In today’s fast-paced manufacturing industry, injection molding stands as one of the most crucial processes for producing a wide range of plastic products. Behind this technology lies the craftsmanship of injection mold manufacturers, who blend art and science to create precision molds that enable the mass production of everything from household items to automotive components. In this article, we will delve into the world of injection mold manufacturing, exploring its significance, techniques, and the key factors that make a successful injection mold manufacturer.
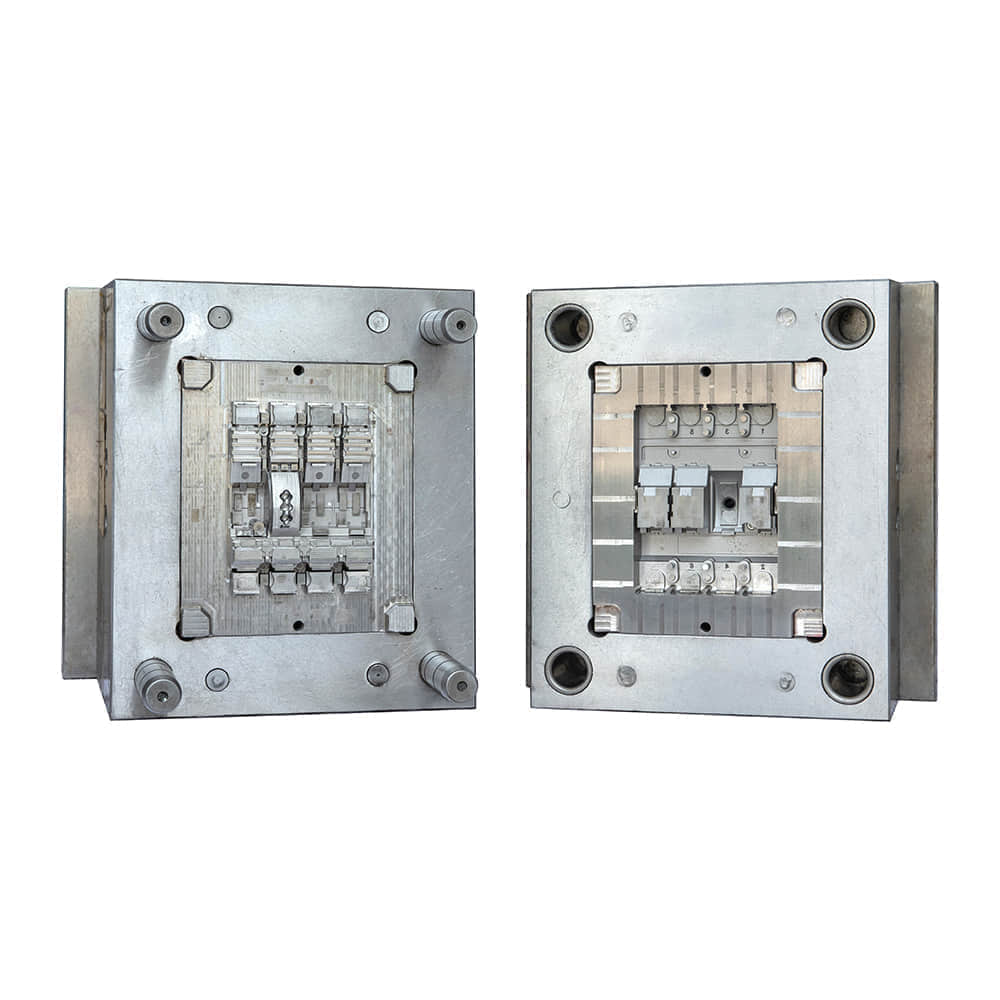
The Significance of Injection Mold Manufacturing
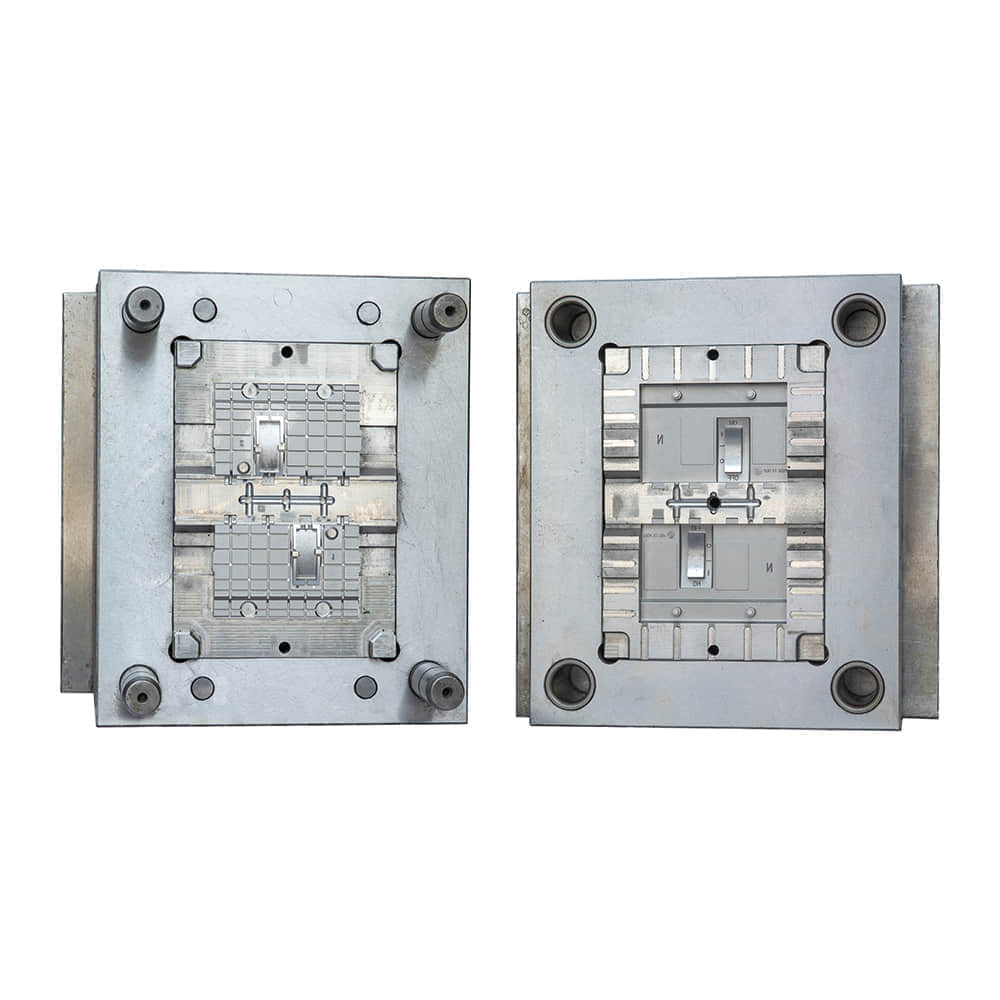
Injection mold manufacturing is the cornerstone of modern manufacturing. It plays a pivotal role in industries such as automotive, consumer electronics, medical devices, and packaging. The process involves melting plastic pellets and injecting the molten material into a meticulously designed mold. Once cooled and solidified, the mold is opened, revealing a perfectly shaped plastic part. This efficient and cost-effective method allows for high-volume production with remarkable precision and consistency. The significance of injection mold manufacturing lies in its ability to transform design concepts into tangible products. Whether it’s the sleek dashboard of a luxury car or the housing of a smartphone, the molds used in these processes are the unsung heroes behind every successful product launch. Manufacturers rely on injection mold makers to produce molds that are not only accurate and durable but also optimized for efficient production. The Art of Designing Injection Molds Crafting injection molds is both an art and a science. It starts with the design phase, where engineers and designers collaborate to create molds that meet the specific requirements of a product. The design process involves meticulous attention to detail, as even minor flaws can result in defective parts and costly production delays. One of the key artistic elements in mold design is understanding the flow of molten plastic. Mold designers must anticipate how the plastic will fill every cavity of the mold, ensuring that it cools uniformly and solidifies without defects. Achieving this requires a deep understanding of materials, thermodynamics, and fluid dynamics. The Science of Precision Manufacturing Once the mold design is complete, the manufacturing process begins. This phase demands precision and consistency to produce molds that can withstand thousands or even millions of cycles without degradation. Injection mold manufacturers employ advanced CNC machining techniques to shape the mold components with micron-level accuracy. Materials selection is another critical aspect of the process. Molds must withstand high temperatures and pressures, so choosing the right materials, such as tool steel or aluminum, is essential to ensure longevity and performance. Furthermore, surface finishing and polishing are integral to creating molds that produce flawless parts. Any imperfections or rough spots on the mold’s surface can transfer to the final product, leading to defects. The Role of Technology and Innovation In today’s competitive manufacturing landscape, injection mold manufacturers are constantly pushing the boundaries of technology and innovation. Computer-aided design (CAD) and computer-aided manufacturing (CAM) software have revolutionized mold design and production. These tools enable manufacturers to simulate and optimize the entire injection molding process, reducing the need for costly trial-and-error iterations. Furthermore, 3D printing and additive manufacturing have opened up new possibilities in rapid prototyping and mold development. Manufacturers can quickly produce prototype molds for testing and validation before investing in full-scale production molds. Conclusion Injection mold manufacturing is a captivating blend of art and science. The precision and craftsmanship required to design and produce molds that meet the demands of modern manufacturing are nothing short of remarkable. As technology continues to advance, injection mold manufacturers will play an increasingly vital role in shaping our world by turning innovative ideas into tangible products with speed and precision.