SMC Molding: A Revolution in Composite Materials
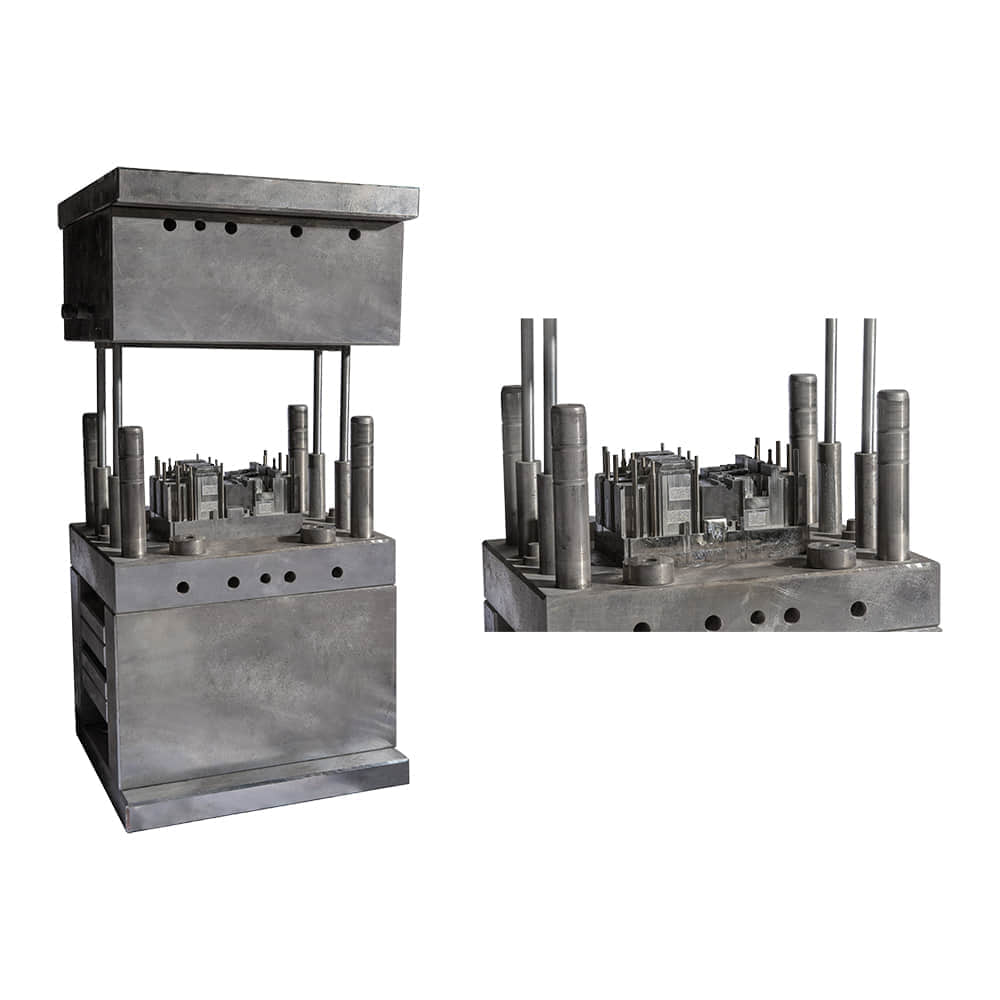
In the realm of advanced manufacturing and composite materials, Sheet Molding Compound (SMC) molding has emerged as a revolutionary technique that has transformed industries and redefined possibilities. This article delves into the world of SMC molding, shedding light on its fundamentals, applications, advantages, and the future it promises.
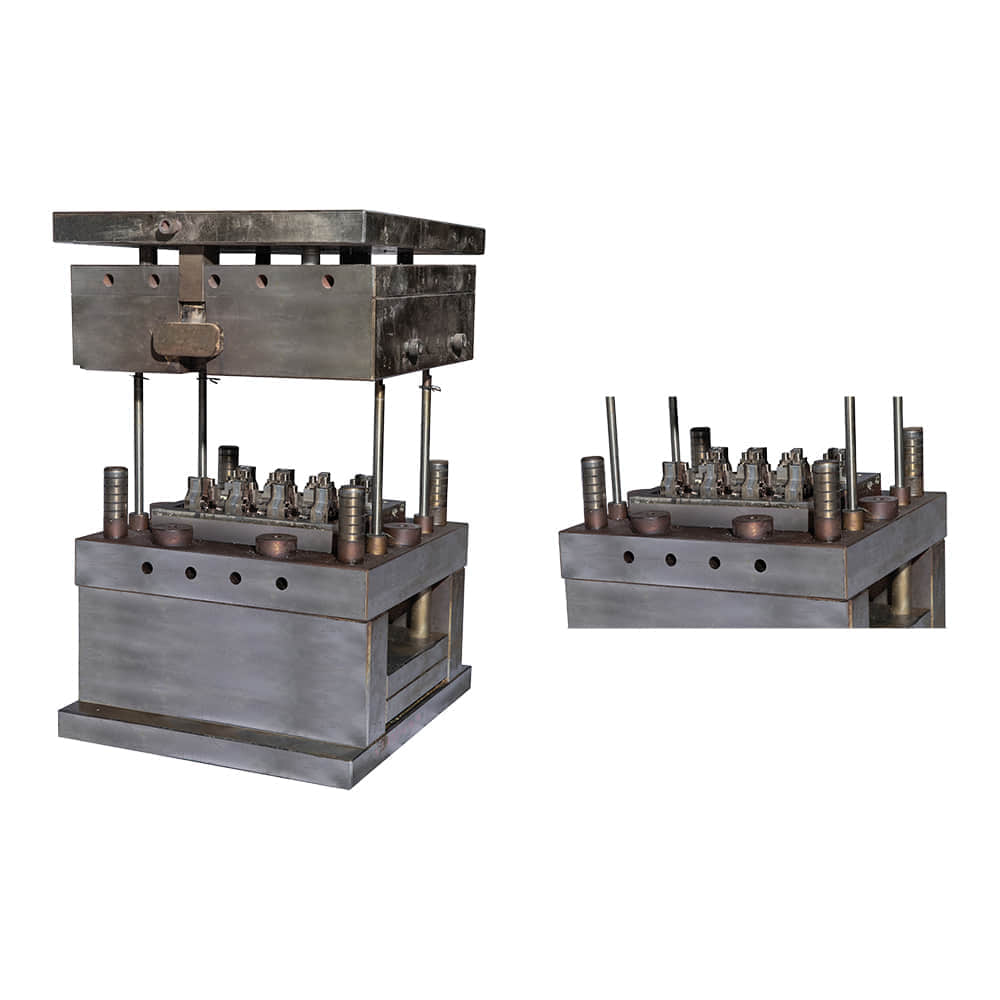
The Basics of SMC Molding SMC molding is a composite manufacturing process that involves the compression molding of a pre-mixed composite material. This material, known as Sheet Molding Compound, typically consists of a blend of thermosetting resins, reinforcing fibers (such as glass or carbon), additives, and fillers. These components are precisely mixed to create a homogeneous sheet of composite material. The SMC process begins with the preparation of this sheet, which is then placed in a heated mold cavity. Pressure is applied, and the material is cured, resulting in a part with exceptional strength and durability. The process can be customized to produce a wide range of shapes and sizes, making it versatile for various applications. Applications Across Industries One of the remarkable aspects of SMC molding is its versatility, which has led to its adoption in numerous industries: Automotive:SMC components are increasingly used in automotive manufacturing due to their lightweight properties, corrosion resistance, and ability to meet stringent safety standards. Bumpers, hoods, and interior components are just a few examples. Construction:SMC materials are utilized in the construction of architectural panels, utility boxes, and infrastructure components due to their weather resistance and long-term durability. Electrical:The excellent electrical insulation properties of SMC make it ideal for electrical enclosures, insulators, and switchgear components. Aerospace:In aerospace applications, SMC parts are valued for their weight-saving potential, which can enhance fuel efficiency and reduce emissions. Renewable Energy:SMC molding plays a vital role in the production of components for wind turbines, solar panels, and other renewable energy systems, where durability and weather resistance are paramount. Consumer Goods:SMC is also used in the manufacturing of various consumer goods, from sports equipment to household appliances. Advantages of SMC Molding SMC molding offers several key advantages that contribute to its widespread adoption: High Strength:SMC parts are known for their exceptional strength-to-weight ratio, providing structural integrity while remaining lightweight. Corrosion Resistance:SMC materials are highly resistant to corrosion, making them suitable for outdoor and harsh environments. Design Flexibility:The molding process allows for complex and intricate part designs, including undercuts and deep draws. Excellent Surface Finish:SMC parts typically have a smooth, aesthetically pleasing surface finish that requires minimal post-processing. Cost-Efficiency:Mass production of SMC components can be cost-effective due to efficient molding processes and minimal waste. The Future of SMC Molding As industries continue to prioritize lightweight, durable, and sustainable materials, the future of SMC molding appears bright. Ongoing research and development efforts are focused on improving material properties, reducing cycle times, and exploring new applications. In the coming years, we can anticipate further innovations in SMC formulations, making them even more environmentally friendly and energy-efficient. This will likely lead to expanded use in electric vehicle manufacturing, aerospace advancements, and the construction of sustainable infrastructure. In conclusion, SMC molding has carved a significant niche in the world of composite materials and advanced manufacturing. Its versatility, strength, and wide-ranging applications make it a valuable asset across various industries. As technology advances and sustainability becomes an even greater concern, SMC molding is poised to play an increasingly pivotal role in shaping our future.
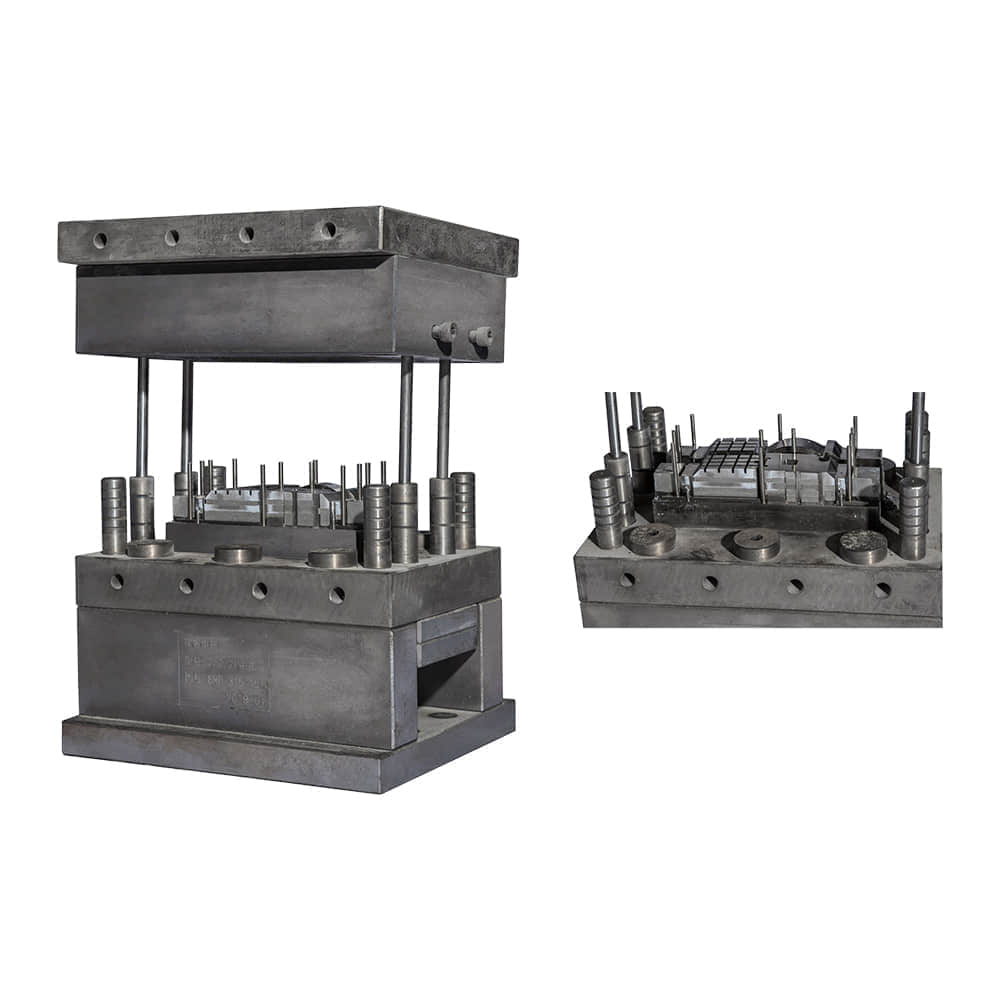