In today’s rapidly evolving industrial landscape, the role of an injection mold manufacturer is of paramount importance. Injection molding, a versatile manufacturing process, has found applications in a plethora of industries, ranging from automotive to consumer electronics, medical devices to packaging. This article delves into the key aspects of injection mold manufacturing and its significance in shaping various sectors.
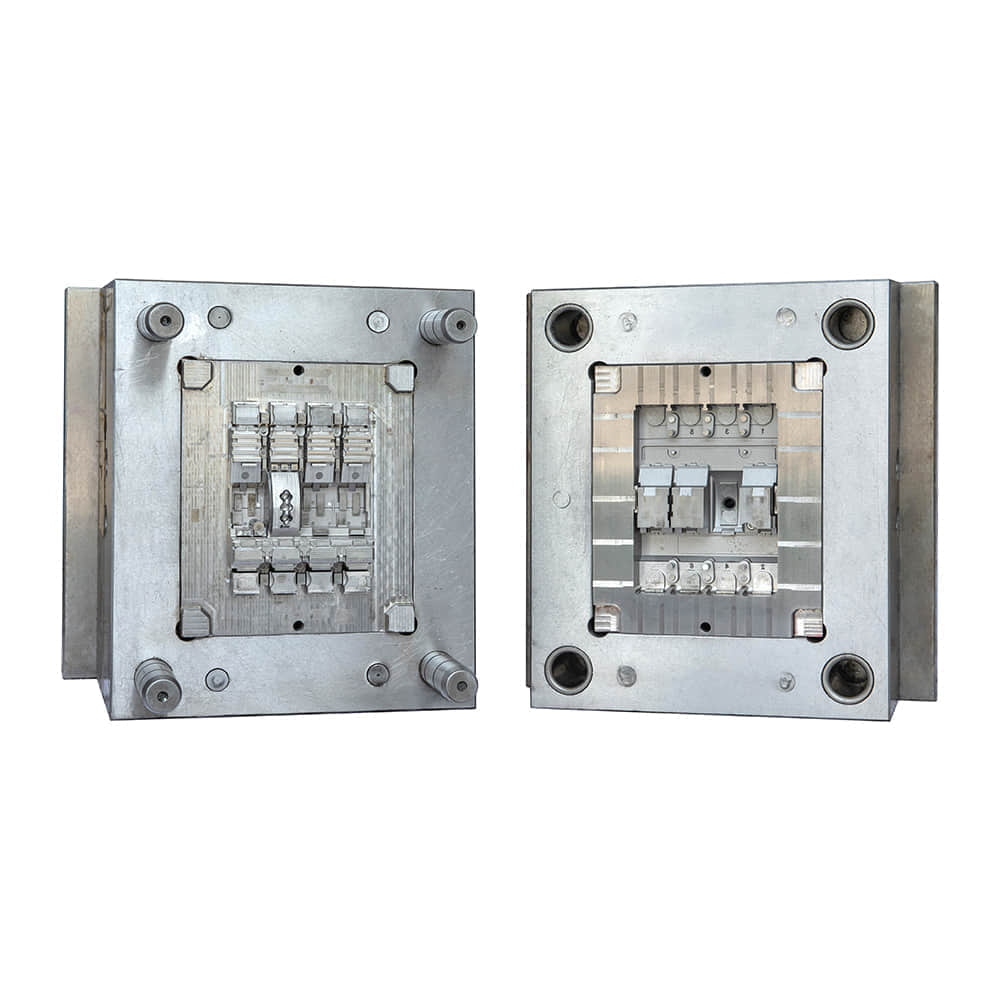
Understanding Injection Mold Manufacturing
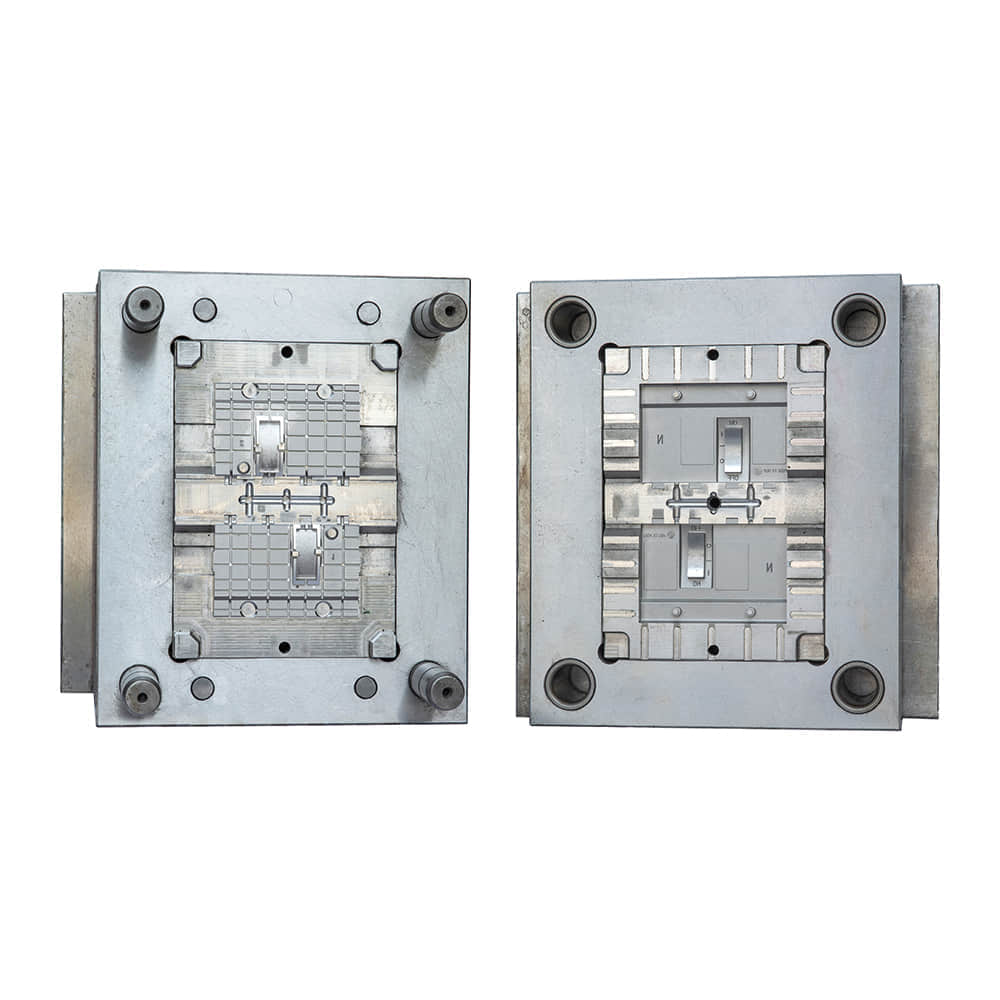
Injection mold manufacturing is the process of creating intricate and precise molds used for injecting molten material, usually plastic, into a desired shape. These molds are the cornerstone of the injection molding process, which enables the mass production of identical components with minimal variations. Manufacturers employ advanced design and engineering techniques to create molds that not only facilitate precise molding but also ensure efficiency and longevity. The Significance of Injection Mold Manufacturers Precision Engineering:Injection mold manufacturers play a pivotal role in engineering molds that translate design concepts into physical reality. The precision and intricacy of the mold’s design directly impact the quality and consistency of the final product. Manufacturers leverage computer-aided design (CAD) and computer-aided manufacturing (CAM) technologies to achieve the exact specifications required by clients. Diverse Industry Applications:The reach of injection mold manufacturing extends across a broad spectrum of industries. Whether it’s the automotive sector demanding complex and durable components, the medical field requiring sterile and reliable devices, or the consumer electronics domain seeking sleek and functional parts, injection mold manufacturers cater to diverse requirements. Innovation and Material Expertise:Modern injection mold manufacturers are at the forefront of material innovation. They continually explore new plastics and composite materials that offer improved mechanical properties, sustainability, and cost-efficiency. Manufacturers’ expertise in material selection is crucial for producing products that meet stringent industry standards and customer expectations. Efficiency and Scalability:Injection molding is renowned for its ability to produce large quantities of components with minimal time and cost implications. Injection mold manufacturers optimize mold designs and production processes to ensure efficiency and scalability, contributing to cost-effective mass production. Collaborative Approach:Successful injection mold manufacturers engage in close collaboration with clients. They understand the unique requirements of each project, offer valuable insights during the design phase, and provide support throughout the entire manufacturing process. This collaborative approach fosters innovation and ensures that the final product aligns with the client’s vision. Quality Assurance:Maintaining consistent quality is a hallmark of reputable injection mold manufacturers. Rigorous quality control measures are employed at every stage of manufacturing, from design and material selection to mold creation and testing. This commitment to quality guarantees that the produced components meet or exceed industry standards. The Future of Injection Mold Manufacturing As industries continue to evolve, so does the landscape of injection mold manufacturing. The adoption of advanced technologies like additive manufacturing (3D printing) for producing molds, the integration of smart sensors for real-time quality monitoring, and the emphasis on sustainable materials are reshaping the future of injection mold manufacturing. In conclusion, the role of an injection mold manufacturer extends beyond the realm of mere production. These manufacturers are architects of precision, efficiency, and innovation, enabling industries to bring their ideas to life. With their expertise, collaborative spirit, and dedication to quality, injection mold manufacturers are indispensable partners in driving progress across diverse sectors.
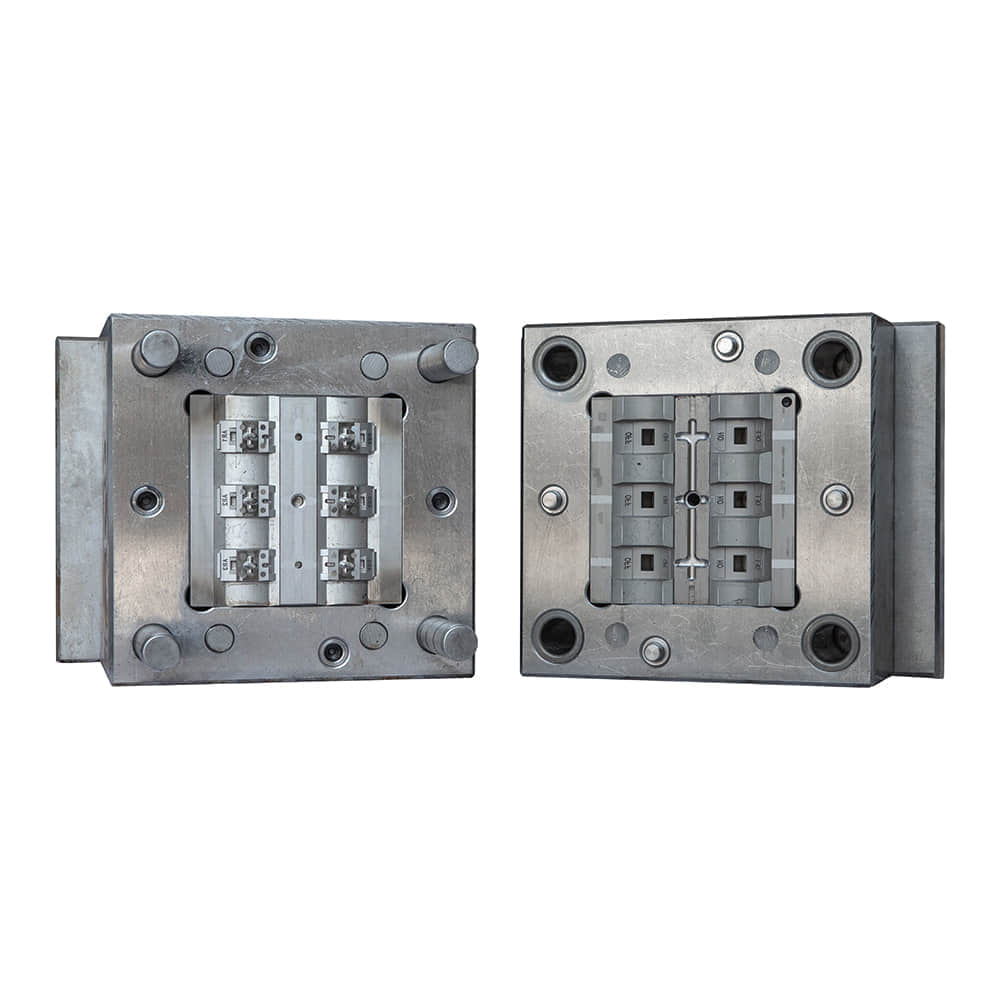