Thermoplastic Injection Molds: Revolutionizing Manufacturing
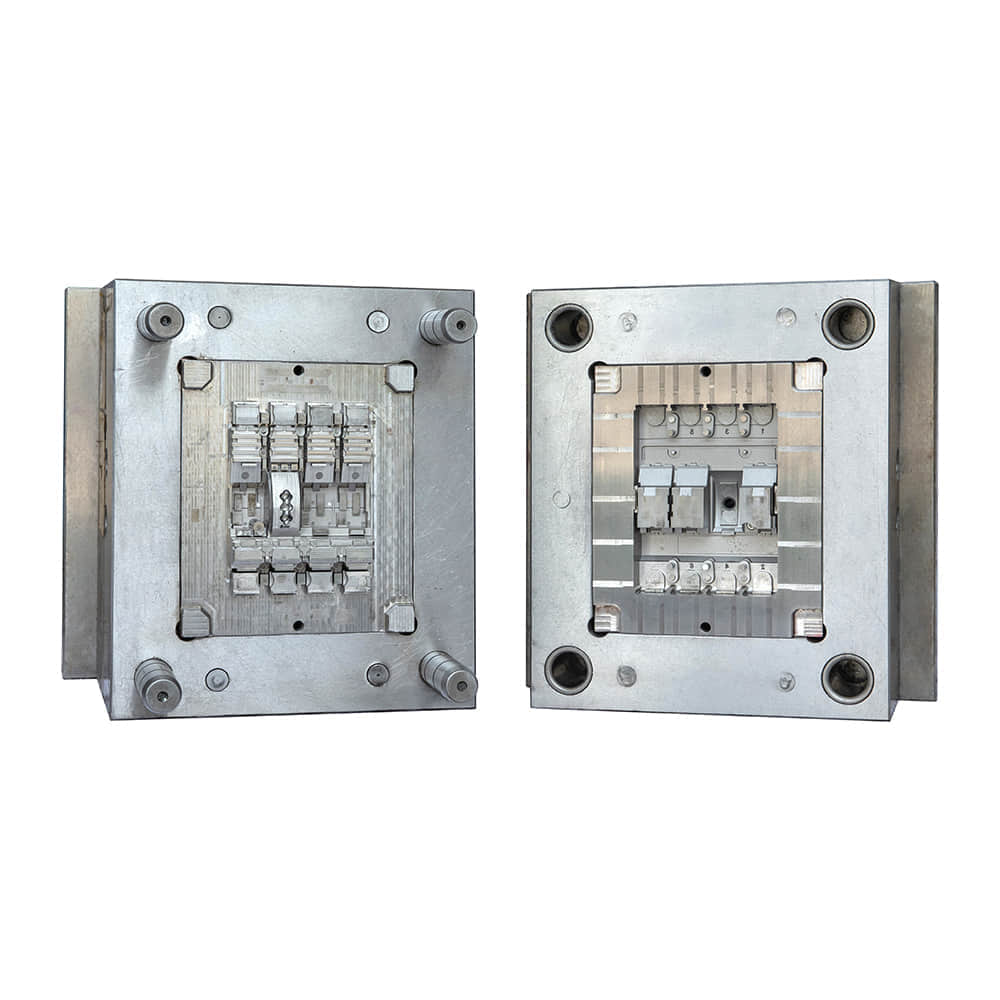
In the ever-evolving landscape of manufacturing, innovation is the key to success. One such innovation that has transformed the industry is thermoplastic injection molding. This cutting-edge technology has revolutionized the way products are designed and manufactured, offering efficiency, precision, and versatility that were once unimaginable. In this article, we will delve into the world of thermoplastic injection molds, exploring their advancements and diverse applications.
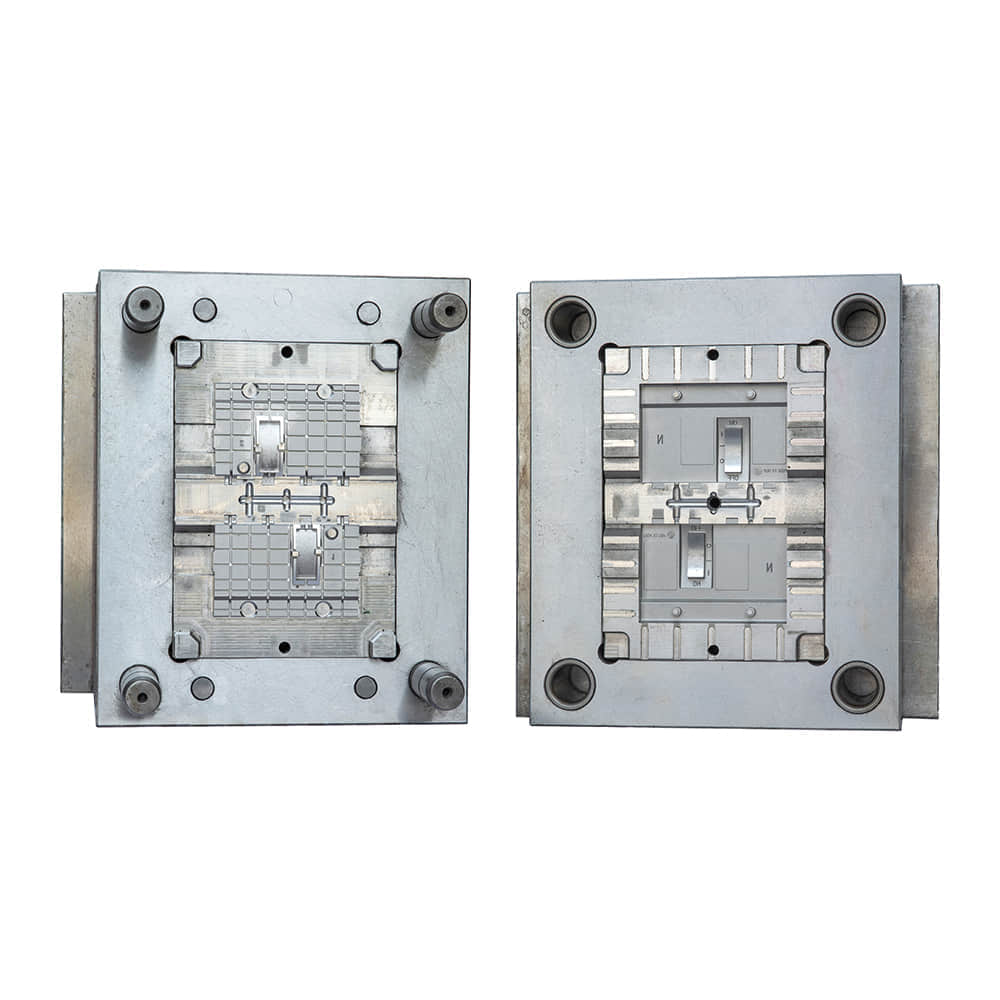
Understanding Thermoplastic Injection Molds Thermoplastic injection molding is a manufacturing process that involves injecting molten thermoplastic materials into a mold cavity. Once the material cools and solidifies, the mold is opened, revealing a finished product. This process is highly precise, allowing for the creation of complex and intricate parts with remarkable consistency. The following are some of the key advancements and applications of thermoplastic injection molds. 1. Precision Engineering One of the most notable advancements in thermoplastic injection molding is the level of precision it offers. Computer-aided design (CAD) and computer-aided manufacturing (CAM) have revolutionized mold design and production. Engineers can create intricate molds with micro-level details, ensuring that each product is manufactured with the utmost precision. This level of accuracy is invaluable in industries such as aerospace, medical devices, and electronics, where even the slightest imperfection can have dire consequences. 2. Cost-Effective Production Thermoplastic injection molds have significantly reduced production costs. Mass production is more efficient than ever before, thanks to rapid cycle times and minimal material waste. This cost-effectiveness has made it possible for small and medium-sized businesses to compete with larger corporations, leveling the playing field and encouraging innovation. 3. Material Versatility Another remarkable aspect of thermoplastic injection molding is its material versatility. Manufacturers can choose from a wide range of thermoplastic materials, each with unique properties. From the durability of ABS to the clarity of polycarbonate, these materials can be tailored to meet specific product requirements. This versatility is particularly beneficial in industries such as automotive, where parts must withstand extreme conditions, and consumer goods, where aesthetics play a crucial role. 4. Environmental Sustainability In today’s environmentally conscious world, thermoplastic injection molds have also made strides in sustainability. The process generates minimal waste, as excess material can be recycled. Additionally, the use of biodegradable thermoplastics is becoming more common, reducing the environmental impact of the manufacturing process. Applications of Thermoplastic Injection Molds The applications of thermoplastic injection molds are vast and diverse, spanning across various industries. Here are a few notable examples: 1. Automotive Industry Automobile manufacturers use thermoplastic injection molds to produce interior and exterior components. These molds create parts that are not only durable but also lightweight, contributing to improved fuel efficiency. 2. Medical Devices In the medical field, precision and consistency are paramount. Thermoplastic injection molds are used to manufacture intricate medical devices, such as syringes, catheters, and prosthetic components. 3. Consumer Electronics The production of consumer electronics demands high precision and material versatility. Thermoplastic injection molds are employed to create casings, buttons, and connectors for a wide range of electronic devices. 4. Packaging The packaging industry benefits from thermoplastic injection molding to create custom-designed packaging solutions that protect products and enhance their visual appeal. Conclusion Thermoplastic injection molds have transformed the manufacturing landscape, offering precision, cost-effectiveness, material versatility, and sustainability. As technology continues to advance, the potential applications of this innovative process are boundless. From aerospace to healthcare, thermoplastic injection molds play a pivotal role in shaping the products we use in our daily lives. As we move forward, it is certain that these molds will continue to be at the forefront of manufacturing, driving innovation and efficiency in industries across the globe.
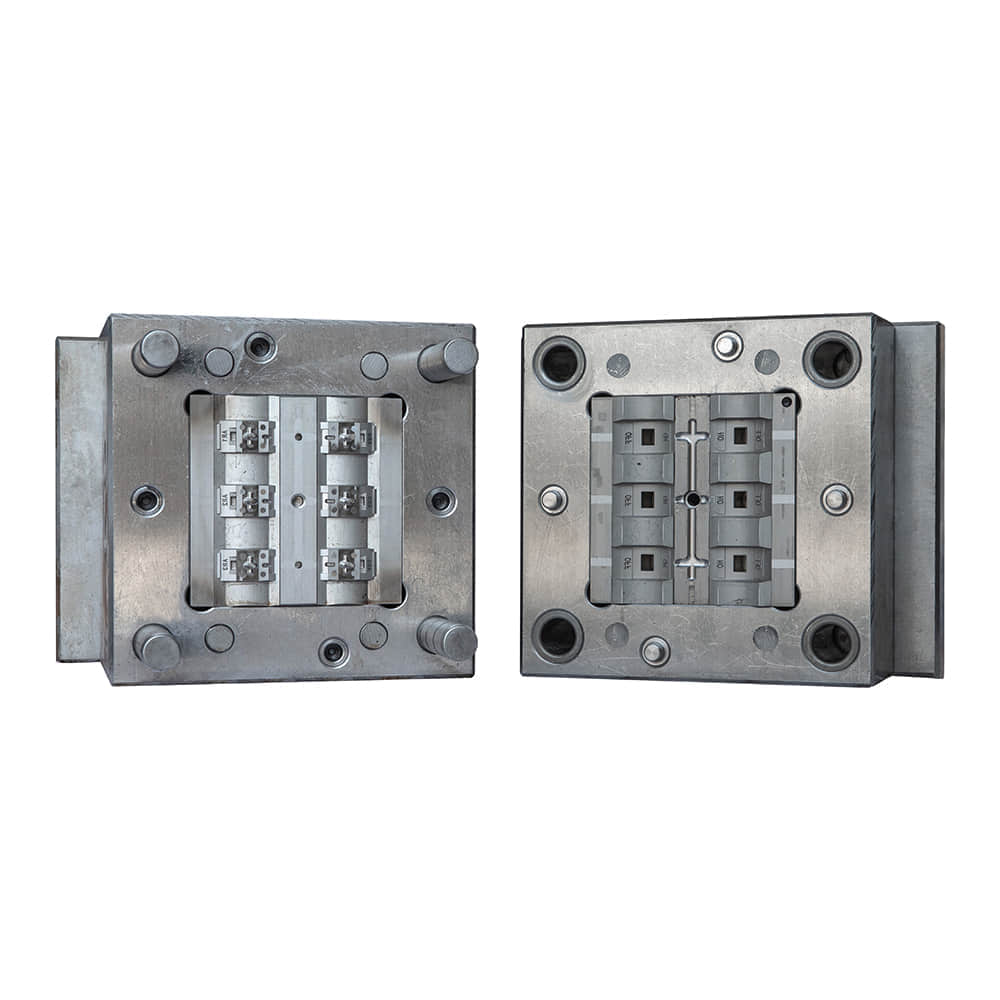