The Moulded Case Circuit Breaker (MCCB) manufacturing industry has been at the forefront of electrical protection for decades, playing a pivotal role in safeguarding electrical systems from potential hazards. This article delves into the intricacies of MCCB manufacturing, highlighting its significance, challenges, and advancements in the field.
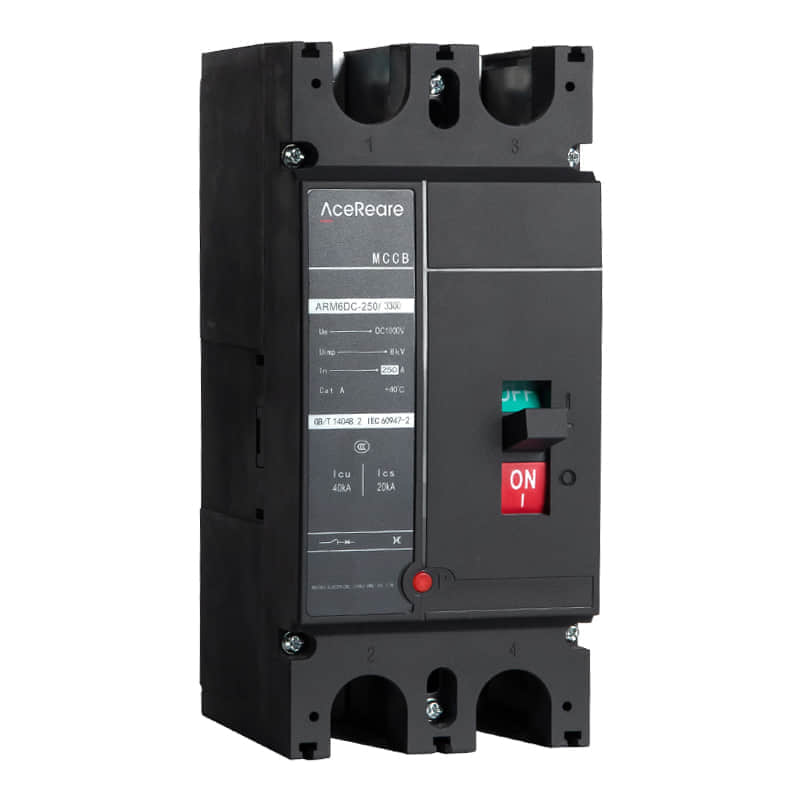
MCCBs, also known as molded case circuit breakers, are designed to provide circuit protection in low-voltage distribution systems. Their compact design, combined with superior performance, has made them a popular choice for both industrial and commercial applications. The manufacturing process of MCCBs involves precision engineering, high-quality materials, and strict quality control measures to ensure reliability and durability.
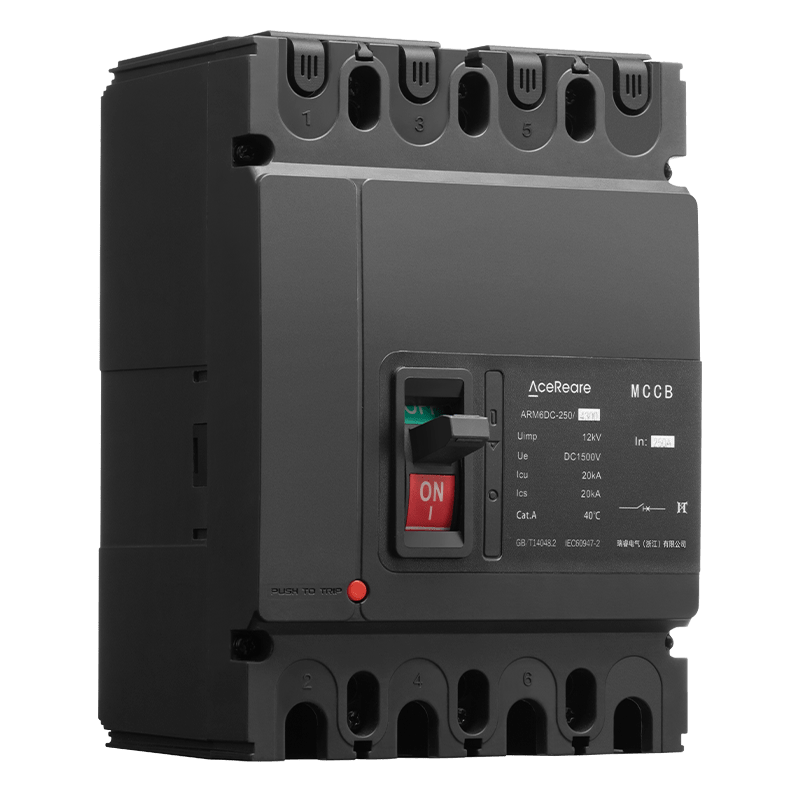
The core of any MCCB is its tripping mechanism, which is responsible for interrupting the circuit in the event of an overload or short circuit. Manufacturers employ advanced technologies to design and fabricate these mechanisms, ensuring quick and accurate response times. The use of modern simulation software allows for detailed analysis and optimization of the tripping mechanism’s performance, leading to improved safety and reliability. Materials selection is another crucial aspect of MCCB manufacturing. Manufacturers utilize high-grade thermoplastic resins and insulating materials to ensure the breaker’s structural integrity and electrical insulation. These materials must withstand high temperatures, mechanical stress, and chemical exposure to maintain the breaker’s performance over its lifetime.
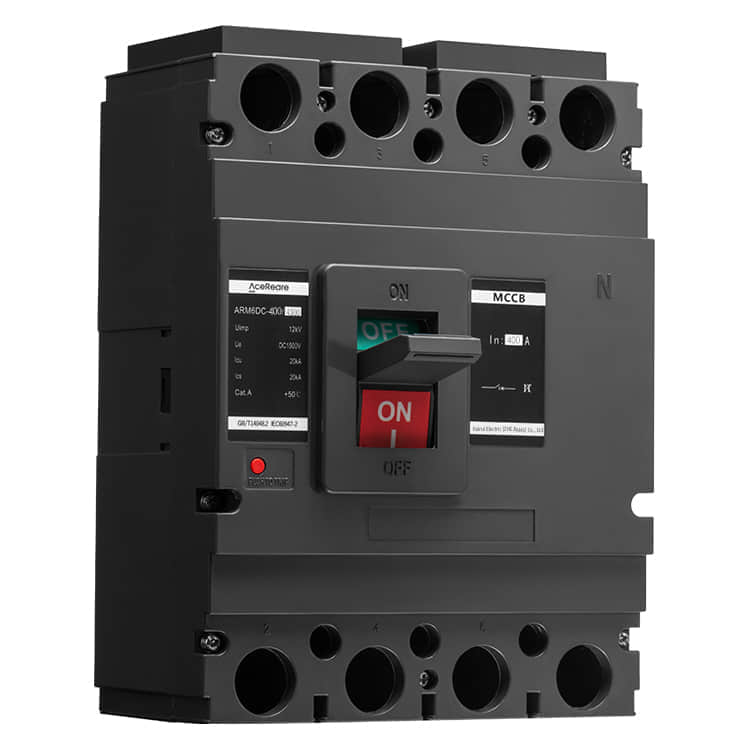