Thermosetting plastics are an essential component of numerous industries, including automotive, aerospace, electronics, and more. These materials are widely used for their outstanding mechanical and thermal properties. However, their transformation from raw materials into functional products requires the expertise of skilled thermosetting mold manufacturers. In this article, we delve into the world of thermosetting mold manufacturers, exploring their significance, processes, and innovations.
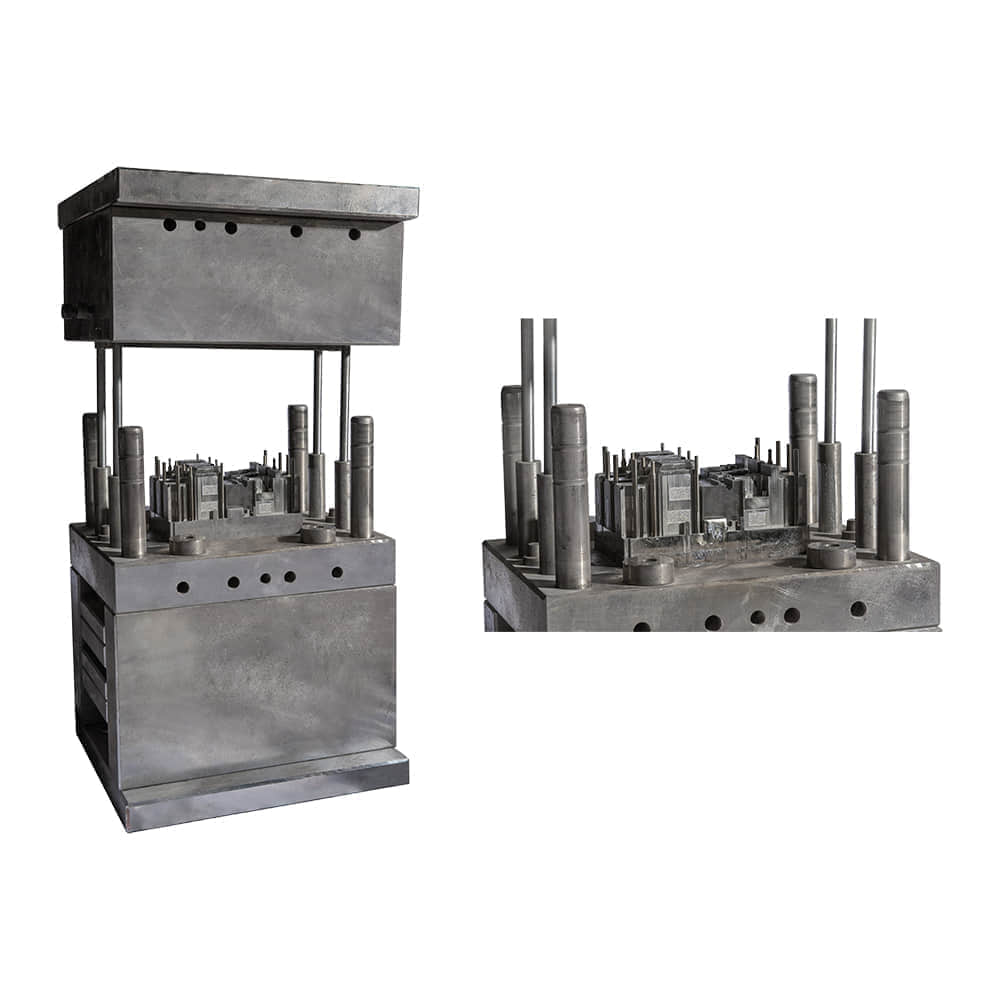
The Significance of Thermosetting Mold Manufacturers
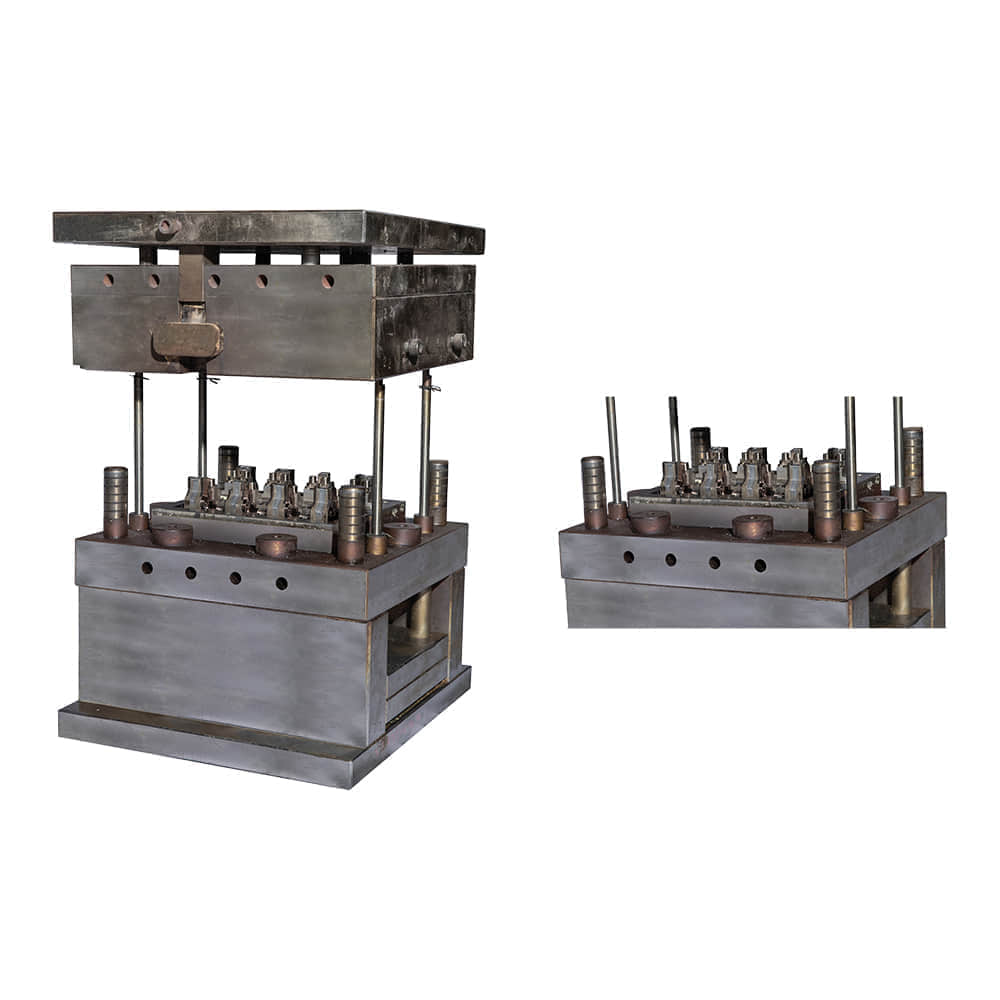
Thermosetting plastics, unlike thermoplastics, undergo a chemical change when heated, solidifying into a fixed form. This irreversible process demands precision and expertise in molding, making thermosetting mold manufacturers invaluable. They play a pivotal role in various industries by producing molds that shape these materials into components, parts, and products with exceptional durability and heat resistance. The Molding Process Thermosetting mold manufacturers employ a meticulous process to create molds that meet industry-specific requirements. The process typically involves the following steps: 1. Material Selection:The first step is selecting the appropriate thermosetting material, such as epoxy, phenolic, or melamine. The choice depends on factors like intended use, mechanical properties, and resistance to heat and chemicals. 2. Mold Design:Manufacturers design molds based on the desired shape and dimensions of the final product. This stage involves CAD (Computer-Aided Design) and CAM (Computer-Aided Manufacturing) software to ensure precision. 3. Mold Fabrication:Skilled craftsmen then create the mold using various techniques, such as machining, CNC milling, or electrical discharge machining (EDM), depending on the complexity and material requirements. 4. Mold Preheating:Before molding, the mold is preheated to a specific temperature to facilitate the curing process of the thermosetting material. 5. Material Injection:The thermosetting material is injected into the preheated mold cavity, taking the desired shape and hardening during the curing process. 6. Cooling and Demolding:After curing, the mold is cooled, and the hardened product is carefully removed from the mold. 7. Quality Control:Strict quality control measures ensure that the molded product meets all specifications, including dimensions, surface finish, and mechanical properties. Innovations in Thermosetting Molding To stay competitive and meet the evolving demands of industries, thermosetting mold manufacturers are continually innovating. Some notable advancements include: 1. 3D Printing:Additive manufacturing technologies, such as 3D printing, have revolutionized mold fabrication. Complex and customized molds can be created more efficiently, reducing lead times and costs. 2. Composite Molds:Manufacturers are experimenting with composite materials for molds, combining the strength of metals with the lightweight properties of composites, leading to enhanced durability and reduced energy consumption during the molding process. 3. IoT Integration:The Internet of Things (IoT) is being incorporated into mold manufacturing, allowing for real-time monitoring of mold conditions, temperature, pressure, and other critical parameters to optimize production and quality. 4. Sustainable Practices:Many manufacturers are adopting sustainable practices by recycling and reusing materials, reducing waste, and minimizing energy consumption in their processes. Conclusion Thermosetting mold manufacturers are the backbone of industries that rely on high-performance thermosetting plastics. Their expertise and innovation in mold design and fabrication are essential for producing durable and heat-resistant components. As technology continues to advance, we can expect even more efficient and sustainable practices from these manufacturers, further contributing to the success of various industries.
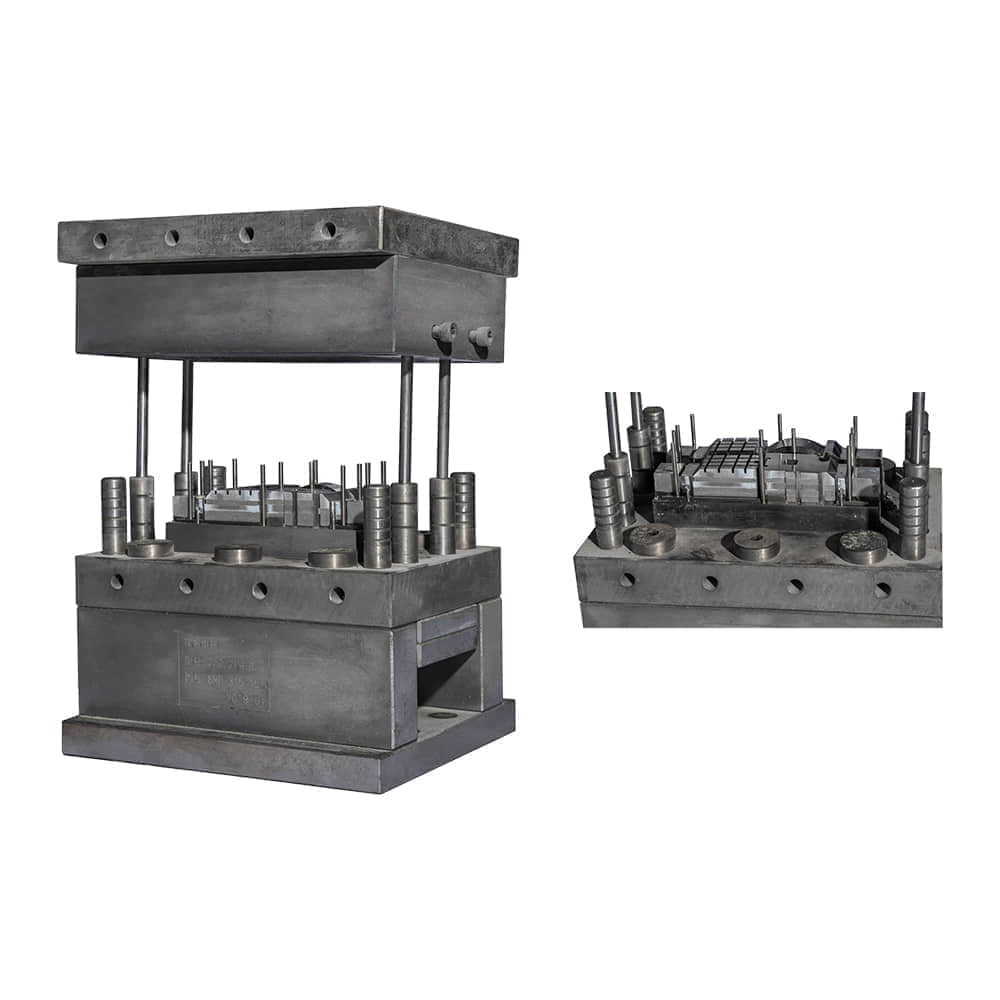