In the realm of modern industrial automation, the pneumatic actuator stands as a pivotal component, driving various industrial processes with precision and reliability. This article delves into the intricacies of the pneumatic actuator, exploring its function, working principles, and the diverse applications it finds in today’s industrial landscape.
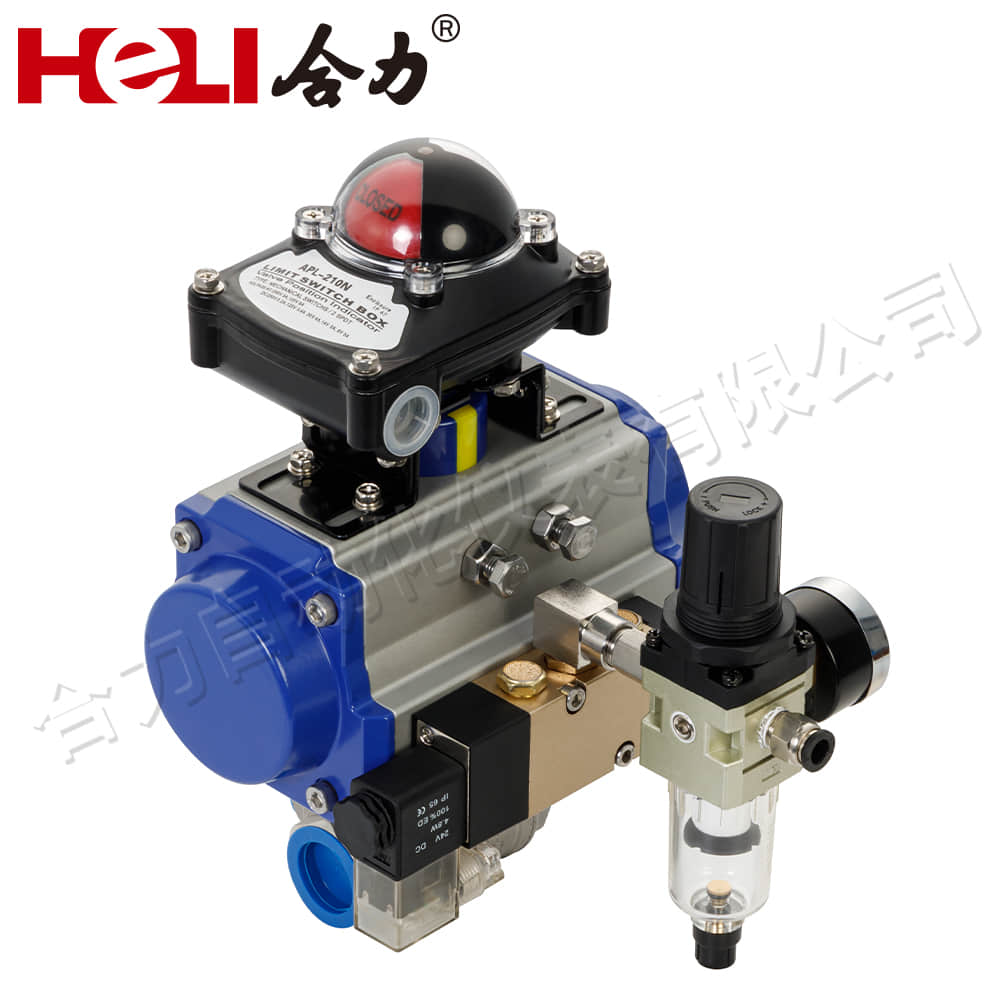
The pneumatic actuator, often referred to as a pneumatic actuator or pneumatic drive, is an energy-conversion device that converts compressed air into mechanical motion. It operates on the principle of utilizing the pressure difference created by compressed air to generate a force that can be harnessed to move or control mechanical systems. This force is transmitted through the actuator’s internal mechanisms, ultimately driving the desired motion or action.
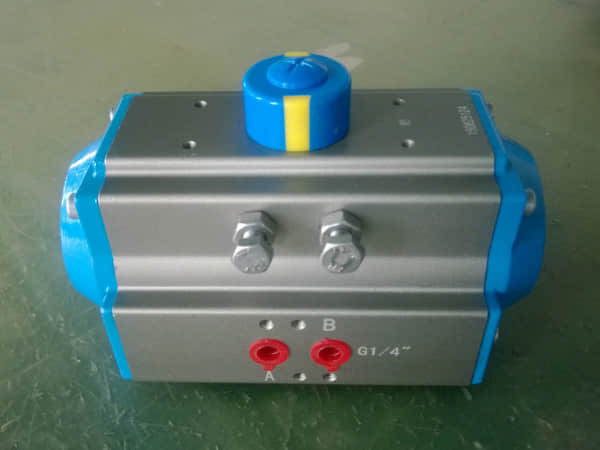
The working principle of the pneumatic actuator is relatively straightforward. Compressed air is supplied to the actuator, typically through a control valve. The pressure of the air acts on a piston or diaphragm within the actuator, causing it to move. This movement is then translated into the desired mechanical action, such as opening or closing a valve, moving a lever, or rotating a shaft. The amount of force generated by the actuator can be precisely controlled by adjusting the pressure of the compressed air. The versatility and reliability of the pneumatic actuator have made it a popular choice in a wide range of industrial applications. One significant area where pneumatic actuators excel is in the automation of fluid control systems. They are often used to operate valves in pipelines, allowing for precise control over the flow of liquids or gases. In manufacturing processes, pneumatic actuators are employed to position tools, clamp workpieces, and perform various other automated tasks.
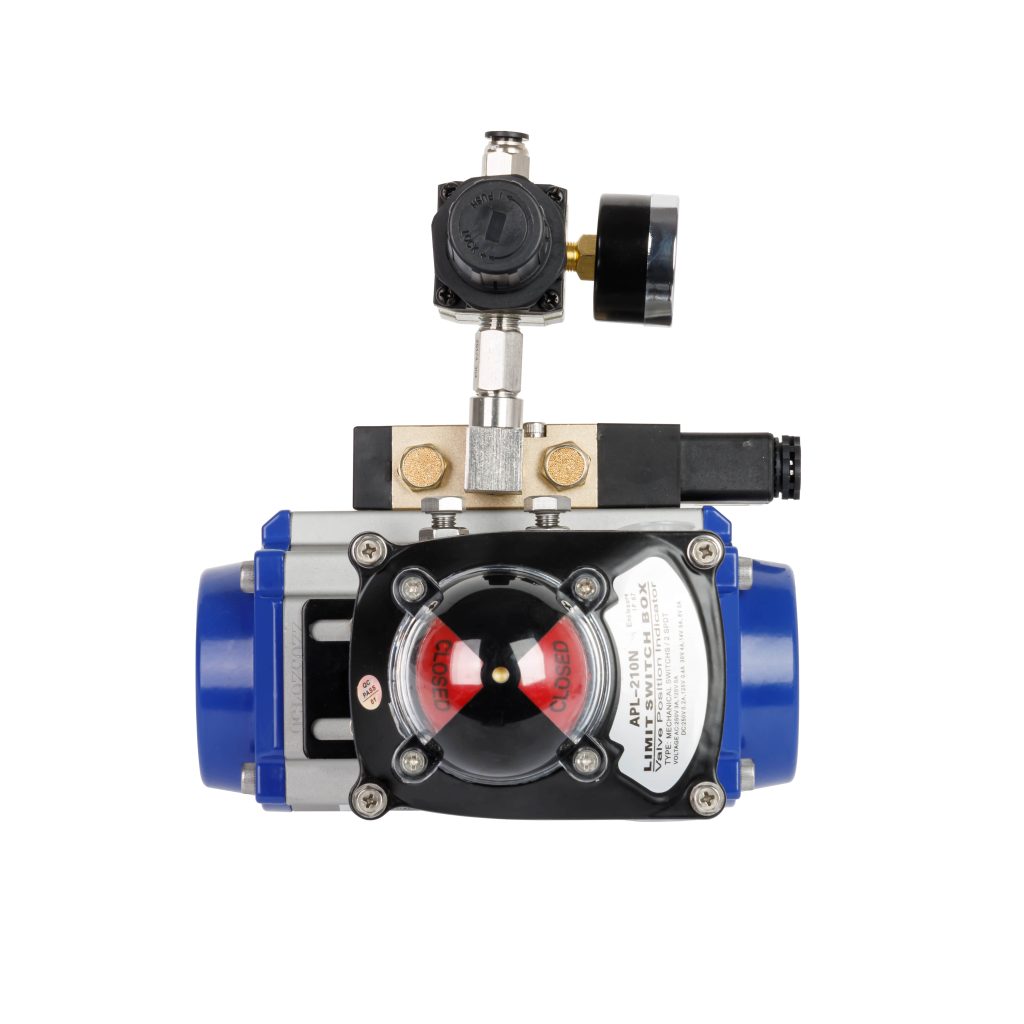