Molded Case Parts, a crucial aspect of modern manufacturing, play a pivotal role in various industries, including electronics, automotive, medical, and aerospace. These precision-molded components, often made from plastic or rubber, offer a range of benefits that make them indispensable in numerous applications.
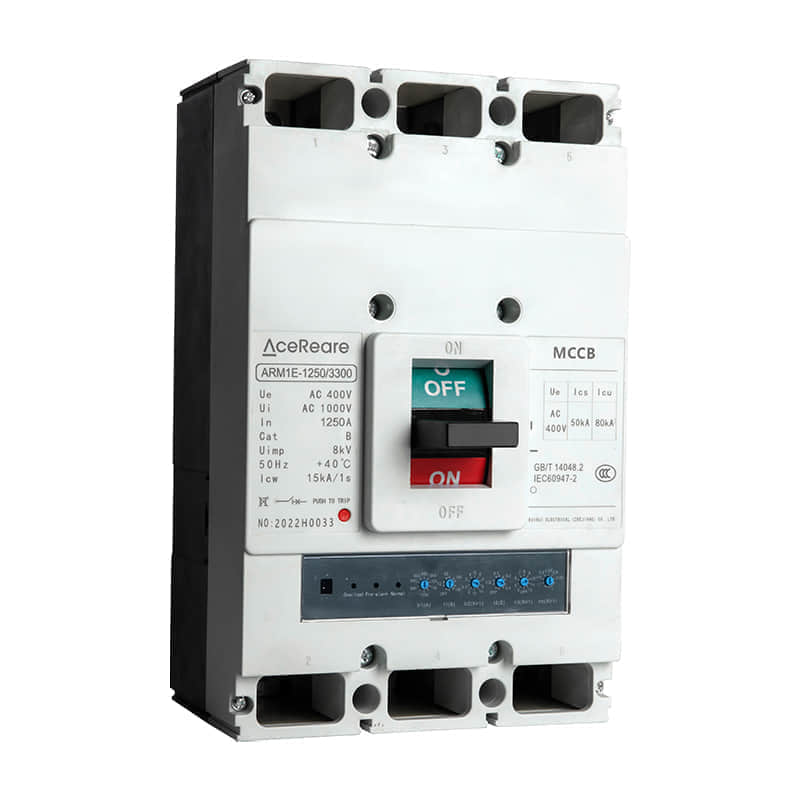
The process of molding Case Parts typically involves the use of molds or dies to shape the material into the desired form. Injection molding is a common technique, where molten plastic is injected into a mold cavity under high pressure, taking the shape of the cavity and solidifying to form the part. Other molding methods include compression molding, transfer molding, and vacuum molding, depending on the specific requirements of the application.
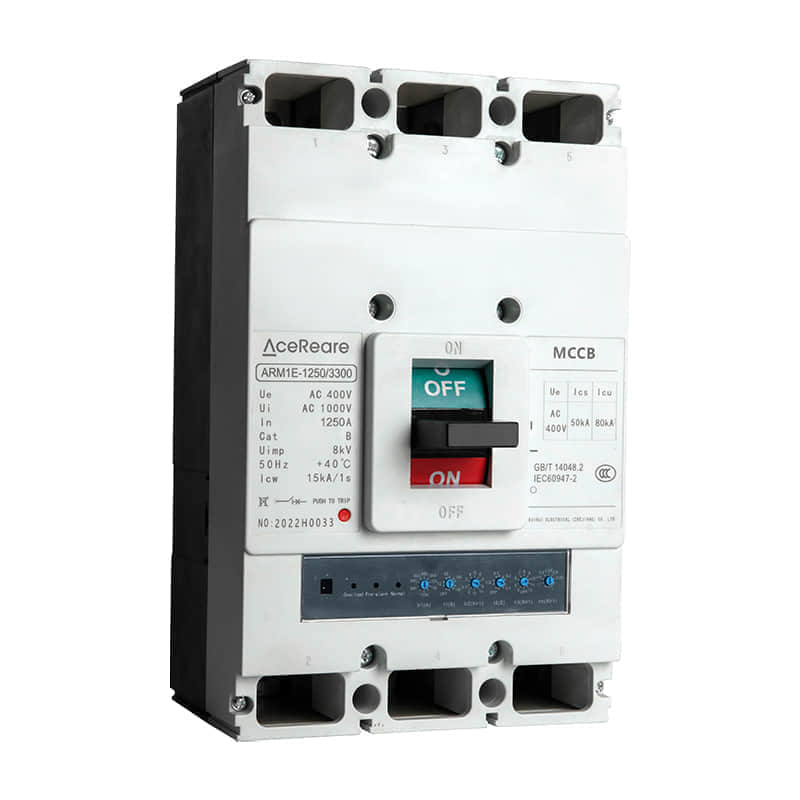
The materials used for Molded Case Parts are diverse and tailored to meet the needs of each application. Engineering plastics, such as nylon, polyester, and polycarbonate, offer excellent mechanical properties, heat resistance, and chemical stability. General-purpose plastics like ABS, polyethylene, and polypropylene are also widely used, thanks to their cost-effectiveness and versatility. The significance of Molded Case Parts lies in their numerous advantages. Firstly, they offer excellent durability and resistance to impact, making them suitable for use in demanding environments. Secondly, these parts provide excellent insulation, protecting sensitive electronic components from damage. Furthermore, their chemical resistance makes them suitable for use in corrosive environments.
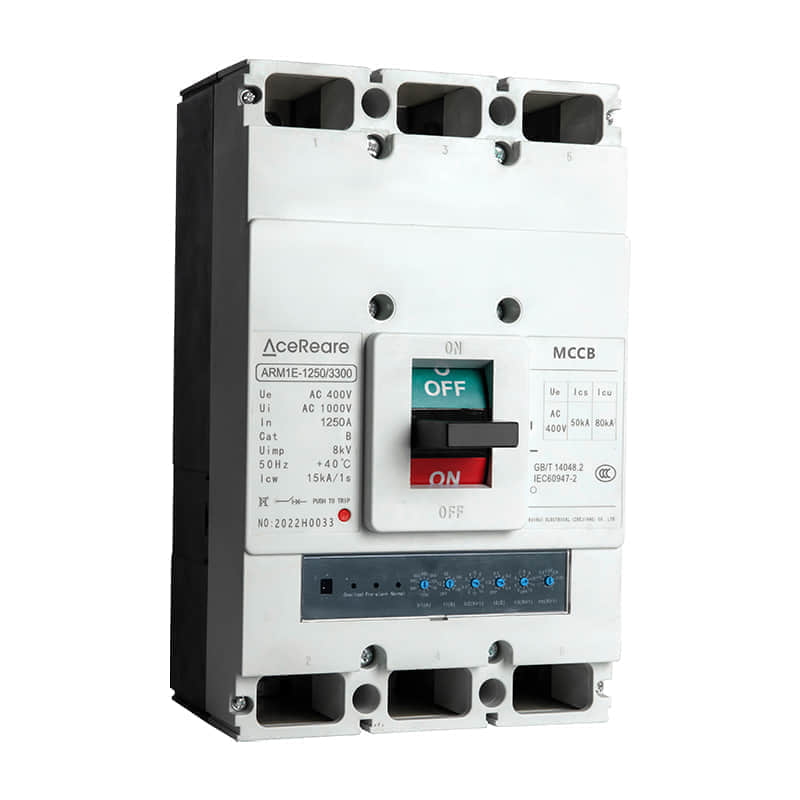