In recent years, the demand for advanced automation solutions has surged across various industries, leading to significant growth in the market for electric actuators. Among these solutions, intelligent control wireless electric actuators have gained particular attention for their versatility, efficiency, and ease of integration into existing systems. China, as a global manufacturing powerhouse, has established itself as a leading manufacturer of these innovative devices, catering to diverse sectors such as manufacturing, oil and gas, renewable energy, and smart buildings.
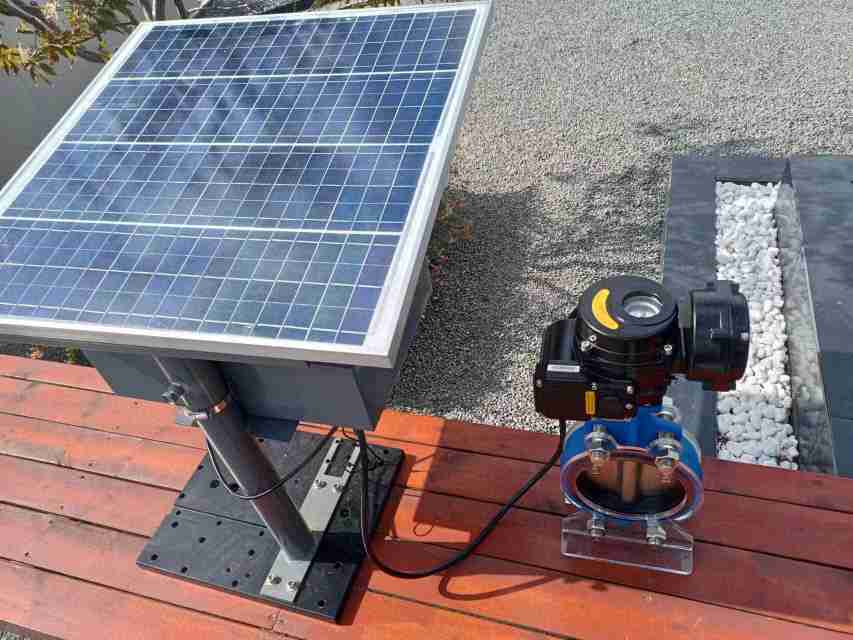
Overview of Wireless Electric Actuators
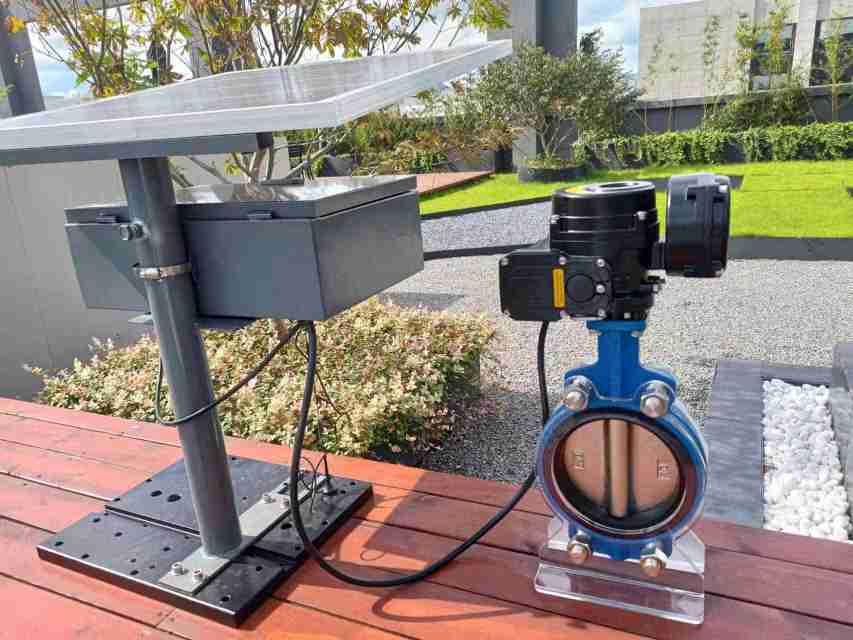
Wireless electric actuators are devices that convert electrical energy into mechanical motion, enabling automated control of valves, dampers, and other equipment without the need for cumbersome wired connections. These actuators utilize advanced technologies, including microcontrollers, wireless communication, and sensors, to deliver precise control and monitoring capabilities. The intelligent control aspect refers to the incorporation of algorithms and artificial intelligence, allowing these actuators to learn from their operating environments and optimize their performance accordingly. Key Features of Intelligent Control Wireless Electric Actuators
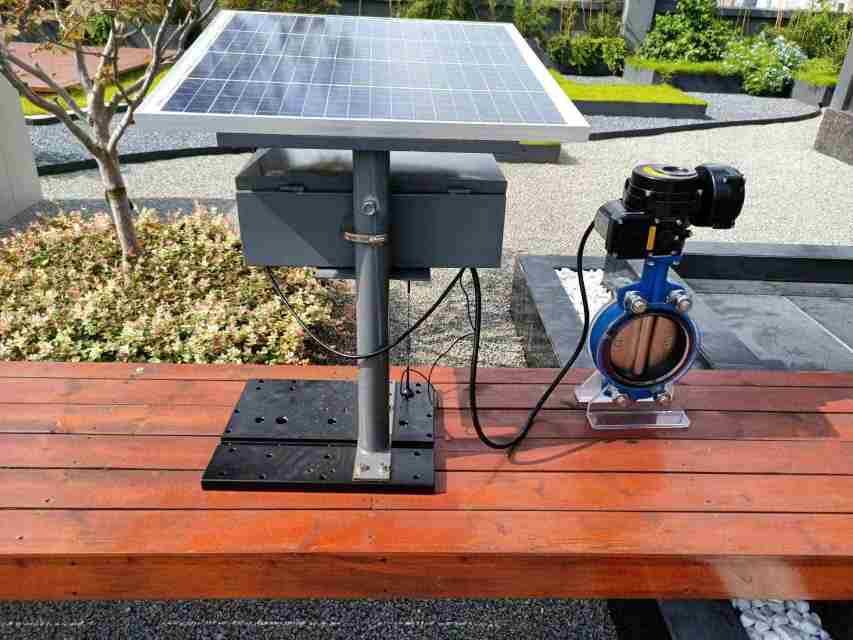