Introduction
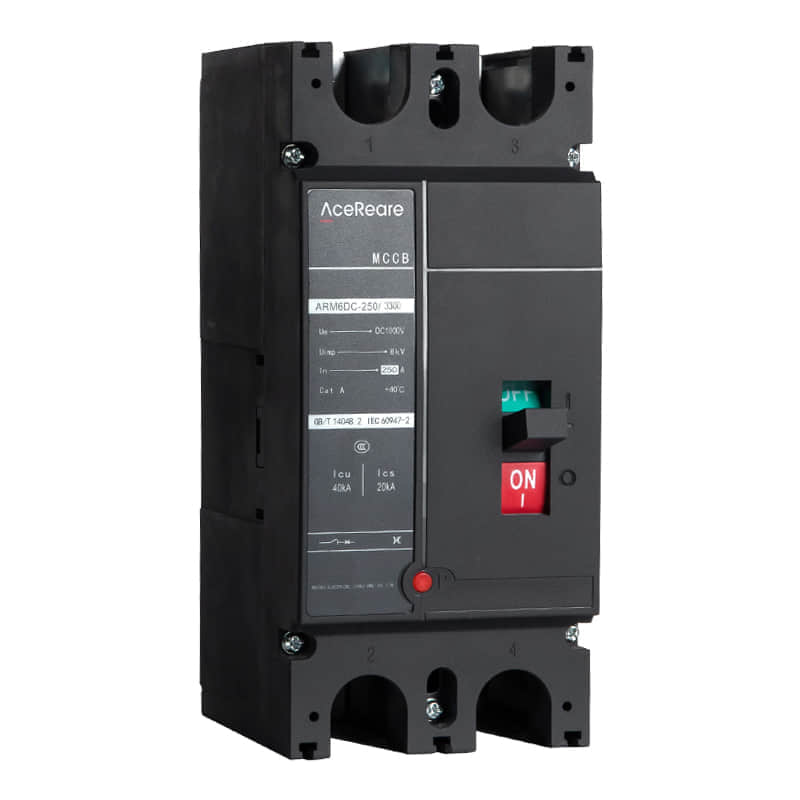
Molded Case Circuit Breakers (MCCBs) are essential components of electrical distribution systems. They play a crucial role in protecting electrical circuits and equipment from overloads and short circuits. The manufacturing process of MCCBs involves several intricate steps to ensure their reliability, safety, and performance. This article provides an overview of the manufacturing process of MCCBs, highlighting the key stages involved.
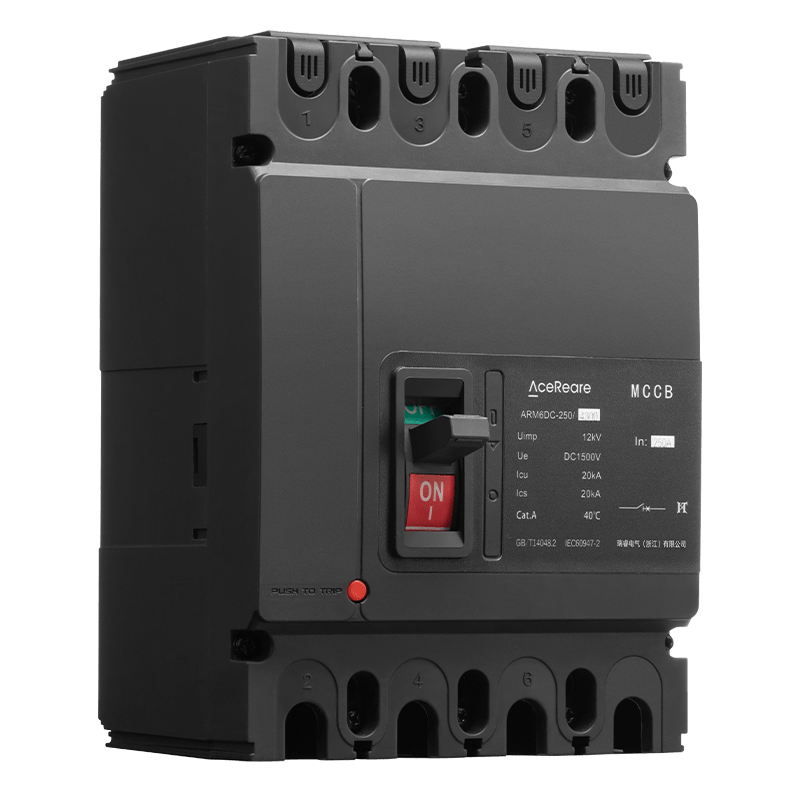
Design and Development The manufacturing of MCCBs begins with the design and development phase. Engineers and designers collaborate to create the product specifications, taking into account factors such as current rating, voltage rating, breaking capacity, and environmental conditions. The design process involves selecting suitable materials for the housing, internal components, and insulation, ensuring that the MCCB meets industry standards and regulations. Material Selection The choice of materials is critical to the performance and longevity of MCCBs. The housing is typically made of high-quality thermosetting plastics that offer excellent mechanical strength, insulation, and fire resistance. Internal components, such as contacts and trip mechanisms, are often constructed from materials with high conductivity and heat resistance to ensure efficient current interruption and minimal energy loss. Manufacturing of Components The manufacturing process of MCCB components involves various techniques such as injection molding, stamping, and machining. The housing is created through injection molding, where the selected plastic material is heated, melted, and injected into molds to form the desired shape. Internal components like contacts are often stamped or machined from materials like copper or silver alloys for their superior electrical conductivity. Assembly The assembly process is a critical stage where individual components come together to form a functional MCCB. Skilled technicians carefully assemble components such as contacts, arc chutes, trip mechanisms, and auxiliary switches according to precise specifications. The assembly must be precise to ensure that the MCCB operates correctly under different fault conditions. Calibration and Testing After assembly, each MCCB undergoes calibration and rigorous testing. Calibration ensures that the trip mechanism operates accurately for various levels of current and fault conditions. Testing involves assessing parameters like tripping time, breaking capacity, insulation resistance, and temperature rise. Only MCCBs that meet the specified performance criteria proceed to the next stage. Quality Control Quality control is integrated into every step of the manufacturing process. Regular inspections and quality checks help identify any deviations or defects, ensuring that the final product meets safety standards and customer expectations. Any non-conforming components or MCCBs are rejected or reworked to maintain the highest quality. Packaging and Distribution Once MCCBs pass quality control, they are packaged and prepared for distribution. Proper packaging is essential to protect the MCCBs during transportation and storage. Clear labeling and documentation accompany each MCCB to provide users with important information such as ratings, installation instructions, and safety precautions. Conclusion The manufacture of Molded Case Circuit Breakers is a meticulous process that combines engineering expertise, precise assembly techniques, and stringent quality control measures. These electrical components are vital for safeguarding electrical systems, making their reliable performance crucial. By following a systematic manufacturing approach, MCCB manufacturers ensure that their products meet industry standards and contribute to the safe and efficient operation of electrical distribution systems worldwide.
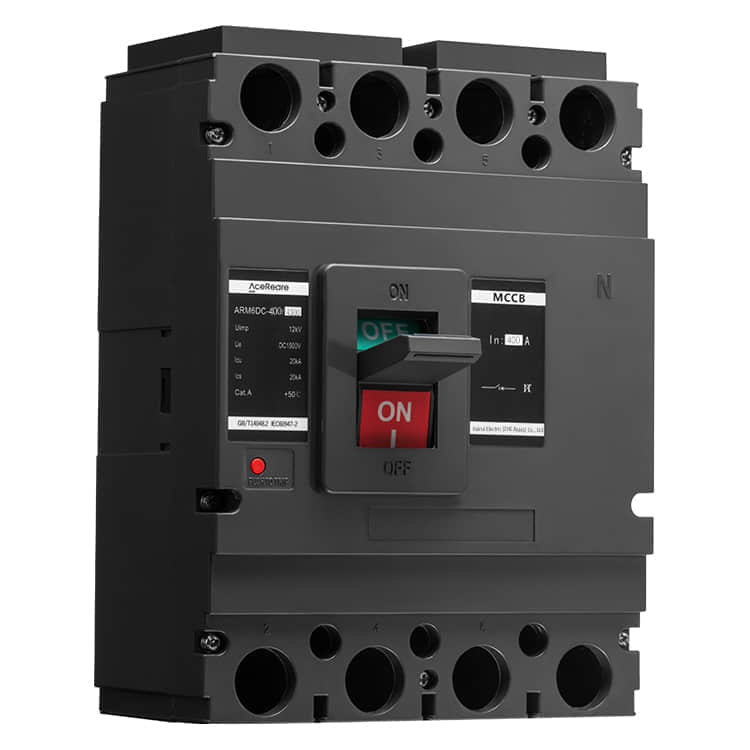