In the world of advanced manufacturing, DMC molding has emerged as a pioneering technique with significant potential. DMC, short for Dough Molding Compound, is a composite material that combines resins, fillers, and reinforcements to create parts with exceptional strength, durability, and versatility. As industries demand lightweight yet robust components, DMC molding manufacturers play a crucial role in shaping the future of engineering and design.
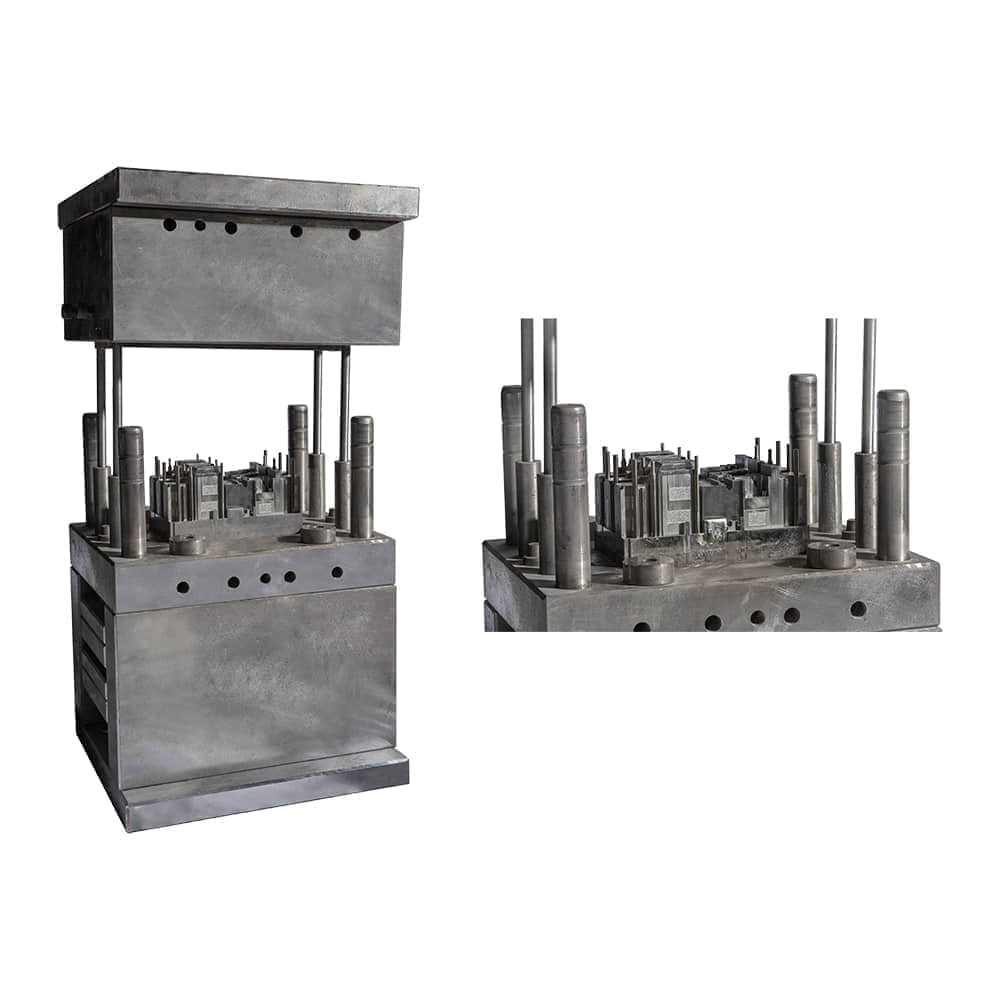
Unveiling the DMC Molding Process
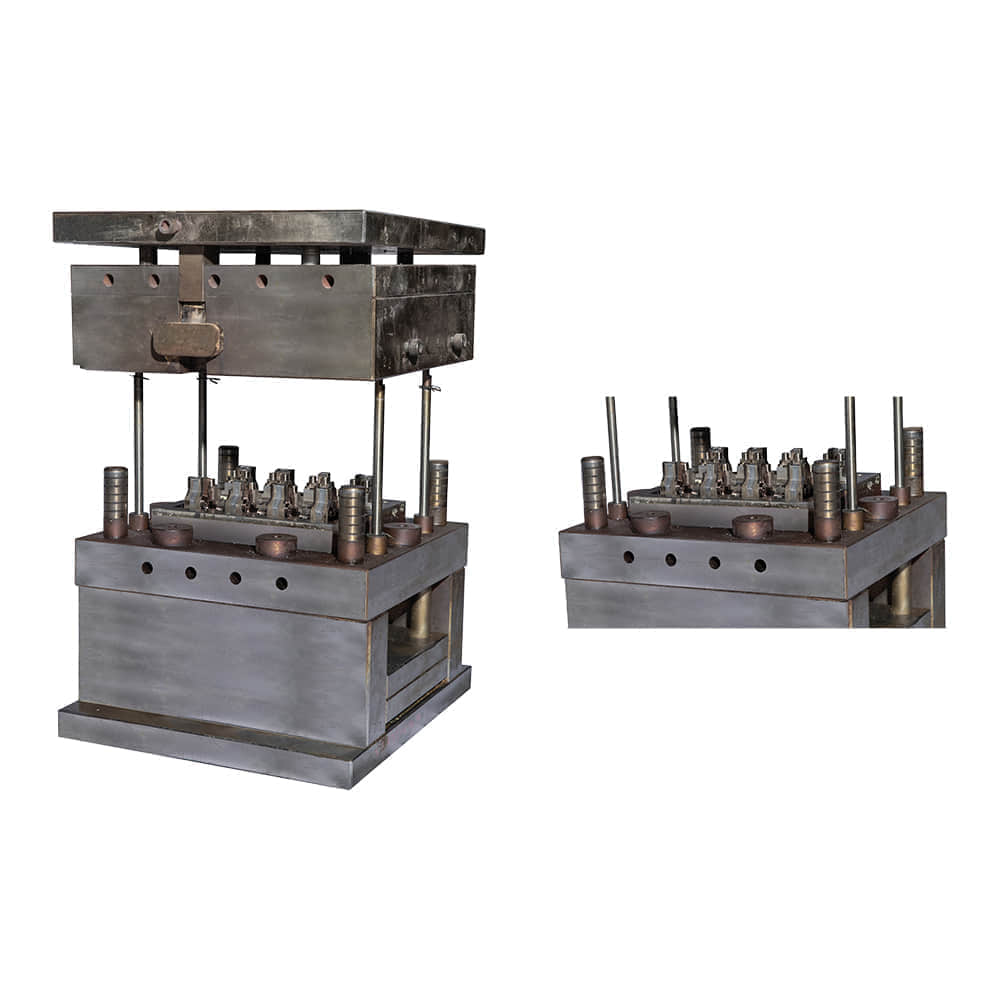
DMC molding is a complex process that requires precision and expertise. The key components are the resin, chopped glass fibers, and fillers. These materials are blended together to create a mixture resembling dough, hence the name “Dough Molding Compound.” The resulting compound is then molded under heat and pressure to form the desired shape. This process allows for intricate designs and high-quality surface finishes. Strength and Durability One of the primary advantages of DMC molding is its exceptional strength and durability. Parts manufactured through this process exhibit resistance to impact, chemicals, and extreme temperatures. This resilience makes DMC components ideal for use in automotive, aerospace, and electrical applications. Whether it’s a lightweight aircraft component or a robust electrical enclosure, DMC molding delivers the structural integrity required in demanding environments. Lightweight Design and Cost Efficiency In today’s engineering landscape, weight reduction is a key consideration. DMC molding excels in this aspect by offering lightweight solutions without compromising on strength. This weight reduction not only improves fuel efficiency in transportation but also lowers shipping costs and enhances overall cost efficiency. Manufacturers benefit from reduced material and transportation expenses while delivering top-quality products to their customers. Design Flexibility and Complexity DMC molding offers a level of design flexibility that few other manufacturing processes can match. The ability to create complex, intricate shapes with tight tolerances opens up new possibilities for product design and innovation. Manufacturers can tailor their DMC molding processes to suit a wide range of specifications, from small and intricate components to large and robust structures. Environmental Sustainability As the world increasingly focuses on sustainability, DMC molding plays a crucial role in eco-friendly manufacturing. The process generates minimal waste, as excess material can be recycled. Additionally, the durability and longevity of DMC-molded components reduce the need for frequent replacements, contributing to resource conservation. Applications Across Industries DMC molding has found applications across various industries. In the automotive sector, it’s used for manufacturing lightweight yet sturdy components, such as bumpers, grilles, and under-the-hood parts. In the aerospace industry, DMC parts contribute to weight reduction in aircraft, leading to improved fuel efficiency. Electrical and electronics industries benefit from DMC’s insulation properties, ensuring the safety and reliability of electrical enclosures. Continuous Innovation and Advancement The field of DMC molding is far from stagnant. Manufacturers are constantly innovating to improve the process, materials, and end-product performance. Advanced techniques like in-mold coating and integrated electronics are pushing the boundaries of what DMC molding can achieve. Conclusion As industries continue to seek lightweight, durable, and environmentally friendly solutions, DMC molding manufacturers are at the forefront of innovation. Their ability to deliver high-quality, complex components while addressing sustainability concerns makes them key players in shaping the future of advanced manufacturing. With a commitment to excellence and a focus on continuous improvement, DMC molding manufacturers are poised to revolutionize industries and contribute to a more sustainable and efficient world.
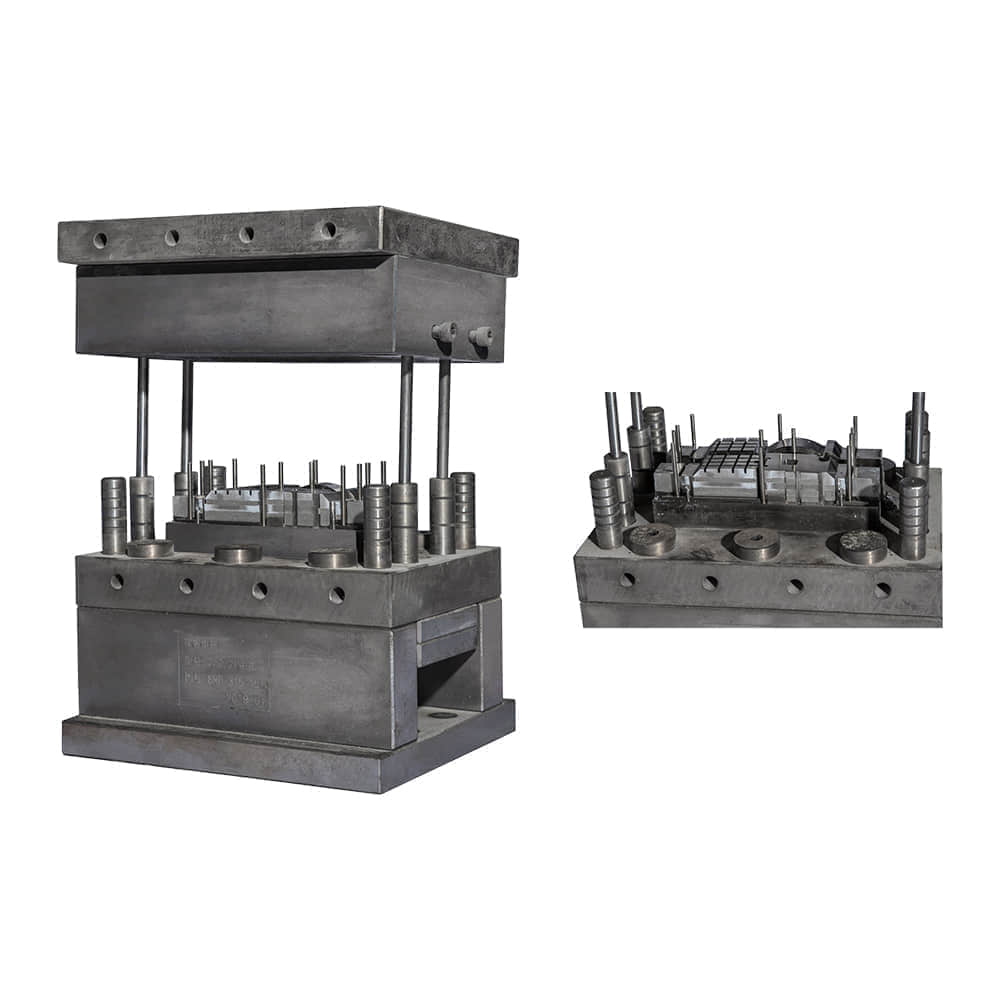