In the rapidly evolving field of automation, the demand for precision, efficiency, and adaptability in systems has reached new heights. One key component driving this transformation is the Intelligent Integrated Actuator (IIA). As industries push toward smarter, more flexible operations, IIAs have emerged as vital enablers of innovation, offering enhanced control and improved performance in a variety of applications. These advanced actuators are integral to applications in robotics, aerospace, automotive, manufacturing, and more, offering unprecedented levels of integration and intelligence.
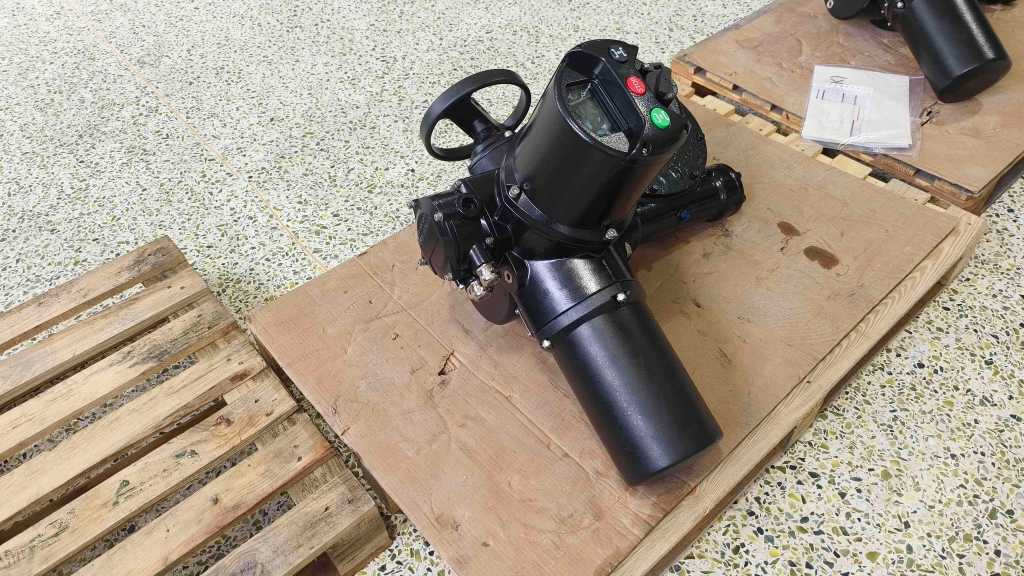
Understanding Intelligent Integrated Actuators
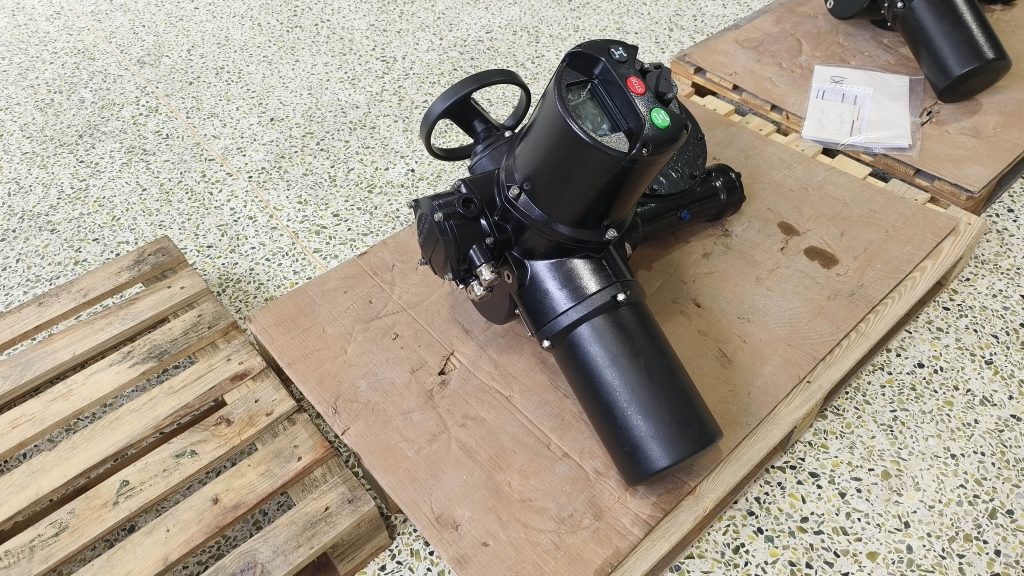
An Intelligent Integrated Actuator is an advanced actuator that combines traditional mechanical actuation elements with embedded sensors, control algorithms, and communication capabilities in a single, compact unit. Unlike conventional actuators, which often require separate components for control and feedback, IIAs offer a high degree of integration by incorporating intelligence directly within the actuator. This makes them more efficient, reducing the need for external controllers or complex wiring systems.
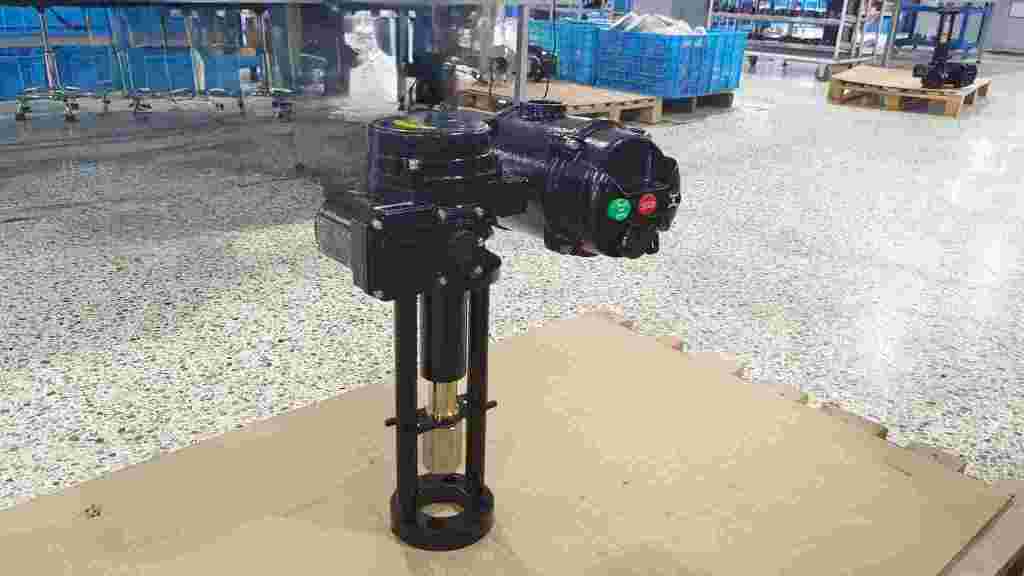
The core function of an actuator is to convert energy (typically electrical, hydraulic, or pneumatic) into mechanical motion. IIAs take this basic function a step further by embedding processing power and sensors that enable real-time monitoring and decision-making. The result is a system that can respond to its environment, adapt to changing conditions, and provide enhanced performance and accuracy.
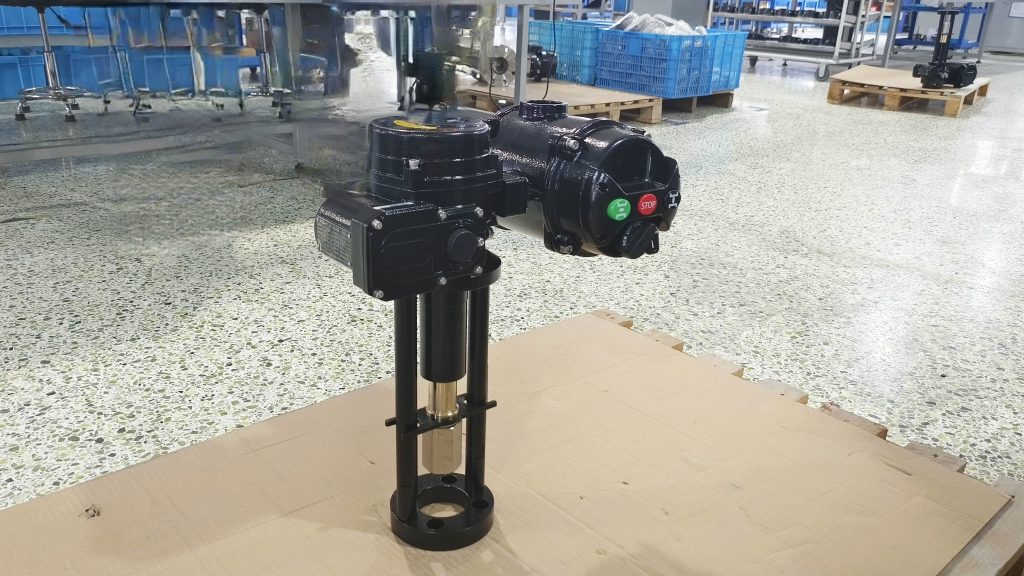
Key Features of Intelligent Integrated Actuators
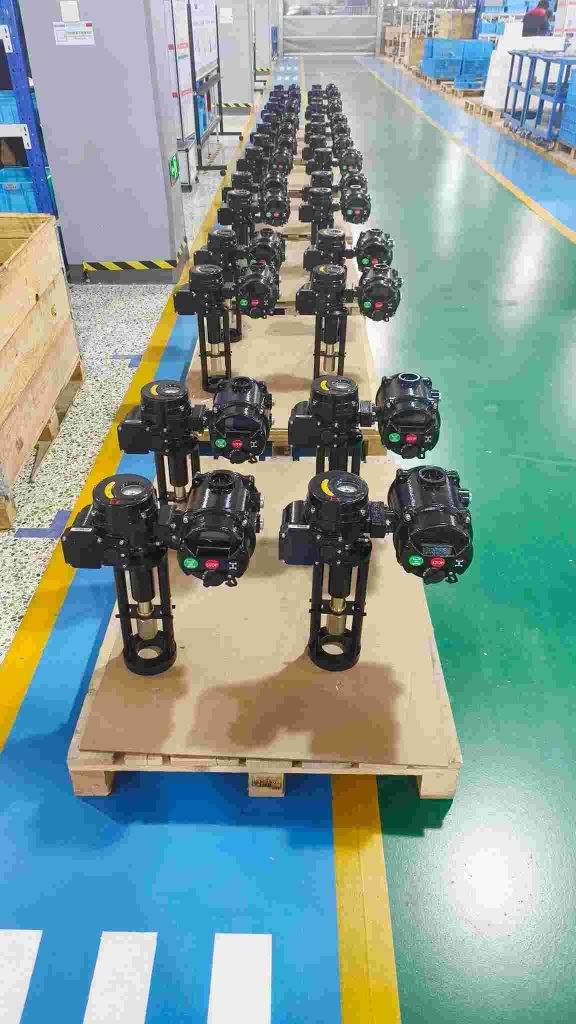
Embedded Intelligence: At the heart of an IIA is its ability to process data locally. Integrated microcontrollers or processors allow the actuator to execute complex tasks without relying on external systems. This not only improves speed and response times but also makes the actuator more independent, reducing the need for constant communication with a central control unit. Sensor Integration: IIAs are equipped with sensors that monitor parameters such as position, temperature, force, and speed. These sensors provide valuable feedback, allowing the actuator to adjust its behavior in real-time for optimal performance. For example, if the actuator senses a deviation in position or force, it can adjust its movement to correct the issue, ensuring precision. Self-diagnostics and Monitoring: Intelligent actuators often have built-in diagnostic capabilities. These systems can detect potential faults or performance degradation, enabling predictive maintenance and minimizing downtime. The actuator can alert operators to issues before they become critical, ensuring continuous operation and reducing the risk of unexpected failures.
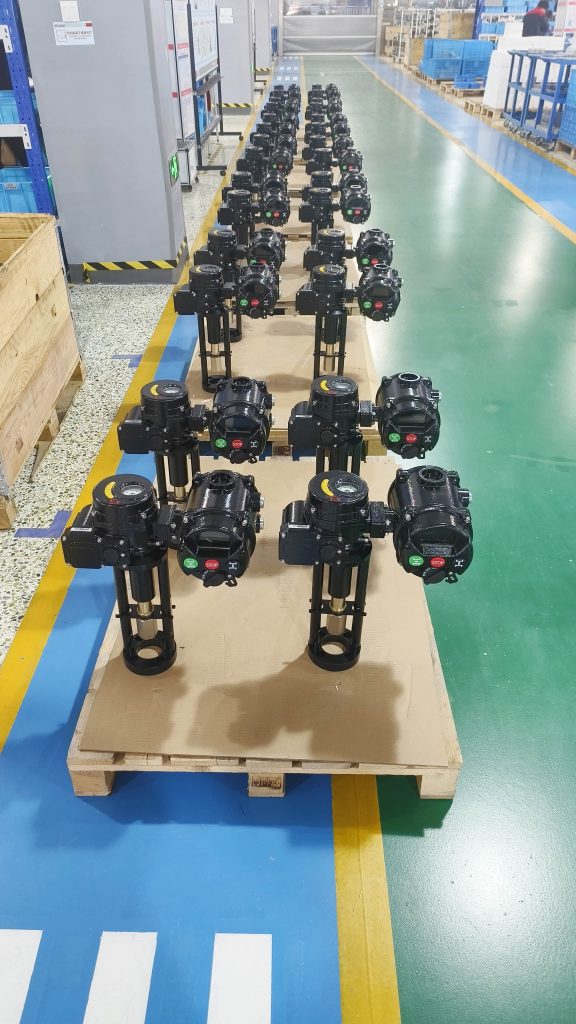