In the ever-evolving landscape of renewable energy, the emergence of the Hydrogen Energy Electric Warlord stands as a testament to the potential of clean, sustainable power. This formidable entity, a pioneer in the integration of hydrogen energy and electric technology, is leading the charge towards a greener, more efficient future.
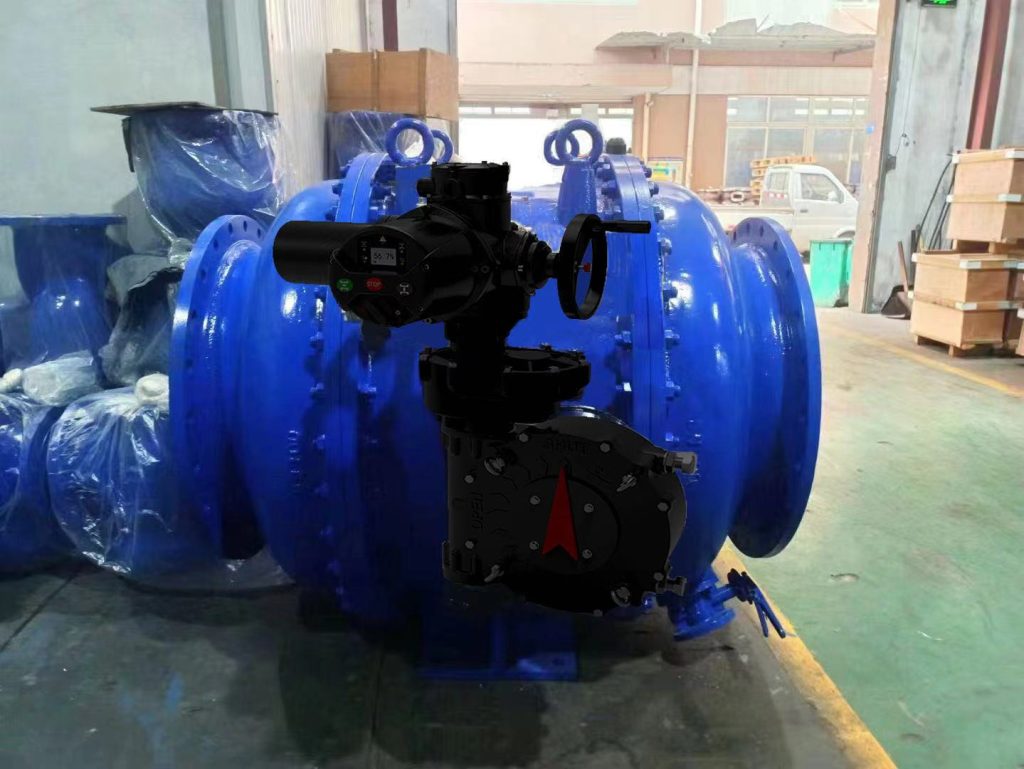
The Hydrogen Energy Electric Warlord recognizes the vast potential of hydrogen as an energy source. Hydrogen, the most abundant element in the universe, offers a clean and efficient alternative to fossil fuels. When combined with oxygen, it produces only water as a byproduct, eliminating the harmful emissions that contribute to climate change. The Warlord’s vision is to harness this powerful element and utilize it to power our vehicles, homes, and industries.
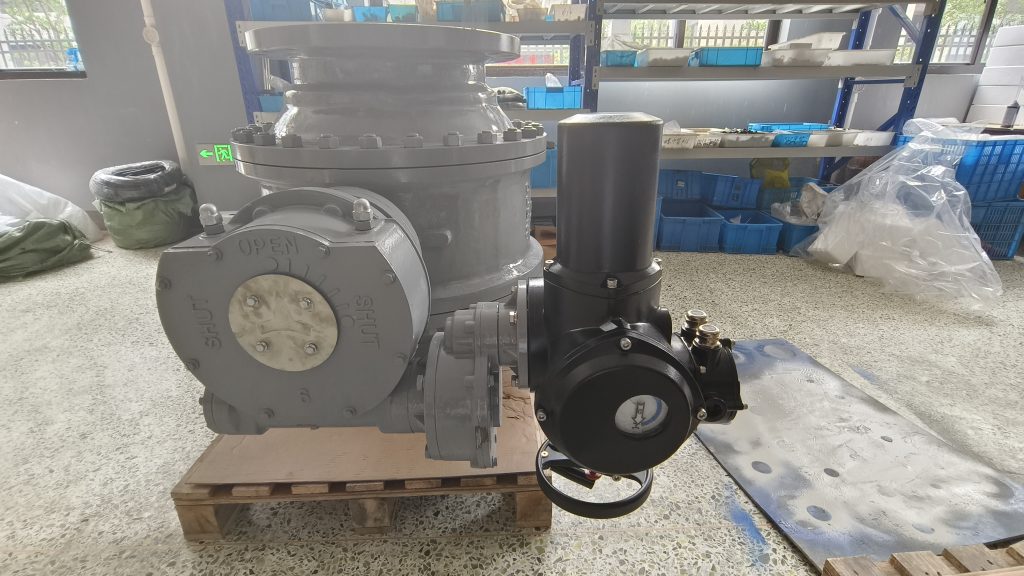
The Electric Warlord’s strategy is multifaceted. It involves the development of advanced hydrogen production techniques, the establishment of a robust infrastructure for hydrogen storage and distribution, and the creation of innovative electric vehicles that can efficiently utilize hydrogen fuel cells. This comprehensive approach ensures that the Warlord is positioned at the forefront of the hydrogen energy revolution. One of the key areas of focus for the Warlord is the development of hydrogen fuel cell technology. Fuel cells convert hydrogen and oxygen into electricity, with water as the only byproduct. This process is not only efficient but also emission-free, making it a highly attractive option for electric vehicles. The Warlord is investing heavily in research and development to improve the performance and durability of fuel cells, making them more suitable for widespread commercial use.
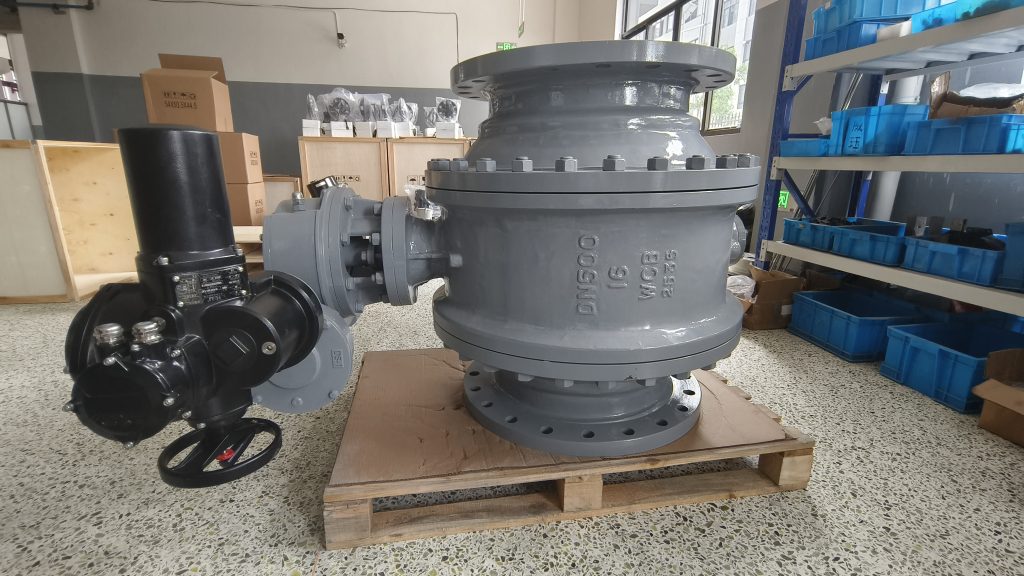