In industries where flammable gases, vapors, or liquids are present, the need for safety and reliability becomes paramount. One critical component that plays a significant role in ensuring safety in such environments is the explosion-proof electric valve. These specialized valves are designed to prevent the ignition of explosive atmospheres, thereby protecting both personnel and equipment from potential hazards.
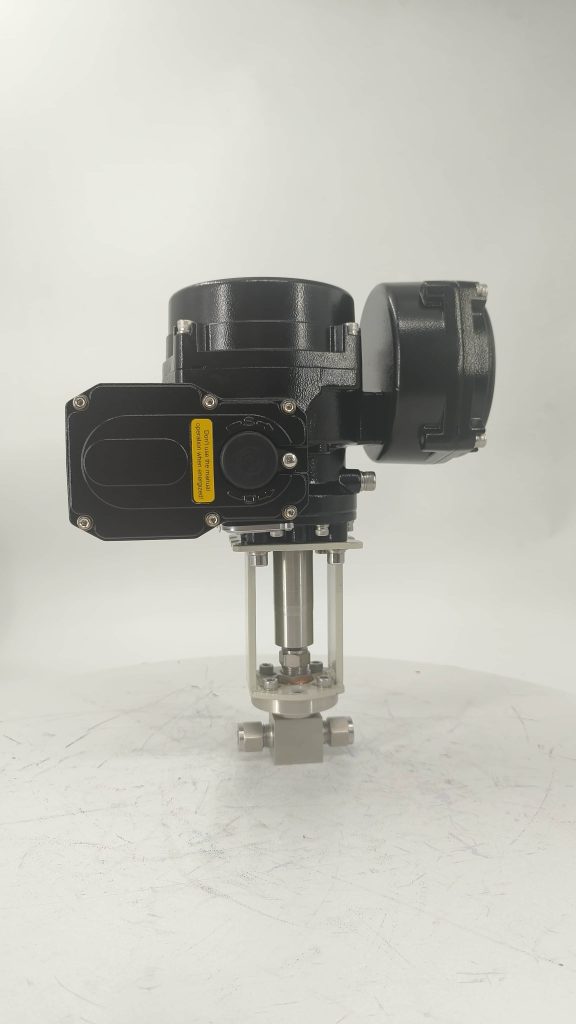
What is an Explosion-Proof Electric Valve?
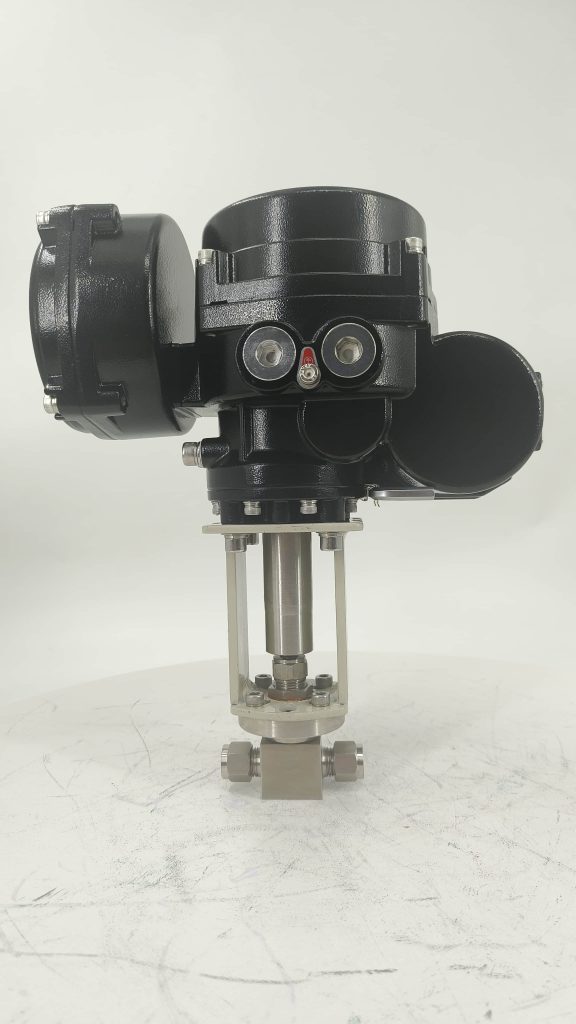
An explosion-proof electric valve is a type of valve equipped with an electric actuator that can operate safely in hazardous locations. The term “explosion-proof” refers to the valve’s ability to contain any explosion within its housing, preventing it from spreading to the surrounding atmosphere. These valves are commonly used in industries such as oil and gas, chemicals, pharmaceuticals, and wastewater treatment, where the risk of explosion due to the presence of combustible materials is significant. Key Features of Explosion-Proof Electric Valves Robust Construction: Explosion-proof electric valves are typically made from high-strength materials that can withstand extreme pressure and temperature variations. This durability is crucial in environments where mechanical failure could lead to catastrophic incidents.
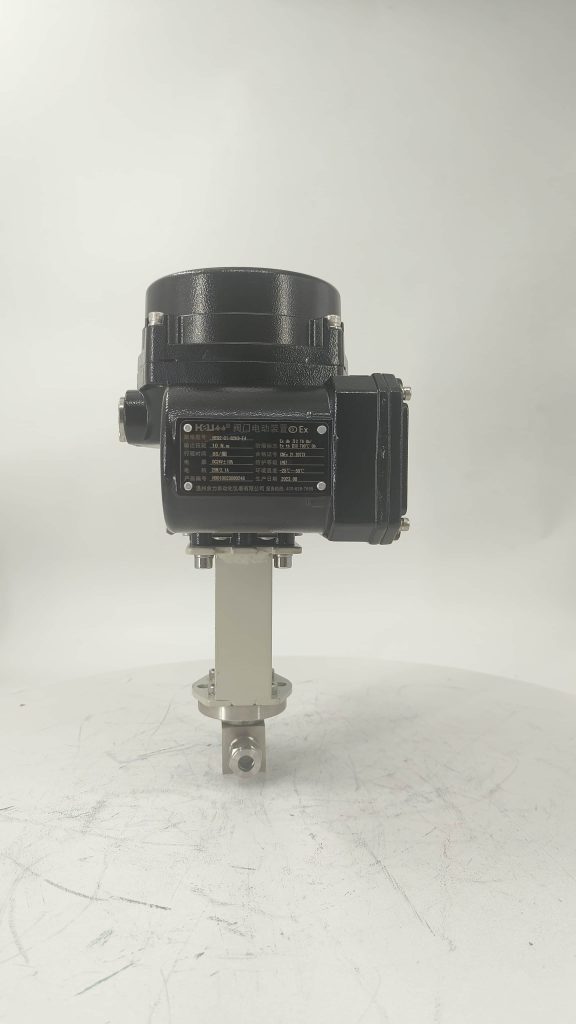