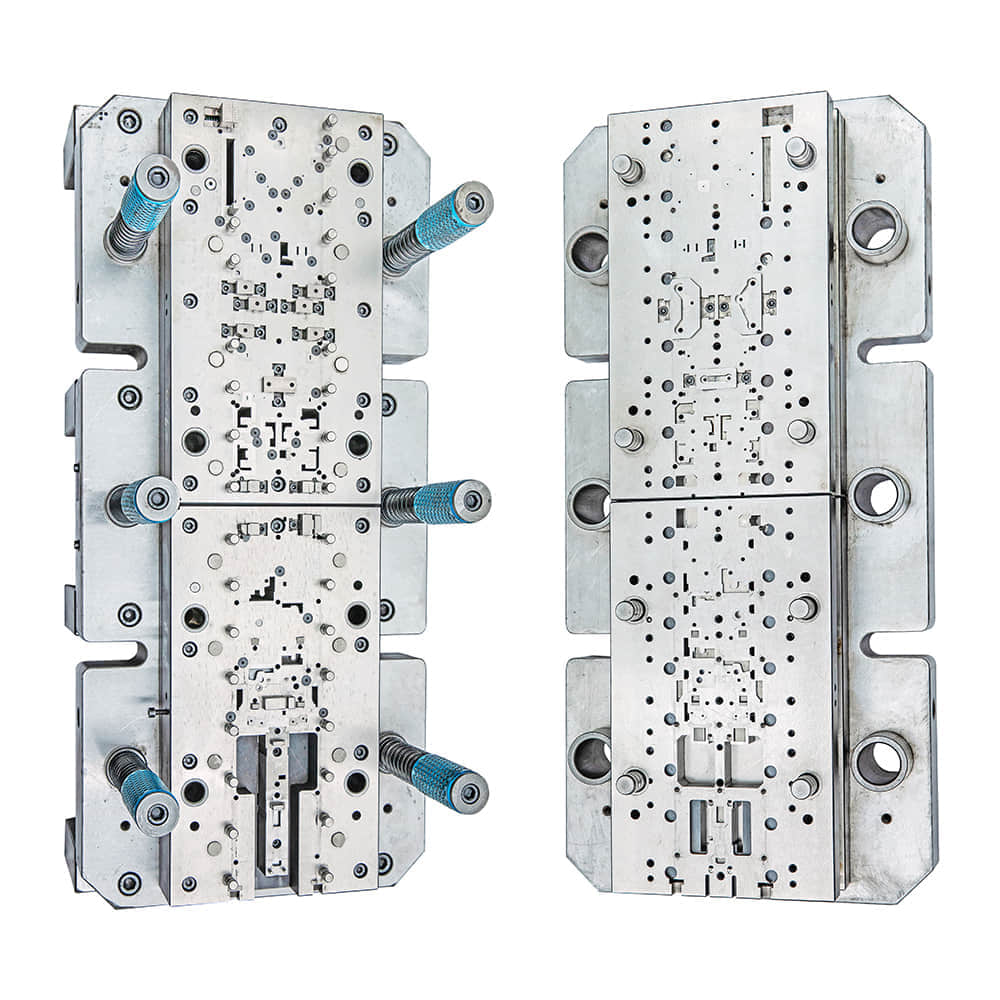
A Glimpse into Progressive Die Technology
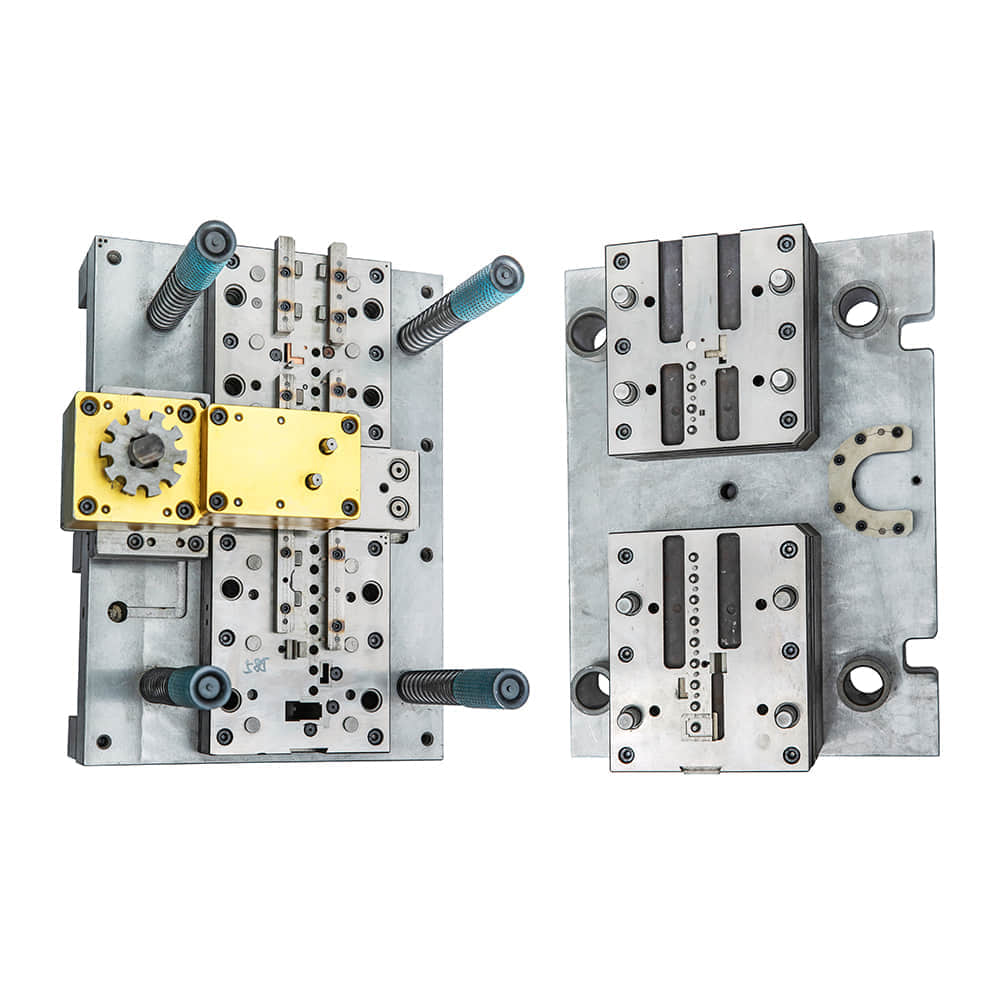
At its core, a progressive die is a specialized tool used in metalworking to efficiently cut, shape, and transform sheet metal into a desired product or component. What sets progressive die technology apart is its ability to perform a sequence of operations in a continuous manner, progressively advancing the metal sheet through a series of stations, each carrying out a specific task. These tasks can include cutting, punching, bending, and forming. The concept of the progressive die dates back to the late 19th century, but it wasn’t until the mid-20th century that significant advancements propelled it into the spotlight. The integration of computer numerical control (CNC) technology, along with improvements in materials and machining processes, revolutionized the capabilities of progressive dies, making them more versatile, precise, and reliable. The Advantages of Progressive Die Technology Enhanced Efficiency: One of the primary advantages of progressive die technology is its efficiency. By integrating multiple operations into a single tool and automating the process, manufacturers can significantly reduce production time and labor costs. Consistent Precision: Progressive dies are engineered with high precision, ensuring that each operation is carried out with accuracy and consistency. This results in components that meet tight tolerances and adhere to strict quality standards. Cost-Effectiveness: Despite the initial investment required for tooling and setup, progressive die technology proves to be cost-effective in the long run due to its high production rates and minimal scrap waste. Reduced Material Waste: Traditional manufacturing methods often result in substantial material wastage. Progressive die technology minimizes this waste by optimizing the layout of parts on the sheet, maximizing material utilization. Design Flexibility: With computer-aided design (CAD) software and CNC machining, progressive dies can accommodate complex part geometries and intricate designs, providing manufacturers with greater design flexibility. Innovations Shaping the Future As industries continue to evolve, progressive die technology remains at the forefront of innovation. Several trends are currently shaping the future of this technology: Smart Manufacturing: The integration of Internet of Things (IoT) devices and sensors into progressive die machinery allows for real-time monitoring and data collection. This enables manufacturers to optimize processes, predict maintenance needs, and enhance overall efficiency. Additive Manufacturing Integration: Additive manufacturing, or 3D printing, is being integrated with progressive die technology to create hybrid processes that leverage the strengths of both methods. This leads to reduced lead times for tooling and increased design complexity. Materials Advancements: New materials with improved strength, durability, and formability are emerging. Progressive die technology is adapting to accommodate these materials, expanding its range of applications. Miniaturization and Micro-Forming: The demand for smaller, more intricate components is driving the development of micro-forming techniques within progressive die technology. This is particularly relevant in industries like electronics and medical devices. Conclusion Progressive die technology has come a long way since its inception, propelling manufacturing processes to new heights of efficiency and quality. With its ability to perform multiple operations in a single pass, coupled with ongoing technological advancements, it continues to be an essential tool across a wide spectrum of industries. As innovations such as smart manufacturing, additive manufacturing integration, and materials advancements continue to shape the landscape, the future of progressive die technology appears brighter than ever.
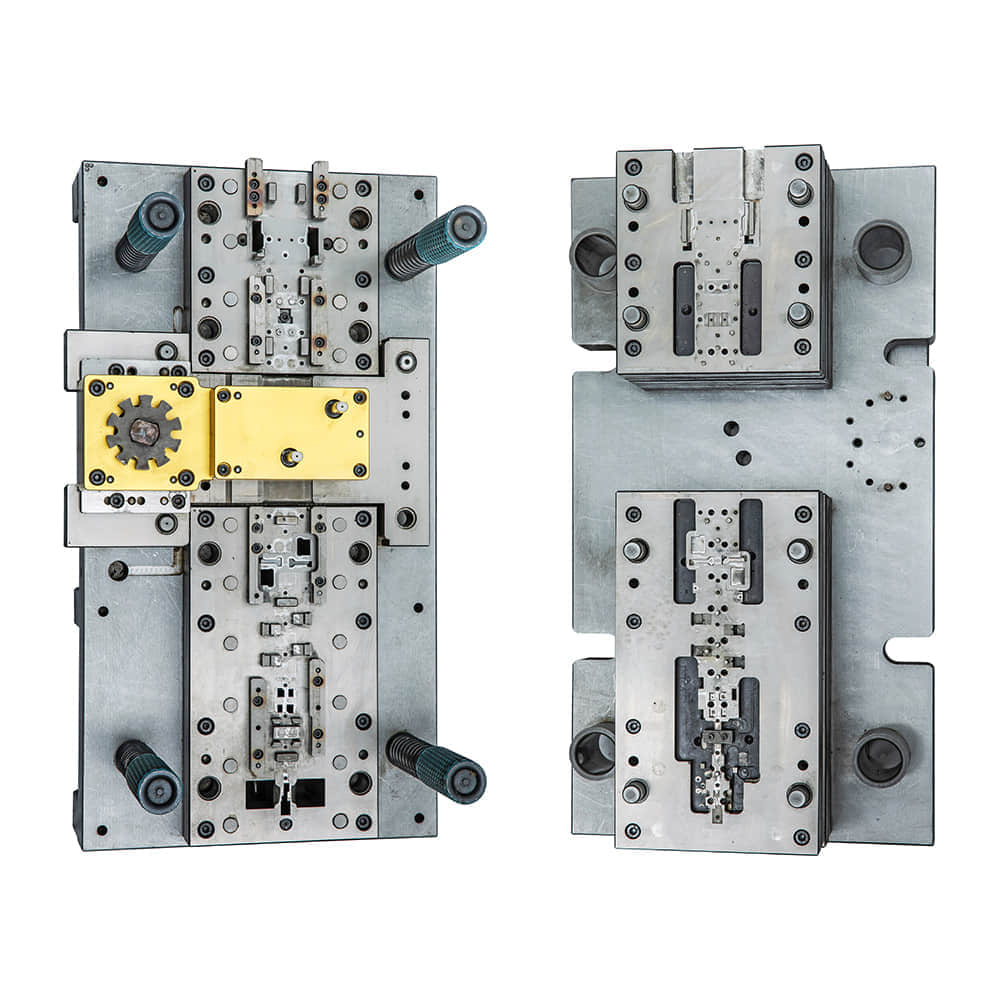