Molded case parts are an integral component of numerous industries, serving as essential elements in various applications. These parts, crafted through a molding process, offer a range of functionalities that contribute to the efficiency, safety, and reliability of machinery and equipment. This article delves into the world of molded case parts, shedding light on their characteristics, manufacturing process, and diverse applications.
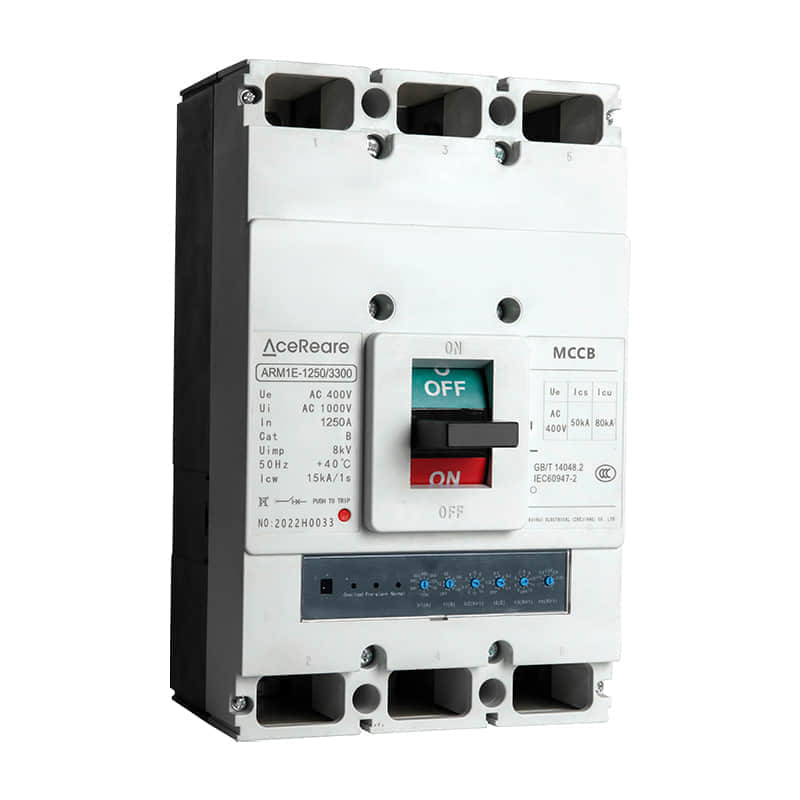
Characteristics of Molded Case Parts:
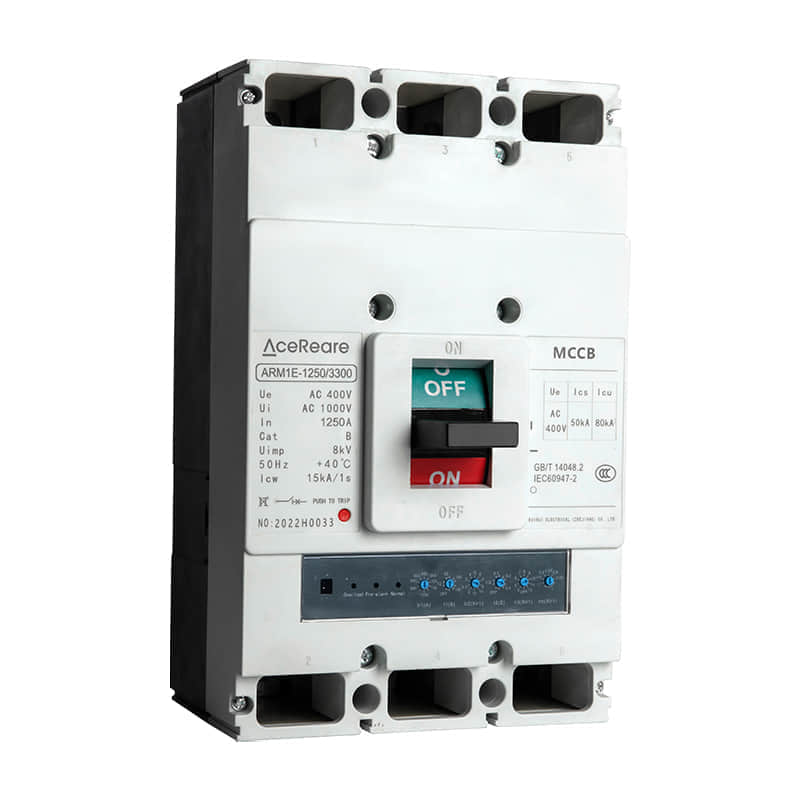
Molded case parts are typically made from thermoplastic or thermosetting materials, such as polypropylene, polycarbonate, or nylon. These materials are chosen for their durability, heat resistance, and mechanical strength. The molding process involves melting the chosen material and injecting it into a mold cavity, where it solidifies to take the desired shape. This manufacturing method ensures consistent quality, precision, and dimensional accuracy of the molded parts. Manufacturing Process: The manufacturing process of molded case parts begins with the design of the mold cavity. Computer-aided design (CAD) software is employed to create intricate and precise designs that match the intended final product. Once the design is finalized, the mold is created using advanced machining techniques or additive manufacturing methods. The chosen material is then heated to its melting point and injected into the mold under high pressure. After cooling and solidification, the mold is opened, and the finished molded case part is ejected. Applications of Molded Case Parts: Electrical Industry:Molded case parts find extensive use in the electrical industry, particularly in circuit breakers and switchgear. These parts provide insulation, protection, and structural support within electrical enclosures. The inherent electrical insulation properties of materials used in molded case parts prevent short circuits and enhance the overall safety of electrical systems. Automotive Sector:In automobiles, molded case parts are employed in various components, including dashboard panels, interior trim, and engine enclosures. Their strength, lightweight nature, and ability to withstand environmental factors make them a preferred choice for enhancing both aesthetics and functionality in vehicles. Consumer Goods:Many household appliances and consumer electronics incorporate molded case parts. These parts can be found in items like coffee machines, vacuum cleaners, and gaming consoles. They offer durability and customizable designs, enabling manufacturers to create sleek and appealing products. Medical Devices:Molded case parts are crucial in the medical field due to their biocompatibility, which makes them suitable for devices that come into contact with the human body. They are used in equipment such as diagnostic machines, patient monitoring devices, and surgical instruments. Industrial Machinery:Industrial machinery, such as manufacturing equipment and conveyor systems, relies on molded case parts for their robustness and ability to withstand heavy-duty applications. These parts contribute to the smooth operation of industrial processes. Aerospace Applications:Molded case parts are also finding their way into aerospace applications, where lightweight yet durable components are of paramount importance. From cabin interiors to critical aircraft systems, these parts contribute to the overall performance and safety of aerospace vehicles. In conclusion, molded case parts are versatile components that play a pivotal role in multiple industries. Their distinctive characteristics, precision manufacturing process, and wide-ranging applications make them indispensable in modern manufacturing and technology. As industries continue to evolve, molded case parts will likely continue to advance, offering innovative solutions that drive progress across various sectors.
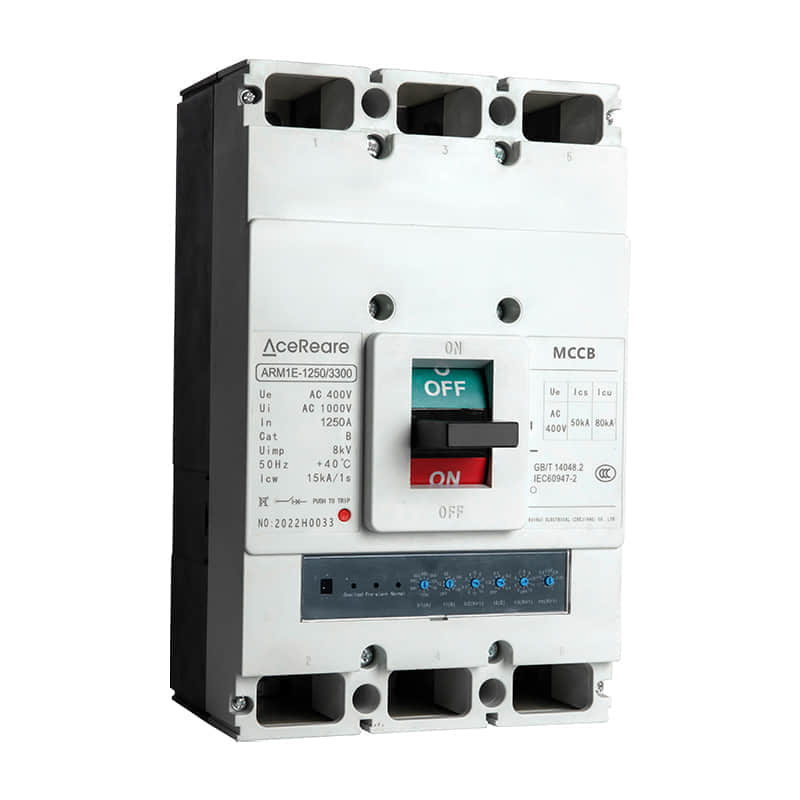