In modern industrial applications, precision, control, and efficiency are key to optimizing processes and reducing costs. One component that plays a pivotal role in achieving these goals is the valve. Among the many types of valves available, the Electric V-Ball Valve stands out for its innovative design and ability to provide precise control over flow in various systems. This article explores the features, benefits, and applications of the Electric V-Ball Valve, showcasing why it is becoming an essential part of many industries.
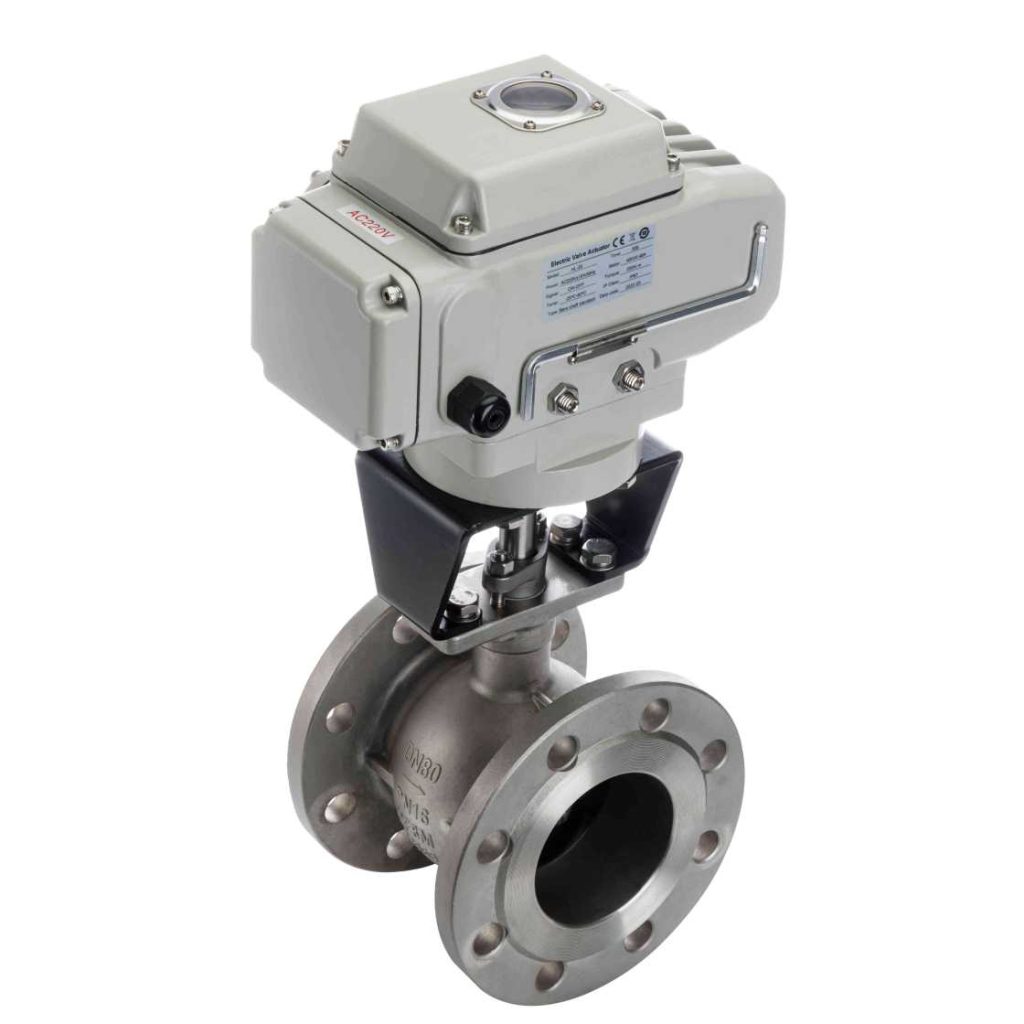
What is an Electric V-Ball Valve?
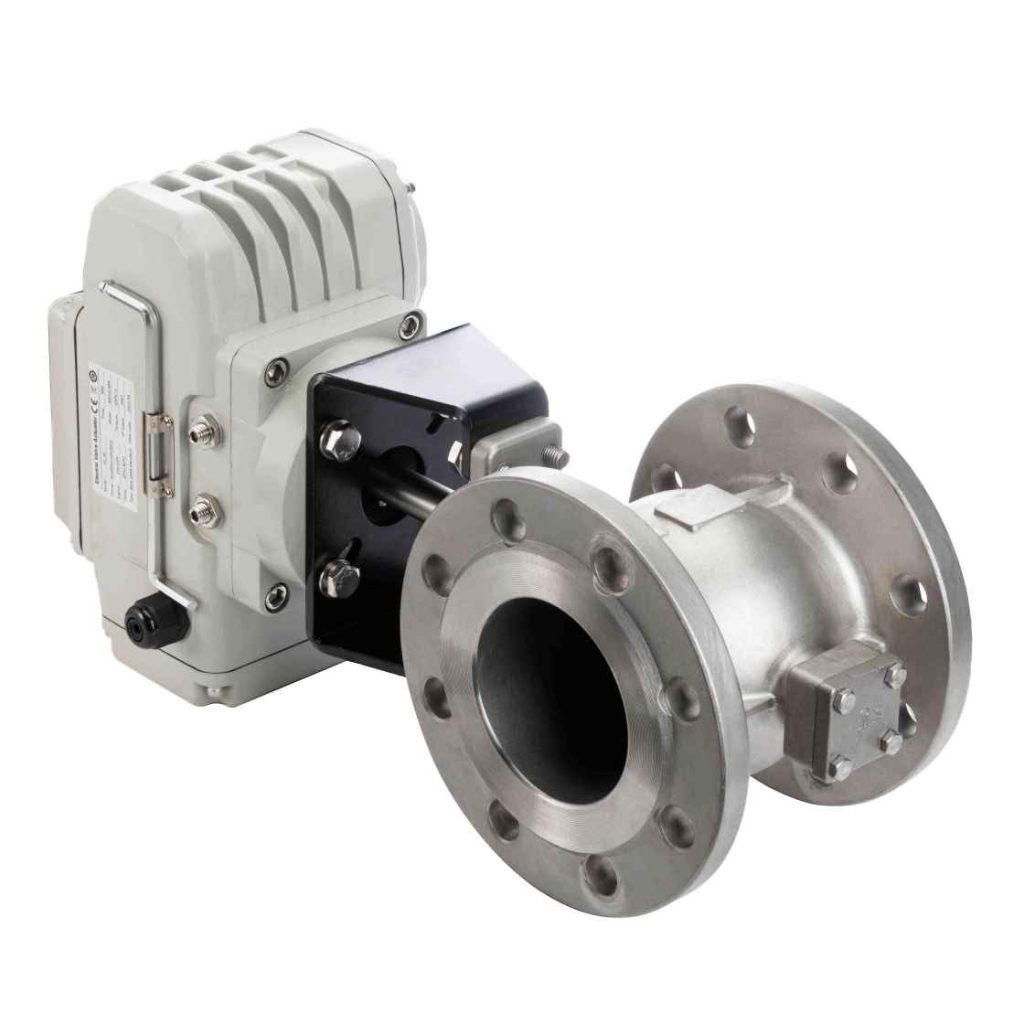
An Electric V-Ball Valve is a type of ball valve that combines the functionality of a traditional ball valve with the precision of electric actuation. The “V” in the name refers to the V-shaped notch or port within the valve ball, which is designed to create a controlled flow profile. This design allows for better throttling capability compared to conventional ball valves, which typically offer either full open or full closed positions without the same level of flow control. Electric V-Ball Valves are equipped with electric actuators, which provide automated control over the valve’s opening and closing. The electric actuator can be controlled remotely, allowing for easy integration into automated control systems, such as SCADA (Supervisory Control and Data Acquisition) or DCS (Distributed Control Systems). This feature is especially beneficial for industries that require constant monitoring and adjustment of flow rates.
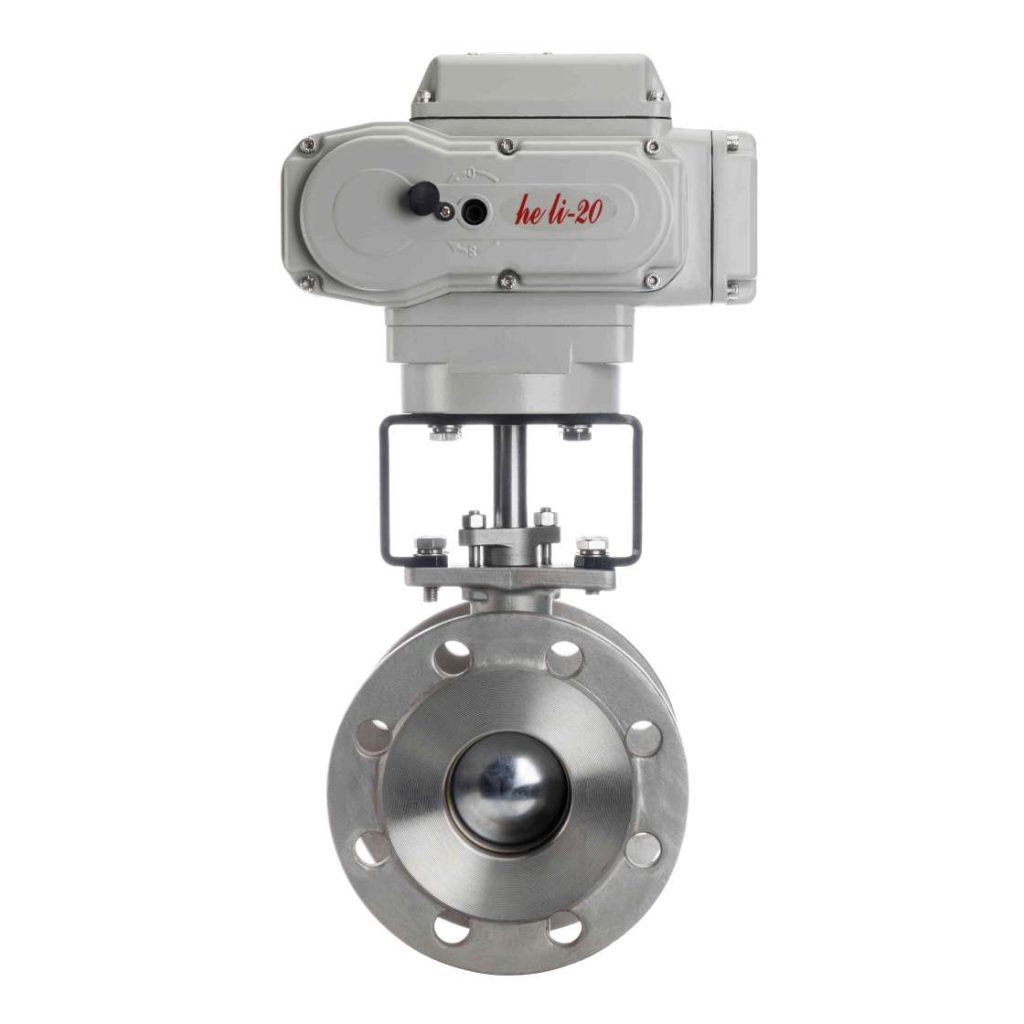