Metal stamping dies, often referred to as tooling, are an integral part of the manufacturing process for various industries. These precision-engineered tools are used to shape, cut, or form sheet metal into specific shapes and sizes. In this article, we will delve into the world of metal stamping dies, exploring their types, design considerations, and significance in modern manufacturing.
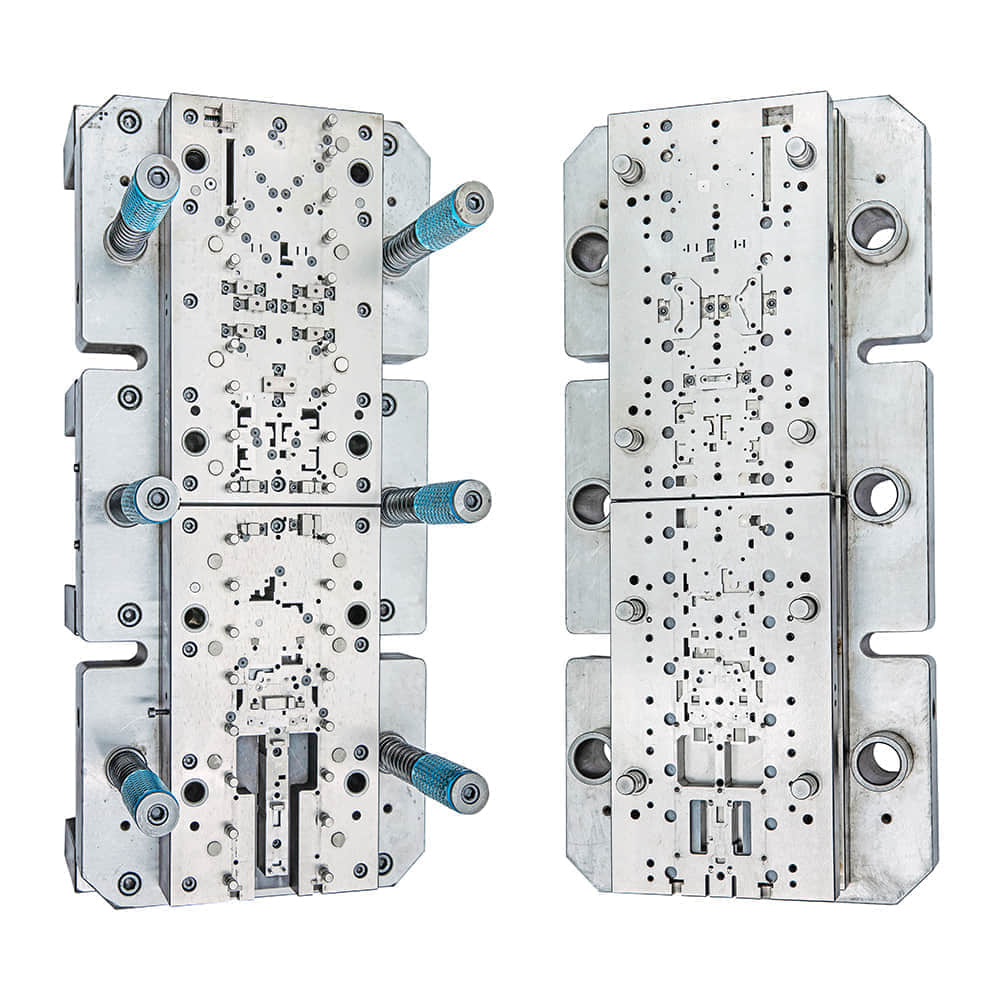
Types of Metal Stamping Dies
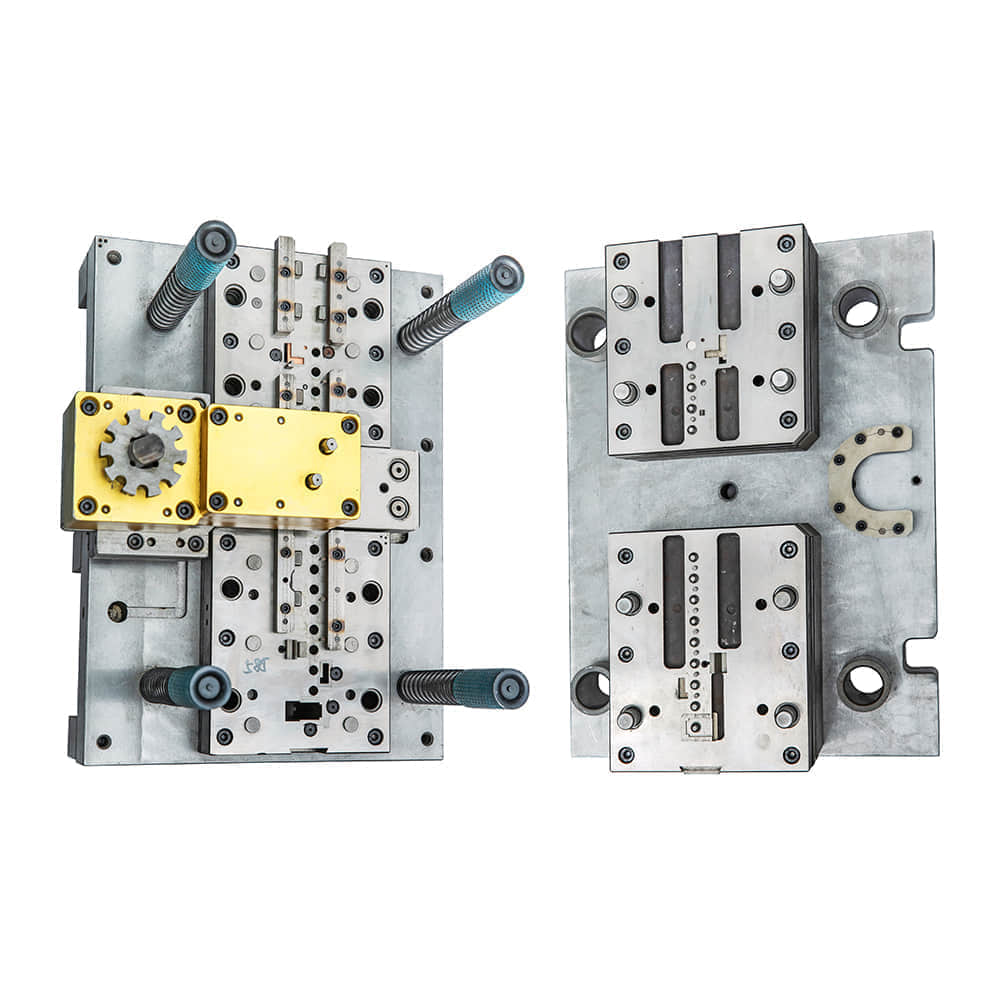
Metal stamping dies come in various types, each tailored to specific applications. The primary categories include: Blanking Dies:These dies are used to cut flat pieces, or blanks, from sheet metal. They are commonly used in the production of components like washers and brackets. Piercing Dies:Piercing dies create holes or openings in sheet metal, serving a vital role in the creation of components such as electrical enclosures and automotive parts. Bending Dies:Bending dies are designed to deform sheet metal into predetermined shapes. This type of die is crucial in fabricating components with complex geometries, such as appliance panels and aircraft parts. Drawing Dies:Drawing dies are employed to transform flat sheet metal into three-dimensional shapes. They are commonly used in the production of items like beverage cans and kitchen sinks. Progressive Dies:These dies are a combination of several dies working in tandem to perform multiple operations in a single pass. Progressive dies are highly efficient for high-volume production of components like connectors and fasteners. Compound Dies:Compound dies are used for operations that require more than one cutting or shaping operation, such as blanking and bending in a single die. Design Considerations The design of metal stamping dies is a meticulous process that requires careful consideration of several factors: Material Selection:Die materials must be chosen for their durability and ability to withstand high levels of wear and stress. Common die materials include tool steel, carbide, and various high-speed steels. Die Geometry:The geometry of the die must precisely match the desired end product. This involves meticulous planning and engineering to ensure accurate and consistent results. Tolerances:Tight tolerances are often necessary in precision manufacturing. Die designers must account for these tolerances to ensure the final product meets quality standards. Surface Finish:A smooth surface finish on the die is crucial to prevent defects in the stamped parts. Proper surface treatments and coatings are applied to achieve this. Die Maintenance:Regular maintenance is essential to ensure the longevity of stamping dies. This includes sharpening cutting edges, inspecting for wear, and making necessary repairs. The Significance of Metal Stamping Dies Metal stamping dies play a pivotal role in modern manufacturing for several reasons: Cost-Effective Production:Stamping dies enable cost-effective mass production of complex metal components, reducing labor costs and material waste. Precision and Consistency:Stamping dies offer unparalleled precision and consistency in shaping metal parts, leading to high-quality products. Efficiency:Progressive and compound dies can perform multiple operations in a single pass, increasing production efficiency and reducing lead times. Versatility:Metal stamping dies can be customized for various materials, including steel, aluminum, and copper, making them adaptable to a wide range of industries. Reduced Scrap:Precision dies minimize material waste, contributing to environmentally sustainable manufacturing processes. In conclusion, metal stamping dies are the unsung heroes of modern manufacturing. Their precision engineering and versatility enable the production of a wide array of metal components across diverse industries. As technology continues to advance, we can expect even more innovative developments in the world of metal stamping dies, further revolutionizing the manufacturing landscape.
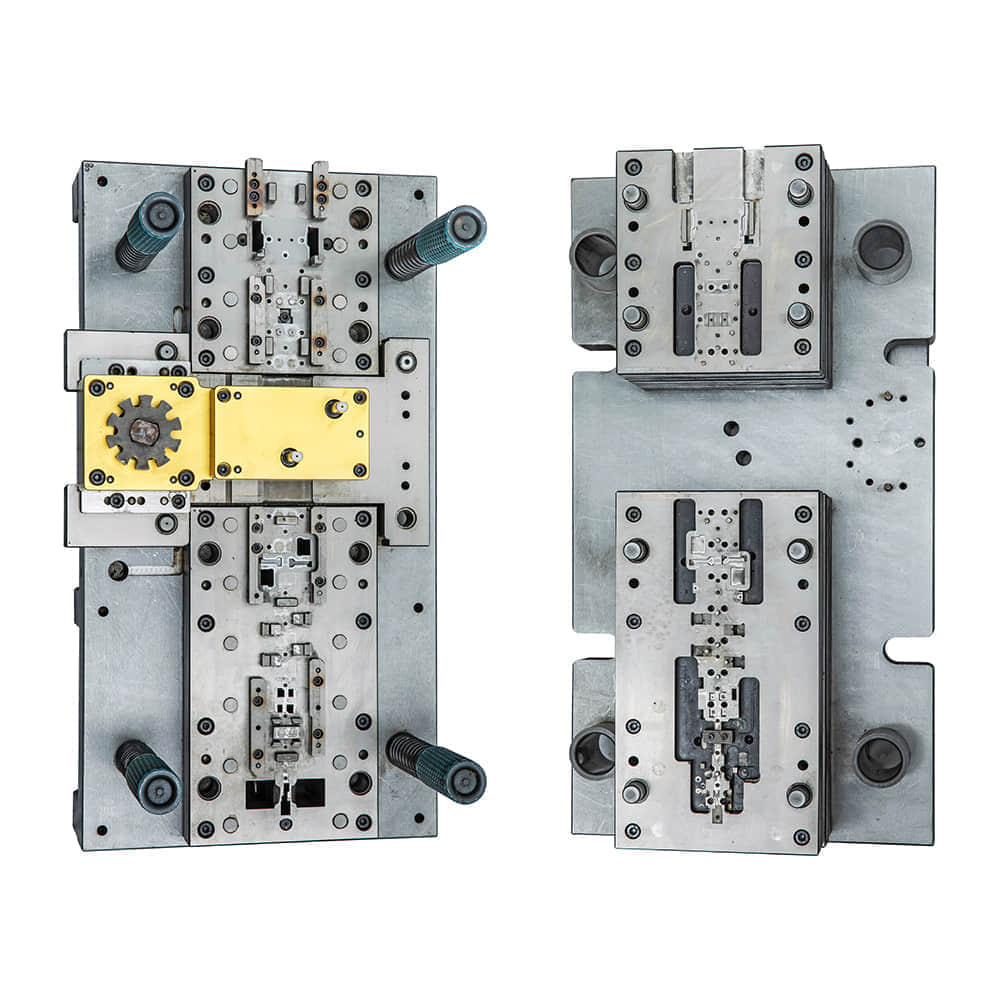