In the realm of advanced manufacturing, where precision, innovation, and quality converge, BMC Molding Manufacturers have carved an indelible niche for themselves. With a steadfast commitment to excellence, these manufacturers have become synonymous with cutting-edge technology, impeccable craftsmanship, and unmatched reliability. This article delves into the realm of BMC molding manufacturing, exploring its significance, processes, and the impact it has on various industries.
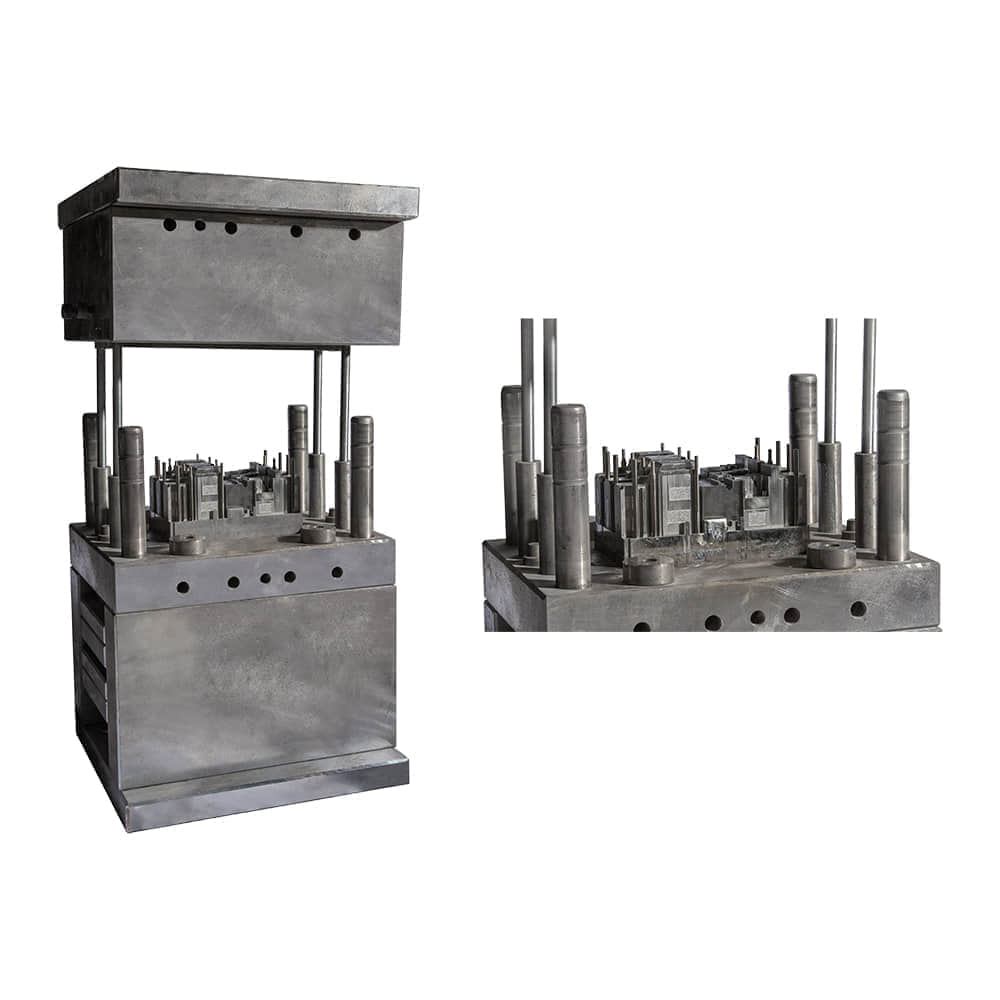
The Essence of BMC Molding Manufacturing
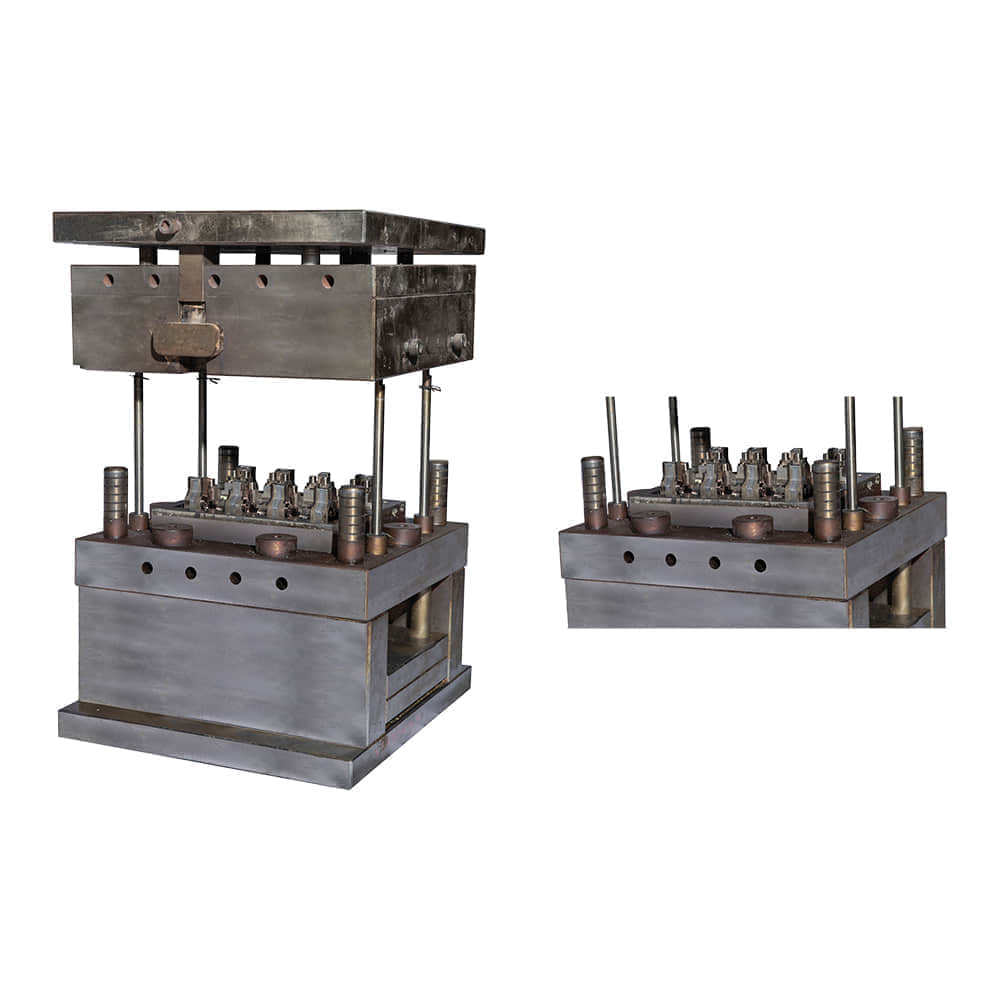
BMC, or Bulk Molding Compound, is a versatile material widely utilized in the production of intricate components for a range of applications, from automotive and aerospace to electrical and consumer goods. What sets BMC apart is its exceptional blend of strength, heat resistance, and dimensional stability. These attributes make it an ideal choice for manufacturing intricate parts that demand a high level of precision and durability. Precision Redefined: The Manufacturing Process At the heart of BMC molding manufacturing lies an intricate process that seamlessly blends science and art. The process begins with the meticulous mixing of various raw materials including resin, glass fibers, fillers, and additives. This concoction is then compressed and shaped according to the desired specifications using specialized machinery. The blend is subjected to intense heat and pressure within a mold, causing it to cure and solidify into the final product. What emerges is a component that boasts not only exceptional mechanical properties but also a flawless finish. The precision achievable through BMC molding manufacturing is unparalleled, meeting the exacting demands of industries where even the slightest deviation can have far-reaching consequences. Versatility and Impact The versatility of BMC molding manufacturing is a testament to its importance across diverse industries. In the automotive sector, BMC components find their way into critical parts such as brake systems and engine compartments, contributing to the overall safety and performance of vehicles. The aerospace industry benefits from BMC’s lightweight yet rugged nature, employing it in the creation of interior components and structural elements. Moreover, BMC’s excellent electrical insulation properties make it a preferred choice for electrical enclosures and insulators. Even the realm of consumer goods is touched by BMC molding, as it facilitates the production of intricately designed appliance parts and housings. Innovation at the Core BMC molding manufacturers are at the forefront of innovation, constantly pushing the boundaries of what’s possible. From incorporating advanced automation for enhanced precision to the development of novel composite materials that further elevate performance, these manufacturers are relentless in their pursuit of excellence. In addition, sustainable practices have taken center stage. Many BMC molding manufacturers are embracing eco-friendly materials and processes, reducing their carbon footprint while maintaining the highest quality standards. This commitment to sustainability not only resonates with environmentally conscious consumers but also aligns with global initiatives aimed at a greener future. Conclusion In the intricate tapestry of modern manufacturing, BMC molding manufacturers stand out as beacons of precision, innovation, and quality. Their mastery over the BMC molding process, coupled with their unwavering commitment to excellence, has shaped industries and driven progress. As technology continues to evolve, we can only anticipate that these manufacturers will lead the charge, continually raising the bar for what is achievable in the realm of advanced manufacturing.
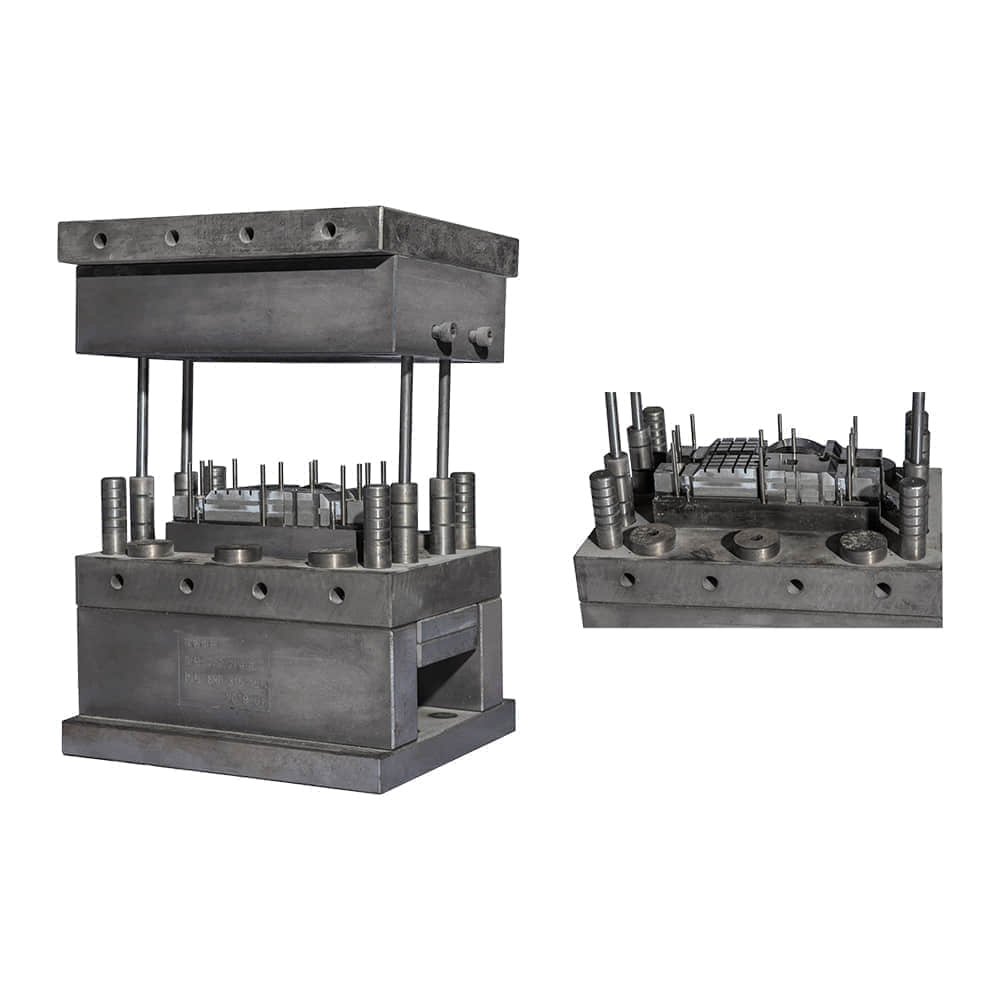