In modern agriculture, efficient water management is essential to ensure healthy crop growth while conserving valuable resources. With the increasing demand for high-performance irrigation systems, various technologies have been developed to optimize water flow and minimize wastage. Among these innovations, the WCB Electric Butterfly Valve for Agricultural Irrigation has gained popularity due to its reliability, durability, and ease of use. This article explores the advantages of using WCB Electric Butterfly Valves in agricultural irrigation systems and their role in improving irrigation efficiency.
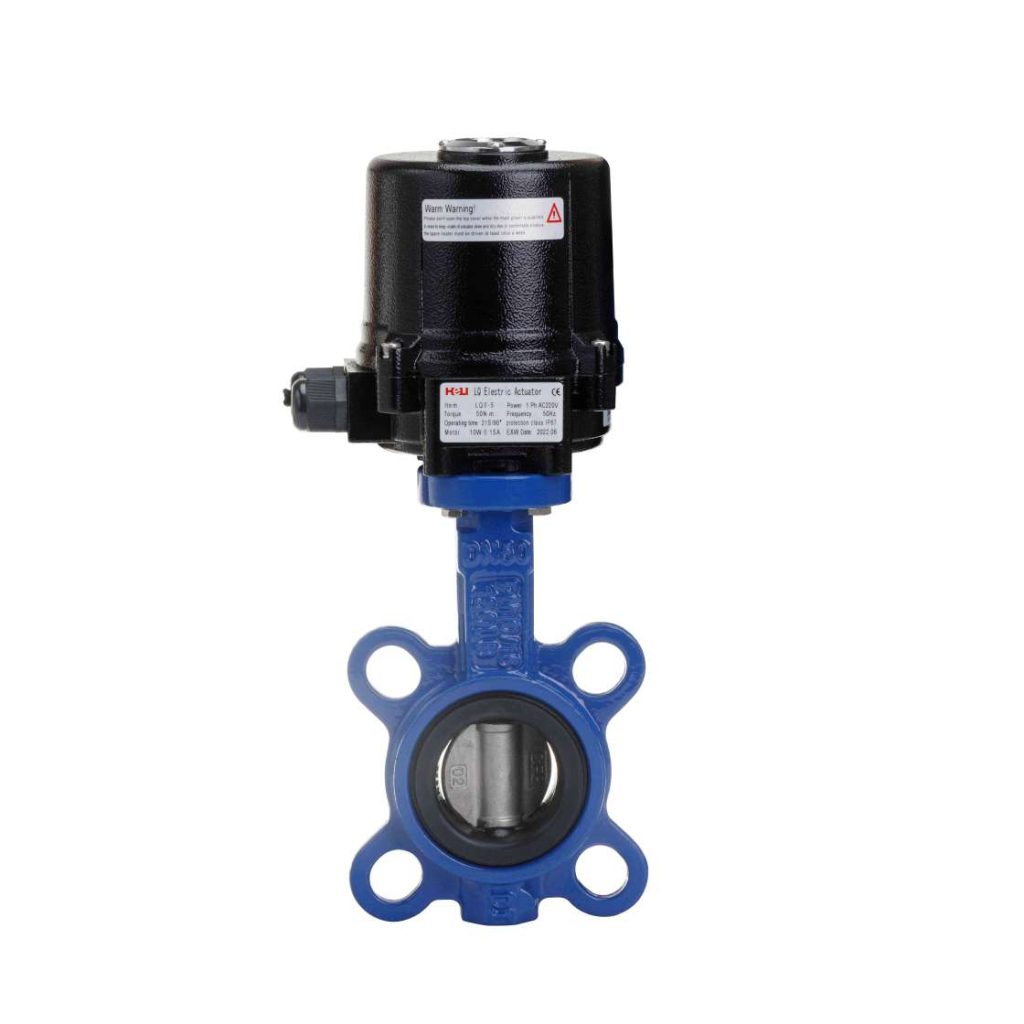
Understanding the WCB Electric Butterfly Valve
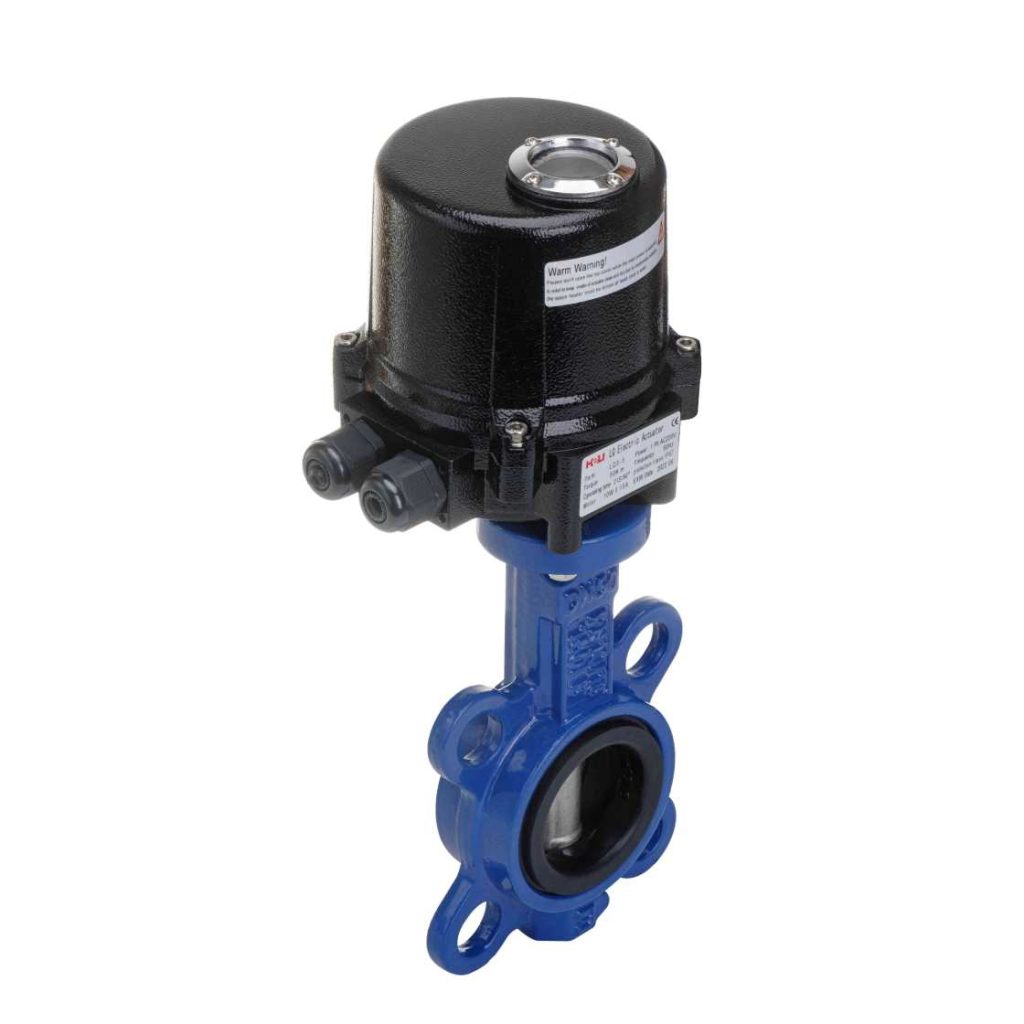
The WCB Electric Butterfly Valve is a type of valve designed to regulate water flow in irrigation systems. The valve consists of a rotating disc (or “butterfly”) that is mounted on a shaft. When the valve is activated, the disc rotates to open or close the flow path, effectively controlling the volume of water passing through the system. The “electric” component refers to the valve’s automated operation, which is controlled by an electric actuator. This actuator allows the valve to be adjusted remotely, without the need for manual intervention, offering significant advantages in terms of convenience and precision.
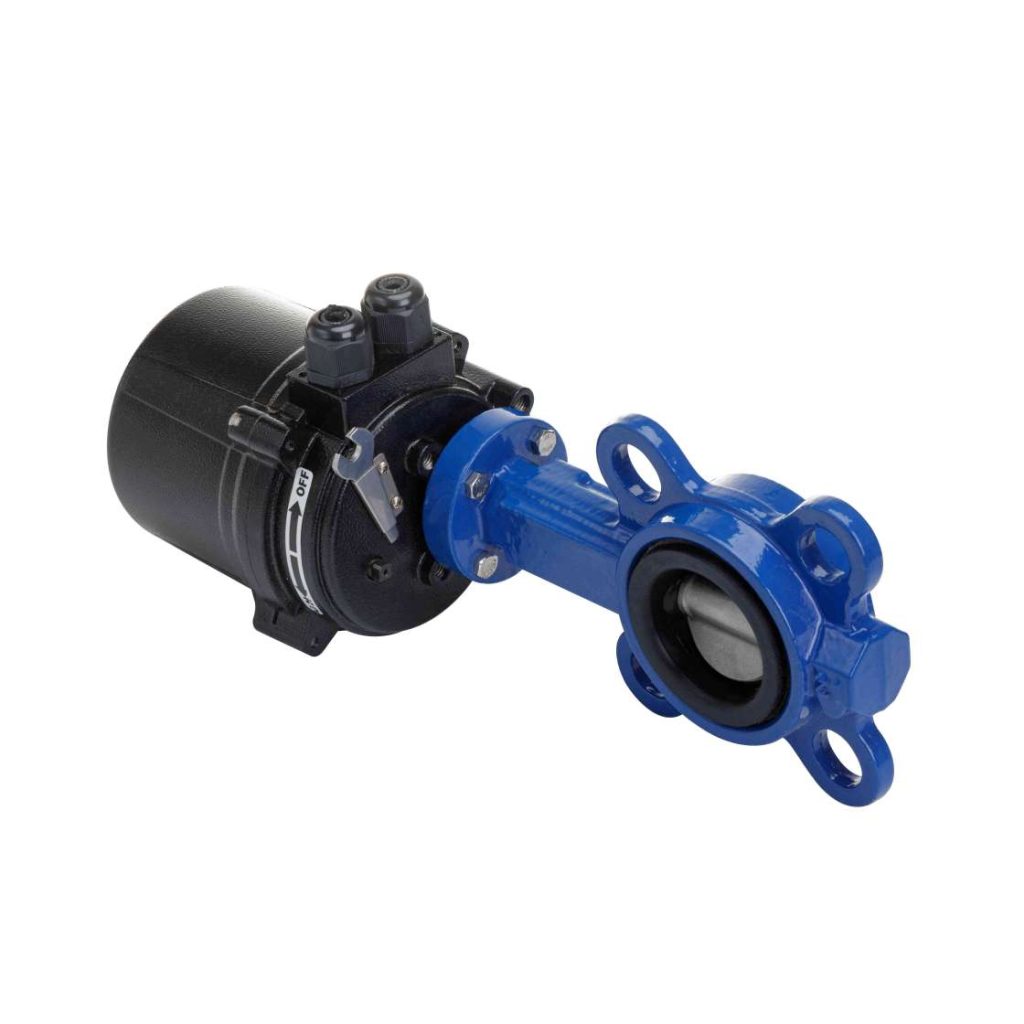