In the ever-evolving landscape of manufacturing and industrial processes, precision and efficiency are paramount. One technology that has gained significant traction in recent years is DMC injection, an innovative method that has revolutionized various industries. In this article, we will delve into the intricacies of DMC injection, its applications, benefits, and the promising future it holds.
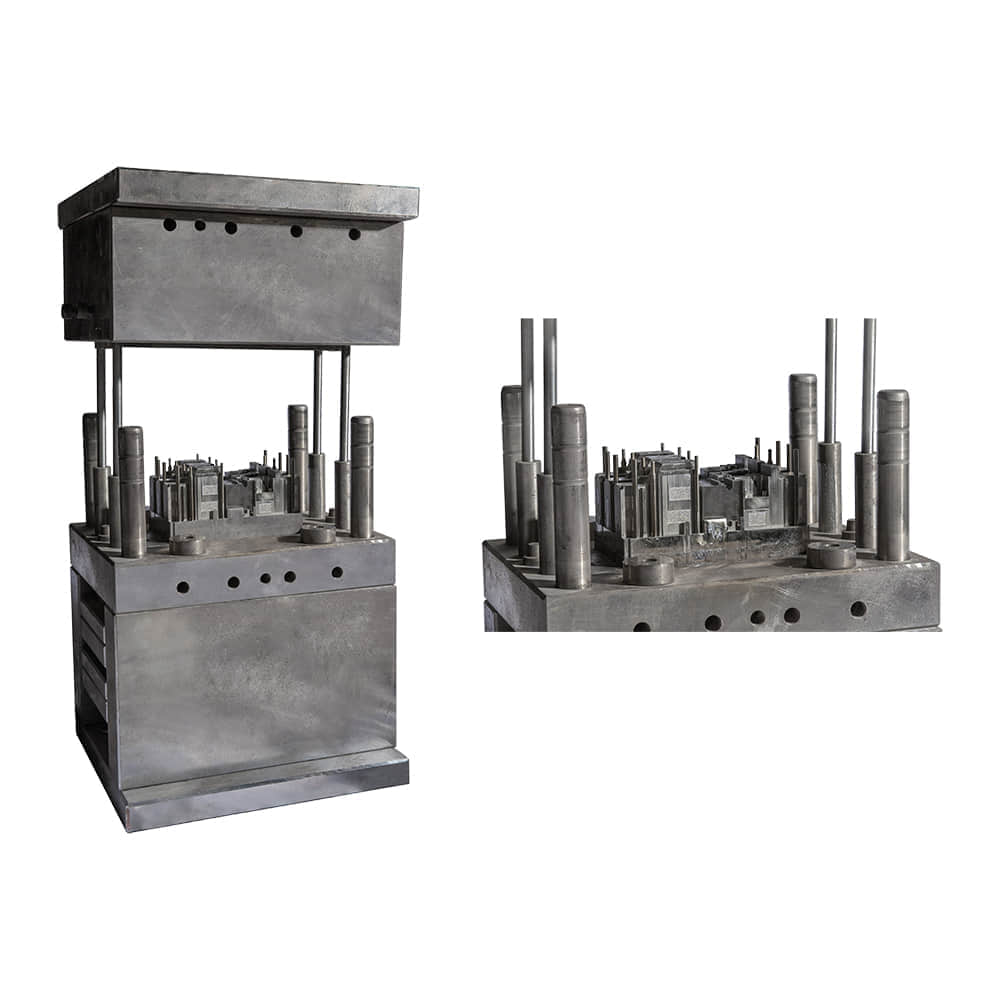
Understanding DMC Injection
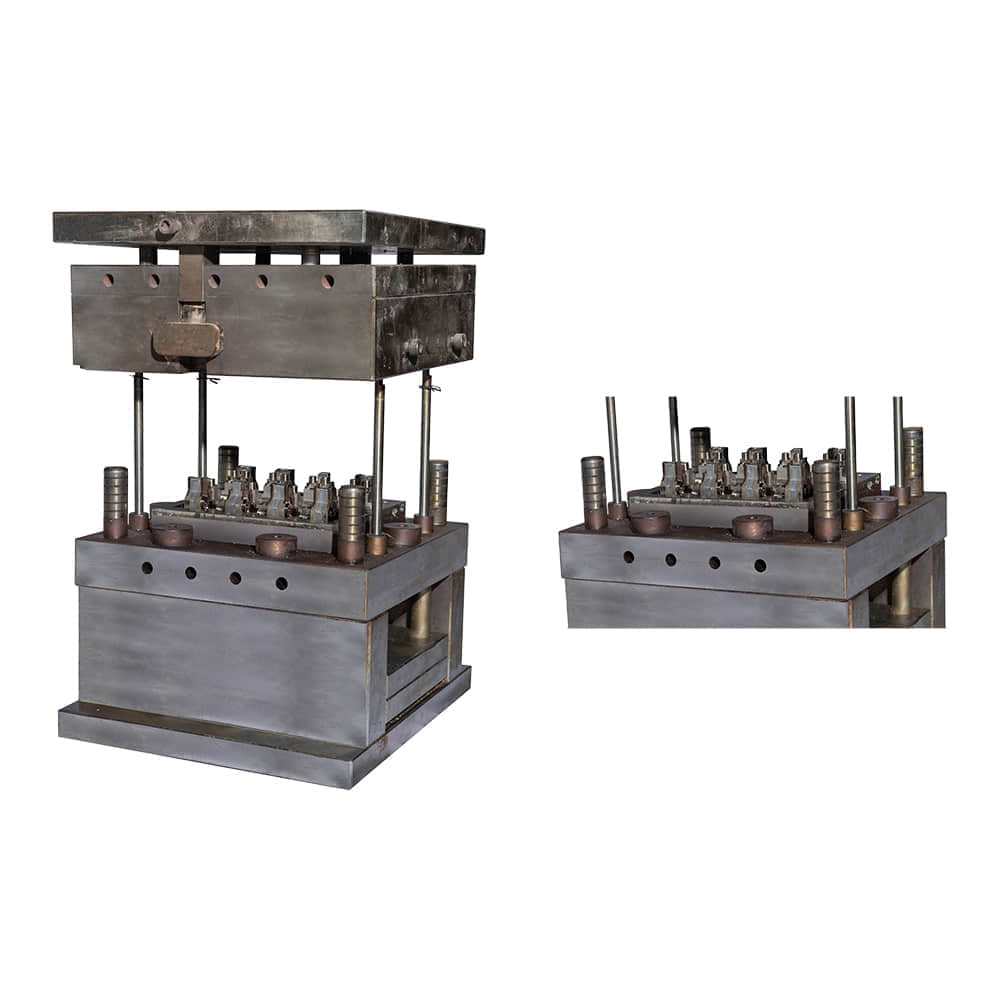
DMC injection, or Direct Metal Casting injection, is a cutting-edge manufacturing technique that combines the principles of 3D printing and metal casting. It enables the production of intricate and complex metal components with unparalleled precision and speed. This process involves the injection of molten metal into a mold, where it solidifies to form the desired part. Applications of DMC Injection Aerospace Industry One of the primary beneficiaries of DMC injection is the aerospace industry. The demand for lightweight, high-strength components in aircraft and spacecraft is incessant. DMC injection allows for the creation of such components with reduced weight and increased structural integrity. This not only enhances fuel efficiency but also ensures the safety of passengers and crew. Automotive Sector In the automotive sector, DMC injection is reshaping the way vehicles are manufactured. Engine components, transmission parts, and even entire chassis are now being produced using this technology. The advantages include improved fuel efficiency, durability, and the ability to design more aerodynamic and aesthetically pleasing vehicles. Medical Devices The medical field benefits from DMC injection by producing customized implants and prosthetics. These devices are not only more comfortable for patients but also offer enhanced biocompatibility, reducing the risk of rejection. Additionally, the speed of production means patients can receive their personalized implants faster, improving their overall quality of life. Electronics In the electronics industry, DMC injection is employed to create intricate circuitry and heat-dissipating components. The precision offered by this technology ensures that electronic devices are smaller, more energy-efficient, and have increased processing power. Advantages of DMC Injection Precision DMC injection provides unmatched precision in manufacturing. The ability to create complex geometries and fine details is unrivaled, making it ideal for industries where precision is paramount. Speed Traditional metal casting processes can be time-consuming. DMC injection, on the other hand, significantly reduces production time. This speed is invaluable, particularly in industries with rapidly changing demands. Material Efficiency This technology minimizes material waste by precisely injecting only the required amount of molten metal into the mold. This not only reduces costs but also aligns with sustainable manufacturing practices. Cost-Effectiveness Despite being a cutting-edge technology, DMC injection is becoming more cost-effective as it gains wider acceptance. Its advantages in precision, speed, and material efficiency translate into reduced overall production costs. Future Prospects The future of DMC injection holds great promise. As research and development efforts continue, we can anticipate further advancements in the technology. This may include the expansion of compatible materials, even greater precision, and the ability to create larger components. Moreover, DMC injection is likely to become more accessible to smaller manufacturers and startups, democratizing the advantages it offers. This democratization could lead to innovative applications in fields we have yet to explore fully. Conclusion In conclusion, DMC injection is a game-changer in the world of manufacturing. Its applications span across various industries, offering unmatched precision, speed, and cost-effectiveness. As this technology continues to evolve, we can expect to see even more groundbreaking developments, ultimately shaping the future of manufacturing and design. DMC injection is not just a manufacturing method; it’s a testament to human ingenuity and our unending quest for progress.
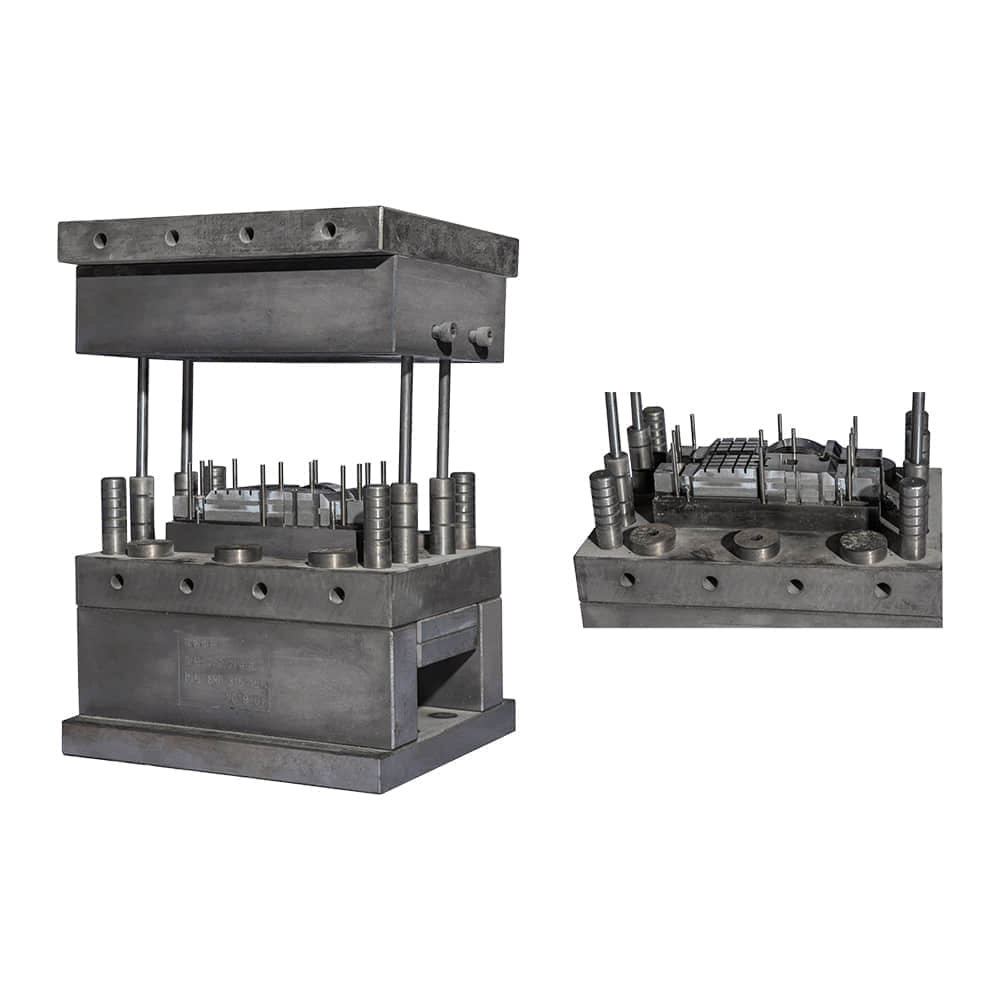