In the realm of modern manufacturing, metal stamping dies play a pivotal role in shaping the products that power our world. These intricate tools, meticulously designed and crafted by skilled professionals, enable the mass production of complex metal components used in a wide range of industries. Metal stamping die manufacturers stand as the unsung heroes behind the scenes, contributing to technological advancement and innovation. This article delves into the world of metal stamping die manufacturers, exploring their significance, the craftsmanship involved, and the impact of their work on various sectors.
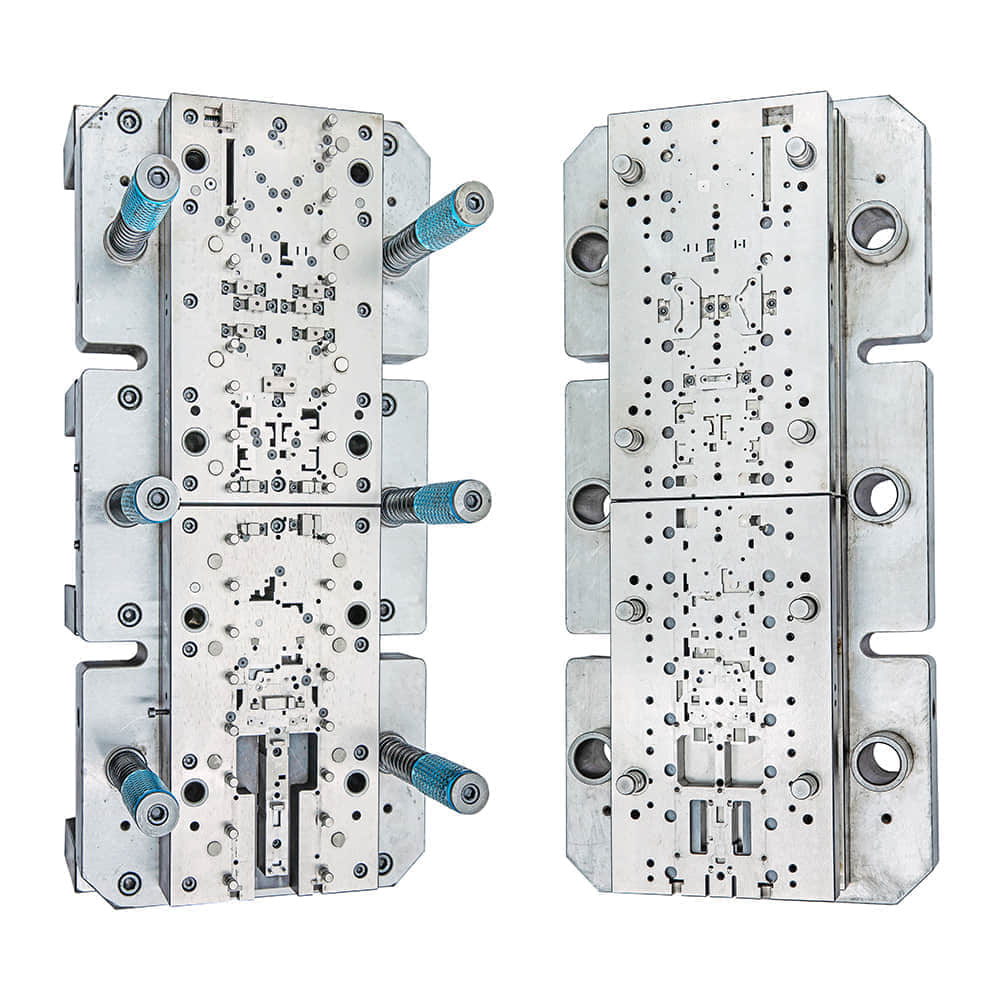
Crafting Precision with Expertise

Metal stamping die manufacturers are the architects of industrial precision. Their expertise lies in designing and fabricating molds that transform raw metal sheets into intricate parts used in automobiles, electronics, appliances, aerospace, and beyond. Every detail matters in this process, from the design of the die to the choice of materials, heat treatment, and finishing. Manufacturers use advanced software and cutting-edge machinery to create dies that guarantee high-quality, consistent, and accurate outputs in large-scale production settings. The Intersection of Art and Engineering Creating metal stamping dies is a delicate dance between art and engineering. It requires not only a deep understanding of material properties, mechanical principles, and production processes but also a keen eye for detail and creativity. Manufacturers must strike a balance between functionality and aesthetics, ensuring that the die not only produces precise components but also optimizes material usage and minimizes waste. This intricate interplay of factors showcases the fusion of science and artistry in modern manufacturing. Driving Innovation Across Industries The impact of metal stamping die manufacturers reverberates across industries. In the automotive sector, these manufacturers contribute to the production of engine parts, body panels, and structural components, enhancing vehicle safety and efficiency. In electronics, they enable the creation of intricate parts for devices like smartphones and computers. Aerospace applications benefit from their work in producing lightweight yet robust components critical for flight. Their contributions extend to everyday items as well, including kitchen appliances and medical equipment. Meeting Challenges Head-On Manufacturing precision is not without its challenges. Metal stamping die manufacturers continually push the boundaries of technology to meet the demands of increasingly complex designs and tighter tolerances. They tackle challenges such as minimizing defects, reducing cycle times, and improving tool life. Additionally, environmental concerns drive the need for sustainable practices in die manufacturing, urging manufacturers to explore eco-friendly materials and energy-efficient processes. Collaboration and Customization Successful metal stamping die manufacturing thrives on collaboration. Manufacturers work closely with clients, understanding their unique needs and translating them into functional designs. Customization is often key, as industries demand components tailored to specific requirements. This collaborative approach ensures that the final product aligns with the client’s vision while meeting industry standards for quality and performance. The Path Forward As industries continue to evolve, so too will the role of metal stamping die manufacturers. The integration of technologies like artificial intelligence, simulation software, and additive manufacturing is poised to reshape the landscape. These advancements promise to streamline the design process, enhance precision, and reduce lead times. However, at its core, the craftsmanship, dedication, and ingenuity of metal stamping die manufacturers will remain fundamental to driving manufacturing excellence. In conclusion, metal stamping die manufacturers are the architects of industrial progress, shaping the products that shape our world. Their precision craftsmanship, blending expertise and creativity, fuels innovation across diverse sectors. Challenges are met with determination, and collaboration with clients ensures customized solutions. As technology marches forward, the essence of their work will continue to be a cornerstone of efficient, precise, and sustainable manufacturing processes.
