In recent years, lithium batteries have gained immense popularity in various industries due to their high energy density, long lifespan, and lightweight nature. These batteries are found in everything from consumer electronics to electric vehicles (EVs) and even renewable energy storage systems. However, as with any technology, there are inherent risks associated with lithium batteries, including the potential for overheating, overcharging, and even thermal runaway, which can result in fires or explosions. To mitigate these risks, one of the essential safety components in lithium-ion battery systems is the Stainless Steel Lithium Battery Valve.
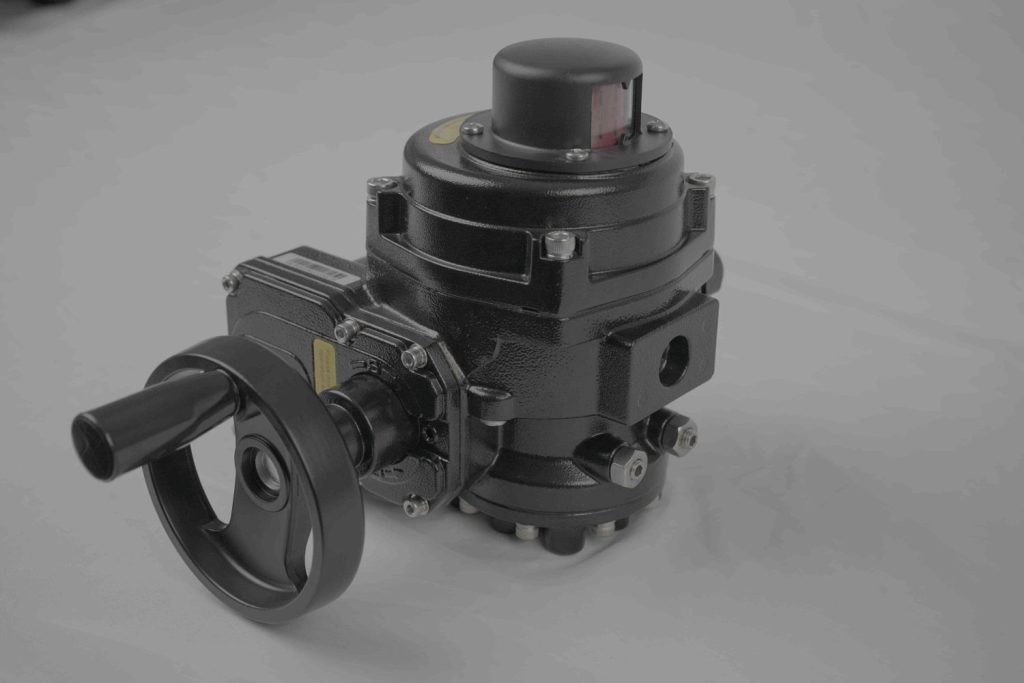
What is a Stainless Steel Lithium Battery Valve? A stainless steel lithium battery valve is a crucial safety feature designed to prevent the dangerous buildup of pressure within a lithium battery. These valves are typically made from high-quality stainless steel to ensure both durability and resistance to the harsh conditions inside a battery. The valve is equipped with a mechanism that activates when the pressure inside the battery reaches a certain threshold, allowing excess gas to escape in a controlled manner. By doing so, it prevents the battery from rupturing or catching fire due to excessive internal pressure.