Metal Stamping: A Crucial Industrial Process
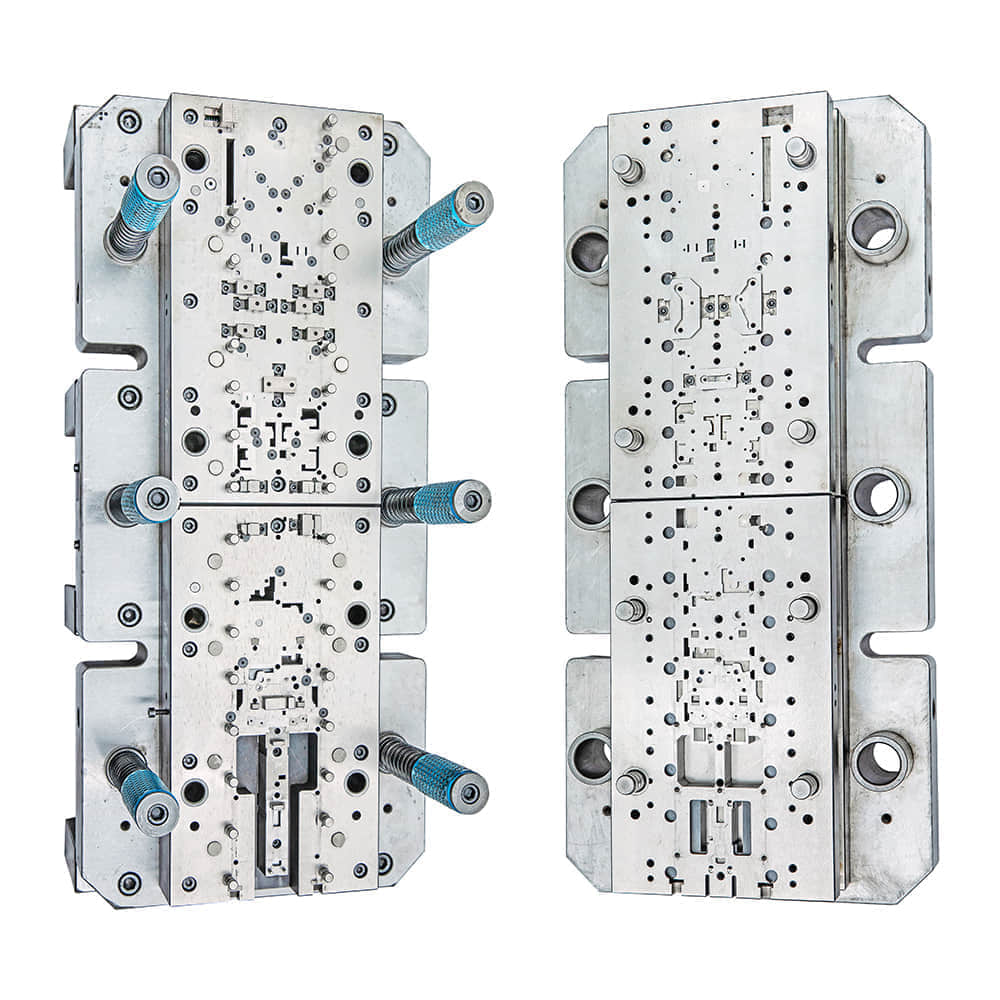
In the world of manufacturing, precision and efficiency are paramount. Whether it’s producing intricate components for the automotive industry or creating small yet vital parts for electronics, metal stamping plays a pivotal role. At the heart of this process lies the metal stamping die, and behind every great die is a dedicated Metal Stamping Die Manufacturer.
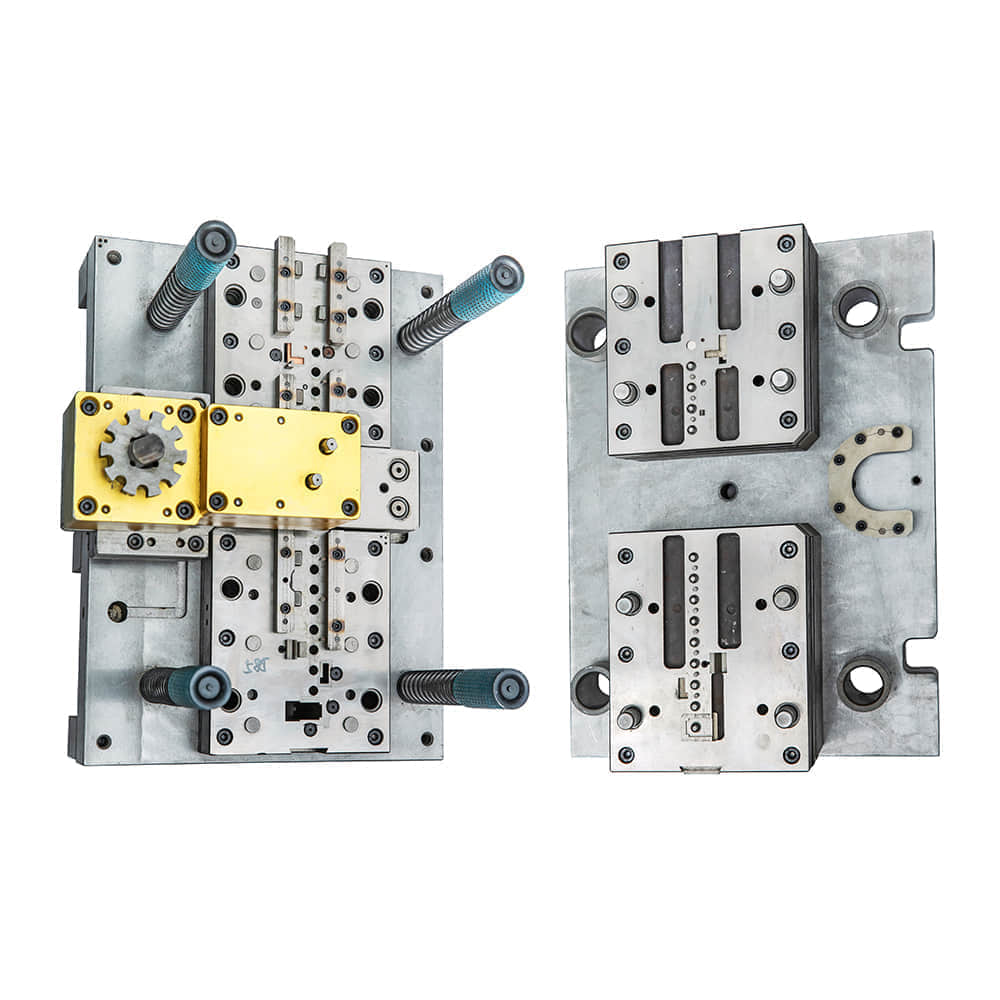
The Art and Science of Metal Stamping Dies Metal stamping dies are the unsung heroes of modern manufacturing. These specialized molds, often made of hardened steel, are meticulously designed and crafted to shape raw metal sheets into precise components. From simple brackets to complex gears, the quality of a metal stamping die can make or break a product’s performance. Behind every successful die is a Metal Stamping Die Manufacturer who combines art and science to create these essential tools. Let’s delve deeper into the world of these manufacturers and their pivotal role in the industry. Mastering Precision Engineering The process of metal stamping is all about precision. Even the tiniest imperfection in a die can result in faulty components and production delays. Metal Stamping Die Manufacturers are experts in precision engineering. They use cutting-edge technologies like computer-aided design (CAD) and computer numerical control (CNC) machining to create dies with astonishing accuracy. These manufacturers understand that every product has unique specifications. They work closely with their clients to develop custom dies that meet these requirements. Whether it’s crafting a die for a one-of-a-kind prototype or producing a die for mass production, precision is non-negotiable. Materials Matter To withstand the immense pressure and heat generated during the metal stamping process, the materials used in die manufacturing must be of the highest quality. Metal Stamping Die Manufacturers carefully select and test materials, ensuring they can endure the rigors of high-volume production without compromising on precision. Furthermore, the choice of materials can impact the lifespan of a die. Manufacturers aim for longevity, as replacing dies can be costly and time-consuming. Through metallurgical expertise, they strike the perfect balance between hardness and durability. Innovative Design and Prototyping Innovation is at the heart of the metal stamping die manufacturing process. Manufacturers invest in research and development to create cutting-edge designs and tooling techniques. They understand that the success of their clients’ projects often depends on the innovation embedded within their dies. Before mass production begins, prototypes are rigorously tested to ensure that the die performs flawlessly. Any adjustments or fine-tuning necessary to optimize the die’s performance are made at this stage. It’s a meticulous process that demands both skill and patience. Quality Assurance Quality assurance is an integral part of every Metal Stamping Die Manufacturer’s ethos. They employ rigorous quality control measures to guarantee that each die they produce meets the highest standards. This includes meticulous inspections, precision measurements, and performance testing. Manufacturers take pride in the fact that their dies contribute to the production of high-quality products across various industries. Whether it’s a critical safety component in an automobile or a miniature part in a medical device, the precision of metal stamping dies ensures product reliability. The Human Touch Behind the machinery and technology, there’s a human touch that sets Metal Stamping Die Manufacturers apart. Craftsmanship, honed through years of experience, plays a significant role in die production. The delicate art of hand-finishing and polishing can elevate a die from good to exceptional. In conclusion, Metal Stamping Die Manufacturers are the unsung heroes of modern manufacturing. Their precision engineering, choice of materials, innovative designs, and unwavering commitment to quality assurance ensure that the products we rely on every day meet the highest standards. As technology continues to advance, these manufacturers will remain at the forefront, pushing the boundaries of what’s possible in the world of metal stamping.
