In recent years, the demand for more efficient, reliable, and sustainable automation solutions has been growing across various industries. One of the key innovations in this field is the lithium battery-powered electric actuator. These actuators play a pivotal role in enhancing the functionality and performance of automation systems, particularly in industries such as robotics, manufacturing, and automotive. Among the companies leading the charge in this technological revolution is HeLi Automation, a pioneering force in the development of cutting-edge automation solutions that utilize lithium battery-powered electric actuators to optimize productivity and energy efficiency.
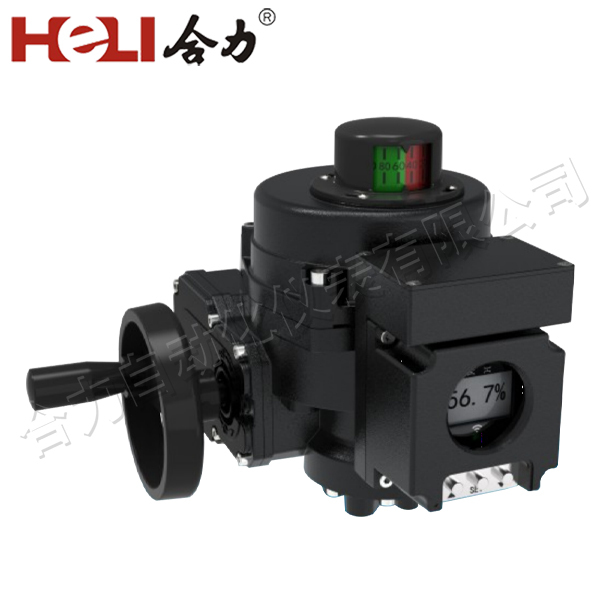
Lithium Battery Electric Actuators: An Overview
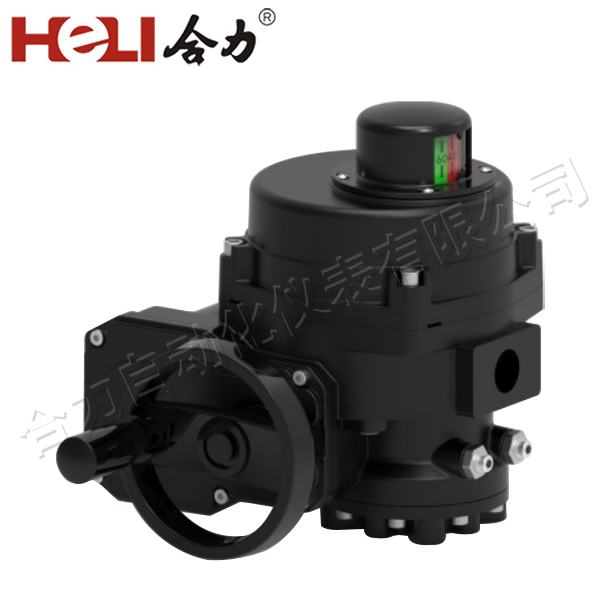
Electric actuators powered by lithium batteries are designed to provide high torque, precise control, and energy efficiency in automated systems. These actuators convert electrical energy into mechanical motion, allowing for precise movement in machines and systems. Unlike traditional pneumatic or hydraulic actuators, lithium battery-powered electric actuators offer several advantages, including reduced maintenance, quieter operation, and the ability to operate in environments where compressed air or hydraulic fluid might not be suitable. Lithium batteries, known for their lightweight and long-lasting performance, further enhance the capabilities of electric actuators. With their high energy density, these batteries provide extended operation times and can support demanding applications without the need for frequent recharging. This makes them ideal for use in systems where uptime and operational efficiency are critical.
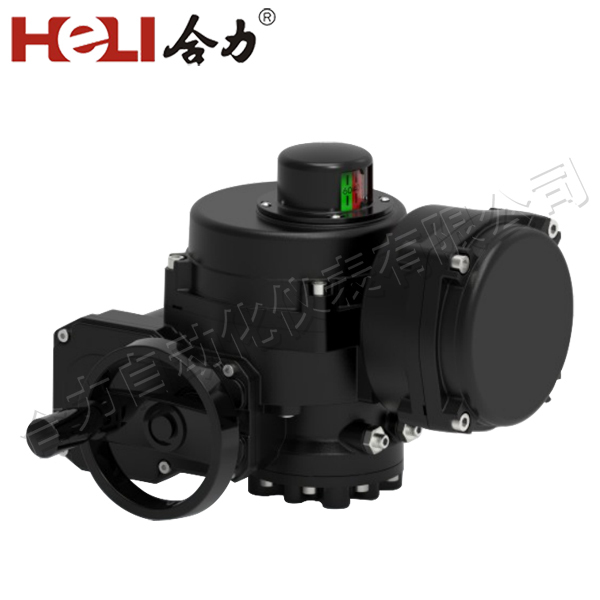