Progressive Die: Precision in Mass Production
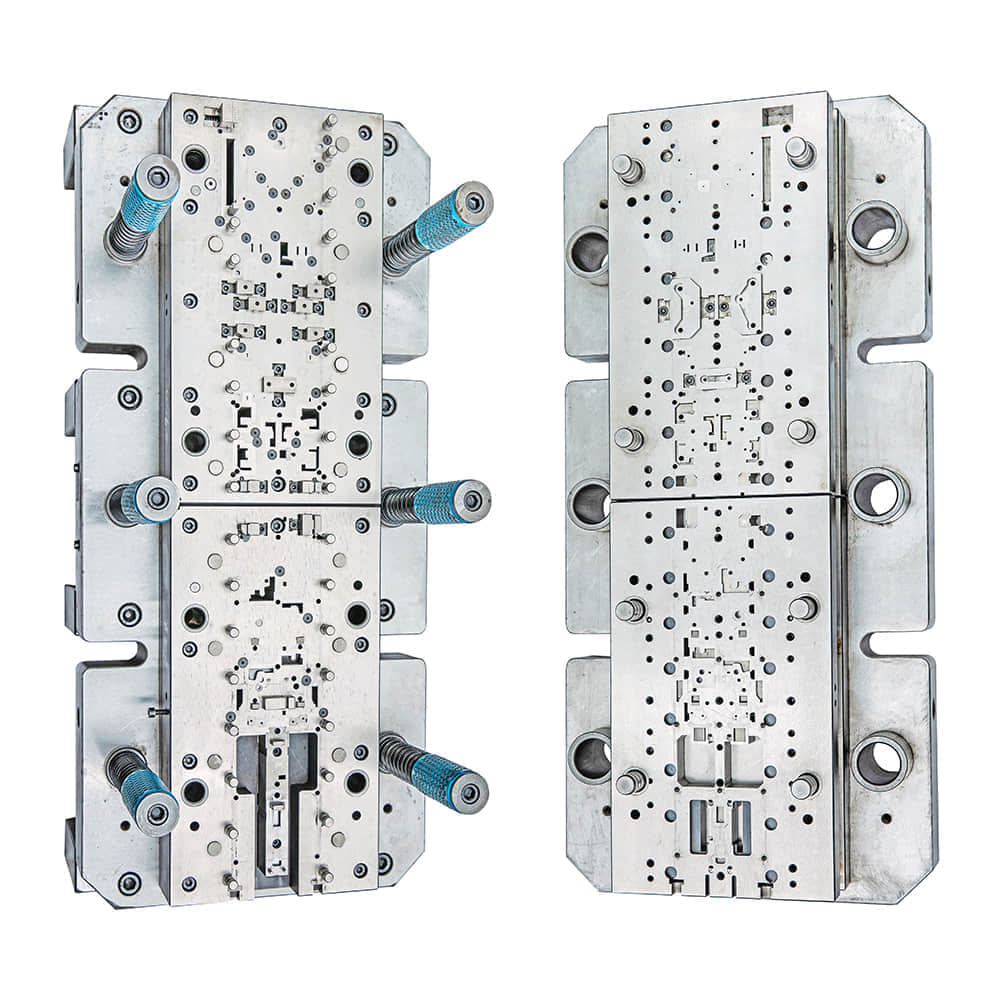
In today’s fast-paced manufacturing world, achieving high levels of precision and efficiency is paramount. Progressive die technology has emerged as a crucial tool in the arsenal of manufacturers seeking to meet these demands. This advanced tooling system enables the mass production of intricate parts with exceptional accuracy. In this article, we will delve into the world of progressive dies, exploring their functionality, advantages, and diverse applications in the manufacturing industry.
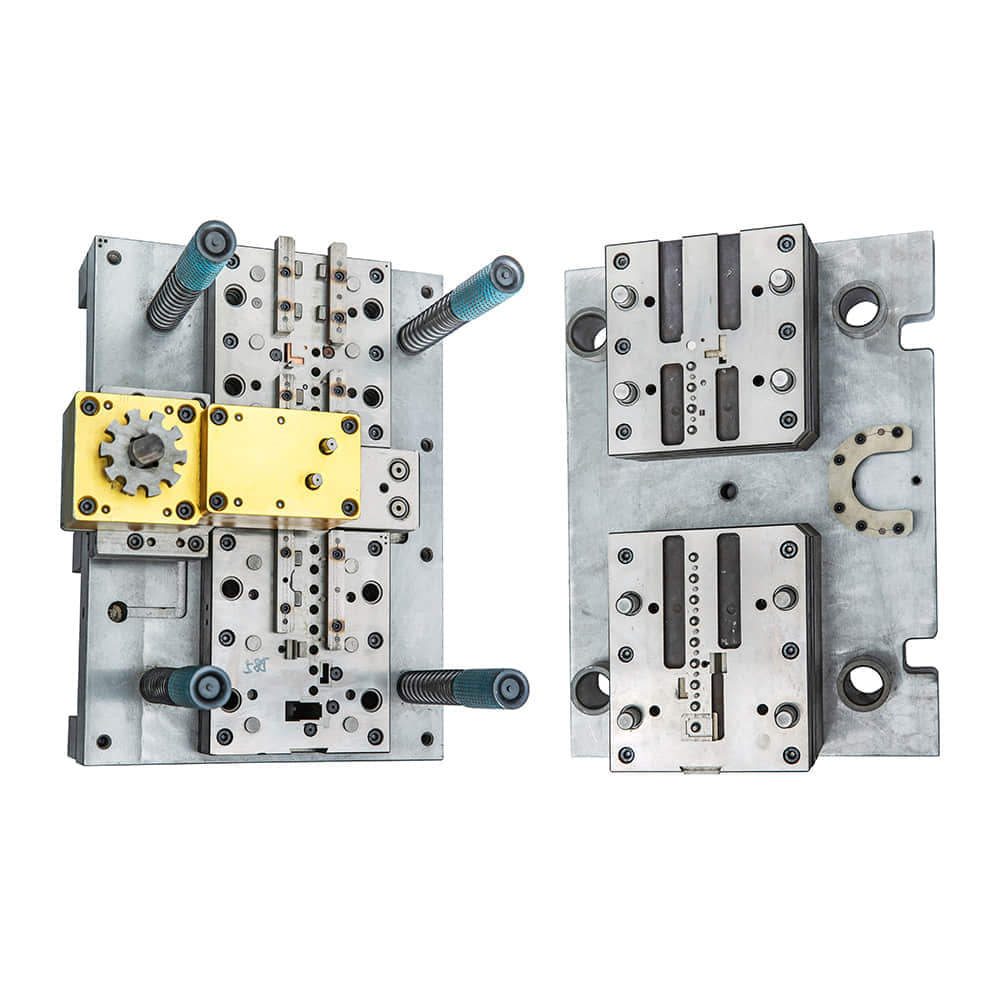
Progressive Die: An Overview A progressive die is a specialized tool used in metal stamping and forming processes. It comprises a series of stations, each with a unique cutting or forming operation. The workpiece, typically a metal strip, progresses through these stations, with each station performing a specific operation until the final part is produced. The use of multiple stations in a single die greatly enhances production efficiency and precision. How Progressive Dies Work The operation of a progressive die is a symphony of precision and coordination. Here is a step-by-step breakdown of how it works: Feeding: The process begins with a coil or strip of metal being fed into the die. This strip is typically made of materials such as steel, aluminum, or copper. Piercing and Blanking: The first station is often dedicated to piercing and blanking. Piercing creates holes in the material, while blanking cuts out the rough shape of the part. Bending: In subsequent stations, the strip may be bent or formed into the desired shape. Precision tooling and careful design ensure that each bend is accurate and consistent. Coining and Embossing: Some progressive dies include stations for coining and embossing, which add fine details and patterns to the part’s surface. Trimming: Trimming stations ensure that the final part has clean edges and consistent dimensions. Extraction: Once the part has passed through all necessary stations, it is extracted from the strip, leaving behind scrap material. Advantages of Progressive Dies Progressive dies offer numerous advantages to manufacturers: High Efficiency: By performing multiple operations in a single pass, progressive dies significantly reduce production time, resulting in higher output. Precision: The intricate design of progressive dies allows for exceptionally tight tolerances and consistent part dimensions. Cost-Effective: Despite the initial investment in tooling, progressive dies prove cost-effective in high-volume production due to their efficiency and longevity. Versatility: Progressive dies can be designed for a wide range of part geometries and materials, making them suitable for various industries. Reduced Scrap: Precise control over the manufacturing process reduces material waste, minimizing environmental impact. Applications of Progressive Dies Progressive dies find applications across a multitude of industries: Automotive: Progressive dies are commonly used to manufacture automotive components such as brackets, clips, and connectors. Electronics: They play a crucial role in producing intricate electronic components like connectors and contact springs. Appliances: Progressive dies are used to manufacture parts for household appliances, ensuring consistent quality. Aerospace: In the aerospace industry, progressive dies are employed to create precision components for aircraft and spacecraft. Medical Devices: The medical sector relies on progressive dies for producing intricate components used in medical devices. Consumer Goods: From zippers to buttons, progressive dies are instrumental in the production of various consumer goods. In conclusion, progressive dies are a cornerstone of modern manufacturing, enabling the production of intricate parts with unparalleled precision and efficiency. Their versatility and ability to streamline mass production make them indispensable tools in a wide range of industries. As technology continues to advance, we can expect progressive dies to play an even more significant role in shaping the future of manufacturing.
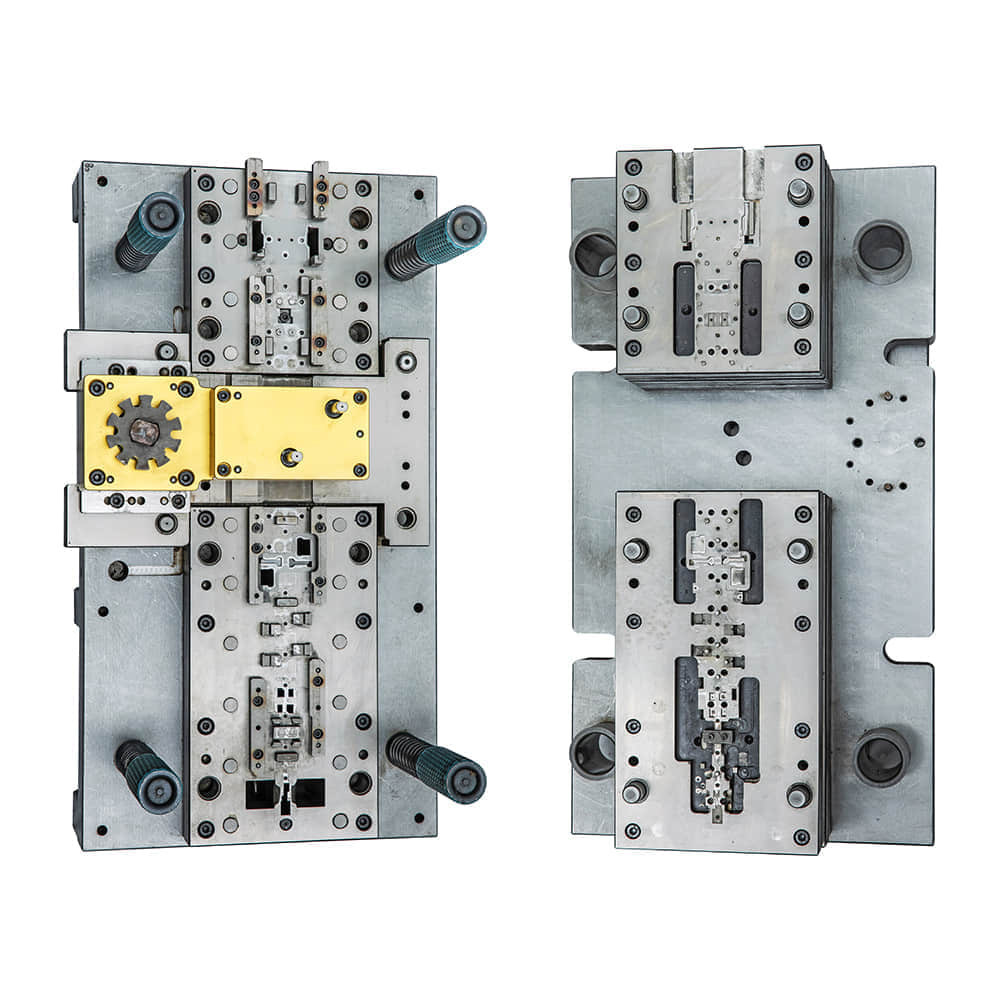