Introduction
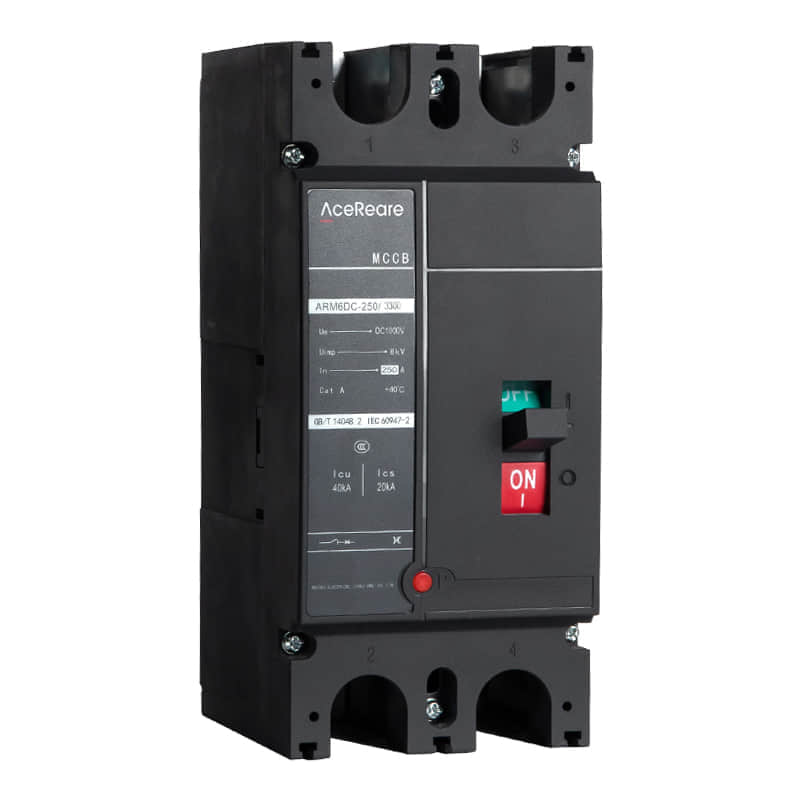
Moulded Case Circuit Breakers (MCCBs) play a vital role in maintaining electrical safety by protecting circuits and equipment from overloads and short circuits. The manufacturing process of MCCBs involves intricate engineering and quality control to ensure their reliable performance. This article delves into the various stages of MCCB manufacturing, highlighting the key steps that ensure the production of high-quality circuit breakers.
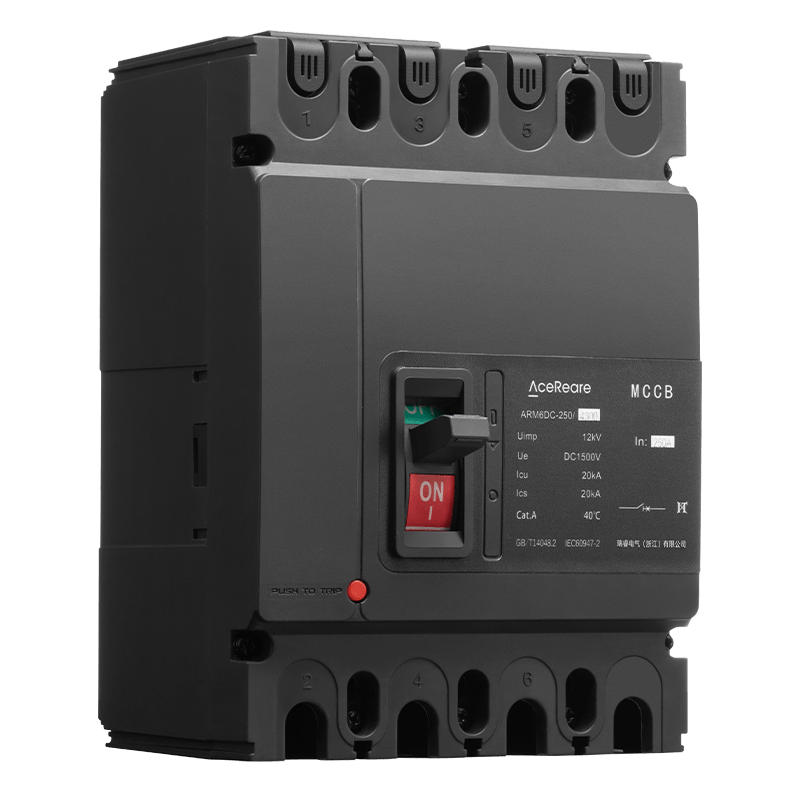
Design and Engineering The manufacturing journey of MCCBs begins with meticulous design and engineering. Experienced engineers collaborate to create designs that meet industry standards and specific customer requirements. The design phase involves selecting appropriate materials, determining the optimal circuit configuration, and calculating the breaker’s current-carrying capacity. Material Selection The choice of materials is critical to the MCCB’s performance and durability. High-quality insulating materials, conductive parts, and arc-quenching materials are carefully selected to withstand the electrical and thermal stresses that MCCBs may encounter during operation. These materials ensure the breaker’s ability to interrupt faults without compromising safety. Component Manufacturing The manufacturing of MCCB components involves precision machining, casting, and molding. Conductive parts, such as contacts and terminals, are machined to exact specifications to ensure proper electrical connections. Insulating components are often molded from durable plastics or ceramics, providing excellent insulation and mechanical strength. Assembly Assembly is a crucial phase where all the individual components come together to form a functional MCCB. Skilled technicians meticulously assemble the breaker according to the design, ensuring proper alignment and secure connections. The assembly process includes fitting the contacts, arc chutes, trip units, and other essential components. Calibration and Testing After assembly, each MCCB undergoes a series of rigorous tests to verify its performance and reliability. Calibration of the trip unit is a critical step to ensure accurate and consistent tripping at specified currents. Various tests, such as temperature rise, short-circuit withstand, and endurance tests, are conducted to ensure that the breaker can operate effectively under different conditions. Quality Control Stringent quality control measures are implemented throughout the manufacturing process. Automated inspections and manual checks are performed to identify any defects or deviations from the desired specifications. Any MCCB that does not meet the set standards is rejected, emphasizing the commitment to delivering only top-quality products. Packaging and Distribution Once the MCCBs pass all tests and quality checks, they are packaged carefully to prevent damage during transportation. Clear labeling and user manuals are included to guide electricians and users in proper installation and usage. The distribution network ensures that MCCBs are delivered to various industries, including residential, commercial, and industrial sectors. Conclusion Moulded Case Circuit Breakers are integral to modern electrical systems, providing a crucial layer of protection against electrical faults. The journey from design and engineering to manufacturing and distribution involves a series of precise steps to ensure the production of reliable and high-performance MCCBs. The commitment to quality, safety, and innovation in MCCB manufacturing contributes significantly to the overall stability of electrical networks and the safety of individuals and assets.
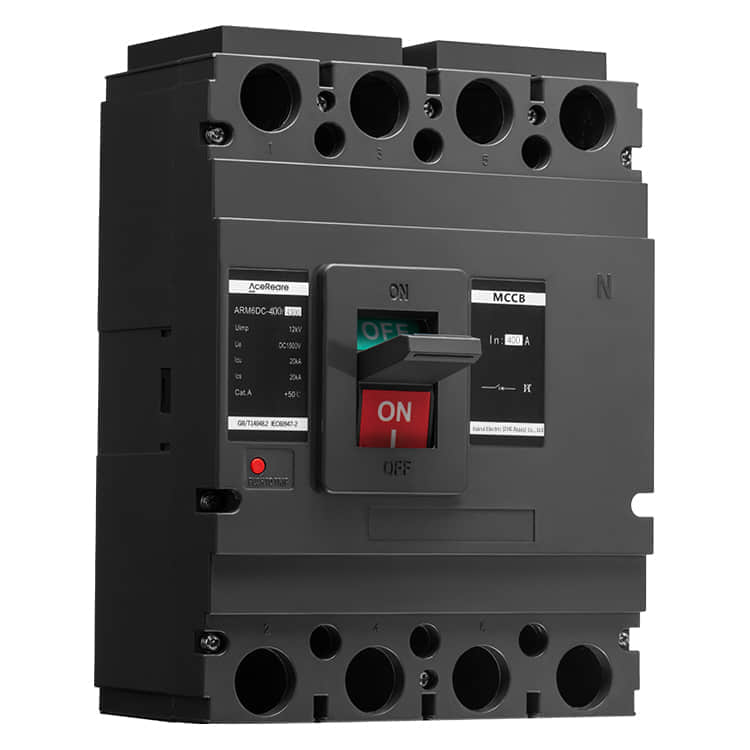