The industrial world is rapidly advancing, with new technologies and innovations emerging to improve operational efficiency and product quality. In this environment, regulating valves play a critical role in ensuring the precise control of fluid flow across a wide range of sectors, including manufacturing, energy, and chemical processing. Among these, the China Electric Single Seat Regulating Valve has gained significant attention due to its performance, reliability, and versatility. As a result, China has become a leading manufacturer of this essential valve, contributing significantly to global industries’ automation and process control systems.
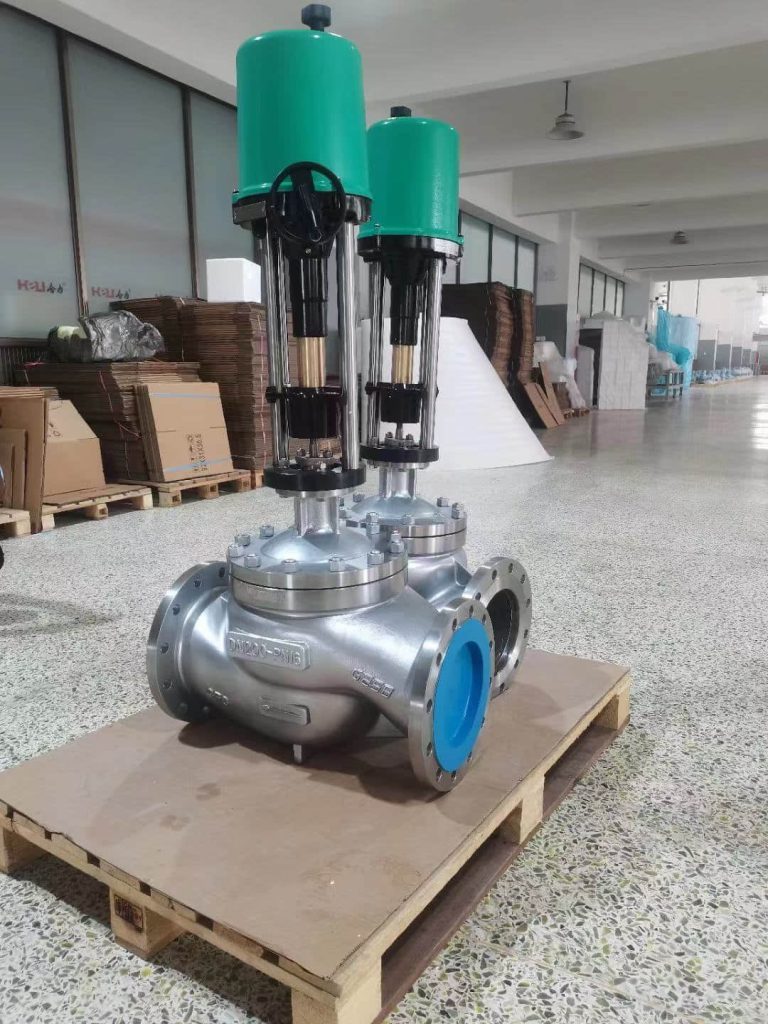
What is an Electric Single Seat Regulating Valve? An electric single seat regulating valve is a type of control valve commonly used to regulate the flow of fluids within a pipeline. It consists of a single valve seat, and its operation is driven by an electric actuator that adjusts the valve position based on feedback from sensors or control systems. The primary function of this valve is to maintain constant flow rates, pressure, or temperature within a system, making it ideal for applications requiring high precision and automated control. Electric single seat regulating valves are essential in a variety of industries, such as oil and gas, power generation, pharmaceuticals, water treatment, and food processing. Their accuracy, ease of automation, and ability to handle a wide range of fluids, from gases to liquids, make them indispensable in modern industrial processes.