In the realm of electrical safety and distribution, Moulded Case Circuit Breakers (MCCBs) stand as the unsung heroes, diligently protecting our homes, industries, and infrastructure from electrical mishaps. Behind their unassuming exteriors lies a world of intricate craftsmanship and precision engineering. This article delves into the fascinating world of MCCB manufacturing, exploring the meticulous processes and dedication that go into creating these vital electrical components.
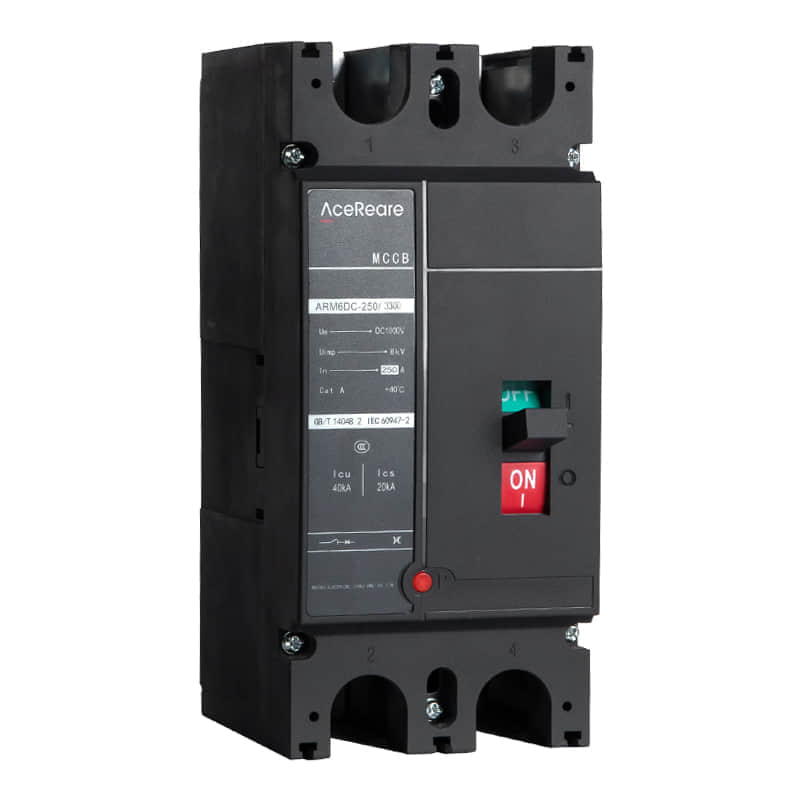
The Birth of a Guardian: Design and Planning
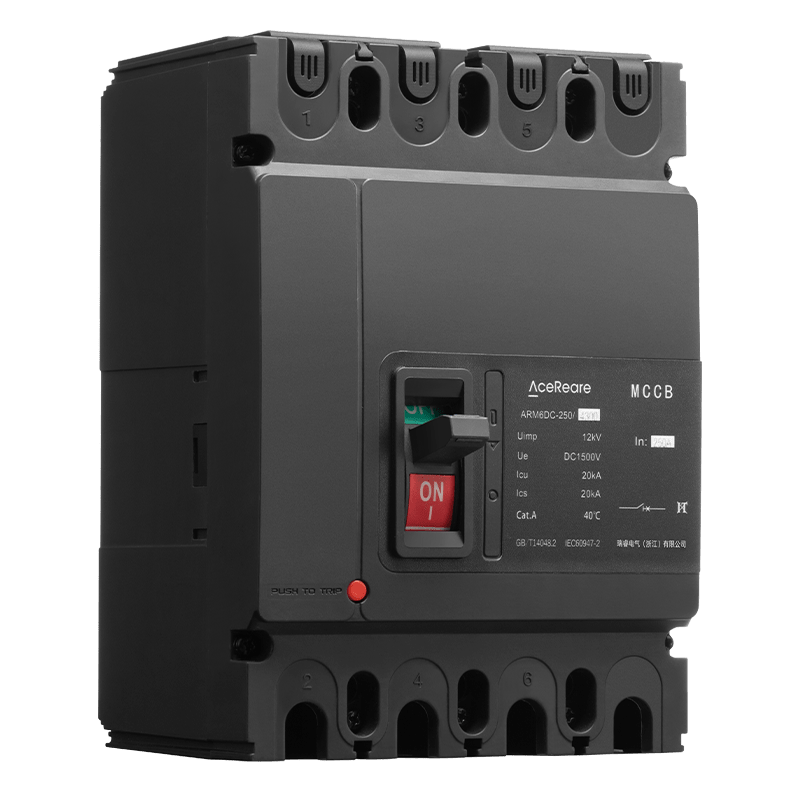
MCCBs are born from a blend of art and science. Before the manufacturing process even begins, a team of engineers and designers meticulously plan every detail. They consider factors such as current ratings, voltage requirements, breaking capacity, and fault protection mechanisms to ensure the MCCB can handle diverse electrical systems safely and efficiently. Materials Selection: The Foundation of Reliability One of the key secrets behind the reliability of MCCBs lies in the choice of materials. Manufacturers carefully select materials like insulating plastics, conductive metals, and precision-crafted internal components. These materials are chosen for their durability, heat resistance, and electrical conductivity, ensuring that MCCBs can perform under the most challenging conditions. Precision Molding: Shaping the Future of Safety The heart of MCCB manufacturing lies in precision molding. Advanced injection molding machines create the outer casing, while meticulous attention is paid to every detail, from smooth surfaces to intricate patterns for better heat dissipation. This process is where MCCBs get their distinct and often colorful exteriors, reflecting the creativity of their creators. Assembly: A Symphony of Components Assembling an MCCB is like orchestrating a complex symphony. The internal components, including contact assemblies, trip mechanisms, and arc chutes, must be meticulously assembled. Each component plays a vital role in ensuring the MCCB’s ability to detect faults and interrupt electrical currents swiftly. Testing and Quality Assurance: The Crucial Final Act Before an MCCB is deemed ready for service, it undergoes a battery of rigorous tests. These tests check for various parameters, including fault detection, overload protection, and temperature tolerance. Any MCCB that doesn’t meet the exacting standards is sent back for adjustments or disposal. Customization: Tailoring to Unique Needs Not all electrical systems are created equal, and MCCB manufacturers understand this. Many offer customization options, allowing customers to specify features like adjustable trip settings, additional auxiliary contacts, and remote operation capabilities. This flexibility ensures that MCCBs can adapt to a wide range of applications. Sustainability: A Commitment to the Environment In today’s environmentally conscious world, MCCB manufacturers are also focused on sustainability. They aim to reduce their carbon footprint by using recyclable materials and optimizing manufacturing processes to minimize waste. Some even develop MCCBs that consume less energy during operation, contributing to greener electrical systems. Global Impact: MCCBs in Action Once the MCCBs are manufactured, they find their way into electrical systems around the world. They guard against short circuits, overloads, and electrical faults in residential, commercial, and industrial settings. Without them, the modern world would be a far riskier place. In conclusion, Moulded Case Circuit Breakers may appear unassuming, but their journey from conception to deployment is a testament to human ingenuity and dedication to safety. The world of MCCB manufacturing is a symphony of precision, craftsmanship, and innovation that ensures our electrical systems remain secure. The next time you flip a switch or plug in a device, take a moment to appreciate the silent guardians, the MCCBs, that make it all possible.
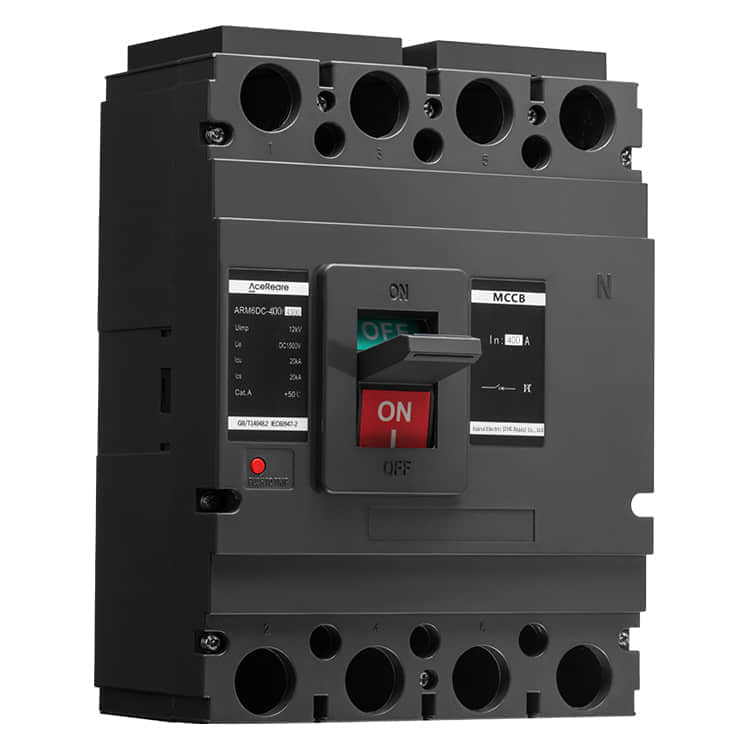