In the realm of modern manufacturing, where efficiency, precision, and quality converge, injection molded parts manufacturers stand as the cornerstone of countless industries. Through their advanced techniques and innovative processes, these manufacturers have transformed the way products are made, revolutionizing industries such as automotive, electronics, medical devices, and consumer goods. This article delves into the intricate world of injection molded parts manufacturing, exploring its techniques, applications, and impact.
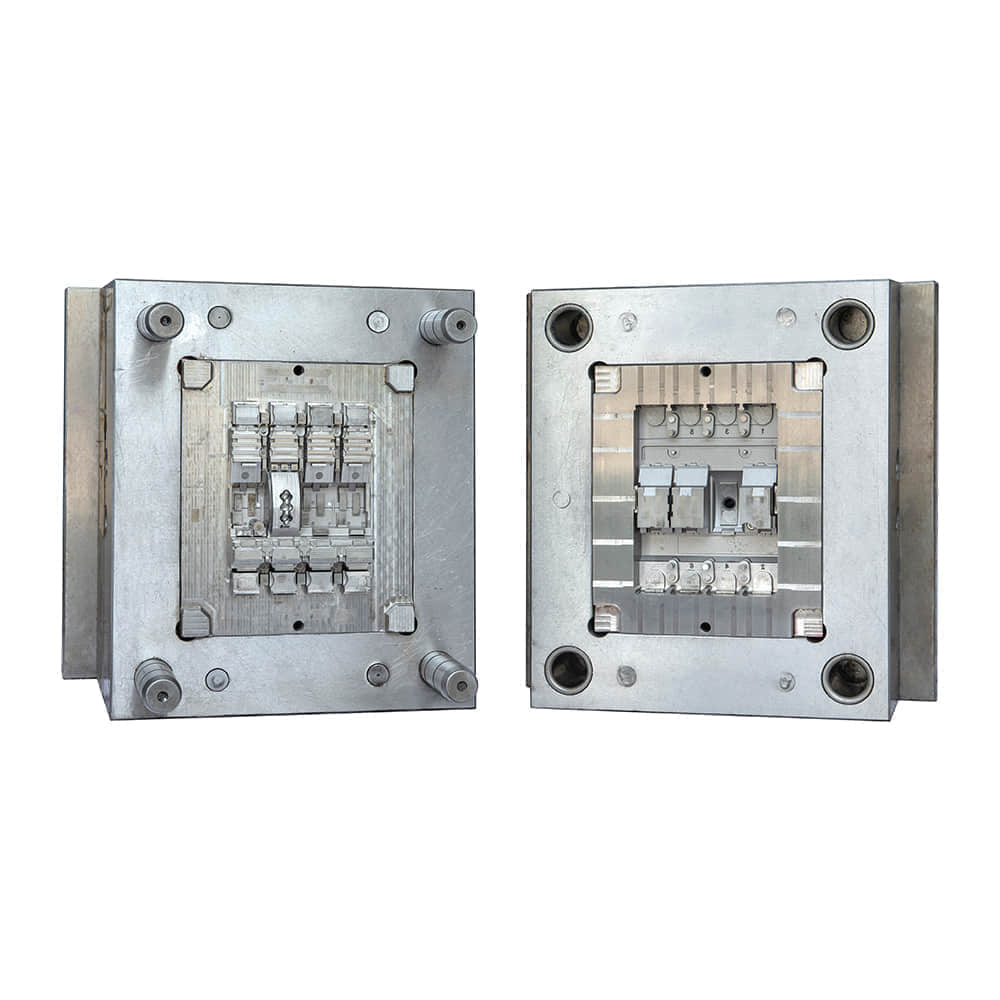
Injection Molding Process: Mastering Complexity with Precision
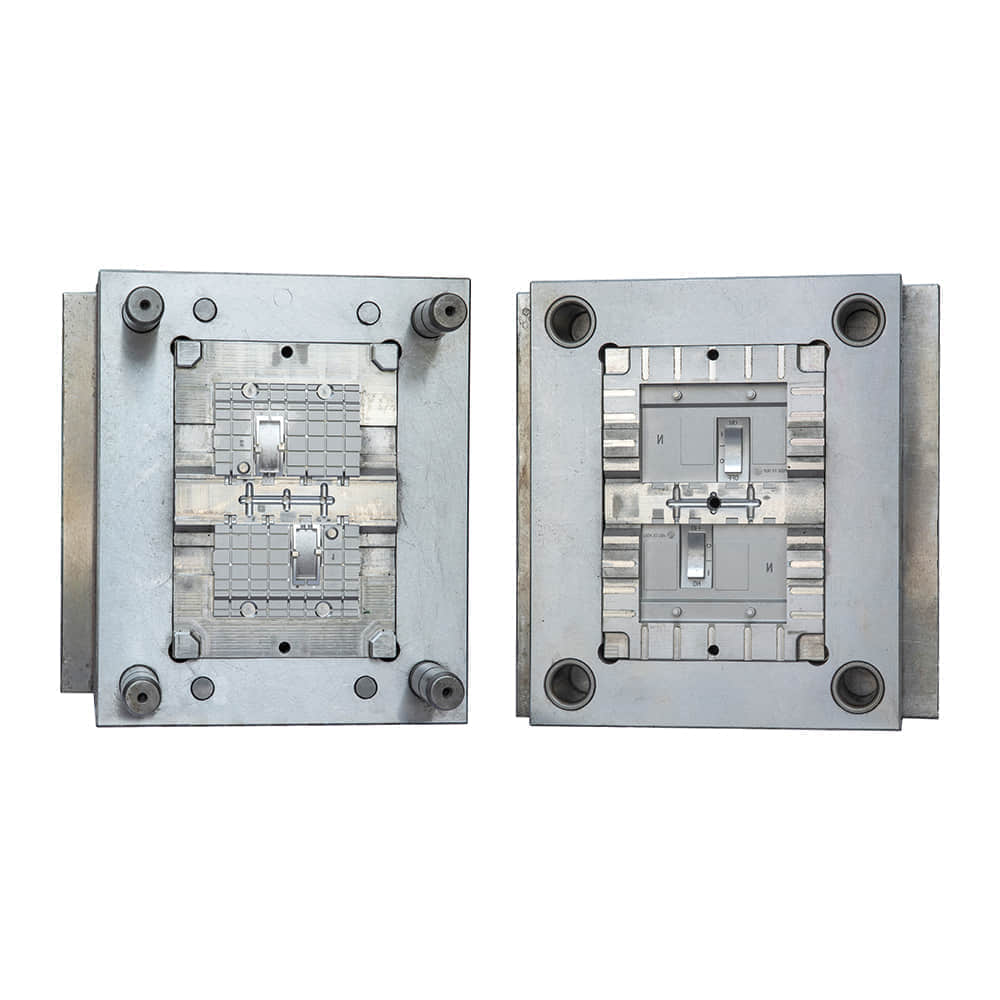
Injection molding is a manufacturing process that involves injecting molten material, typically plastic, into a specially designed mold. This mold is crafted to exact specifications, enabling the creation of intricate and complex shapes with remarkable accuracy. The process begins with the selection of the appropriate material, which is then melted and injected into the mold at high pressure. Once the material cools and solidifies, the mold is opened, and the finished product is ejected. The precision of injection molding is unmatched in the manufacturing world. Manufacturers can produce intricate details, tight tolerances, and consistent dimensions with every part they create. This level of accuracy not only ensures product quality but also enhances functionality and performance, especially in industries that demand uncompromising precision. Applications Across Industries: From Automotive to Healthcare Injection molded parts are ubiquitous, playing a crucial role in various industries. In the automotive sector, these parts contribute to lightweight and fuel-efficient vehicles, while maintaining structural integrity and safety standards. From interior components like dashboards and seats to critical elements like bumpers and engine parts, injection molded components are the driving force behind innovation in the automotive field. The electronics industry benefits from injection molding as well, producing intricate casings for devices like smartphones, laptops, and wearables. The method enables the creation of components with built-in features such as snap fits, hinges, and tiny, precise channels for wiring and cooling. In the healthcare sector, injection molded parts find their place in the production of medical devices, equipment, and even packaging. The ability to create sterile and functional parts with consistency is essential in this field, where patient safety is paramount. The Environmental Aspect: Efficiency and Sustainability Modern injection molding manufacturers are not only concerned with precision and quality but also with sustainability. Many have adopted environmentally friendly practices by incorporating recycled materials, optimizing production processes to reduce waste, and employing energy-efficient machinery. The durability and longevity of injection molded parts also contribute to sustainability, as they often outlast alternatives and require fewer replacements. Challenges and Innovations Despite its many advantages, injection molding isn’t without challenges. Designing intricate molds can be complex and time-consuming, and selecting the right material for each application requires careful consideration. However, manufacturers are continuously pushing the boundaries of innovation. Advanced software and simulation tools aid in mold design, while material science advancements lead to the development of more versatile and durable plastics. The Future of Injection Molded Parts Manufacturing As technology continues to evolve, the future of injection molded parts manufacturing looks promising. The integration of automation, artificial intelligence, and machine learning could further enhance efficiency and precision. Customization could also take center stage, allowing manufacturers to cater to individual needs with shorter lead times. In conclusion, injection molded parts manufacturers play a vital role in shaping the modern world. Their unwavering commitment to precision, innovation, and sustainability ensures that industries continue to thrive. From the cars we drive to the devices we use, injection molded parts are the unsung heroes driving progress and perfection.
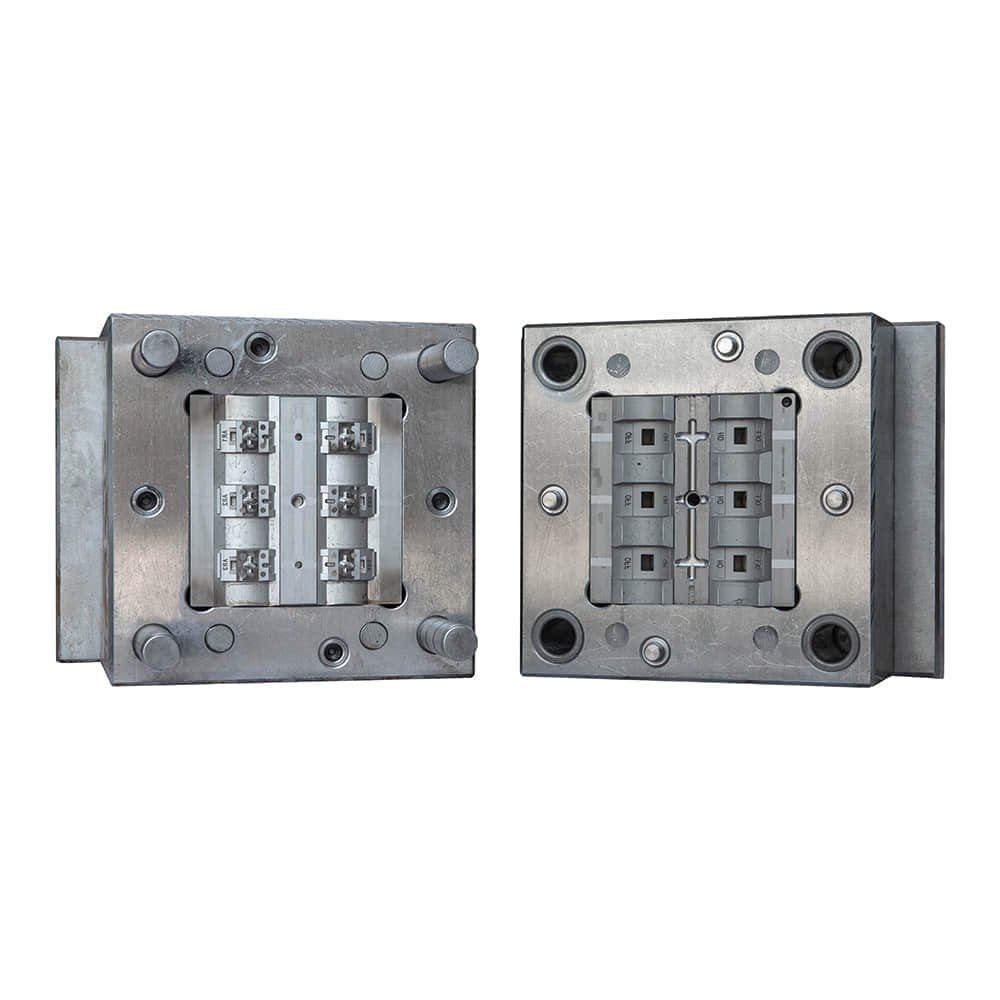