In today’s fast-paced manufacturing industry, precision and efficiency are paramount. Manufacturers constantly seek innovative solutions to create products that meet high-quality standards while optimizing production costs. One method that has revolutionized the production of intricate components is injection molding. This process allows for the mass production of complex parts with unparalleled accuracy and speed. In this article, we delve into the fascinating world of injection molded parts, exploring their manufacturing process, applications, advantages, and future prospects.
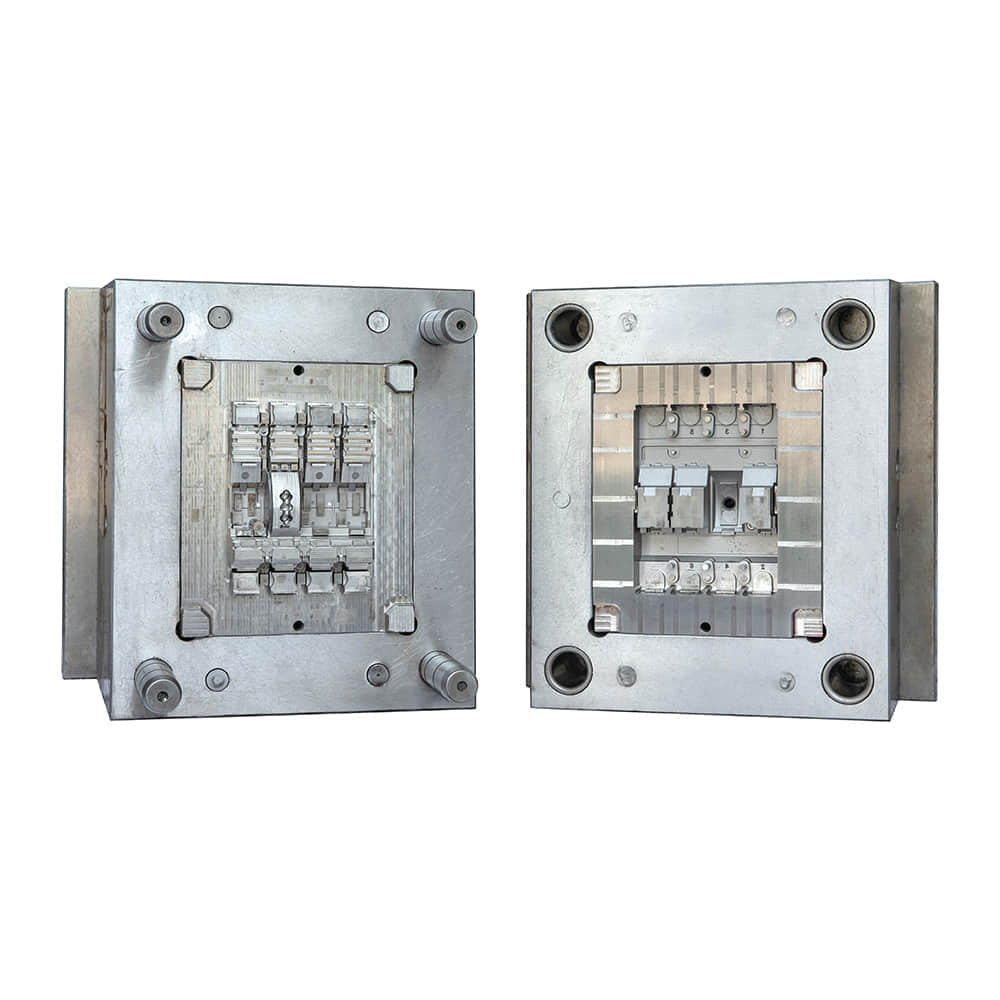
The Injection Molding Process
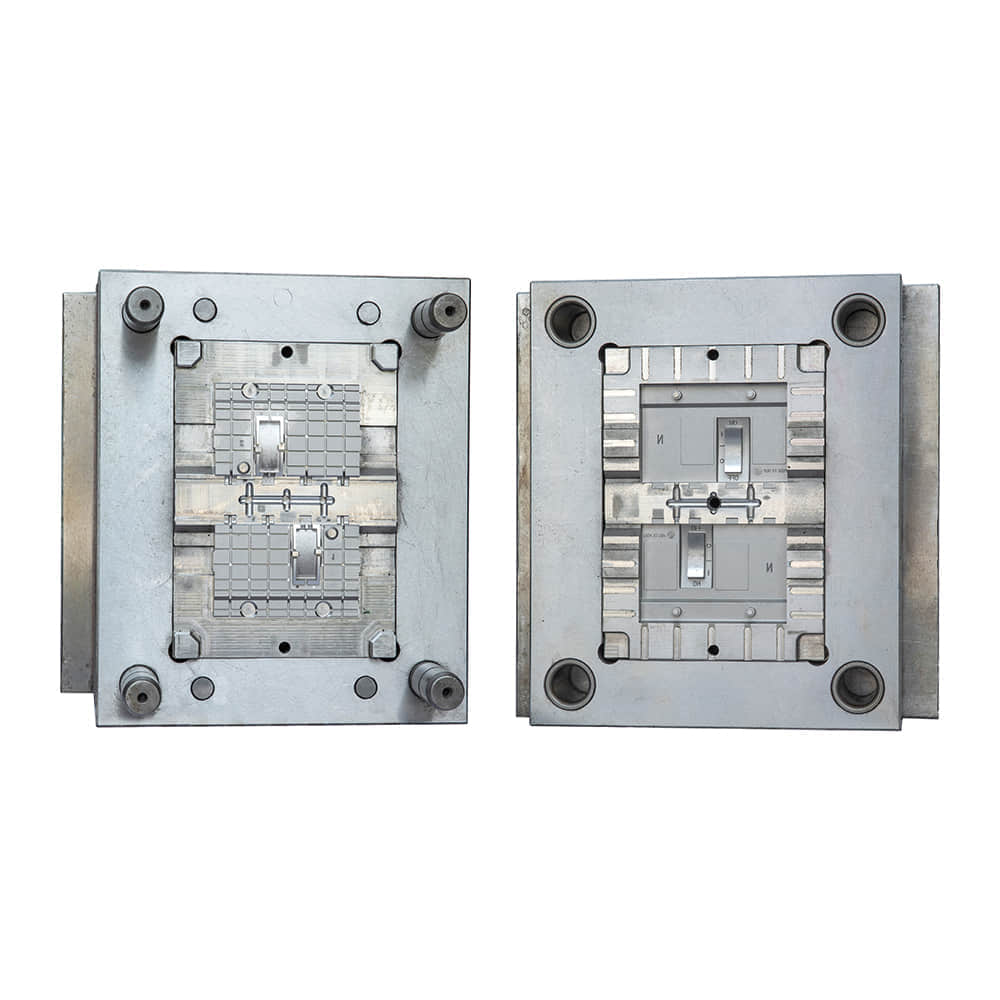
Injection molding is a manufacturing technique that involves injecting molten material into a mold cavity, where it cools and solidifies, forming the desired part. The process consists of several key stages: Material Selection:Injection molding can accommodate a wide range of materials, including plastics, metals, ceramics, and more. The choice of material depends on the specific requirements of the part. Mold Design:A precision-crafted mold, typically made of steel or aluminum, is created to shape the final product. Mold design is critical for achieving the desired part geometry. Injection:The selected material is melted and injected into the mold cavity at high pressure. This ensures that the material fills every crevice of the mold, producing a detailed and accurate part. Cooling and Solidification:The molten material cools and solidifies within the mold. Cooling time is carefully controlled to prevent defects and ensure uniformity. Ejection:Once the material has solidified, the mold opens, and the finished part is ejected. The cycle then repeats for continuous production. Applications of Injection Molded Parts Injection molded parts are ubiquitous in various industries, thanks to their versatility and precision. Some common applications include: Automotive:Components such as dashboards, bumpers, and interior trim are often produced through injection molding. Electronics:Plastic casings for electronic devices, connectors, and insulating components are manufactured using this process. Medical:Medical devices and equipment, including syringes, IV connectors, and surgical instruments, rely on injection molded parts for their precision and cleanliness. Consumer Goods:Toys, packaging, containers, and household appliances frequently feature injection molded components. Aerospace:Lightweight and durable parts for aircraft and spacecraft are made using advanced injection molding techniques. Advantages of Injection Molding Injection molding offers numerous advantages over other manufacturing methods: Precision:Injection molding can produce highly intricate and detailed parts with tight tolerances. Cost-Effective:Once the mold is created, production costs per part decrease significantly for large quantities. High Production Speed:The cycle time for injection molding is relatively short, leading to faster production rates. Minimal Material Waste:The process generates minimal material waste compared to other manufacturing methods. Material Variety:The ability to use various materials allows for a wide range of applications. The Future of Injection Molded Parts As technology continues to advance, the future of injection molded parts looks promising. Some trends to watch out for include: Sustainability:The industry is moving towards eco-friendly materials and processes to reduce environmental impact. 3D Printing Integration:Combining injection molding with 3D printing techniques can offer unique design possibilities. Smart Manufacturing:The adoption of IoT and data analytics in injection molding will enhance quality control and process optimization. Nanotechnology:The incorporation of nanomaterials will enable the development of stronger and more durable parts. In conclusion, injection molded parts play a crucial role in modern manufacturing. Their precision, efficiency, and versatility make them indispensable in a wide range of industries. As technology continues to evolve, we can expect even more innovative applications and sustainable practices in the world of injection molding.
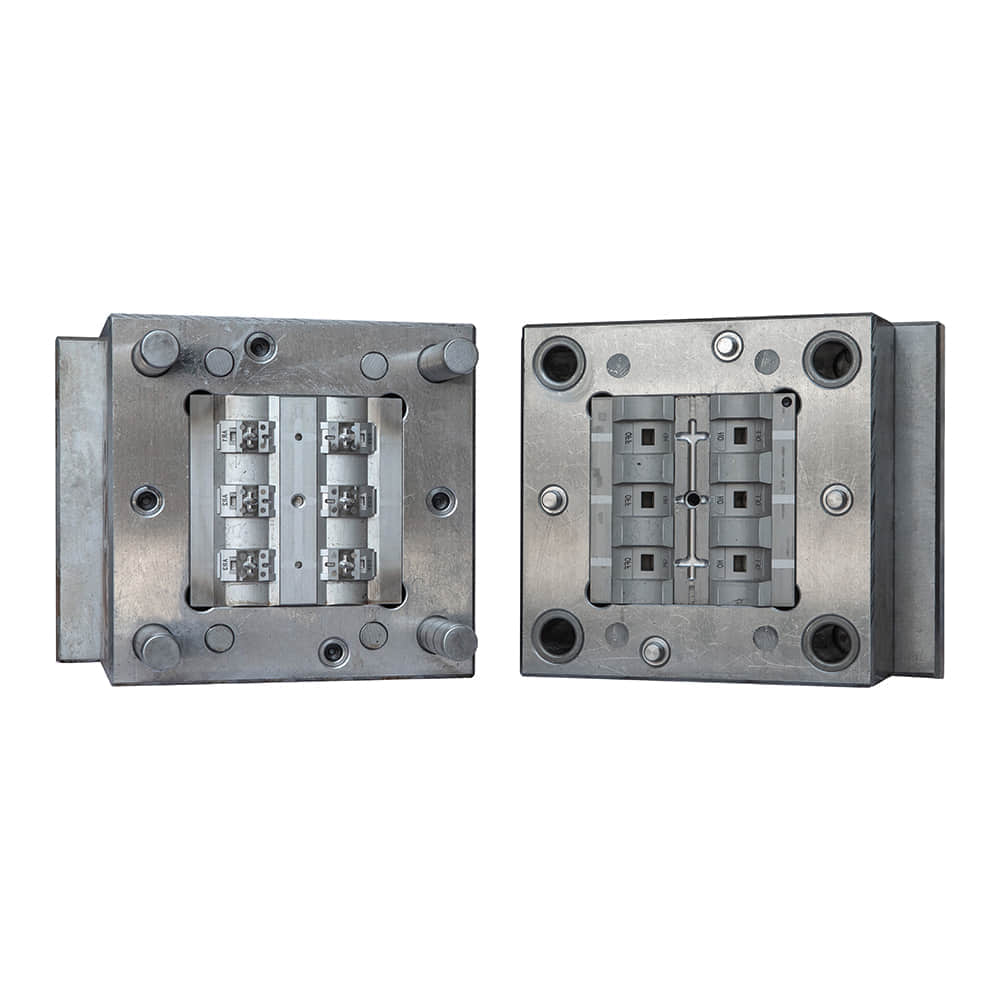