In the world of manufacturing, metal stamping parts play a crucial role in various industries, from automotive to electronics. These parts are the backbone of countless products, ensuring their functionality, durability, and precision. Behind the scenes, metal stamping parts manufacturers are the unsung heroes, driving innovation and quality in manufacturing processes. In this article, we will delve into the world of metal stamping parts manufacturers, exploring their significance, processes, and commitment to excellence.
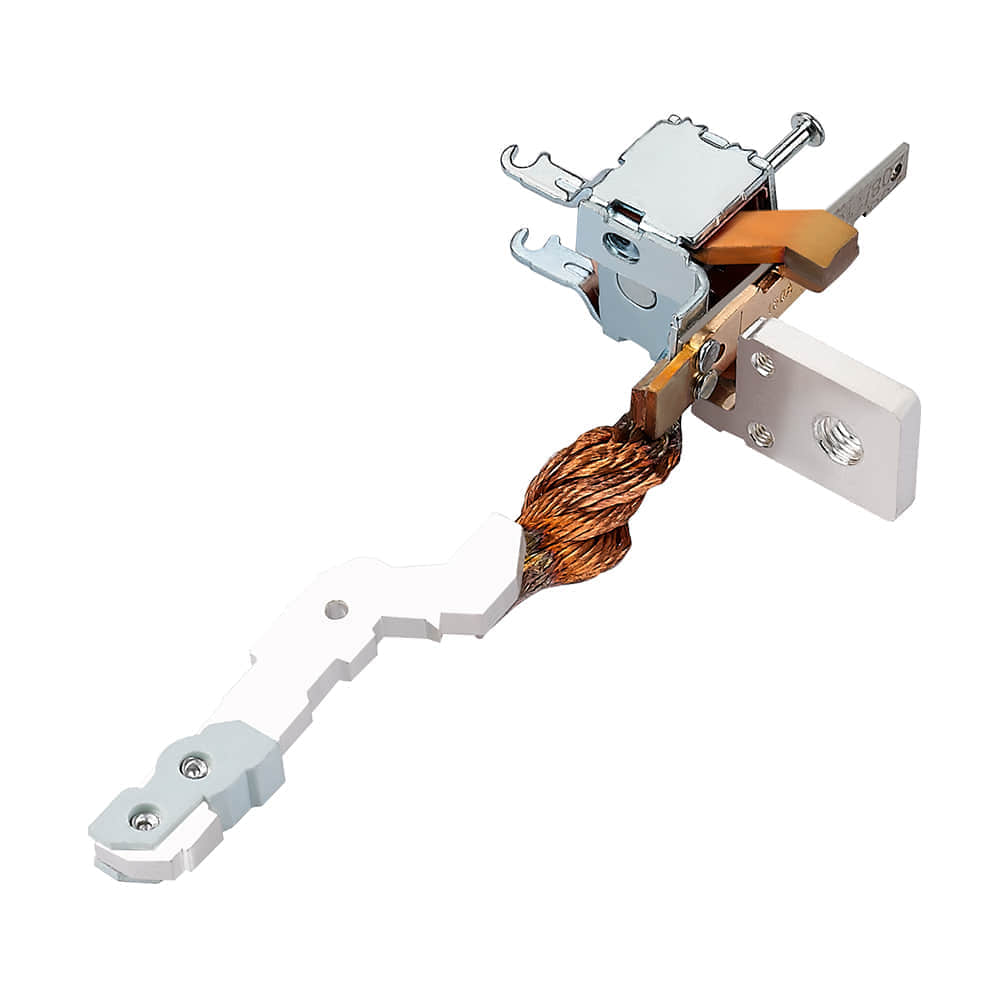
Precision in Every Detail
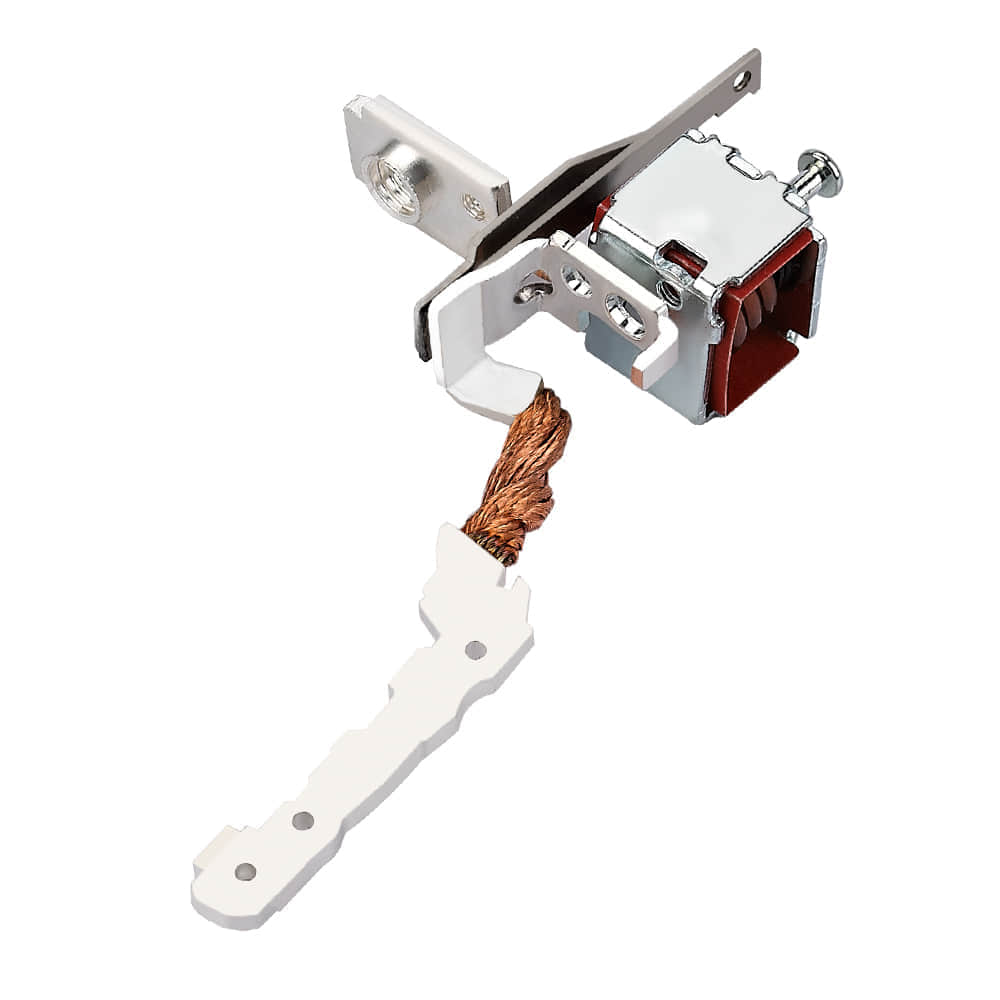
Metal stamping is a manufacturing process that involves shaping sheets of metal into desired forms and sizes. It requires precision machinery, skilled operators, and meticulous attention to detail. Metal stamping parts manufacturers excel in all these aspects, delivering parts that meet the most stringent quality standards. One of the defining features of metal stamping is its ability to produce consistent, high-quality parts. Manufacturers employ computer-controlled machines, ensuring every piece is identical to the last. This precision is essential for industries where even the slightest deviation can lead to catastrophic consequences, such as aerospace and medical equipment manufacturing. Materials and Innovation Metal stamping parts manufacturers work with a wide range of materials, from steel and aluminum to exotic alloys. Their expertise lies not only in shaping these materials but also in selecting the right material for each application. This involves an in-depth understanding of material properties, durability, and cost-effectiveness. Moreover, innovation is a driving force in this industry. Manufacturers constantly explore new materials, technologies, and processes to improve the efficiency and performance of metal stamping parts. This commitment to innovation ensures that customers receive parts that are not only of high quality but also cost-effective. The Production Process The metal stamping process involves a series of steps, each executed with precision: Material Selection: Manufacturers choose the appropriate metal sheet for the intended part, considering factors like thickness and strength. Tool Design: Engineers design the stamping dies, which are precision tools that shape the metal. Stamping: The metal sheet is placed in the stamping press, and the die is used to cut and shape it. Quality Control: Each part undergoes rigorous quality checks to ensure it meets the required specifications. Finishing: Depending on the application, parts may undergo additional processes like welding, plating, or coating. Packaging and Delivery: Finished parts are carefully packaged and delivered to the customer. Throughout this process, manufacturers employ skilled technicians and engineers who oversee every aspect to ensure the highest level of quality. Customization and Flexibility Metal stamping parts manufacturers offer customization options to meet the unique requirements of their customers. Whether it’s designing a specific part or adapting an existing design, these manufacturers are equipped to deliver tailor-made solutions. This flexibility is invaluable to industries with specialized needs. Environmental Responsibility In recent years, environmental sustainability has become a significant concern for manufacturers. Metal stamping parts manufacturers are no exception. Many have adopted eco-friendly practices, such as recycling scrap metal and using energy-efficient machinery. This commitment to sustainability not only benefits the environment but also resonates with environmentally conscious customers. Conclusion Metal stamping parts manufacturers are the backbone of modern manufacturing. Their precision, innovation, and commitment to quality ensure that industries across the spectrum can rely on them for critical components. As technology continues to advance, we can expect metal stamping to evolve further, pushing the boundaries of what is possible in the world of manufacturing. These manufacturers are more than just producers; they are the driving force behind progress and innovation.
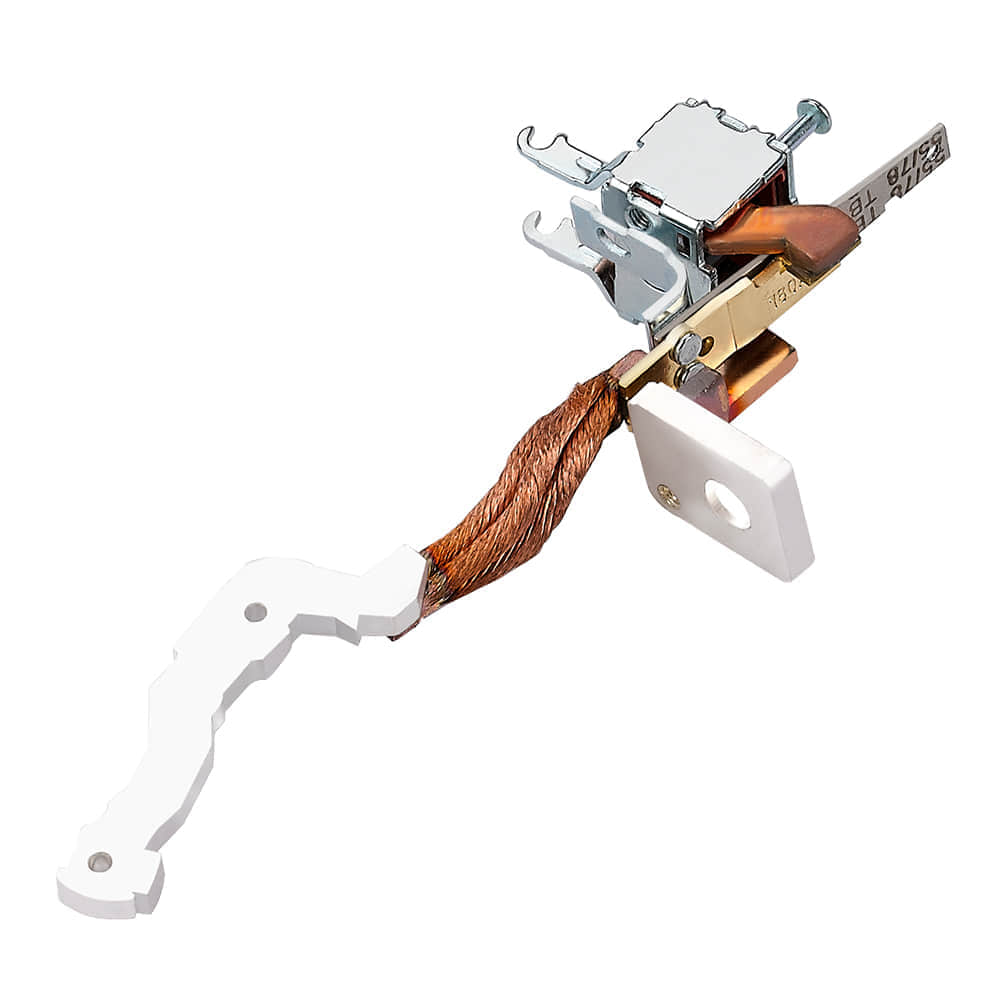