In recent years, the global energy landscape has shifted dramatically towards renewable sources, and among these, solar energy has emerged as a leading contender. This transition not only emphasizes the importance of harnessing solar power but also highlights the critical role of advanced technologies in optimizing its utilization. One such technology is the intelligent control solar electric actuator, a key component in modern solar energy systems. In this context, China has positioned itself as a prominent manufacturer of these innovative devices, offering solutions that enhance efficiency and reliability in solar energy applications.
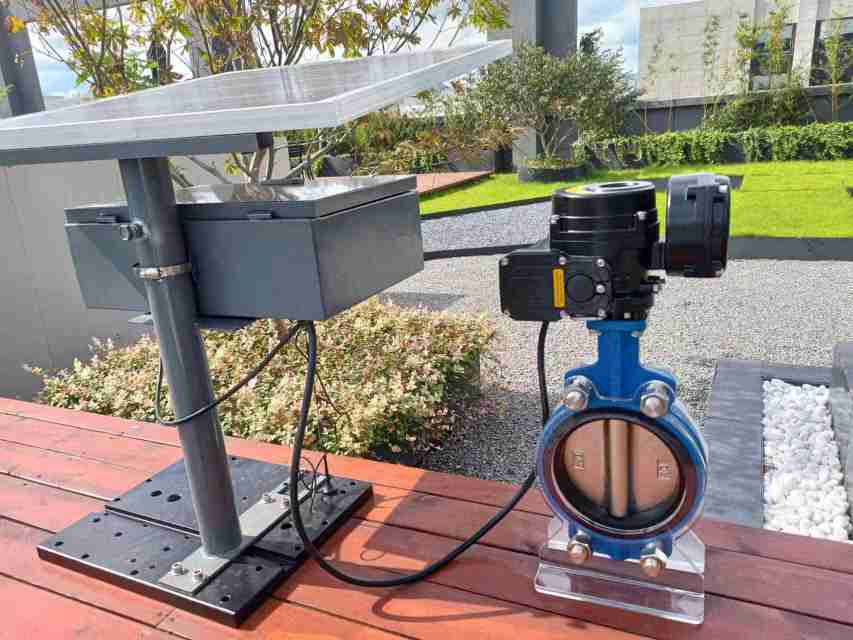
Understanding Solar Electric Actuators
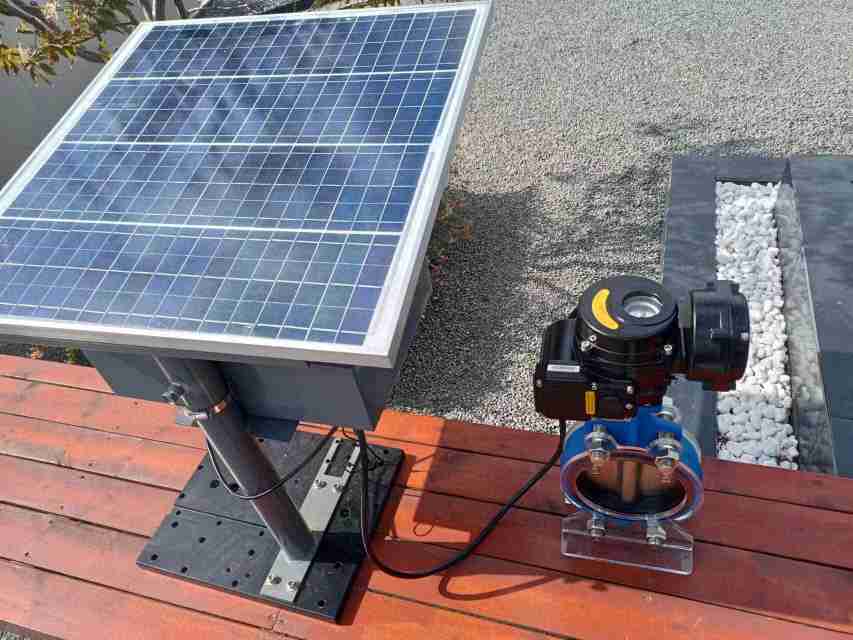
Solar electric actuators are devices that convert electrical energy into mechanical motion. They play a pivotal role in solar tracking systems, which adjust the orientation of solar panels to maximize their exposure to sunlight throughout the day. By utilizing actuators, solar installations can significantly increase energy capture, leading to higher efficiency and greater returns on investment. The intelligent control aspect of these actuators refers to their ability to adapt and respond to changing environmental conditions. Equipped with sensors and advanced control algorithms, these actuators can automatically adjust the position of solar panels in real-time, ensuring optimal performance under varying weather conditions. This smart functionality is essential for maximizing energy output and extending the lifespan of solar systems.
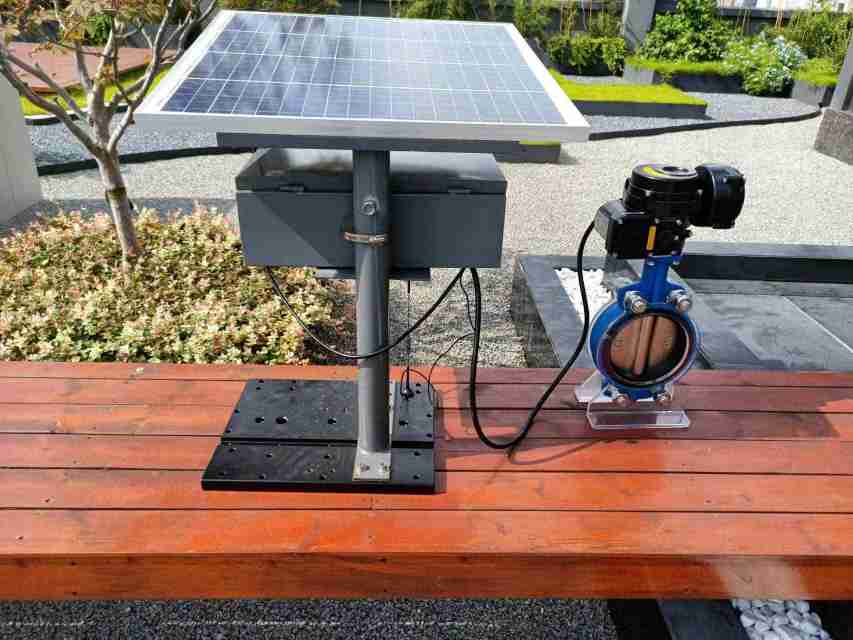