Introduction
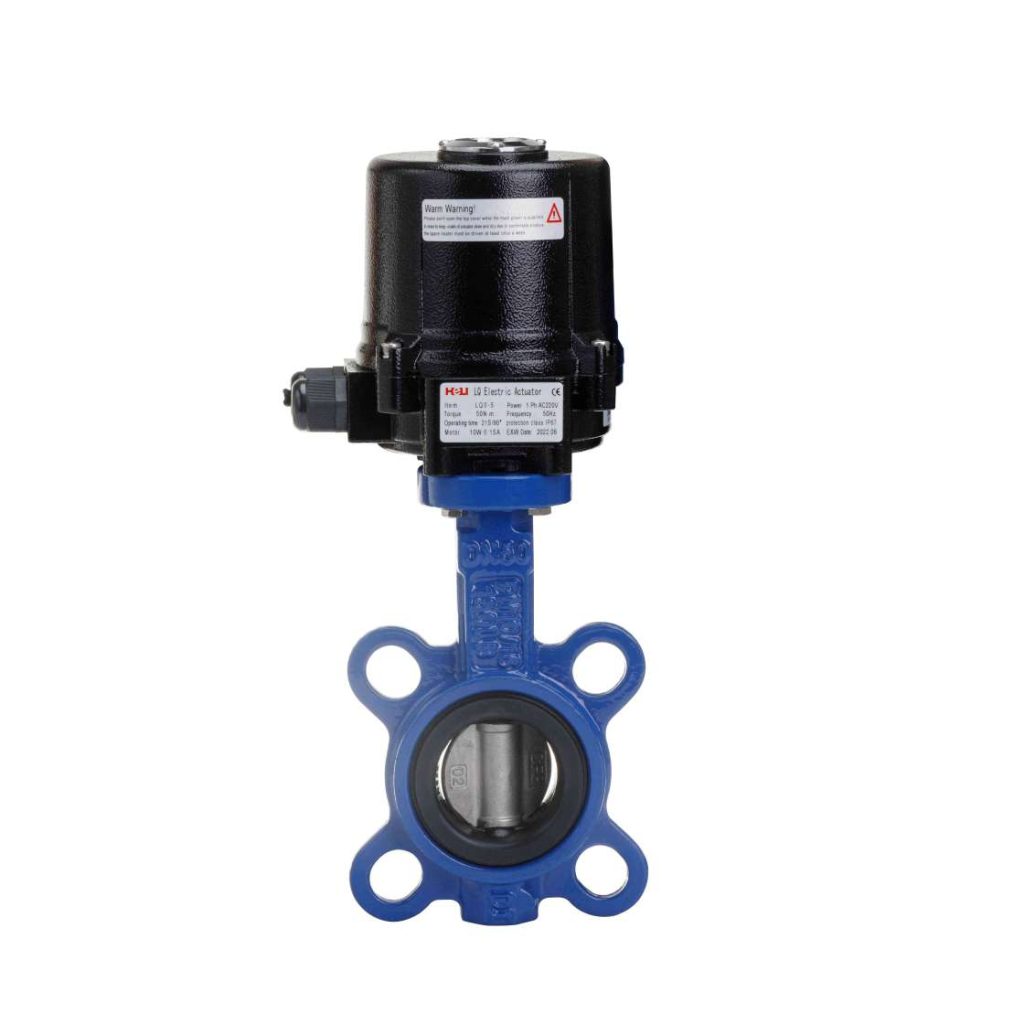
Stainless steel electric butterfly valves are essential components in various industries, providing reliable control over fluid flow in pipelines. These valves are characterized by their unique design, efficient operation, and durability, making them ideal for applications that require precision and reliability. This article will delve into the functionalities, advantages, applications, and maintenance of stainless steel electric butterfly valves.
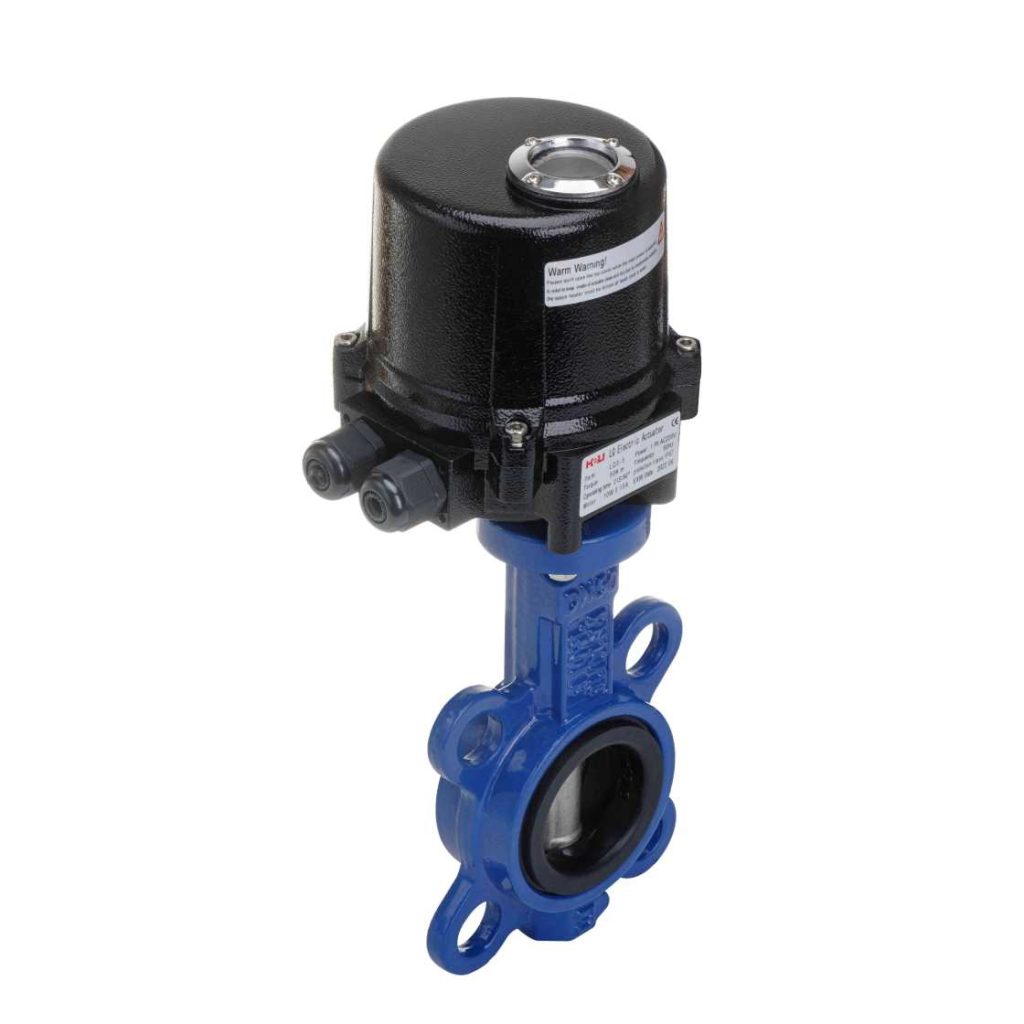
What is a Stainless Steel Electric Butterfly Valve? A stainless steel electric butterfly valve is a type of quarter-turn valve that uses a rotating disc to regulate flow. The valve consists of a stainless steel body, a disc (or plate), an electric actuator, and various seals. The actuator is responsible for opening and closing the valve, allowing for smooth and efficient fluid control. The stainless steel material ensures corrosion resistance and longevity, making it suitable for various environments, including those with high temperatures and pressures. Functionality and Operation The operation of stainless steel electric butterfly valves is straightforward. When the actuator is energized, it rotates the disc from a closed position (90 degrees) to an open position (0 degrees) or vice versa. This rotation allows fluid to flow freely through the pipeline when the valve is open. Conversely, when the valve is closed, the disc obstructs the flow, effectively controlling the amount of fluid passing through.
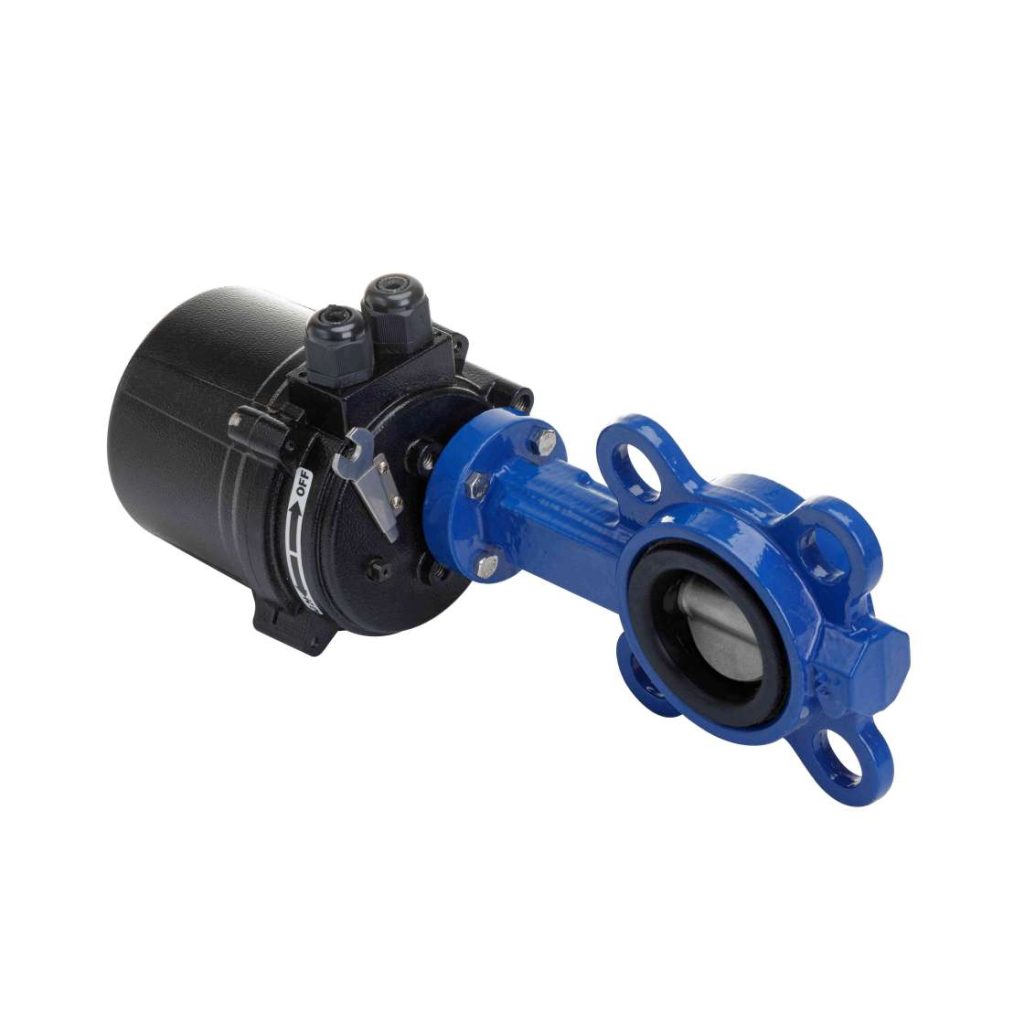