Metal stamping is a widely used manufacturing process that allows for the creation of complex and precise metal parts. At the heart of this process lies the metal stamping die, a crucial tool that determines the quality and accuracy of the final product. In this article, we will delve into the world of metal stamping dies, exploring their design, construction, and essential role in modern manufacturing.
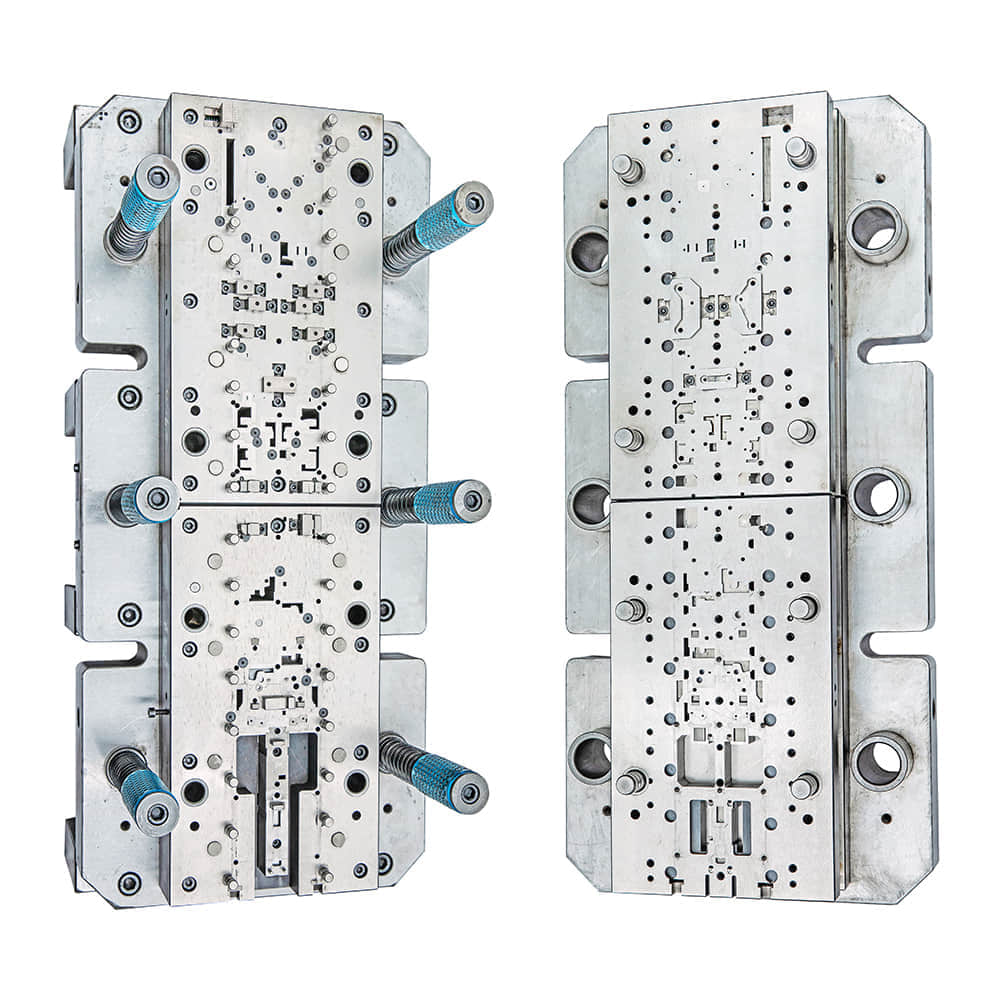
Designing the Blueprint
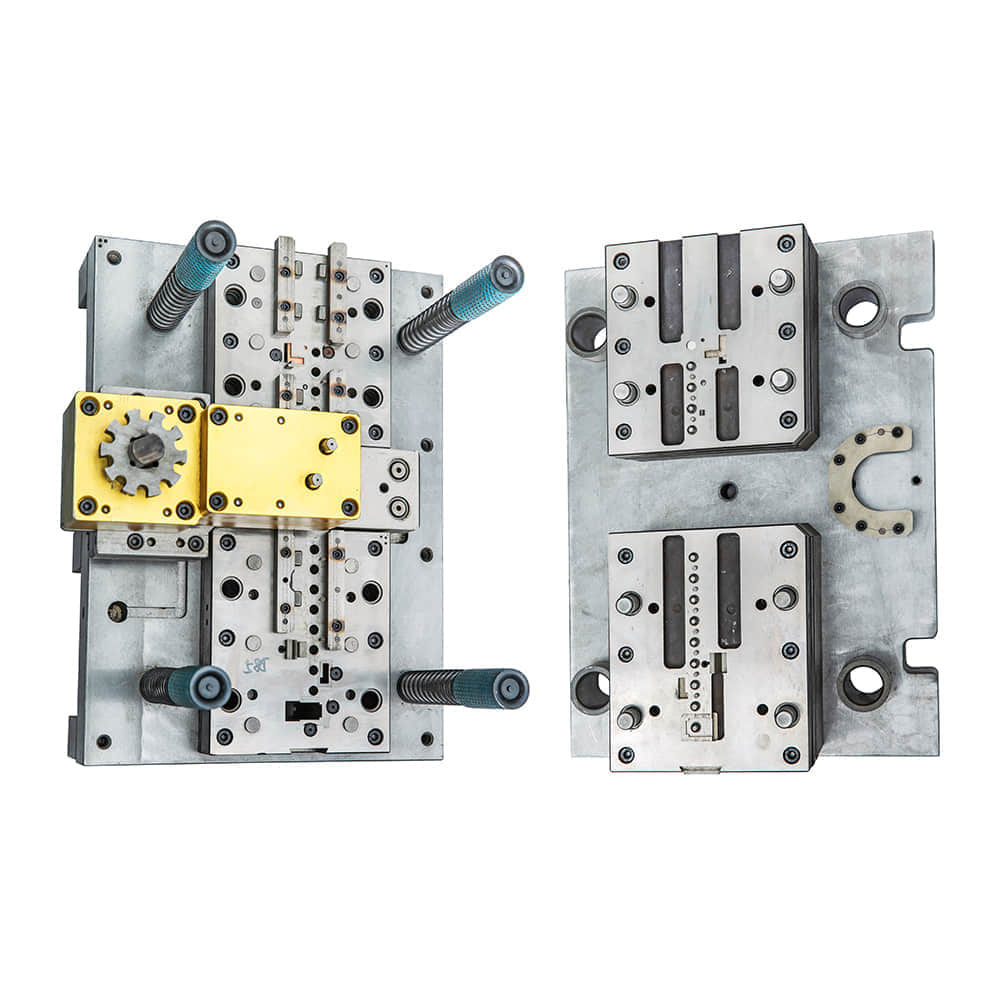
Before a metal stamping die can be fabricated, meticulous planning and design are required. Engineers and toolmakers collaborate to create a blueprint that outlines the die’s specifications, including its size, shape, and the intended metal materials to be stamped. This blueprint serves as a guide throughout the die-making process. Material Selection Selecting the right material for a stamping die is crucial. The material must be durable, able to withstand high levels of stress and wear over time. Common materials used for stamping dies include tool steels such as A2, D2, and S7, as well as carbide for specialized applications. The choice of material depends on factors like the type of metal being stamped and the expected production volume. Machining and Heat Treatment Once the material is chosen, the die-making process begins with precision machining. Computer Numerical Control (CNC) machines are often used to cut and shape the die according to the blueprint. After machining, the die undergoes heat treatment to enhance its hardness and durability. Heat treatment processes like quenching and tempering help optimize the die’s performance and lifespan. Die Components A metal stamping die consists of several components, each with a specific function. The primary components include: Punch and Die:These are the core components responsible for shaping the metal. The punch is the male component, while the die is the female component. They work together to create the desired part shape. Strippers:Strippers help remove the formed part from the punch after each stamping operation, preventing sticking and ensuring a smooth production process. Guide Pins and Bushings:These components ensure precise alignment of the punch and die, reducing the risk of misalignment and defects in the stamped parts. Die Sets:Die sets hold all the components together and provide structural integrity to the die. Precision and Accuracy The hallmark of a well-crafted metal stamping die is its ability to consistently produce parts with precision and accuracy. Tolerances in the micrometer range are not uncommon. Engineers and toolmakers painstakingly fine-tune the die to achieve these high levels of precision, using techniques such as die surface grinding and lapping. Quality Control Quality control is an integral part of the die-making process. Before being put into production, the die undergoes rigorous testing to ensure that it meets the specified tolerances and performs flawlessly. This includes test stamping with sample materials to assess the die’s functionality and identify any issues that need correction. Versatility and Customization Metal stamping dies are highly versatile and can be customized for various applications. They can produce intricate parts for industries ranging from automotive and aerospace to electronics and medical devices. Customization often involves modifying the die’s design and components to accommodate specific part geometries and production requirements. The Future of Metal Stamping Dies As technology continues to advance, so does the field of metal stamping die manufacturing. Computer-aided design (CAD) and simulation software have revolutionized the design process, allowing engineers to visualize and optimize dies before they are physically fabricated. Additionally, the integration of automation and robotics in stamping processes enhances efficiency and productivity. In conclusion, metal stamping dies are the unsung heroes of modern manufacturing. They embody precision craftsmanship and play a pivotal role in shaping the products we use in our daily lives. From concept and design to fabrication and quality control, the journey of creating a metal stamping die is a testament to human ingenuity and engineering excellence.
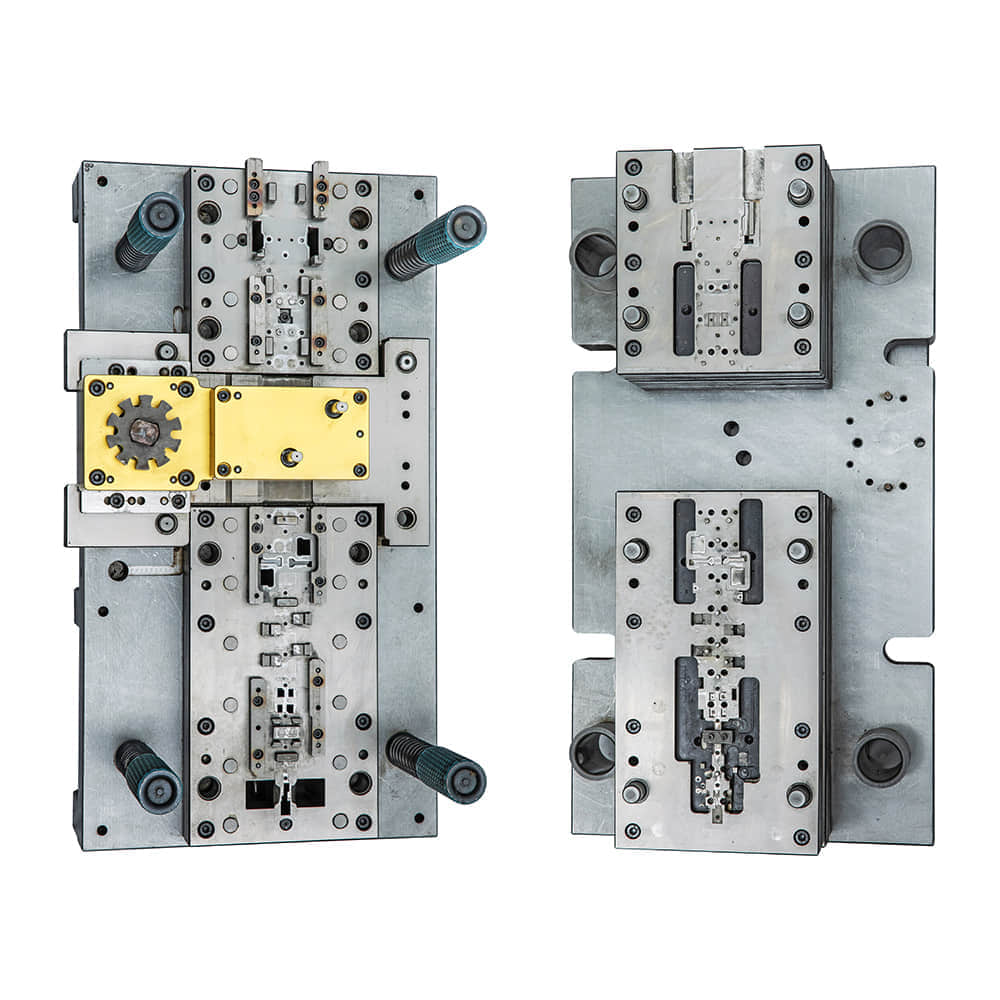