In today’s industrial world, the need for precise and efficient fluid control is essential for the smooth operation of a variety of systems, from oil and gas pipelines to manufacturing plants and chemical processes. One of the critical components in achieving optimal control is the pneumatic ball valve, a device that has become indispensable in many industries. The role of a pneumatic ball valve manufacturer is to provide high-quality, durable, and reliable products that meet the stringent demands of fluid handling systems. This article delves into the significance of pneumatic ball valves, the manufacturing process, and the qualities that set a good manufacturer apart from the rest.
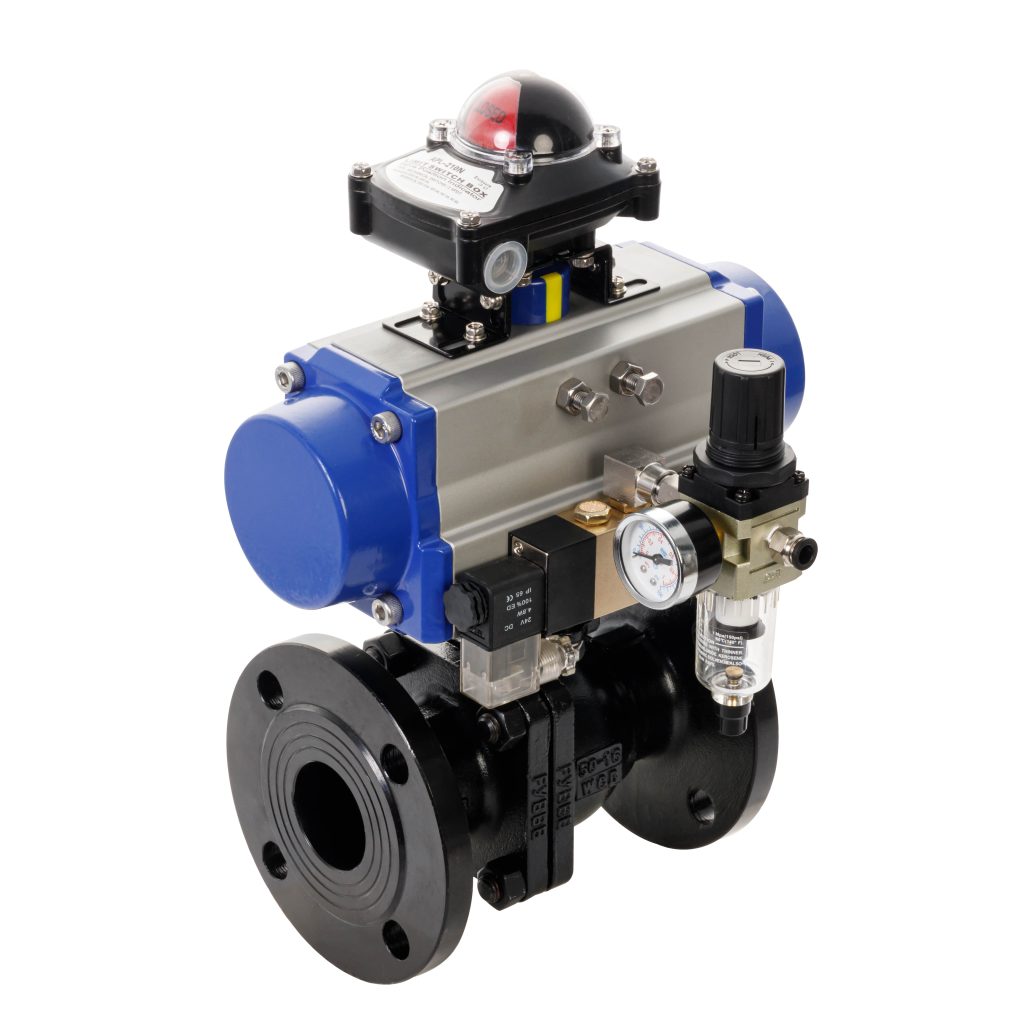
What is a Pneumatic Ball Valve?
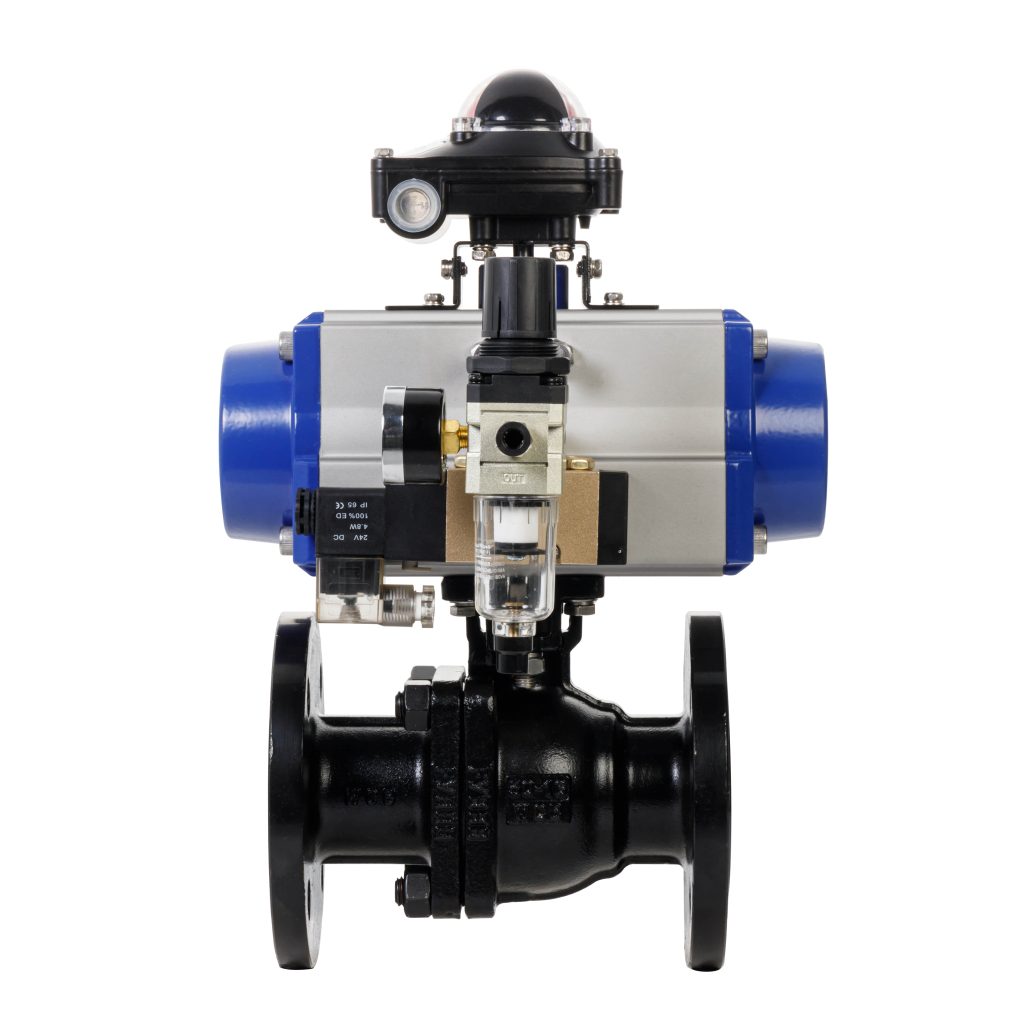
A pneumatic ball valve is a type of valve that utilizes compressed air to control the movement of the valve’s ball, which in turn regulates the flow of fluids through a pipeline. These valves are designed to provide quick, reliable, and tight shut-off, making them ideal for applications where leakage must be minimized or avoided entirely. Pneumatic ball valves typically consist of a hollow ball with a hole through its center. When the valve is open, the hole aligns with the pipe’s flow, allowing fluids to pass. When closed, the ball rotates to block the flow, ensuring complete sealing. What makes pneumatic ball valves particularly advantageous is their ability to operate with minimal human intervention. Their actuator, powered by compressed air, allows for remote or automated control, making them an integral part of automated fluid control systems.
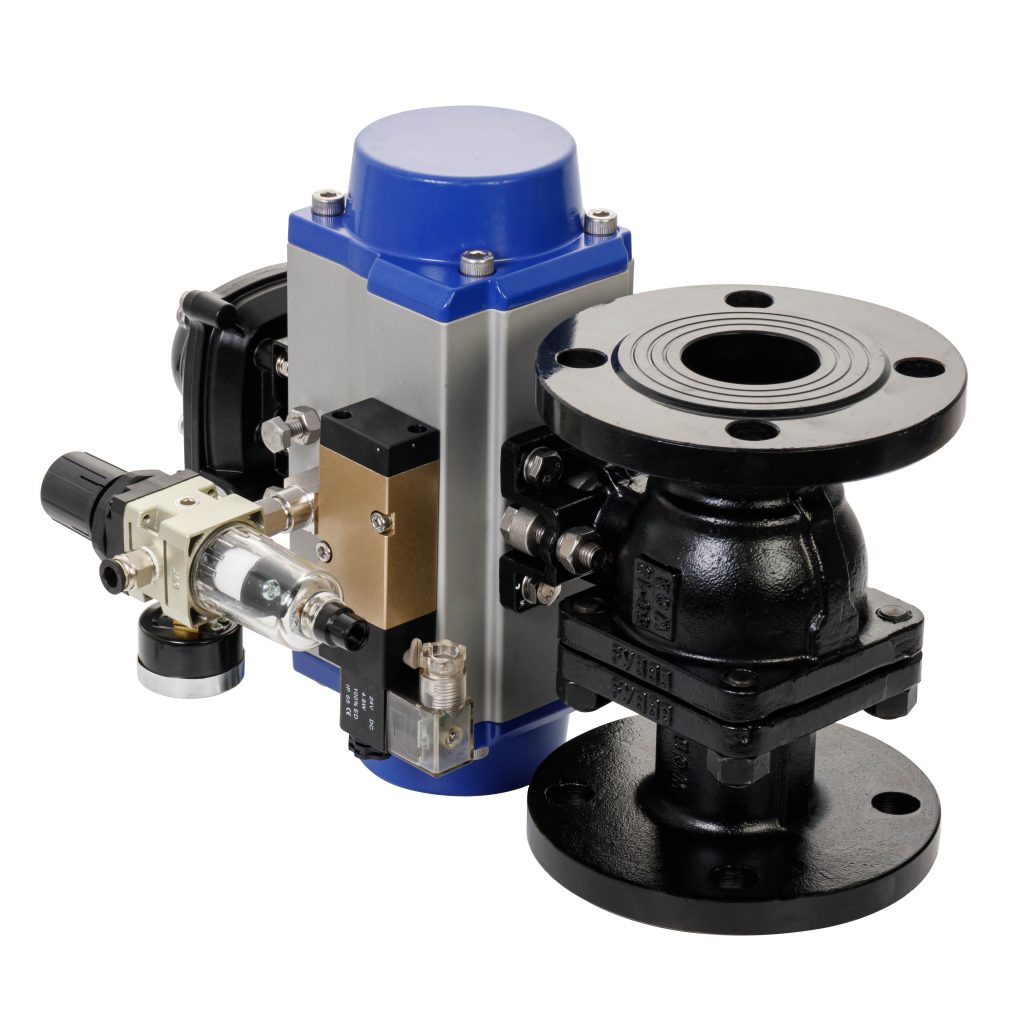