The Stainless Steel Electric Clamp Butterfly Valve is a high-quality valve designed for precise control and reliable performance in various industrial applications. Combining durability, efficiency, and automation, it is widely used in industries like water treatment, chemical processing, food and beverage, HVAC systems, and many others. This article explores the features, advantages, and applications of the Stainless Steel Electric Clamp Butterfly Valve, while focusing on how automation solutions from HeLi Automation (合力自动化) enhance its performance and reliability.
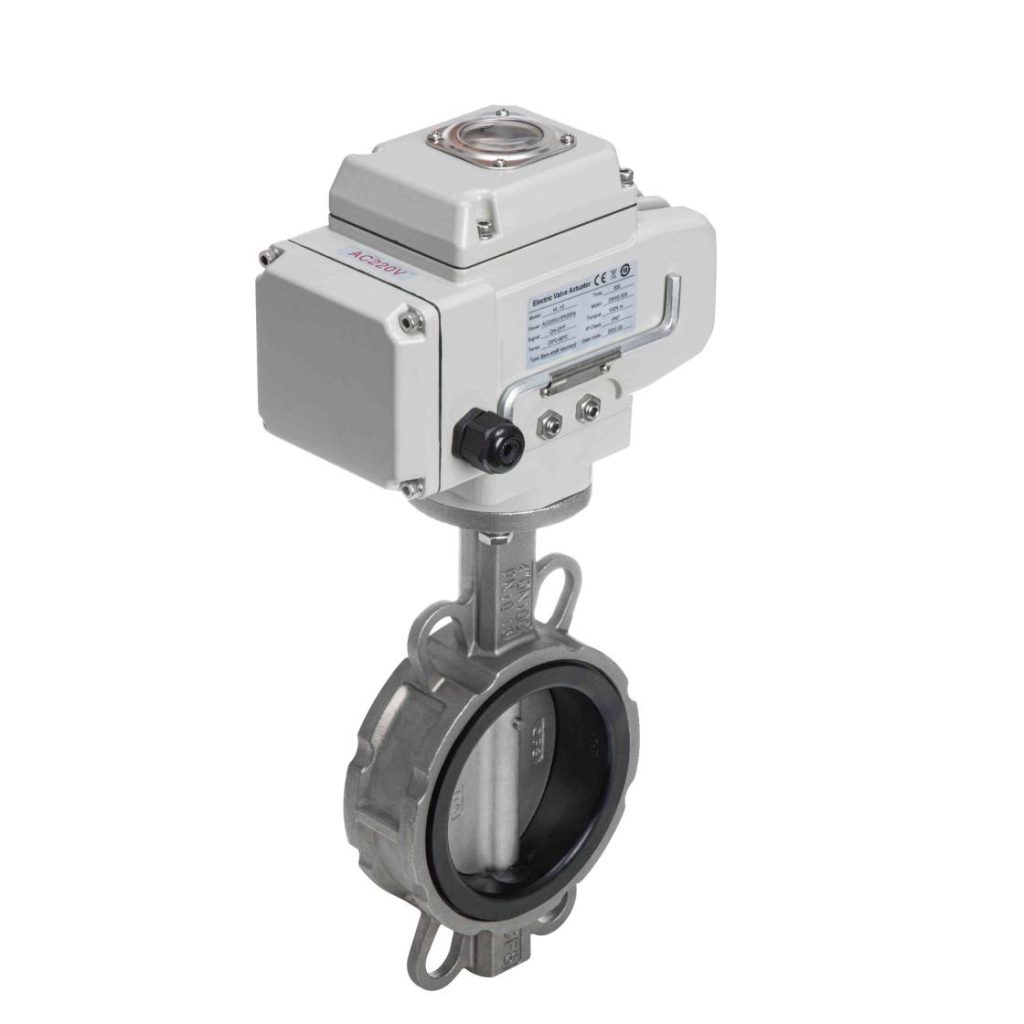
Key Features of the Stainless Steel Electric Clamp Butterfly Valve
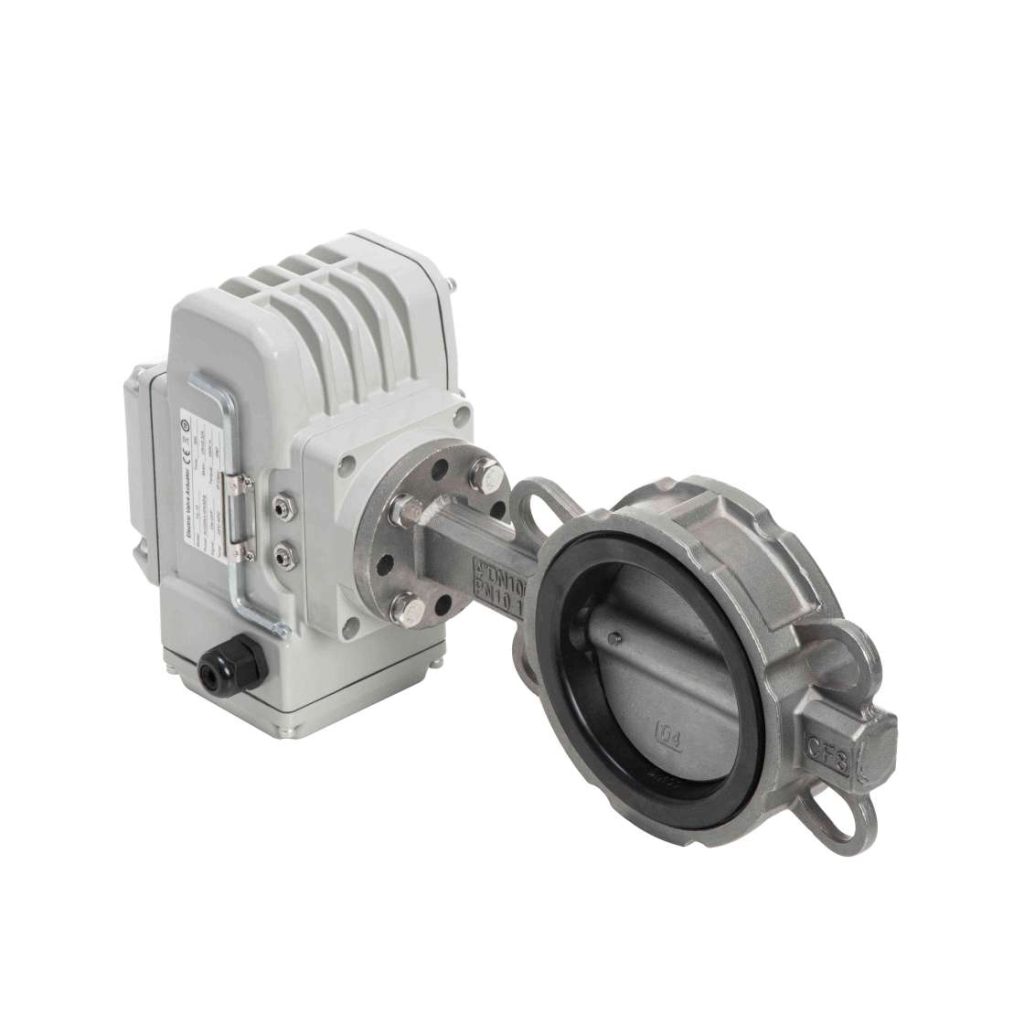
The Stainless Steel Electric Clamp Butterfly Valve is made of high-grade stainless steel, ensuring superior corrosion resistance and longevity. The electric actuator is designed to provide smooth and precise valve operation, enabling accurate flow control. The clamp design allows for easy installation and removal, making maintenance and servicing a hassle-free process. The valve is engineered to handle a wide range of temperatures and pressures, making it versatile for numerous industrial applications. It features a compact design, which helps save space while maintaining robust performance. The electric actuator is equipped with advanced technology for automated operation, contributing to increased efficiency in system control.
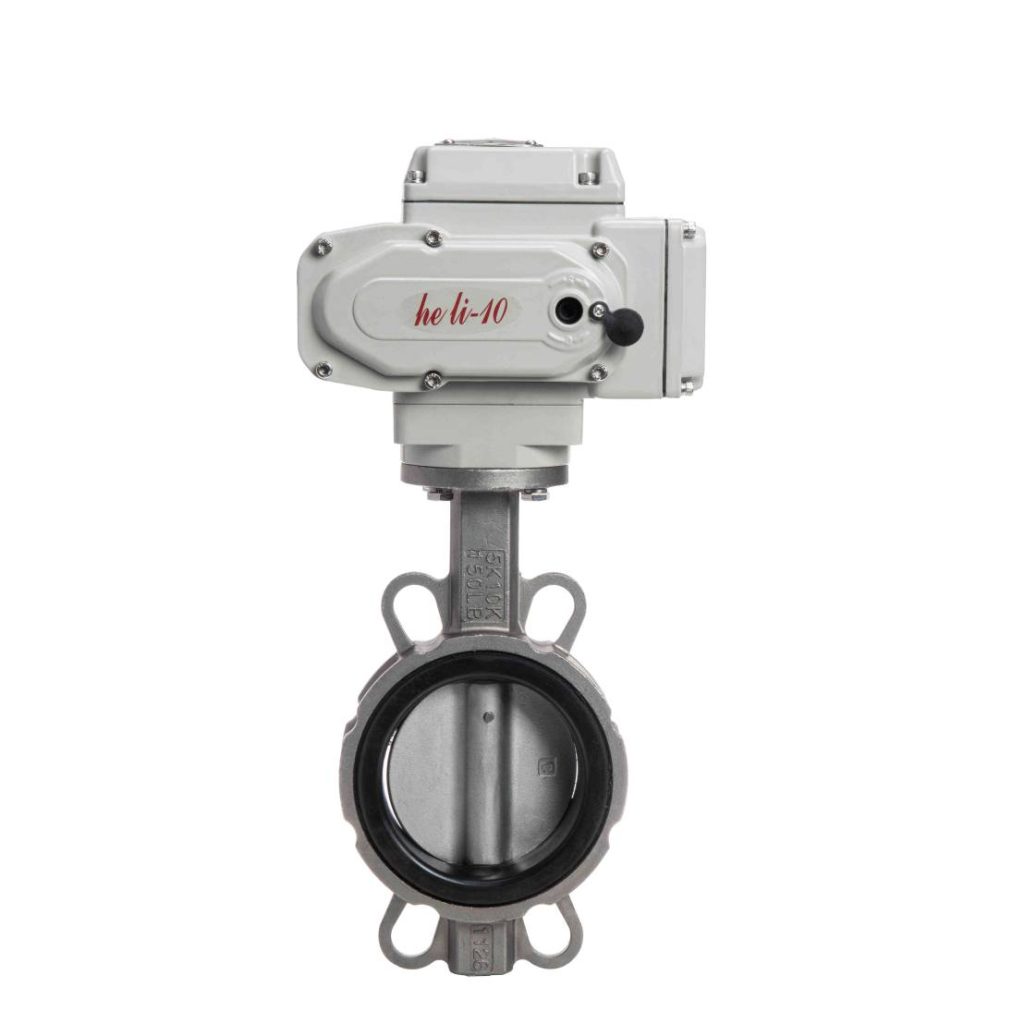