Moulded Case Circuit Breakers (MCCBs) play a crucial role in electrical systems by protecting circuits and electrical appliances from overcurrents. These devices are designed to interrupt the flow of electricity when it exceeds safe levels, preventing electrical fires and damage to equipment. In this article, we will explore the intricate process of manufacturing MCCBs, from the initial design phase to the final product assembly.
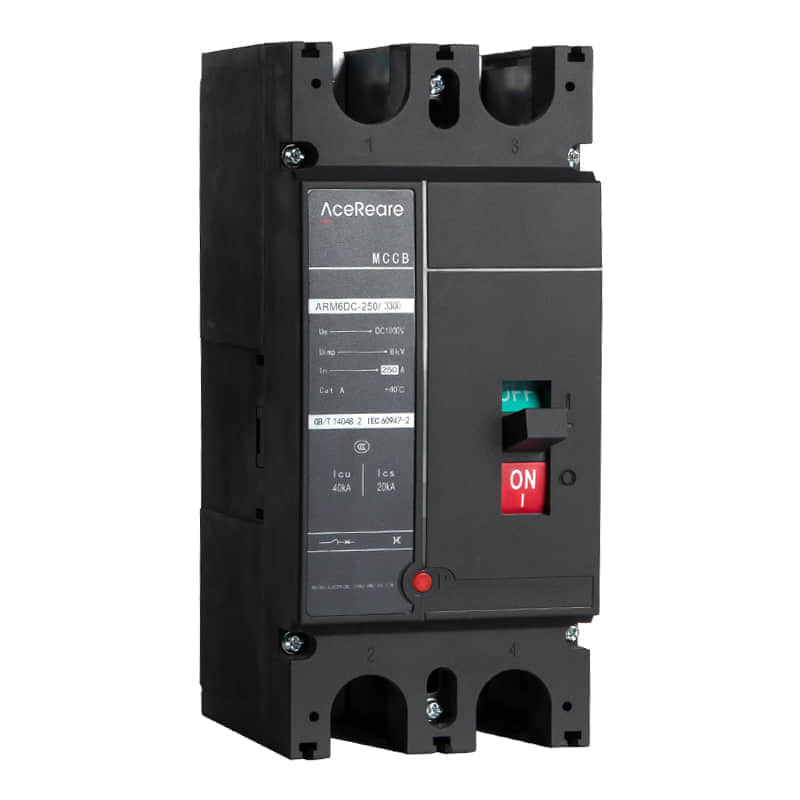
Design and Engineering
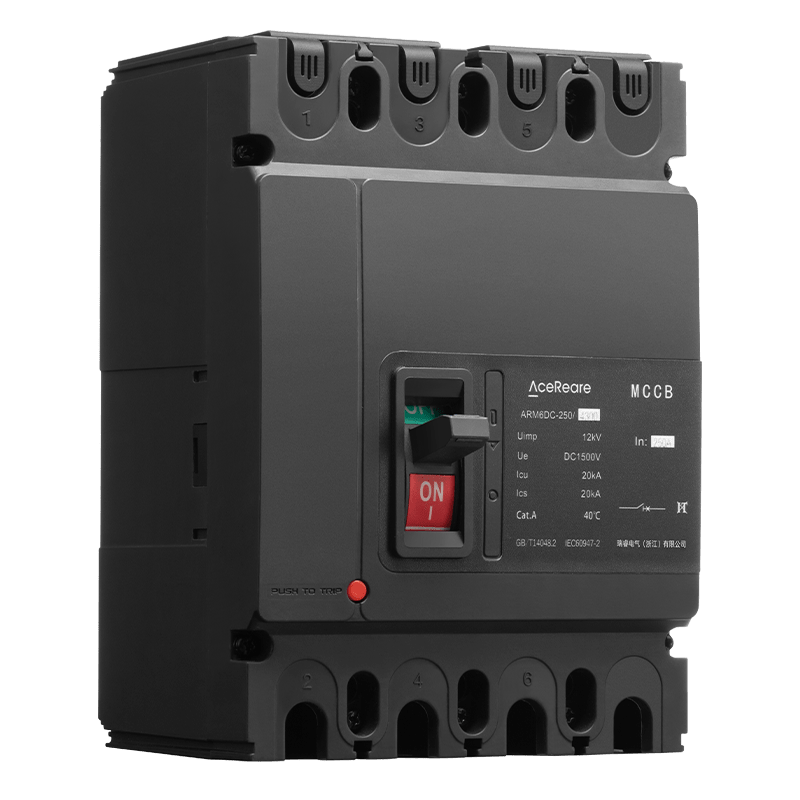
The journey of manufacturing an MCCB begins with meticulous design and engineering. Electrical engineers and product designers work together to create a product that meets safety standards and performance requirements. The design phase involves selecting the appropriate materials, determining the electrical rating, and ensuring the MCCB’s compatibility with various electrical systems. Material Selection Selecting the right materials is crucial for the MCCB’s reliability and safety. The housing or frame of the MCCB is typically made from high-quality, flame-retardant thermoplastics or thermosetting materials that can withstand high temperatures and mechanical stress. The internal components, such as contacts and trip units, are made from materials with excellent electrical conductivity and heat resistance. Manufacturing of Components Once the materials are selected, the manufacturing process begins. This phase involves creating the various components of the MCCB, including the arc extinguishing chamber, operating mechanism, and thermal or magnetic trip units. Advanced machining and molding techniques are employed to ensure precision and consistency in the components’ production. Assembly With the components ready, the MCCB assembly process can commence. Skilled technicians carefully assemble the MCCB, following strict quality control protocols. The arc extinguishing chamber, which plays a vital role in extinguishing arcs created during overcurrents, is carefully positioned within the housing. The contacts, designed to carry and interrupt electrical currents, are aligned precisely. Quality Control Quality control is a critical step in MCCB manufacturing. Each MCCB undergoes rigorous testing to ensure it meets safety and performance standards. This includes electrical testing to verify that the device trips at the correct current levels and mechanical testing to assess its durability and reliability. Calibration and Adjustment MCCBs often include trip units that can be adjusted to meet specific circuit protection requirements. During this phase, the trip units are calibrated to ensure they operate precisely as needed. This customization allows MCCBs to protect a wide range of electrical circuits with varying current levels. Final Inspection Before the MCCBs are packaged and shipped, a final inspection is conducted. This inspection includes visual checks to ensure the MCCB’s physical integrity, as well as functional tests to verify that it operates as designed. Any MCCBs that do not meet the stringent quality standards are rejected and either repaired or recycled. Packaging and Distribution Once the MCCBs pass the final inspection, they are carefully packaged to protect them during transportation. The packaging also includes detailed product information and instructions for installation and operation. MCCBs are then distributed to electrical wholesalers, retailers, and industrial customers worldwide. In conclusion, the manufacture of Moulded Case Circuit Breakers is a complex and highly precise process that involves careful design, material selection, component manufacturing, assembly, quality control, calibration, and final inspection. These steps ensure that MCCBs perform their critical role in safeguarding electrical systems and equipment. The commitment to quality and safety in MCCB manufacturing underscores their importance in modern electrical infrastructure.
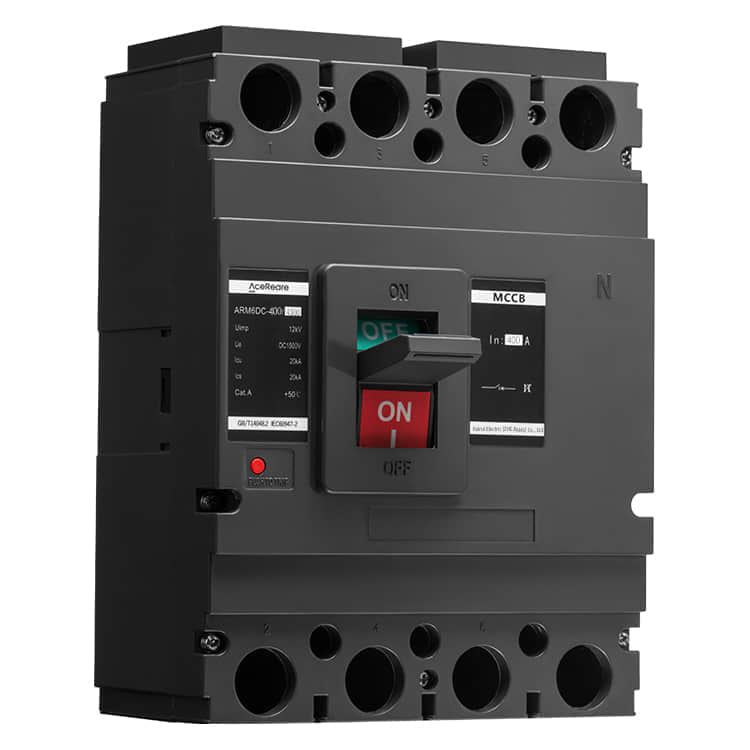