In the realm of modern manufacturing, injection molded parts have emerged as a cornerstone of precision and efficiency. This innovative process has revolutionized the way we create complex and intricate components for a vast array of industries, from automotive to electronics and beyond. In this article, we will delve into the world of injection molded parts, exploring their production, applications, and the numerous advantages they bring to the manufacturing table.
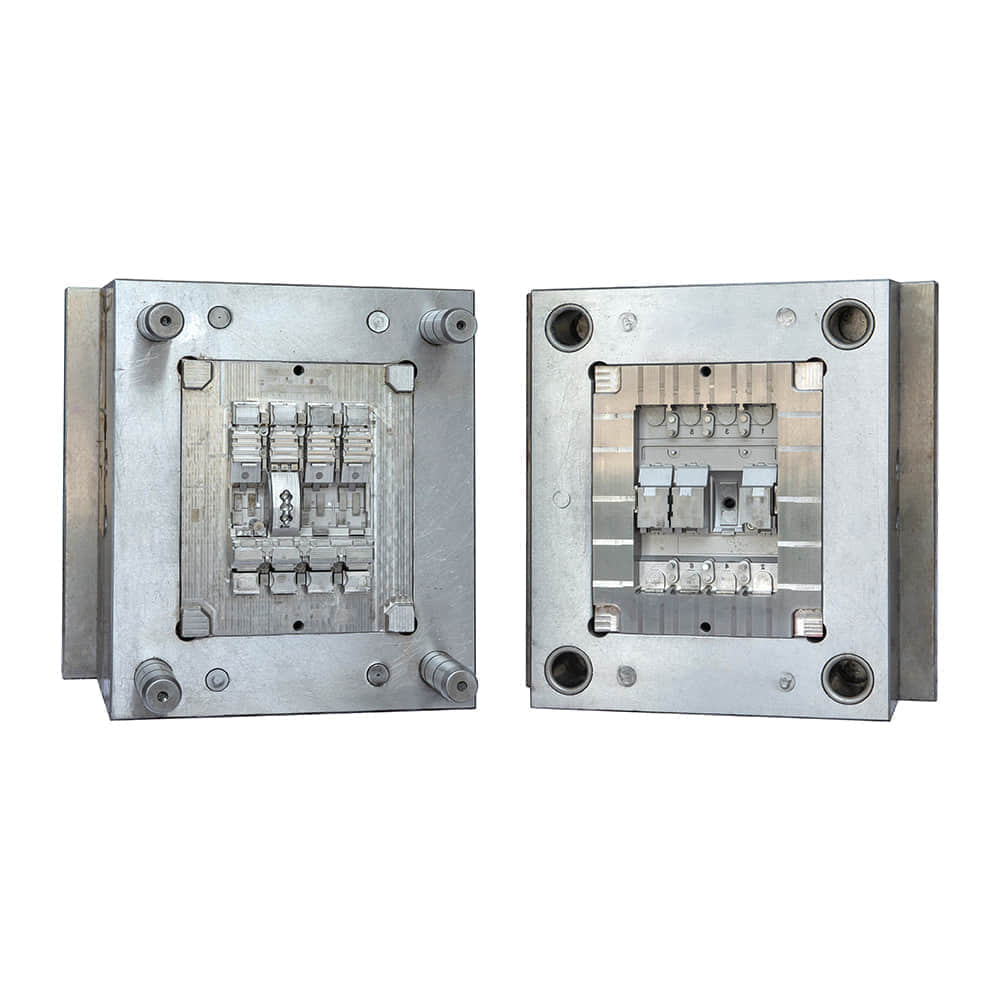
The Injection Molding Process
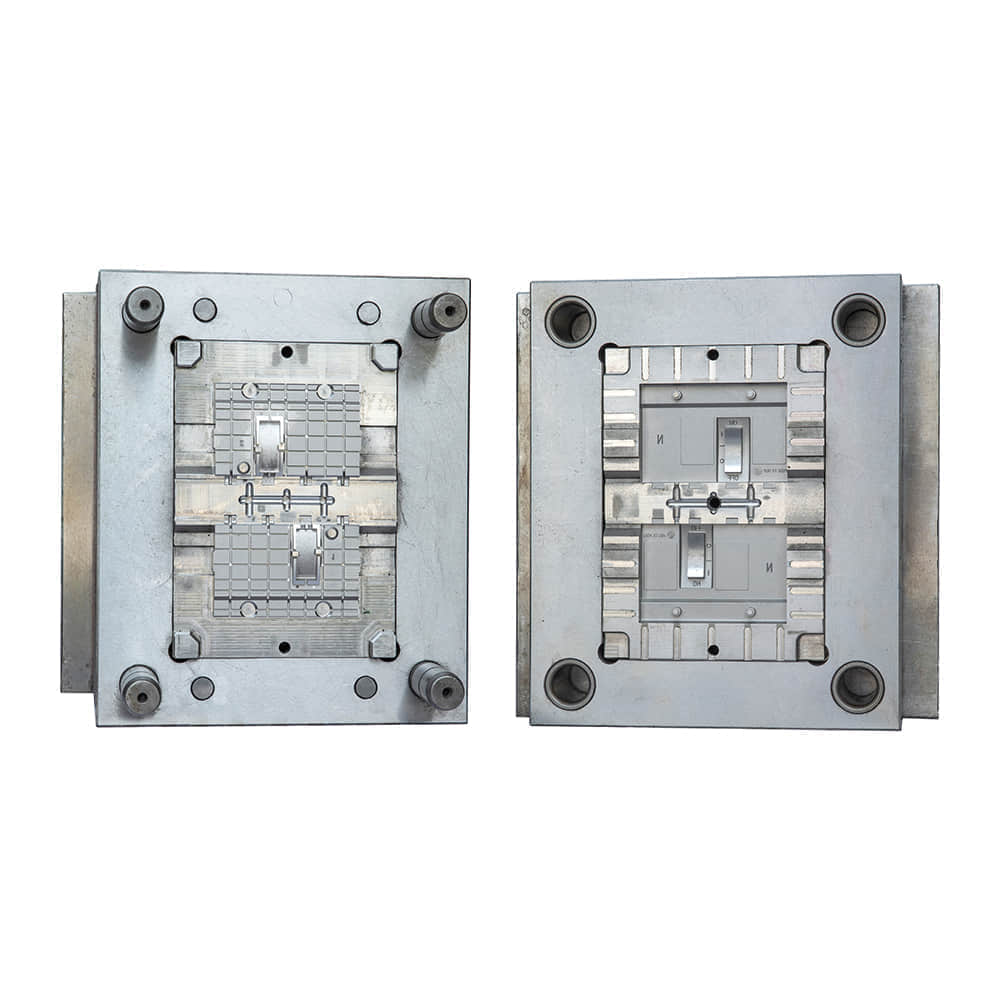
Injection molding is a manufacturing technique that involves injecting molten material – typically plastic – into a specially designed mold, allowing it to cool and solidify to form the desired shape. The process begins with the preparation of the mold, which is precision-engineered to mirror the final product. Once the mold is ready, the chosen material is heated to its melting point and then injected under high pressure into the mold cavity. After the material fills the mold and takes its shape, it is cooled, and the mold is opened to reveal the newly formed part. Precision Engineering and Design Flexibility One of the primary advantages of injection molded parts is the level of precision they offer. The molds themselves are crafted with meticulous attention to detail, often employing advanced technologies such as computer-aided design (CAD) and computer-aided manufacturing (CAM). This results in parts that boast consistent dimensions and intricate features, meeting the strictest of tolerances. Furthermore, injection molding provides remarkable design flexibility. Engineers can create parts with complex geometries, undercuts, and varying wall thicknesses – elements that might be challenging to achieve with other manufacturing methods. This versatility allows manufacturers to produce components that are not only functional but also aesthetically pleasing. Wide-Ranging Applications The applications of injection molded parts are virtually limitless. Industries such as automotive, electronics, medical devices, consumer goods, and aerospace heavily rely on these parts to achieve their desired outcomes. In the automotive sector, injection molded components are found in everything from interior panels to intricate engine parts. Electronics benefit from the process by obtaining small, intricately designed parts for devices like smartphones and laptops. The medical field utilizes injection molding to create sterile and precise medical equipment. Advantages Galore The adoption of injection molded parts brings forth a multitude of advantages. First and foremost, the efficiency of the process translates into reduced production costs. The rapid cycle times of injection molding allow for a higher volume of parts to be produced in a shorter time frame, lowering labor costs and energy consumption. The ability to use a wide range of materials is another feather in the cap of injection molding. Whether it’s commodity plastics or engineering-grade materials, the process can accommodate various material types, each chosen for its unique properties such as strength, durability, or resistance to heat and chemicals. Sustainability and the Future In an era where environmental consciousness is paramount, injection molding stands out for its potential in sustainable manufacturing. Many of the materials used in the process are recyclable, contributing to the circular economy. Additionally, the efficiency of injection molding results in less material waste compared to traditional machining methods. Looking ahead, technological advancements continue to enhance the capabilities of injection molding. From improved mold design and simulation software to the integration of automation and robotics, the future holds even greater promise for this already impressive manufacturing technique. Conclusion Injection molded parts have undoubtedly transformed the manufacturing landscape. With their precision, design flexibility, and wide-ranging applications, they have become an integral part of countless industries. As technology continues to evolve, injection molding is poised to become even more efficient, sustainable, and essential in shaping the products of tomorrow.
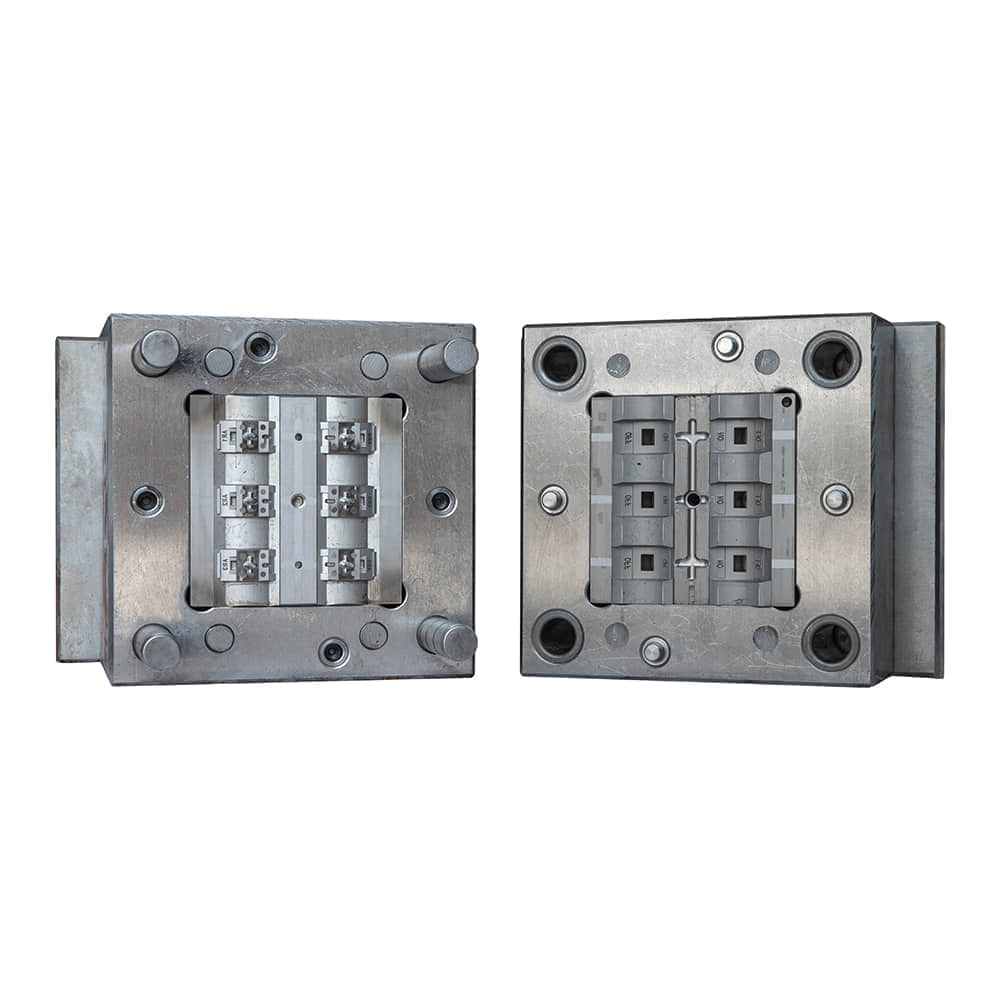